Understanding FR4 and Its Properties
FR4 (Flame Retardant 4) is a widely used material in the electronics industry for manufacturing printed circuit boards (PCBs). It is a composite material made from woven fiberglass cloth and epoxy resin. The “4” in FR4 refers to the material’s flame retardant properties, which meet the UL94V-0 standard.
Composition and Manufacturing Process
FR4 is composed of multiple layers of fiberglass cloth impregnated with epoxy resin. The manufacturing process involves the following steps:
- Impregnation: The fiberglass cloth is impregnated with epoxy resin.
- Stacking: Multiple layers of impregnated fiberglass cloth are stacked together.
- Pressing: The stacked layers are pressed under high pressure and temperature to cure the epoxy resin.
- Cutting: The cured FR4 sheet is cut to the desired size and shape.
Key Properties of FR4
FR4 possesses several key properties that make it an ideal choice for PCB manufacturing:
- Flame Retardancy: FR4 meets the UL94V-0 standard, which means it is highly resistant to ignition and flame spread.
- Electrical Insulation: The epoxy resin in FR4 provides excellent electrical insulation properties, preventing short circuits and signal interference.
- Mechanical Strength: The combination of fiberglass and epoxy resin gives FR4 high mechanical strength and durability.
- Thermal Stability: FR4 maintains its properties over a wide temperature range, typically from -40°C to +130°C.
- Moisture Resistance: FR4 has good moisture resistance, making it suitable for use in various environmental conditions.
Factors Affecting FR4 Quality
Several factors can impact the quality of FR4 material, which in turn affects the performance and reliability of the PCBs manufactured using it. Let’s explore these factors in detail.
Raw Material Quality
The quality of the raw materials used in FR4 production plays a crucial role in determining the final product’s quality. The two main components are fiberglass cloth and epoxy resin.
Fiberglass Cloth Quality
The quality of the fiberglass cloth is determined by several factors:
- Fiber Type: E-glass is the most commonly used fiber type in FR4 production. Its properties, such as strength and electrical insulation, directly impact the quality of the FR4 material.
- Weave Pattern: The weave pattern of the fiberglass cloth affects the mechanical and electrical properties of the FR4. Common weave patterns include plain, twill, and satin.
- Thickness: The thickness of the fiberglass cloth influences the overall thickness and mechanical strength of the FR4 material.
Epoxy Resin Quality
The quality of the epoxy resin used in FR4 production is equally important. Key factors include:
- Purity: The purity of the epoxy resin affects its electrical insulation properties and overall performance.
- Viscosity: The viscosity of the epoxy resin determines how well it impregnates the fiberglass cloth and affects the final product’s uniformity.
- Curing Properties: The curing properties of the epoxy resin, such as curing time and temperature, impact the final properties of the FR4 material.
Manufacturing Process Control
Strict control over the manufacturing process is essential to ensure consistent FR4 quality. Key aspects of process control include:
- Temperature and Pressure: Maintaining the correct temperature and pressure during the pressing stage is crucial for proper curing of the epoxy resin and achieving the desired properties.
- Stacking and Alignment: Proper stacking and alignment of the impregnated fiberglass layers ensure a uniform thickness and prevent internal stresses or defects.
- Contamination Prevention: Preventing contamination during the manufacturing process is essential to maintain the purity and integrity of the FR4 material.
Quality Testing and Inspection
Rigorous quality testing and inspection procedures are necessary to ensure that the FR4 material meets the required specifications and standards. Common quality tests include:
- Dimensional Inspection: Verifying the thickness, width, and length of the FR4 sheets to ensure they meet the specified tolerances.
- Electrical Testing: Measuring the dielectric constant, dissipation factor, and insulation resistance to ensure the FR4 material meets the required electrical properties.
- Mechanical Testing: Evaluating the flexural strength, tensile strength, and peel strength to ensure the FR4 material has the necessary mechanical properties.
- Thermal Testing: Assessing the thermal expansion coefficient and glass transition temperature to ensure the FR4 material can withstand the expected thermal stresses.
Storage and Handling
Proper storage and handling of FR4 material are essential to maintain its quality and prevent degradation. Key considerations include:
- Temperature and Humidity Control: Storing FR4 in a controlled environment with stable temperature and humidity levels prevents warping, moisture absorption, and other issues.
- Protective Packaging: Using appropriate protective packaging, such as moisture barrier bags, prevents damage and contamination during storage and transportation.
- Shelf Life Management: Adhering to the recommended shelf life of the FR4 material ensures that it maintains its properties and performance over time.
FR4 Grades and Classifications
FR4 material is available in various grades and classifications, each with specific properties and performance characteristics. Understanding these grades helps in selecting the most suitable FR4 for a given application.
NEMA Grades
The National Electrical Manufacturers Association (NEMA) has established a grading system for FR4 material based on its properties and performance. The most common NEMA grades are:
- FR4 Grade: Standard grade FR4 with good mechanical, electrical, and thermal properties.
- FR4 High Tg: FR4 with a higher glass transition temperature (Tg) for improved thermal stability.
- FR4 Low Dk: FR4 with a lower dielectric constant (Dk) for high-frequency applications.
- FR4 High Density: FR4 with a higher density for improved mechanical strength and dimensional stability.
IPC Classifications
The IPC (Association Connecting Electronics Industries) has developed a classification system for FR4 based on its performance and reliability. The most common IPC classifications are:
- IPC-4101: Specification for base materials for rigid and multilayer printed boards.
- IPC-6012: Qualification and performance specification for rigid printed boards.
- IPC-6018: Microwave end product board inspection and test.
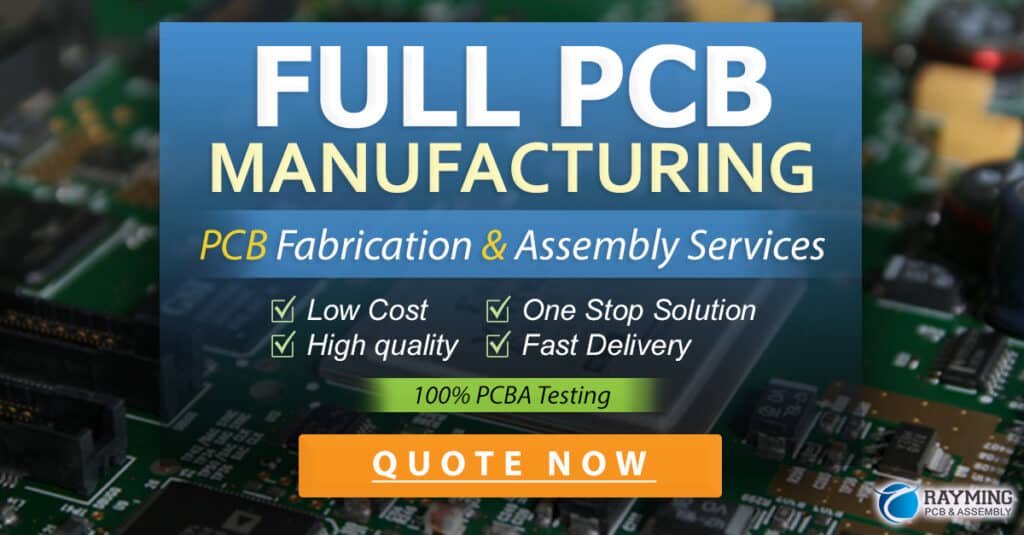
Selecting the Right FR4 Quality for Your Application
Choosing the appropriate FR4 quality for your application is crucial to ensure the desired performance, reliability, and cost-effectiveness. Consider the following factors when selecting FR4:
-
Electrical Requirements: Consider the required dielectric constant, dissipation factor, and insulation resistance based on your application’s electrical demands.
-
Thermal Requirements: Evaluate the expected operating temperature range and thermal stresses to select an FR4 grade with suitable thermal properties.
-
Mechanical Requirements: Assess the required mechanical strength, flexibility, and dimensional stability based on your application’s mechanical needs.
-
Frequency and Signal Integrity: For high-frequency applications or designs with critical signal integrity requirements, choose FR4 grades with low dielectric constant and dissipation factor.
-
Cost and Availability: Consider the cost and availability of different FR4 grades and select the one that offers the best balance between performance and cost for your application.
Frequently Asked Questions (FAQ)
1. What is the difference between FR4 and other PCB Materials?
FR4 is a composite material made from woven fiberglass cloth and epoxy resin, offering excellent electrical insulation, mechanical strength, and flame retardancy. Other PCB Materials, such as polyimide or PTFE, may offer specific properties like higher temperature resistance or lower dielectric constant but at a higher cost.
2. Can FR4 be used for high-frequency applications?
Standard FR4 may not be the best choice for high-frequency applications due to its relatively high dielectric constant and dissipation factor. For such applications, specialized FR4 grades like FR4 Low Dk or other low-loss materials like Rogers or Taconic are recommended.
3. How does the thickness of FR4 affect its performance?
The thickness of FR4 affects its mechanical strength, thermal dissipation, and electrical properties. Thicker FR4 offers higher mechanical strength and better thermal dissipation but may increase the overall thickness of the PCB. Thinner FR4 allows for more compact designs but may compromise mechanical stability. The choice of thickness depends on the specific requirements of the application.
4. What are the storage and handling requirements for FR4?
FR4 should be stored in a controlled environment with stable temperature and humidity levels to prevent warping, moisture absorption, and other issues. It should be protected from dust, dirt, and other contaminants using appropriate packaging materials. Adhering to the recommended shelf life is essential to ensure the material maintains its properties and performance.
5. How can I ensure consistent FR4 quality for my PCB production?
To ensure consistent FR4 quality, partner with reputable suppliers who have strict quality control processes in place. Regularly audit your suppliers and request quality certifications and test reports. Implement incoming material inspection and testing procedures to verify the quality of the FR4 material before using it in production. Continuously monitor the performance and reliability of your PCBs and address any quality issues promptly.
Conclusion
FR4 is a versatile and widely used material in the electronics industry for PCB manufacturing. Its excellent properties, including flame retardancy, electrical insulation, mechanical strength, and thermal stability, make it an ideal choice for a wide range of applications.
Understanding the factors that affect FR4 quality, such as raw material quality, manufacturing process control, and quality testing, is essential to ensure the desired performance and reliability of the final product. Selecting the appropriate FR4 grade and classification based on the specific requirements of your application is crucial for optimal results.
By partnering with reputable suppliers, implementing strict quality control measures, and following proper storage and handling procedures, you can ensure consistent FR4 quality and achieve successful PCB production.
Property | Typical Value |
---|---|
Dielectric Constant (Dk) @ 1 MHz | 4.5 |
Dissipation Factor (Df) @ 1 MHz | 0.02 |
Dielectric Breakdown Strength (kV/mm) | 20 |
Thermal Conductivity (W/mK) | 0.3 |
Glass Transition Temperature (Tg) (°C) | 130-140 |
Coefficient of Thermal Expansion (CTE) (ppm/°C) | 12-16 |
Flexural Strength (MPa) | 415 |
Tensile Strength (MPa) | 345 |
Density (g/cm³) | 1.85 |
Table: Typical properties of standard FR4 material.
By carefully considering the quality aspects of FR4 and selecting the appropriate grade for your application, you can ensure the optimal performance, reliability, and cost-effectiveness of your PCB Designs.
No responses yet