Introduction to Flexible Circuitry
Flexible circuitry, also known as flex circuits or flexible printed circuit boards (FPCBs), is a revolutionary technology that has transformed the electronics industry. Unlike traditional rigid printed circuit boards (PCBs), flexible circuits are designed to bend, twist, and conform to various shapes and sizes without compromising their electrical functionality. This unique characteristic has opened up a world of possibilities for product designers, enabling them to create more compact, lightweight, and versatile electronic devices.
What is Flexible Circuitry?
Flexible circuitry is a type of printed circuit board that consists of a thin, flexible substrate, typically made of polyimide or other flexible materials, with conductive traces and components attached to it. The substrate is usually made of multiple layers, with each layer serving a specific purpose, such as signal routing, power distribution, or shielding. The conductive traces are typically made of copper and are etched or printed onto the substrate using various methods, such as photolithography or screen printing.
Advantages of Flexible Circuitry
Flexible circuitry offers several advantages over traditional rigid PCBs, including:
-
Flexibility and Conformability: Flex circuits can bend, twist, and conform to various shapes and sizes, making them ideal for applications where space is limited or where the device needs to fit into a specific form factor.
-
Lightweight and Compact: Flex circuits are much thinner and lighter than rigid PCBs, which makes them ideal for portable and wearable devices, as well as aerospace and military applications where weight and size are critical factors.
-
Improved Reliability: Flex circuits are more resistant to vibration, shock, and thermal stress than rigid PCBs, which makes them more reliable and durable in harsh environments.
-
Reduced Assembly Costs: Flex circuits can be designed to replace multiple rigid PCBs and connectors, which reduces the number of components and simplifies the assembly process, resulting in lower manufacturing costs.
-
Enhanced Signal Integrity: Flex circuits can be designed with controlled impedance and shielding, which helps to reduce signal noise and improve signal integrity, especially in high-speed applications.
Applications of Flexible Circuitry
Flexible circuitry has found its way into a wide range of applications, from consumer electronics to medical devices, automotive systems, and aerospace and military equipment. Some of the most common applications include:
Consumer Electronics
Flex circuits are widely used in consumer electronics, such as smartphones, tablets, laptops, and wearable devices. They enable manufacturers to create thinner, lighter, and more compact devices with improved functionality and reliability. For example, the camera module in a smartphone typically uses a flex circuit to connect the image sensor to the main board, allowing for a more compact and lightweight design.
Medical Devices
Flex circuits are also used in various medical devices, such as implantable devices, diagnostic equipment, and surgical tools. They enable manufacturers to create smaller, more flexible, and more reliable devices that can withstand the harsh environment of the human body. For example, a pacemaker uses a flex circuit to connect the battery and electronics to the leads that stimulate the heart, allowing for a more compact and reliable design.
Automotive Systems
Flex circuits are increasingly being used in automotive systems, such as infotainment systems, sensors, and electronic control units (ECUs). They enable manufacturers to create more compact and lightweight systems that can withstand the harsh environment of a vehicle, including extreme temperatures, vibrations, and shocks. For example, a flex circuit can be used to connect multiple sensors and ECUs in a vehicle, reducing the number of connectors and cables required and improving reliability.
Aerospace and Military Equipment
Flex circuits are also used in aerospace and military equipment, such as satellites, aircraft, and defense systems. They enable manufacturers to create more compact, lightweight, and reliable systems that can withstand the extreme conditions of space and combat. For example, a satellite uses flex circuits to connect the solar panels to the power management system, reducing weight and improving reliability.
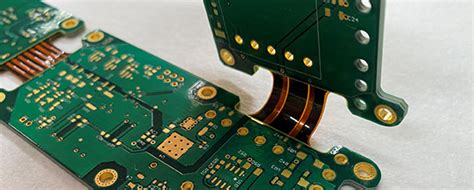
Manufacturing Process of Flexible Circuitry
The manufacturing process of flexible circuitry is similar to that of rigid PCBs, but with some key differences. The basic steps involved in the manufacturing process include:
-
Design and Layout: The first step in the manufacturing process is to design and layout the flex circuit using specialized software tools. The design must take into account the mechanical and electrical requirements of the application, as well as the manufacturing capabilities of the supplier.
-
Substrate Preparation: The next step is to prepare the flexible substrate, typically made of polyimide or other flexible materials. The substrate is cleaned and treated to improve adhesion and prevent delamination.
-
Copper Deposition: A thin layer of copper is then deposited onto the substrate using various methods, such as electroplating, sputtering, or lamination. The copper layer is typically between 18 and 70 microns thick, depending on the application.
-
Patterning: The copper layer is then patterned using photolithography or other methods to create the desired circuit pattern. The unwanted copper is etched away, leaving the conductive traces and pads.
-
Coverlay Application: A coverlay, typically made of polyimide or other flexible materials, is then applied over the circuit pattern to protect the traces and pads from damage and provide electrical insulation.
-
Component Assembly: The final step is to assemble the components onto the flex circuit using various methods, such as surface mount technology (SMT), wire bonding, or flip-chip bonding. The assembled flex circuit is then tested and inspected for quality and functionality.
Manufacturing Process | Description |
---|---|
Design and Layout | Design and layout the flex circuit using specialized software tools |
Substrate Preparation | Prepare the flexible substrate, typically made of polyimide or other flexible materials |
Copper Deposition | Deposit a thin layer of copper onto the substrate using various methods |
Patterning | Pattern the copper layer using photolithography or other methods to create the desired circuit pattern |
Coverlay Application | Apply a coverlay over the circuit pattern to protect the traces and pads from damage and provide electrical insulation |
Component Assembly | Assemble the components onto the flex circuit using various methods and test for quality and functionality |
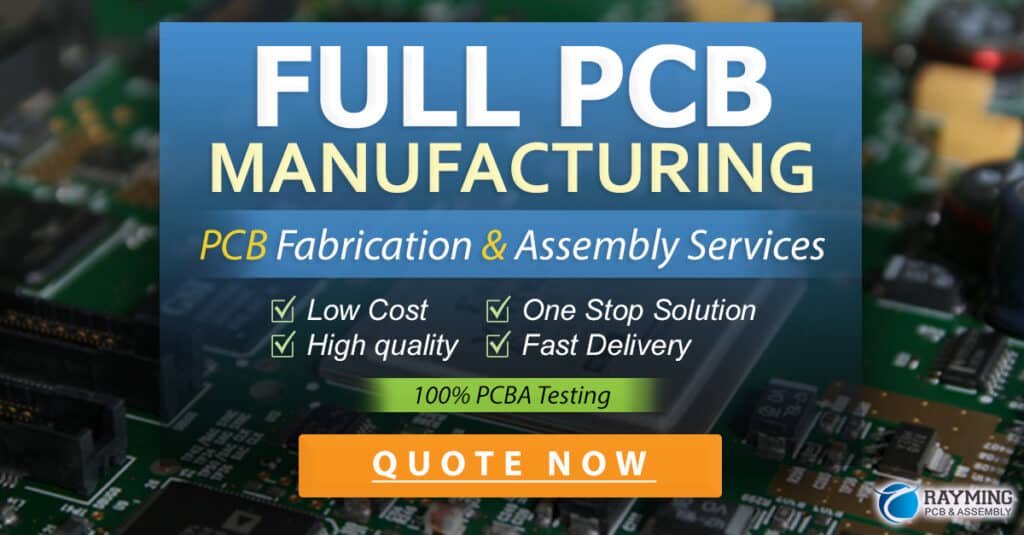
Challenges and Future Trends in Flexible Circuitry
Despite the many advantages of flexible circuitry, there are still some challenges and limitations that need to be addressed. Some of the key challenges include:
-
Material Selection: The selection of materials for flex circuits is critical to ensure the desired mechanical and electrical properties, as well as compatibility with the manufacturing process and end-use environment. The materials must be able to withstand the stresses and strains of bending and twisting, as well as the environmental conditions of the application.
-
Manufacturing Complexity: The manufacturing process of flex circuits is more complex than that of rigid PCBs, requiring specialized equipment and expertise. The thin and flexible nature of the substrate and coverlay materials makes them more prone to damage and defects during handling and processing.
-
Cost: The cost of flex circuits is typically higher than that of rigid PCBs due to the specialized materials and manufacturing processes required. However, the cost can be offset by the reduced assembly costs and improved reliability and functionality of the end product.
Despite these challenges, the future of flexible circuitry looks bright, with several emerging trends and technologies that are expected to drive growth and innovation in the industry. Some of the key trends include:
-
Wearable Electronics: The demand for wearable electronics, such as smartwatches, fitness trackers, and medical devices, is expected to continue to grow, driving the need for more flexible and conformable circuits that can be integrated into clothing and accessories.
-
5G and IoT: The rollout of 5G networks and the growth of the Internet of Things (IoT) are expected to drive the need for more compact, lightweight, and reliable electronic devices that can be deployed in a wide range of environments and applications.
-
Printed Electronics: The development of printed electronics technologies, such as inkjet printing and screen printing, is expected to enable the production of low-cost, high-volume flex circuits for applications such as smart packaging, displays, and sensors.
-
Advanced Materials: The development of new materials, such as graphene and carbon nanotubes, is expected to enable the production of more flexible, stretchable, and conductive circuits that can be used in a wide range of applications, from wearable electronics to soft robotics.
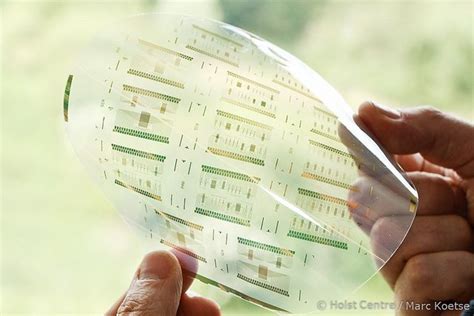
FAQ
1. What is the difference between a flex circuit and a rigid PCB?
The main difference between a flex circuit and a rigid PCB is the substrate material. Flex circuits use a thin, flexible substrate, typically made of polyimide or other flexible materials, while rigid PCBs use a rigid substrate, typically made of fiberglass or other rigid materials. Flex circuits can bend, twist, and conform to various shapes and sizes, while rigid PCBs are fixed in shape and size.
2. What are the advantages of using flex circuits?
The advantages of using flex circuits include:
- Flexibility and conformability, enabling more compact and lightweight designs
- Improved reliability and durability in harsh environments
- Reduced assembly costs and simplified manufacturing processes
- Enhanced signal integrity and reduced noise in high-speed applications
3. What are the typical applications of flex circuits?
Flex circuits are used in a wide range of applications, including:
- Consumer electronics, such as smartphones, tablets, and wearable devices
- Medical devices, such as implantable devices, diagnostic equipment, and surgical tools
- Automotive systems, such as infotainment systems, sensors, and electronic control units
- Aerospace and military equipment, such as satellites, aircraft, and defense systems
4. What are the challenges in manufacturing flex circuits?
The challenges in manufacturing flex circuits include:
- Material selection, ensuring the desired mechanical and electrical properties and compatibility with the manufacturing process and end-use environment
- Manufacturing complexity, requiring specialized equipment and expertise to handle the thin and flexible materials
- Cost, typically higher than rigid PCBs due to the specialized materials and manufacturing processes required
5. What are the future trends in flexible circuitry?
The future trends in flexible circuitry include:
- Wearable electronics, driving the need for more flexible and conformable circuits that can be integrated into clothing and accessories
- 5G and IoT, driving the need for more compact, lightweight, and reliable electronic devices that can be deployed in a wide range of environments and applications
- Printed electronics, enabling the production of low-cost, high-volume flex circuits for applications such as smart packaging, displays, and sensors
- Advanced materials, such as graphene and carbon nanotubes, enabling the production of more flexible, stretchable, and conductive circuits for a wide range of applications
Conclusion
Flexible circuitry is a revolutionary technology that has transformed the electronics industry, enabling the creation of more compact, lightweight, and versatile electronic devices. With its unique characteristics of flexibility, conformability, and improved reliability, flex circuits have found their way into a wide range of applications, from consumer electronics to medical devices, automotive systems, and aerospace and military equipment.
Despite the challenges in manufacturing and material selection, the future of flexible circuitry looks bright, with several emerging trends and technologies that are expected to drive growth and innovation in the industry. From wearable electronics to 5G and IoT, printed electronics, and advanced materials, flex circuits are poised to play a critical role in shaping the future of electronics.
As product designers and engineers continue to push the boundaries of what is possible with flexible circuitry, we can expect to see more innovative and transformative applications in the years to come. Whether it’s a smartwatch that can monitor our health, a medical device that can improve our quality of life, or a satellite that can explore the frontiers of space, flexible circuitry will be at the heart of these innovations, enabling us to create a better, smarter, and more connected world.
No responses yet