Introduction to FR4 Material
FR4 is a widely used material in the electronics industry, particularly in the manufacturing of printed circuit boards (PCBs). It is a composite material made from woven fiberglass cloth with an epoxy resin binder. The “FR” in FR4 stands for “Flame Retardant,” indicating its inherent flame-resistant properties. The “4” represents the woven glass reinforcement used in its construction.
FR4 has become the standard material for PCBs due to its excellent mechanical, electrical, and thermal properties. It provides a stable and reliable base for electronic components and interconnections, making it essential for the proper functioning and durability of electronic devices.
Key Features of FR4 Material
- High strength and stiffness
- Excellent electrical insulation properties
- Good thermal stability
- Flame retardant
- Resistant to moisture and chemicals
- Suitable for high-frequency applications
In this article, we will delve into the properties of FR4 material, its manufacturing process, and its various applications in the electronics industry.
Properties of FR4 Material
Mechanical Properties
FR4 exhibits excellent mechanical properties, making it suitable for a wide range of applications. Its high strength and stiffness provide the necessary support for electronic components and ensure the structural integrity of PCBs.
Tensile Strength
The tensile strength of FR4 refers to its ability to resist breaking under tension. It typically ranges from 310 to 380 MPa (45,000 to 55,000 psi) in the lengthwise direction and 280 to 345 MPa (40,000 to 50,000 psi) in the crosswise direction.
Flexural Strength
Flexural strength measures the material’s ability to resist bending under load. FR4 has a flexural strength of approximately 415 to 485 MPa (60,000 to 70,000 psi) in the lengthwise direction and 345 to 415 MPa (50,000 to 60,000 psi) in the crosswise direction.
Compressive Strength
Compressive strength indicates the material’s resistance to compression. FR4 has a compressive strength of about 415 to 485 MPa (60,000 to 70,000 psi).
Property | Lengthwise Direction | Crosswise Direction |
---|---|---|
Tensile Strength | 310-380 MPa (45,000-55,000 psi) | 280-345 MPa (40,000-50,000 psi) |
Flexural Strength | 415-485 MPa (60,000-70,000 psi) | 345-415 MPa (50,000-60,000 psi) |
Compressive Strength | 415-485 MPa (60,000-70,000 psi) | – |
Electrical Properties
FR4 is an excellent electrical insulator, making it ideal for use in PCBs. Its electrical properties ensure proper signal transmission and minimize signal loss.
Dielectric Constant
The dielectric constant of FR4 is a measure of its ability to store electrical energy. It typically ranges from 4.35 to 4.70 at 1 MHz, depending on the specific formulation and glass content.
Dielectric Strength
Dielectric strength refers to the maximum electric field that FR4 can withstand before electrical breakdown occurs. It is usually around 20 to 28 kV/mm (500 to 700 V/mil).
Dissipation Factor
The dissipation factor, also known as loss tangent, represents the energy loss in FR4 when subjected to an alternating electric field. It is typically in the range of 0.020 to 0.030 at 1 MHz.
Property | Value |
---|---|
Dielectric Constant (1 MHz) | 4.35-4.70 |
Dielectric Strength | 20-28 kV/mm (500-700 V/mil) |
Dissipation Factor (1 MHz) | 0.020-0.030 |
Thermal Properties
FR4 exhibits good thermal stability, allowing it to withstand the heat generated by electronic components and maintain its properties over a wide temperature range.
Glass Transition Temperature (Tg)
The glass transition temperature (Tg) is the temperature at which FR4 transitions from a glassy state to a rubbery state. It is typically around 130°C to 140°C (266°F to 284°F), depending on the specific formulation.
Coefficient of Thermal Expansion (CTE)
The coefficient of thermal expansion (CTE) measures the material’s dimensional change with temperature. FR4 has a CTE of approximately 14 to 16 ppm/°C (8 to 9 ppm/°F) in the x-y plane and 50 to 70 ppm/°C (28 to 39 ppm/°F) in the z-axis.
Thermal Conductivity
Thermal conductivity indicates the material’s ability to conduct heat. FR4 has a relatively low thermal conductivity of about 0.3 to 0.4 W/m·K.
Property | Value |
---|---|
Glass Transition Temperature (Tg) | 130-140°C (266-284°F) |
Coefficient of Thermal Expansion (CTE) – x-y plane | 14-16 ppm/°C (8-9 ppm/°F) |
Coefficient of Thermal Expansion (CTE) – z-axis | 50-70 ppm/°C (28-39 ppm/°F) |
Thermal Conductivity | 0.3-0.4 W/m·K |
Manufacturing Process of FR4
The manufacturing process of FR4 involves several steps to create a composite material with the desired properties.
Step 1: Impregnation
The process begins with the impregnation of woven glass fabric with epoxy resin. The glass fabric is typically a plain weave or twill weave, providing strength and dimensional stability. The epoxy resin is carefully formulated to achieve the desired electrical, thermal, and mechanical properties.
Step 2: Drying
After impregnation, the resin-coated glass fabric is dried to remove any excess moisture. This step is crucial to ensure proper curing and prevent voids or defects in the final product.
Step 3: Cutting and Layup
The dried, resin-impregnated glass fabric is cut to the required size and shape. Multiple layers of the fabric are then stacked and aligned to achieve the desired thickness and orientation.
Step 4: Pressing and Curing
The stacked layers are placed in a press and subjected to high pressure and temperature. The pressure ensures proper consolidation and removes any air pockets, while the heat initiates the curing process of the epoxy resin. Curing typically occurs at temperatures around 170°C to 180°C (338°F to 356°F) for several hours.
Step 5: Cooling and Finishing
After curing, the FR4 Laminate is cooled to room temperature. It may then undergo additional finishing processes, such as surface grinding or polishing, to achieve the desired surface finish and thickness tolerance.
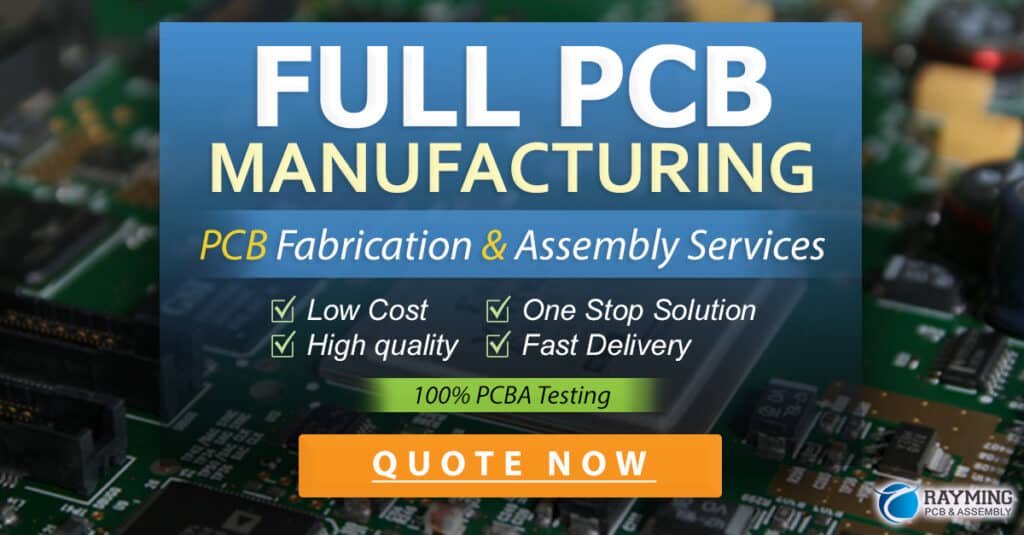
Applications of FR4
FR4 finds extensive use in various industries, particularly in the electronics sector.
Printed Circuit Boards (PCBs)
FR4 is the most common substrate material for PCBs. It provides a stable and insulating base for copper traces and electronic components. FR4 PCBs are used in a wide range of electronic devices, including:
- Consumer electronics (smartphones, tablets, laptops)
- Automotive electronics (engine control units, infotainment systems)
- Industrial equipment (controllers, sensors, automation systems)
- Medical devices (diagnostic equipment, monitoring systems)
- Telecommunications (routers, switches, base stations)
Insulation Materials
FR4 is used as an insulation material in various electrical and electronic applications. Its excellent dielectric properties make it suitable for insulating components, such as transformers, motors, and generators.
Structural Components
Due to its high strength and stiffness, FR4 is used in the construction of structural components in electronic devices. It can be used for brackets, housings, and support structures, providing mechanical stability and protection.
High-Frequency Applications
FR4 is suitable for high-frequency applications, such as radio frequency (RF) and microwave circuits. Its low dissipation factor and stable dielectric constant make it a good choice for high-speed digital and analog circuits.
FR4 vs. Other PCB Materials
While FR4 is the most widely used PCB material, there are other materials available for specific applications.
FR2
FR2 is a lower-grade PCB material made from phenolic resin and paper. It is less expensive than FR4 but has inferior mechanical and electrical properties. FR2 is suitable for low-end, non-critical applications.
CEM-1 and CEM-3
CEM-1 and CEM-3 are composite epoxy materials that combine paper and woven glass reinforcement. They offer a balance between cost and performance, making them suitable for applications that require better properties than FR2 but are less demanding than FR4.
High-Frequency Materials
For high-frequency applications, such as RF and microwave circuits, specialized materials like Rogers RO4000 series, Teflon, and polyimide are used. These materials have lower dielectric constants and dissipation factors, enabling better signal integrity at higher frequencies.
Frequently Asked Questions (FAQ)
1. What does FR4 stand for?
FR4 stands for “Flame Retardant 4.” The “FR” indicates its flame-resistant properties, while the “4” represents the woven glass reinforcement used in its construction.
2. Is FR4 suitable for high-temperature applications?
FR4 has a glass transition temperature (Tg) of around 130°C to 140°C (266°F to 284°F). It can withstand temperatures up to its Tg for extended periods without significant degradation of its properties. However, for applications that require higher temperatures, specialized materials like polyimide or ceramic-based substrates may be more suitable.
3. Can FR4 be used for Flexible PCBs?
FR4 is primarily used for rigid PCBs due to its inherent stiffness. For flexible PCBs, materials like polyimide or polyester are commonly used. These materials offer the necessary flexibility while maintaining good electrical and thermal properties.
4. How does the thickness of FR4 affect its properties?
The thickness of FR4 can influence its mechanical and thermal properties. Thicker FR4 laminates generally have higher stiffness and better thermal management capabilities. However, increasing thickness also affects the weight and cost of the PCB. The choice of thickness depends on the specific requirements of the application, such as strength, thermal dissipation, and electrical performance.
5. What are the environmental considerations when using FR4?
FR4 is a stable and durable material, but proper disposal and recycling practices should be followed to minimize environmental impact. The glass fibers and epoxy resin in FR4 can be recycled or repurposed in various ways. Manufacturers and users of FR4 should adhere to local regulations and guidelines for the disposal and recycling of electronic waste.
Conclusion
FR4 is a versatile and widely used material in the electronics industry, particularly for the fabrication of PCBs. Its excellent mechanical, electrical, and thermal properties make it suitable for a wide range of applications, from consumer electronics to industrial equipment.
Understanding the properties and characteristics of FR4 is crucial for designers and manufacturers to make informed decisions when selecting materials for their projects. By leveraging the strengths of FR4 and considering its limitations, engineers can design reliable and high-performance electronic devices.
As technology advances and new applications emerge, FR4 continues to be a fundamental material in the electronics industry. Its combination of cost-effectiveness, performance, and reliability makes it a preferred choice for many PCB designers and manufacturers.
No responses yet