What is FR4 TG130?
FR4 TG130 is a high-performance, flame-retardant printed circuit board (PCB) material that belongs to the FR4 family. The “TG” in its name stands for “Tg,” which represents the glass transition temperature of the material. The “130” indicates that the glass transition temperature of this particular FR4 variant is 130°C.
FR4 TG130 is manufactured using a specialized epoxy resin system that provides enhanced thermal stability and improved mechanical properties compared to standard FR4 materials. This makes it an ideal choice for applications that require higher reliability and durability under demanding operating conditions.
Composition of FR4 TG130
FR4 TG130 is composed of a reinforced fiberglass fabric substrate that is impregnated with a proprietary epoxy resin system. The fiberglass fabric provides the necessary structural strength and dimensional stability to the PCB, while the epoxy resin acts as a binder and insulator.
The specific composition of FR4 TG130 includes:
- Fiberglass fabric (typically E-glass)
- High-performance epoxy resin system
- Copper foil for conductive layers
- Additional additives for improved properties (e.g., flame retardants, fillers)
Key Features of FR4 TG130
FR4 TG130 offers several key features that set it apart from other PCB materials:
1. High Glass Transition Temperature (Tg)
One of the most significant features of FR4 TG130 is its high glass transition temperature of 130°C. This means that the material maintains its mechanical and electrical properties at higher temperatures compared to standard FR4, which typically has a Tg of around 115°C to 120°C.
The higher Tg of FR4 TG130 provides several benefits:
- Improved thermal stability
- Reduced thermal expansion
- Better resistance to thermal stress and warpage
- Enhanced reliability in high-temperature applications
2. Excellent Mechanical Properties
FR4 TG130 exhibits excellent mechanical properties, making it suitable for applications that require high strength and durability. Some of the key mechanical properties of FR4 TG130 include:
Property | Value |
---|---|
Tensile Strength | 310 MPa |
Flexural Strength | 415 MPa |
Compressive Strength | 425 MPa |
Izod Impact Strength | 120 kJ/m^2 |
These mechanical properties enable FR4 TG130 to withstand various stresses and strains encountered during the manufacturing process and in the final application.
3. Enhanced Electrical Properties
FR4 TG130 offers improved electrical properties compared to standard FR4 materials. Some of the key electrical properties of FR4 TG130 include:
Property | Value |
---|---|
Dielectric Constant (1 MHz) | 4.5 |
Dissipation Factor (1 MHz) | 0.02 |
Dielectric Strength | 45 kV/mm |
Surface Resistivity | 10^12 Ω |
Volume Resistivity | 10^10 Ω·cm |
These electrical properties make FR4 TG130 suitable for high-frequency applications and designs that require low signal loss and reduced electromagnetic interference (EMI).
4. Excellent Thermal Properties
In addition to its high glass transition temperature, FR4 TG130 also exhibits excellent thermal properties. Some of the key thermal properties of FR4 TG130 include:
Property | Value |
---|---|
Thermal Conductivity | 0.3 W/m·K |
Coefficient of Thermal Expansion (CTE) | 12-14 ppm/°C |
Thermal Decomposition Temperature | >320°C |
These thermal properties enable FR4 TG130 to dissipate heat effectively, minimize thermal stress, and maintain its structural integrity in high-temperature environments.
5. Flame Retardancy
FR4 TG130 is a flame-retardant material that meets the UL 94 V-0 flammability rating. This means that the material self-extinguishes within a specified time when exposed to a flame, preventing the spread of fire.
The flame-retardant properties of FR4 TG130 are achieved through the use of halogen-free flame retardants that are incorporated into the epoxy resin system. This not only ensures the safety of the PCB but also complies with various environmental regulations, such as RoHS and REACH.
Applications of FR4 TG130
FR4 TG130 finds applications in various industries and domains where high reliability, thermal stability, and excellent mechanical and electrical properties are required. Some of the key applications of FR4 TG130 include:
- Automotive electronics
- Engine control units (ECUs)
- Powertrain control modules
- Infotainment systems
-
Advanced driver assistance systems (ADAS)
-
Industrial electronics
- Motor drives and controls
- Power supplies
- Instrumentation and measurement devices
-
Factory automation systems
-
Aerospace and defense
- Avionics systems
- Radar and communication equipment
- Military-grade electronics
-
Satellite components
-
Medical devices
- Diagnostic equipment
- Monitoring systems
- Implantable devices
-
Surgical instruments
-
Telecommunications
- Base stations
- Routers and switches
- Optical network equipment
- 5G infrastructure
In these applications, FR4 TG130 provides the necessary reliability, durability, and performance to ensure the proper functioning of the electronic systems under demanding operating conditions.
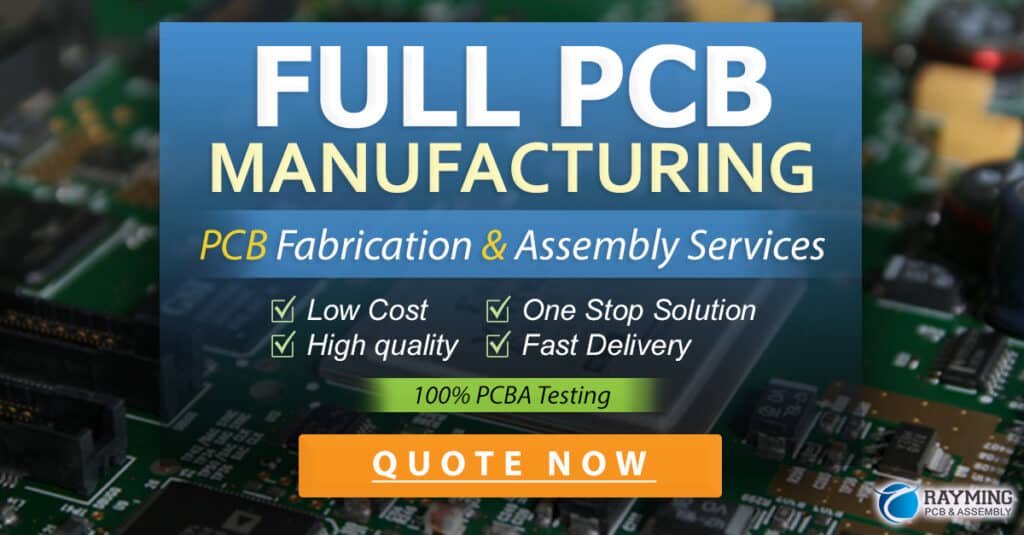
Advantages of FR4 TG130 over Other PCB Materials
FR4 TG130 offers several advantages over other PCB materials, making it a preferred choice for high-performance applications:
-
Higher thermal stability: The high glass transition temperature of FR4 TG130 enables it to maintain its properties at elevated temperatures, reducing the risk of thermal damage and ensuring reliable operation.
-
Improved mechanical strength: The reinforced fiberglass substrate and high-performance epoxy resin system provide FR4 TG130 with excellent mechanical properties, making it resistant to physical stresses and impacts.
-
Better electrical performance: FR4 TG130 exhibits lower dielectric constant and dissipation factor compared to standard FR4, resulting in reduced signal loss and improved high-frequency performance.
-
Enhanced reliability: The combination of high Tg, excellent thermal properties, and strong mechanical properties makes FR4 TG130 a highly reliable material for demanding applications.
-
Environmentally friendly: FR4 TG130 uses halogen-free flame retardants, making it compliant with various environmental regulations and reducing the environmental impact of PCB manufacturing and disposal.
Manufacturing Considerations for FR4 TG130
When manufacturing PCBs using FR4 TG130, there are several considerations to keep in mind:
-
Processing temperature: Due to the higher glass transition temperature of FR4 TG130, the processing temperature during PCB manufacturing should be adjusted accordingly to ensure proper curing and avoid thermal damage.
-
Drilling and routing: The enhanced mechanical properties of FR4 TG130 may require adjustments to drilling and routing parameters to ensure clean and accurate holes and edges.
-
Copper foil selection: Choosing the appropriate copper foil thickness and type is crucial to optimize the electrical performance and reliability of the PCB.
-
Lamination pressure and time: The lamination process for FR4 TG130 may require fine-tuning of pressure and time to achieve optimal bonding between the layers and minimize voids or delamination.
-
Surface finish: Selecting a suitable surface finish, such as ENIG (Electroless Nickel Immersion Gold) or OSP (Organic Solderability Preservative), is important to ensure good solderability and protection of the copper traces.
By considering these manufacturing aspects, PCB manufacturers can effectively leverage the benefits of FR4 TG130 and produce high-quality boards that meet the requirements of demanding applications.
Frequently Asked Questions (FAQ)
-
Q: What is the main difference between FR4 TG130 and standard FR4?
A: The main difference between FR4 TG130 and standard FR4 is the glass transition temperature (Tg). FR4 TG130 has a higher Tg of 130°C, providing improved thermal stability and performance compared to standard FR4, which typically has a Tg of around 115°C to 120°C. -
Q: Is FR4 TG130 suitable for high-frequency applications?
A: Yes, FR4 TG130 is suitable for high-frequency applications due to its enhanced electrical properties, such as lower dielectric constant and dissipation factor. These properties minimize signal loss and improve the overall performance of high-frequency circuits. -
Q: Can FR4 TG130 be used in automotive electronics?
A: Yes, FR4 TG130 is widely used in automotive electronics, particularly in applications that require high reliability and thermal stability. Its ability to withstand higher temperatures and mechanical stresses makes it an ideal choice for automotive control units, infotainment systems, and other critical electronic components. -
Q: Is FR4 TG130 compliant with environmental regulations?
A: Yes, FR4 TG130 is compliant with various environmental regulations, such as RoHS (Restriction of Hazardous Substances) and REACH (Registration, Evaluation, Authorization, and Restriction of Chemicals). It uses halogen-free flame retardants, reducing the environmental impact during manufacturing and disposal. -
Q: Are there any special considerations when designing PCBs with FR4 TG130?
A: When designing PCBs with FR4 TG130, it is important to consider the specific properties and characteristics of the material. This includes accounting for the higher processing temperatures, adjusting drilling and routing parameters, selecting appropriate copper foil and surface finish, and optimizing the lamination process. Working closely with experienced PCB manufacturers can help ensure the successful design and fabrication of FR4 TG130 boards.
Conclusion
FR4 TG130 is a unique and high-performance PCB material that offers several key features and benefits over standard FR4. Its high glass transition temperature, excellent mechanical and electrical properties, and enhanced thermal stability make it an ideal choice for demanding applications in various industries, including automotive, industrial, aerospace, medical, and telecommunications.
By understanding the composition, properties, and manufacturing considerations of FR4 TG130, PCB designers and manufacturers can effectively leverage its advantages to create reliable, durable, and high-performance electronic systems. As technology continues to advance and the requirements for PCBs become more stringent, FR4 TG130 is poised to play a crucial role in enabling the next generation of electronic devices and applications.
No responses yet