Introduction to Flexible Circuit Design
Flexible circuits, also known as flex circuits or flexible printed circuit boards (FPCBs), have revolutionized the electronics industry by providing a versatile and reliable solution for connecting electronic components in a wide range of applications. From consumer electronics to medical devices, aerospace, and automotive industries, flexible circuits offer numerous advantages over traditional rigid PCBs, including reduced weight, improved durability, and enhanced design flexibility.
When designing flexible circuits, there are several crucial factors that engineers and designers must consider to ensure optimal performance, reliability, and manufacturability. This article will explore nine essential aspects of flexible circuit design, providing insights and best practices to help you create successful and cost-effective flexible circuits for your projects.
What is a Flexible Circuit?
A flexible circuit is a type of printed circuit board that consists of a thin, flexible substrate made of materials such as polyimide or polyester. Conductive traces, typically made of copper, are printed or etched onto the substrate to create the desired circuit pattern. Flexible circuits can be single-sided, double-sided, or multi-layered, depending on the complexity of the design and the application requirements.
The main advantages of flexible circuits include:
- Reduced weight and space: Flexible circuits are thinner and lighter than rigid PCBs, making them ideal for applications where weight and space are critical factors.
- Increased durability: The flexible nature of the substrate allows the circuit to withstand repeated bending, twisting, and flexing without damaging the conductive traces or components.
- Improved design flexibility: Flexible circuits can be designed to fit into complex shapes and tight spaces, enabling more compact and efficient packaging of electronic components.
- Enhanced signal integrity: The reduced distance between components and the ability to control impedance in flexible circuits can lead to improved signal integrity and reduced electromagnetic interference (EMI).
The 9 Factors to Consider in Flexible Circuit Design
1. Material Selection
Choosing the right materials for your flexible circuit is crucial for ensuring its performance, reliability, and longevity. The most common substrate materials for flexible circuits are polyimide and polyester. Polyimide is known for its excellent thermal and chemical resistance, making it suitable for high-temperature applications. Polyester, on the other hand, is more cost-effective and offers good flexibility and durability.
When selecting the conductive material, copper is the most widely used option due to its excellent electrical conductivity and cost-effectiveness. However, in some cases, other materials such as silver, gold, or aluminum may be used for specific applications or to improve corrosion resistance.
2. Bend Radius and Flexibility
One of the key considerations in flexible circuit design is the bend radius, which refers to the minimum radius at which the circuit can be bent without causing damage to the conductive traces or compromising its performance. The bend radius is determined by factors such as the substrate material, the thickness of the circuit, and the size and spacing of the conductive traces.
To ensure optimal flexibility and durability, designers should adhere to the recommended minimum bend radius for the chosen substrate material and thickness. Additionally, it is essential to consider the expected number of flexing cycles the circuit will undergo during its lifetime and design accordingly.
3. Circuit Layout and Trace Routing
The layout and routing of conductive traces on a flexible circuit play a significant role in its performance and manufacturability. When designing the circuit layout, engineers should consider factors such as signal integrity, EMI, and crosstalk. Proper trace spacing and width, as well as the use of ground planes and shielding, can help minimize these issues.
In addition to electrical considerations, designers must also take into account the mechanical aspects of the circuit layout. Traces should be routed to avoid areas of high stress or repeated bending, and the use of strain relief features such as curves and serpentine patterns can help distribute stress evenly across the circuit.
4. Adhesive Selection
Adhesives play a crucial role in bonding the layers of a flexible circuit together and attaching components to the substrate. The choice of adhesive will depend on factors such as the substrate material, the operating temperature range, and the environmental conditions the circuit will be exposed to.
Common adhesives used in flexible circuits include:
- Acrylic: Offers good bonding strength and flexibility, suitable for general-purpose applications.
- Epoxy: Provides excellent chemical and temperature resistance, ideal for harsh environments.
- Pressure-sensitive adhesive (PSA): Allows for easy assembly and disassembly of components, suitable for prototyping and low-volume production.
5. Coverlay and Stiffener Design
Coverlay and stiffeners are additional layers added to flexible circuits to provide protection, insulation, and mechanical support. Coverlay is a thin, insulating layer that is laminated over the conductive traces to protect them from damage and prevent short circuits. Stiffeners are used to reinforce specific areas of the circuit, such as connector locations or component mounting sites, to improve mechanical stability and prevent excessive flexing.
When designing coverlay and stiffeners, engineers should consider factors such as the material properties, thickness, and shape to ensure optimal performance and reliability. The use of selective stiffening techniques, such as adding stiffeners only in high-stress areas, can help maintain the overall flexibility of the circuit while providing necessary support.
6. Component Selection and Placement
The selection and placement of components on a flexible circuit are critical for ensuring proper functionality and reliability. When choosing components for a flexible circuit, designers should consider factors such as package type, size, and compatibility with the substrate material and manufacturing processes.
Surface-mount devices (SMDs) are the most commonly used components in flexible circuits due to their small size and compatibility with automated assembly processes. However, in some cases, through-hole components may be necessary for specific applications or to provide additional mechanical strength.
Component placement should be optimized to minimize the overall size of the circuit, reduce signal path lengths, and avoid areas of high stress or repeated bending. The use of 3D modeling tools can help designers visualize the component layout and ensure proper fit and clearance in the final assembly.
7. Manufacturing Process Considerations
When designing a flexible circuit, it is essential to consider the manufacturing processes involved and ensure that the design is optimized for manufacturability. The most common manufacturing processes for flexible circuits include:
- Etching: The process of removing unwanted copper from the substrate to create the desired circuit pattern.
- Lamination: Bonding the layers of the flexible circuit together using heat and pressure.
- Drilling and cutting: Creating holes and openings in the circuit for component mounting and interconnections.
- Solder mask and legend printing: Applying a protective layer over the conductive traces and printing identifying marks on the circuit.
Designers should collaborate closely with the manufacturing team to ensure that the design is compatible with the available processes and equipment. Design for manufacturing (DFM) guidelines should be followed to minimize potential issues and improve yields.
8. Testing and Validation
Thorough testing and validation are essential for ensuring the performance, reliability, and durability of a flexible circuit. Engineers should develop a comprehensive testing plan that includes both electrical and mechanical tests to verify the circuit’s functionality and robustness.
Electrical tests may include continuity, insulation resistance, and signal integrity measurements, while mechanical tests may involve bending, twisting, and environmental exposure to simulate real-world conditions. The use of accelerated life testing (ALT) techniques can help predict the long-term reliability of the circuit and identify potential failure modes.
9. Cost Optimization
Cost optimization is a critical factor in flexible circuit design, as it directly impacts the overall profitability and competitiveness of the end product. Designers should strive to balance performance, reliability, and cost by making informed decisions throughout the design process.
Some strategies for cost optimization in flexible circuit design include:
- Minimizing the use of expensive materials, such as gold or high-performance substrates, unless absolutely necessary.
- Optimizing the circuit layout to reduce the overall size and complexity of the circuit.
- Leveraging standardized components and processes whenever possible to reduce manufacturing costs.
- Collaborating with suppliers and manufacturing partners to identify cost-saving opportunities and negotiate favorable pricing.
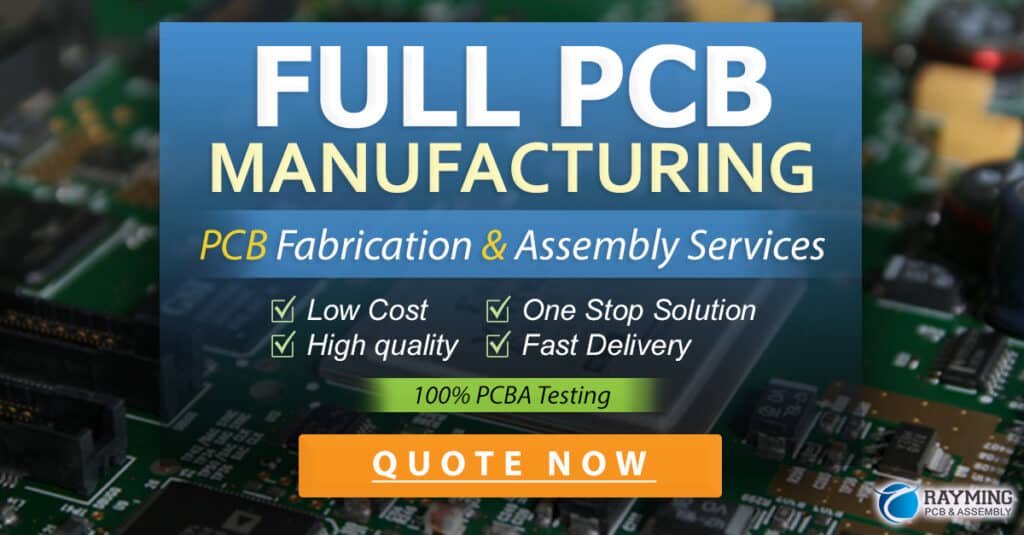
FAQ
1. What is the difference between a flexible circuit and a rigid PCB?
A flexible circuit is a type of printed circuit board that uses a thin, flexible substrate material, such as polyimide or polyester, instead of the rigid FR-4 substrate used in traditional PCBs. This allows flexible circuits to bend, twist, and conform to complex shapes, making them ideal for applications where flexibility and compact packaging are essential.
2. Can flexible circuits be used in high-temperature applications?
Yes, flexible circuits can be designed for high-temperature applications by selecting appropriate substrate materials, such as polyimide, which offers excellent thermal stability. However, designers must also consider the temperature ratings of the components, adhesives, and other materials used in the circuit to ensure reliable performance in high-temperature environments.
3. How do I determine the appropriate bend radius for my flexible circuit?
The appropriate bend radius for a flexible circuit depends on several factors, including the substrate material, thickness, and the size and spacing of the conductive traces. Manufacturers typically provide recommended minimum bend radii for their substrate materials, which should be followed to prevent damage to the circuit. In general, a bend radius of 6-10 times the circuit thickness is considered safe for most applications.
4. What are the advantages of using flexible circuits over traditional wiring?
Flexible circuits offer several advantages over traditional wiring, including reduced weight and space requirements, increased durability and reliability, and improved signal integrity. Flexible circuits also enable more compact and efficient packaging of electronic components, making them ideal for applications where size and weight are critical factors, such as in aerospace, medical devices, and wearable electronics.
5. How can I ensure the manufacturability of my flexible circuit design?
To ensure the manufacturability of your flexible circuit design, it is essential to collaborate closely with your manufacturing partners and adhere to design for manufacturing (DFM) guidelines. This includes considering factors such as minimum feature sizes, trace spacing and width, pad sizes, and component placement. Designers should also optimize the circuit layout to minimize complexity and reduce the overall size of the circuit, while ensuring compatibility with the available manufacturing processes and equipment.
Conclusion
Flexible circuits offer a versatile and reliable solution for connecting electronic components in a wide range of applications, from consumer electronics to medical devices, aerospace, and automotive industries. When designing flexible circuits, engineers and designers must consider several critical factors to ensure optimal performance, reliability, and manufacturability.
These factors include material selection, bend radius and flexibility, circuit layout and trace routing, adhesive selection, coverlay and stiffener design, component selection and placement, manufacturing process considerations, testing and validation, and cost optimization.
By understanding and addressing these key aspects of flexible circuit design, engineers can create successful and cost-effective solutions that meet the unique requirements of their projects. As the demand for compact, lightweight, and flexible electronics continues to grow, the importance of flexible circuit design will only continue to increase, making it an essential skill for engineers and designers in the modern electronics industry.
No responses yet