What are Flexible PCBs?
Flexible PCBs, also known as flex circuits, are a type of printed circuit board made from thin, flexible materials like polyimide or PEEK. Unlike rigid PCBs made from fiberglass, flexible PCBs can bend, fold, and twist without breaking. This allows them to fit into tight spaces and dynamically flex with the product housing.
Flexible PCBs consist of a thin insulating polymer film with conductive copper traces bonded to one or both sides. Additional layers can be laminated together to create multilayer flexible PCBs for more complex designs. Components are surface mounted or attached with special low-profile connectors since through-hole technology is generally not used on flex circuits.
The unique properties of flexible PCBs make them ideal for applications that require:
- Lightweight, space-saving packaging
- Dynamic flexing or bending during use
- High reliability in harsh environments
- High interconnect density
- Conformity to curved surfaces
Some common applications of flexible PCBs include:
- Smartphones, tablets, laptops
- Wearables like smart watches and fitness trackers
- Medical devices like hearing aids and insulin pumps
- Aerospace and military electronics
- Automobiles and vehicles
- Industrial equipment and robotics
Factors that Impact Flexible PCB Cost
Now that we understand what flexible PCBs are and where they are used, let’s examine the main cost drivers in flex circuit fabrication:
1. Board Size
One of the biggest factors in flexible PCB pricing is the size of the board. Larger boards require more raw material, which increases the cost. Additionally, larger panels are more difficult to handle during fabrication, assembly, and testing, further adding to the cost.
Flex PCBs are typically produced on large panels that are then cut down to the individual board size. The panel utilization, or how many boards can fit on a production panel, affects the overall price. Smaller boards nested tightly together have a higher panel utilization, which reduces cost compared to larger boards or boards with irregular shapes.
2. Layer Count
Like rigid PCBs, the number of conductive layers in the flexible circuit impacts cost. More layers require additional materials and more complex fabrication processes, increasing cost.
Single-sided flex circuits with conductors on only one side are the simplest and lowest cost. Double-sided flex circuits have conductors on both sides, often with plated through-holes to interconnect the layers. Multi-layer flex circuits have three or more conductive layers laminated together with insulating layers in between.
Here is a general overview of how layer count affects flex PCB cost:
Flex Circuit Type | Relative Cost |
---|---|
Single-sided | $ |
Double-sided | $$ |
Multi-layer (3-4 layers) | $$$ |
Multi-layer (5+ layers) | $$$$ |
3. Material Selection
The material makeup of the flex circuit has a significant effect on cost. The most common base materials used are:
-
Polyimide (PI) – The default choice for most flex applications, PI offers an excellent balance of properties and cost. Varieties include Kapton (DuPont), Upilex (Ube), and Apical (Kaneka).
-
Polyethylene terephthalate (PET) – Lower cost than PI but also lower temperature resistance and electrical performance. Best for static flex applications.
-
Polyetheretherketone (PEEK) – A high-performance thermoplastic that offers superior mechanical strength and temperature/chemical resistance but at a higher price point than PI. Used in extremely harsh environments.
The copper foil type and thickness also impact flex PCB cost. Thicker copper foils provide higher current carrying capacity but reduce flexibility and increase cost. The most common copper types are:
-
Electrodeposited (ED) copper – The lowest cost option, ED copper is best for simple, static flex designs.
-
Rolled annealed (RA) copper – Higher cost than ED copper but offers better flexibility and fatigue resistance for dynamic flexing.
Flexible solder masks and coverlay materials that protect the circuits also vary in price depending on the material properties and application method (screenprint vs photoimageable).
4. Manufacturing Complexity
The fabrication complexity has a big influence on flexible PCB cost. More complex designs require additional processing steps, materials, and labor, all of which increase cost. Some cost-driving aspects of manufacturing complexity include:
- Tight tolerances and high precision features
- High layer counts and dense interconnects
- Blind/buried vias and microvias
- Controlled impedance
- Fine line width/spacing
- Small holes and pad sizes
- Flex-to-install regions for component assembly
- Special processing like edge plating, selective gold plating, etc.
In general, keeping the design as simple as possible while still meeting the application requirements will minimize flexible PCB cost. Involving the contract manufacturer early in the design process can help identify cost saving opportunities.
5. Order Quantity
As with most manufacturing processes, flexiblePCBs benefit from economies of scale. Ordering higher quantities allows the fixed costs like tooling and setup to be amortized over a larger number of units, reducing the per-piece price.
However, unlike rigid PCBs, flex circuits have a higher minimum order quantity (MOQ) to reach price breaks. Whereas rigid PCBs might see significant price breaks around 1000 pieces, flex circuits typically need 5000-10,000 pieces to achieve volume pricing.
For smaller quantities, flex PCBs will be considerably more expensive than equivalent rigid boards. The price gap narrows as quantities increase.
Here is an illustration of how piece price typically varies with order quantity:
Quantity | Relative Price per Unit |
---|---|
100 | $$$$$ |
500 | $$$$ |
1,000 | $$$ |
5,000 | $$ |
10,000 | $ |
6. Testing and Quality Requirements
The testing and quality assurance requirements play a role in flexible PCB cost. More stringent testing and inspection criteria will require additional time, equipment and labor, increasing cost.
Some common testing and quality assurance activities for flex circuits include:
- Automated optical inspection (AOI)
- Electrical continuity and isolation testing
- Microsection analysis
- Highly accelerated life testing (HALT)
- Flexibility/bend testing
- Visual/dimensional inspection
For critical applications in industries like medical or aerospace, there may be additional testing requirements to meet quality and reliability standards. Working with a manufacturer that is well-versed in these requirements can help control cost.
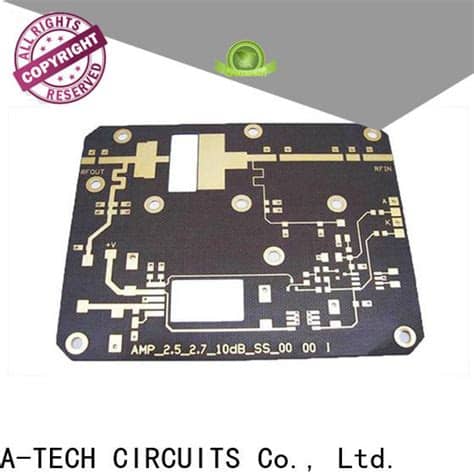
Tips for Controlling Flexible PCB Cost
Based on the cost drivers discussed above, here are some tips for keeping your flexible PCB costs under control:
-
Minimize board size – Reduce the overall board dimensions as much as the design allows. Consider orienting components to maximize panel utilization.
-
Use the minimum number of layers – Keep the layer count as low as possible while still meeting electrical/mechanical requirements. Avoid unused layers.
-
Select standard materials – Unless the application demands otherwise, use standard PI materials and copper foils to reduce cost. Avoid specialty laminates and finishes.
-
Keep manufacturing simple – Minimize complexity in the design files. Use larger feature sizes and looser tolerances where possible. Reduce the number of unique processes.
-
Order in volume – If the design is finalized and tested, order in as high a volume as is reasonable to take advantage of price breaks. Consider blanket orders or future buys.
-
Plan for testing early – Engage the manufacturer early to understand testing capabilities and requirements. Design for manufacturability and testing to control cost.
-
Consider rigid-flex – For some designs, using a rigid-flex combination construction can offer a better balance of cost and performance than using all-flex. Consult with the manufacturer for options.
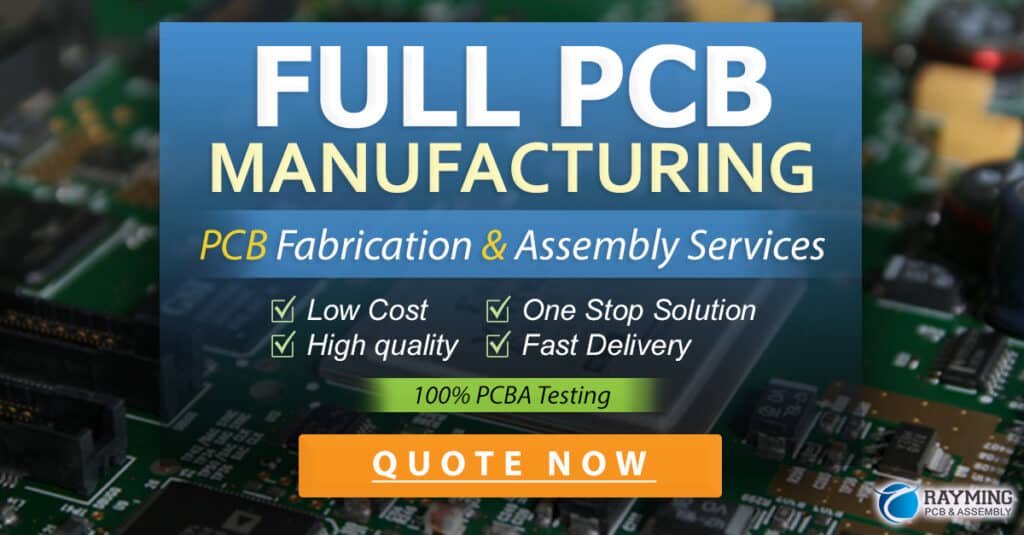
Frequently Asked Questions
How much do flexible PCBs cost?
The cost of flexible PCBs can vary widely depending on the size, complexity, materials, and volume of the design. Simple, single-sided flex circuits in high volumes might cost under $10 per board while complex multi-layer circuits in low volumes can exceed $100 per board. The best way to get an accurate cost estimate is to work with a flex circuit manufacturer and provide the design files for quotation.
Are flexible PCBs more expensive than rigid PCBs?
In general, flexible PCBs are more expensive than equivalent rigid PCBs due to the specialized materials, processes, and equipment required. The price differential is most significant at low volumes but narrows as quantities increase. However, the total system cost may be lower with flex circuits due to their ability to simplify packaging and assembly.
What is the minimum order quantity for flexible PCBs?
The MOQ for flexible PCBs varies by manufacturer but is generally higher than rigid PCBs due to the specialized nature of the process. Typical MOQs range from 100 to 1000 pieces depending on the complexity and materials. Very simple designs may have MOQs as low as 50 while complex, multilayer flex circuits may require 5000 pieces or more for volume pricing.
How long does it take to get flexible PCBs?
Standard lead times for flexible PCBs are longer than rigid PCBs due to the additional processing steps and limited number of suppliers. Simple flex circuits can be manufactured in 2-3 weeks while complex designs can take 6 weeks or more. Expedited services are available from some manufacturers for a premium.
How can I reduce the cost of my flexible PCB?
There are several ways to reduce flex PCB cost as outlined in the tips above. The most effective methods are usually minimizing board size, reducing layer count, selecting standard materials, and simplifying the manufacturing processes. Working closely with an experienced flex circuit manufacturer during the design phase can help identify the most promising cost reduction opportunities.
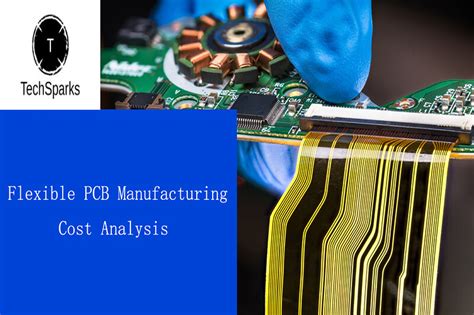
No responses yet