What are Flexible PCBs?
Flexible PCBs, also known as flex circuits, are a type of printed circuit board that can bend and flex without losing their electrical functionality. Unlike traditional rigid PCBs, flexible PCBs are made using a thin, flexible substrate, such as polyimide or polyester, which allows them to conform to various shapes and fit into tight spaces.
Flexible PCBs offer several advantages over rigid PCBs, including:
- Reduced weight and space requirements
- Improved reliability and durability
- Enhanced design flexibility
- Reduced assembly time and costs
These benefits make flexible PCBs an attractive choice for many industries, including consumer electronics, automotive, aerospace, and medical devices.
Factors Affecting Flexible PCB Cost
Several factors influence the cost of flexible PCBs. Understanding these factors can help you make informed decisions when designing and manufacturing your flex circuits.
1. Material Selection
The choice of materials used in flexible PCBs significantly impacts their cost. The most common materials used for the substrate include:
-
Polyimide (PI): Known for its excellent thermal stability and mechanical properties, polyimide is the most popular choice for flexible PCBs. However, it is also one of the most expensive options.
-
Polyester (PET): Polyester is a low-cost alternative to polyimide, offering good electrical properties and flexibility. However, it has lower temperature resistance and mechanical strength compared to polyimide.
-
Flexible copper-clad laminate (FCCL): FCCL is a composite material consisting of a copper layer bonded to a flexible substrate. The cost of FCCL varies depending on the substrate material and copper thickness.
In addition to the substrate, the choice of copper thickness and surface finish also affects the cost. Thicker copper layers and advanced surface finishes, such as gold or silver, increase the overall cost of the flexible PCB.
2. Circuit Complexity
The complexity of your flexible PCB design directly influences its cost. More complex designs require additional manufacturing steps, materials, and time, resulting in higher costs. Factors that contribute to circuit complexity include:
-
Number of layers: Flexible PCBs can have single or multiple layers. As the number of layers increases, so does the cost, due to the additional materials and processing required.
-
Circuit density: Higher circuit density, characterized by smaller trace widths and spacing, requires more precise manufacturing techniques, leading to increased costs.
-
Via and hole size: Smaller vias and holes are more challenging to manufacture and require specialized equipment, resulting in higher costs.
-
Aspect ratio: The aspect ratio, which is the ratio of the PCB’s length to its width, affects the manufacturing process and cost. Higher aspect ratios are more difficult to produce and, therefore, more expensive.
3. Quantity and Lead Time
The quantity of flexible PCBs you order and the required lead time significantly impact the cost per unit. Generally, ordering larger quantities results in lower costs per unit, as the fixed costs associated with setup and tooling are spread across more pieces.
Similarly, longer lead times often result in lower costs, as manufacturers can optimize their production schedules and resource allocation. Rush orders or short lead times may incur additional fees or higher prices.
4. Manufacturing Process
The manufacturing process used for flexible PCBs also affects their cost. There are two primary methods for producing flexible PCBs:
-
Subtractive process: In this method, the circuit pattern is etched from a copper-clad substrate using photolithography and chemical etching. This process is more common and generally less expensive than the additive process.
-
Additive process: Also known as printed electronics, this method involves printing the circuit pattern directly onto the substrate using conductive inks or pastes. While this process offers greater design flexibility and faster turnaround times, it is typically more expensive than the subtractive process.
5. Testing and Certification
Depending on your application and industry, your flexible PCBs may require additional testing and certification to ensure they meet specific standards for quality, reliability, and safety. Some common certifications include:
- UL (Underwriters Laboratories)
- IPC (Institute of Printed Circuits)
- MIL-PRF-31032 (Military Specification for Flexible Printed Wiring)
- ISO 9001 (Quality Management Systems)
The cost of testing and certification varies depending on the specific requirements and the third-party testing facility you choose. These costs should be factored into your overall flexible PCB budget.
Flexible PCB Cost Comparison
To better understand the cost of flexible PCBs, let’s compare the prices of various flexible PCB configurations based on different factors.
Material and Layer Count
Material | 1 Layer | 2 Layers | 4 Layers |
---|---|---|---|
Polyimide | $10-$20 | $20-$40 | $40-$80 |
Polyester | $5-$15 | $15-$30 | $30-$60 |
Prices are per square inch and may vary based on other factors.
Quantity and Lead Time
Quantity | 1-2 Weeks Lead Time | 3-4 Weeks Lead Time |
---|---|---|
100 | $10-$20 | $8-$15 |
500 | $8-$15 | $6-$12 |
1000 | $6-$12 | $4-$10 |
Prices are per unit and may vary based on other factors.
Manufacturing Process
Process | Cost Comparison |
---|---|
Subtractive | Lower cost |
Additive | Higher cost |
Actual costs depend on design complexity and other factors.
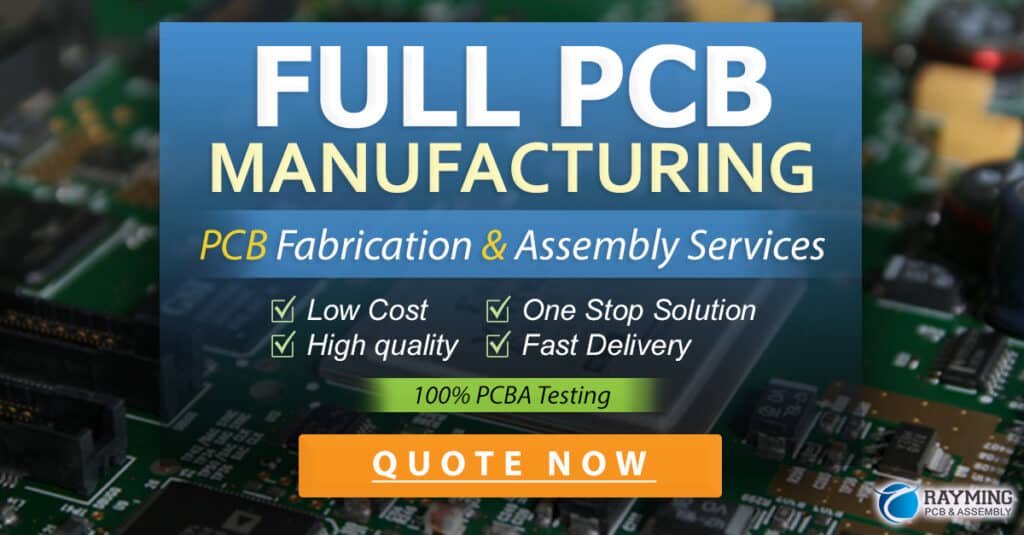
Flexible PCB Cost Optimization Strategies
To minimize the cost of your flexible PCBs without compromising on quality or functionality, consider the following strategies:
-
Simplify your design: Reduce the number of layers, minimize via and hole sizes, and opt for larger trace widths and spacing whenever possible.
-
Choose the right materials: Select materials that balance cost and performance based on your application requirements. Consider using lower-cost alternatives like polyester when appropriate.
-
Optimize panel utilization: Work with your manufacturer to maximize the number of circuits per panel, reducing material waste and lowering costs.
-
Plan ahead: Longer lead times generally result in lower costs. Plan your project timeline accordingly to take advantage of these savings.
-
Consider standardization: Using standardized designs and components can help reduce costs by leveraging economies of scale and minimizing custom manufacturing requirements.
Frequently Asked Questions (FAQ)
-
What is the average cost of a flexible PCB?
The average cost of a flexible PCB can vary greatly depending on factors such as material, layer count, complexity, and quantity. Prices can range from a few dollars to several hundred dollars per unit. -
Are flexible PCBs more expensive than rigid PCBs?
Yes, flexible PCBs are generally more expensive than rigid PCBs due to the specialized materials, manufacturing processes, and design considerations involved. -
How can I reduce the cost of my flexible PCB project?
To reduce the cost of your flexible PCB project, simplify your design, choose cost-effective materials, optimize panel utilization, plan for longer lead times, and consider standardization where possible. -
Do I need special certifications for my flexible PCBs?
The need for special certifications depends on your application and industry. Some common certifications include UL, IPC, MIL-PRF-31032, and ISO 9001. Consult with your manufacturer or industry experts to determine which certifications are necessary for your project. -
How do I choose the right manufacturer for my flexible PCB project?
When choosing a manufacturer for your flexible PCB project, consider factors such as experience, capabilities, quality control processes, certifications, and customer support. Request quotes from multiple manufacturers and evaluate their offerings based on your specific project requirements and budget.
Conclusion
Flexible PCBs offer numerous benefits, including reduced weight, improved reliability, and enhanced design flexibility. However, understanding the factors that influence their cost is crucial for making informed decisions and optimizing your project budget. By considering material selection, circuit complexity, quantity and lead time, manufacturing process, and testing and certification requirements, you can effectively manage the cost of your flexible PCB project.
Remember to work closely with your chosen manufacturer to leverage their expertise and optimize your design for cost-effectiveness. By following the strategies outlined in this guide and staying informed about the latest developments in flexible PCB technology, you can successfully navigate the world of flexible PCB cost and bring your innovative projects to life.
No responses yet