Introduction to Flexible PCB Prototypes
Flexible PCB Prototypes are revolutionizing the electronics industry with their versatile applications and unique properties. These innovative circuit boards offer a range of benefits, including increased durability, improved connectivity, and enhanced design flexibility. In this article, we will explore the world of flexible PCB prototype manufacturing services, discussing their advantages, manufacturing processes, and various applications across industries.
What are Flexible PCB Prototypes?
Flexible PCB prototypes are printed circuit boards made from flexible materials, such as polyimide or polyester, which allow them to bend and conform to various shapes and surfaces. Unlike traditional rigid PCBs, flexible PCBs can be twisted, folded, and stretched without compromising their electrical performance or structural integrity. This unique characteristic makes them ideal for applications that require compact, lightweight, and flexible electronic assemblies.
Advantages of Flexible PCB Prototypes
Flexible PCB prototypes offer several advantages over their rigid counterparts, including:
-
Increased Durability: The flexible nature of these PCBs allows them to withstand repeated bending and flexing without breaking or losing functionality, making them suitable for applications that experience frequent movement or vibration.
-
Improved Connectivity: Flexible PCBs can be designed with a single continuous circuit, eliminating the need for connectors and reducing the risk of connection failures.
-
Enhanced Design Flexibility: The ability to conform to different shapes and surfaces enables designers to create more compact and space-efficient electronic assemblies, leading to smaller and lighter end products.
-
Reduced Assembly Costs: Flexible PCBs can simplify the assembly process by reducing the number of components and connections required, resulting in lower assembly costs and faster production times.
Flexible PCB Prototype Manufacturing Process
The manufacturing process for flexible PCB prototypes involves several key steps, each requiring specialized equipment and expertise. Let’s take a closer look at the various stages involved in creating these innovative circuit boards.
Step 1: Design and Layout
The first step in the flexible PCB prototype manufacturing process is designing the circuit layout using specialized PCB design software. The design must consider the unique properties of flexible materials, such as their bending radius and thermal expansion coefficients, to ensure optimal performance and reliability.
Step 2: Material Selection
Choosing the right flexible substrate material is crucial for the success of the final product. Common materials used in flexible PCB prototypes include:
- Polyimide (PI): Known for its excellent thermal stability and mechanical strength, polyimide is the most widely used substrate material for flexible PCBs.
- Polyester (PET): Polyester offers good electrical properties and is often used in applications that require a more cost-effective solution.
The choice of material depends on factors such as the application requirements, operating environment, and budget constraints.
Step 3: Copper Lamination
Once the substrate material is selected, a thin layer of copper is laminated onto the surface using heat and pressure. The copper layer serves as the conductive pathway for the electrical signals in the circuit.
Step 4: Patterning and Etching
The desired circuit pattern is then transferred onto the copper layer using a photolithographic process. This involves applying a photoresist coating, exposing it to UV light through a photomask, and developing the resist to reveal the desired pattern. The exposed copper is then etched away using a chemical solution, leaving behind the circuit traces.
Step 5: Coverlay Application
To protect the circuitry and provide insulation, a coverlay film is laminated onto the surface of the flexible PCB. The coverlay is typically made from the same material as the substrate and is applied using heat and pressure.
Step 6: Surface Finishing
The final step in the flexible PCB prototype manufacturing process is applying a surface finish to the exposed copper traces. Common surface finishes include:
- ENIG (Electroless Nickel Immersion Gold): Provides excellent solderability and corrosion resistance.
- OSP (Organic Solderability Preservative): Offers a cost-effective solution for short-term storage and assembly.
The choice of surface finish depends on factors such as the application requirements, assembly process, and environmental conditions.
Applications of Flexible PCB Prototypes
Flexible PCB prototypes find applications across a wide range of industries, thanks to their unique properties and design flexibility. Some of the most common applications include:
Wearable Electronics
Flexible PCBs are ideally suited for wearable electronics, such as smartwatches, fitness trackers, and medical monitoring devices. Their ability to conform to the contours of the human body and withstand repeated flexing makes them an essential component in these compact and lightweight devices.
Automotive Electronics
The automotive industry has embraced flexible PCBs for various applications, such as dashboard displays, sensor assemblies, and in-vehicle entertainment systems. The durability and reliability of flexible PCBs make them well-suited for the harsh operating conditions experienced in automotive environments.
Medical Devices
Flexible PCBs are increasingly being used in medical devices, such as implantable sensors, surgical instruments, and diagnostic equipment. Their biocompatibility, small form factor, and ability to integrate with other medical components make them a valuable tool in the development of advanced medical technologies.
Consumer Electronics
From smartphones and tablets to virtual reality headsets and gaming controllers, flexible PCBs are found in a wide range of consumer electronics. Their space-saving design and ability to accommodate complex shapes and folds enable manufacturers to create sleeker and more ergonomic devices.
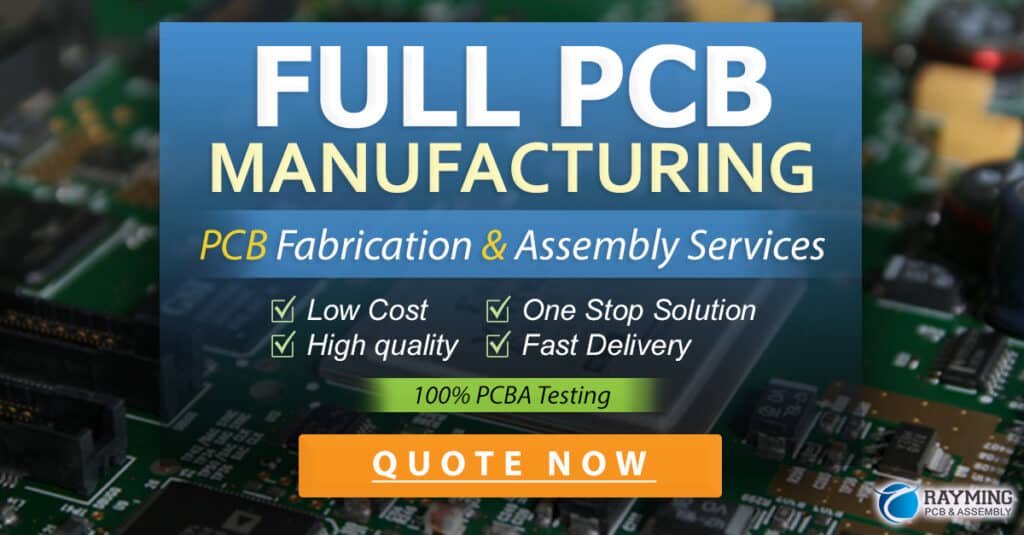
Choosing the Right Flexible PCB Prototype Manufacturing Partner
When selecting a flexible PCB prototype manufacturing partner, it is essential to consider several key factors to ensure the success of your project. Some of the most important considerations include:
Technical Expertise
Look for a manufacturer with a proven track record of producing high-quality flexible PCB prototypes. They should have a deep understanding of the unique challenges associated with flexible PCB design and manufacturing, as well as the expertise to overcome these challenges and deliver a reliable product.
Manufacturing Capabilities
Ensure that the manufacturer has the necessary equipment and facilities to handle your specific project requirements. This includes the ability to work with a variety of flexible substrate materials, copper thicknesses, and surface finishes, as well as the capacity to produce prototypes in the required quantities and timeframes.
Quality Control
A robust quality control process is essential for ensuring the reliability and performance of your flexible PCB prototypes. Look for a manufacturer that adheres to strict quality standards, such as ISO 9001, and employs rigorous testing and inspection procedures throughout the manufacturing process.
Customer Support
Choose a manufacturer that offers excellent customer support and communication throughout the project lifecycle. They should be responsive to your inquiries, provide regular updates on project progress, and be willing to work closely with your team to address any issues or concerns that may arise.
Frequently Asked Questions (FAQ)
-
What is the typical turnaround time for flexible PCB prototype manufacturing?
The turnaround time for flexible PCB prototypes can vary depending on the complexity of the design, the chosen materials, and the manufacturer’s workload. However, most reputable manufacturers can deliver prototypes within 2-3 weeks, with some offering expedited services for urgent projects. -
How do I determine the appropriate thickness for my flexible PCB prototype?
The thickness of your flexible PCB prototype will depend on several factors, including the application requirements, the desired flexibility, and the number of layers in the design. As a general rule, thinner substrates offer greater flexibility but may be more challenging to manufacture. Consult with your manufacturing partner to determine the optimal thickness for your specific project. -
Can flexible PCB prototypes be used in high-temperature applications?
Yes, flexible PCBs can be designed to withstand high temperatures, depending on the choice of substrate material and the specific application requirements. Polyimide, for example, has excellent thermal stability and can maintain its properties at temperatures up to 300°C. -
Are there any design constraints to consider when creating a flexible PCB prototype?
Yes, there are several design constraints to keep in mind when creating a flexible PCB prototype. These include the minimum bend radius, the placement of components and traces to avoid stress concentrations, and the selection of materials with appropriate thermal expansion coefficients. Your manufacturing partner can provide guidance on these and other design considerations to ensure the optimal performance of your prototype. -
How much does it cost to manufacture a flexible PCB prototype?
The cost of manufacturing a flexible PCB prototype can vary widely depending on factors such as the design complexity, the choice of materials, the number of layers, and the quantity required. As a rough estimate, simple single-layer flexible PCB prototypes can cost anywhere from $100 to $500, while more complex multi-layer designs can range from $500 to several thousand dollars. It is best to request a quote from your manufacturing partner based on your specific project requirements.
Conclusion
Flexible PCB prototype manufacturing services are essential for bringing innovative electronics products to market quickly and efficiently. By understanding the unique properties, manufacturing processes, and applications of flexible PCBs, designers and engineers can unlock new possibilities for creating compact, durable, and high-performance electronic assemblies.
When selecting a flexible PCB prototype manufacturing partner, it is crucial to consider factors such as technical expertise, manufacturing capabilities, quality control, and customer support. By choosing the right partner and working closely with them throughout the project lifecycle, you can ensure the success of your flexible PCB prototype and bring your innovative ideas to life.
Aspect | Rigid PCBs | Flexible PCBs |
---|---|---|
Material | FR-4 | Polyimide, Polyester |
Flexibility | Low | High |
Durability | Moderate | High |
Assembly Complexity | High | Low |
Space Efficiency | Moderate | High |
Typical Applications | Computers, Televisions | Wearables, Medical Devices |
As the demand for smaller, lighter, and more flexible electronic devices continues to grow, the importance of flexible PCB prototype manufacturing services will only continue to increase. By staying at the forefront of this rapidly evolving technology, manufacturers and designers can position themselves for success in the competitive world of electronics innovation.
No responses yet