Introduction to Flexible Circuitry
Flexible circuitry, also known as flex circuits or flexible printed circuit boards (FPCBs), is a revolutionary technology that has transformed the electronics industry. Unlike traditional rigid printed circuit boards (PCBs), flexible circuits are designed to bend, twist, and conform to various shapes and sizes without compromising their electrical functionality. This unique characteristic has opened up a world of possibilities for electronic device design, enabling the creation of more compact, lightweight, and versatile products.
In this comprehensive article, we will delve into the world of flexible circuitry, exploring its definition, manufacturing process, advantages, applications, and future prospects. By the end of this piece, you will have a thorough understanding of why flexible circuitry is a game-changer in the electronics industry and why it is becoming increasingly essential for modern electronic devices.
What is Flexible Circuitry?
Flexible circuitry is a type of printed circuit board that consists of a thin, flexible substrate made from materials such as polyimide, polyester, or other polymers. These substrates are laminated with conductive traces, typically made of copper, which carry electrical signals between various components. The flexibility of the substrate allows the circuit to bend, fold, and twist without breaking or losing its electrical properties.
Key Components of Flexible Circuits
- Substrate: The base material that provides the flexibility and support for the conductive traces. Common substrates include polyimide, polyester, and other polymers.
- Conductive Traces: Thin layers of metal, usually copper, that are laminated onto the substrate to carry electrical signals between components.
- Cover Layer: An insulating layer that protects the conductive traces from damage and provides electrical insulation.
- Adhesive: A bonding agent that helps to laminate the conductive traces and cover layer to the substrate.
Types of Flexible Circuits
There are three main types of flexible circuits, each with its own unique characteristics and applications:
- Single-sided Flex Circuits: These circuits have conductive traces on only one side of the substrate. They are the simplest and most cost-effective type of flexible circuit.
- Double-sided Flex Circuits: These circuits have conductive traces on both sides of the substrate, allowing for more complex designs and higher component density.
- Multi-layer Flex Circuits: These circuits consist of multiple layers of substrates and conductive traces, providing even greater design flexibility and component density. They are the most complex and expensive type of flexible circuit.
Manufacturing Process of Flexible Circuits
The manufacturing process of flexible circuits is similar to that of rigid PCBs, with a few key differences to accommodate the flexible nature of the substrate. The process typically involves the following steps:
- Design: The circuit layout is designed using computer-aided design (CAD) software, taking into account the specific requirements of the application, such as bend radius, component placement, and signal integrity.
- Substrate Preparation: The flexible substrate is cleaned and treated to ensure proper adhesion of the conductive traces.
- Lamination: The conductive traces, usually made of copper, are laminated onto the substrate using heat and pressure.
- Etching: The unwanted copper is removed using a chemical etching process, leaving only the desired conductive traces.
- Cover Layer Application: An insulating cover layer is applied to protect the conductive traces and provide electrical insulation.
- Cutting and Drilling: The flexible circuit is cut to the desired shape and size, and any necessary holes are drilled for component placement.
- Component Assembly: Electronic components are attached to the flexible circuit using various methods, such as surface mount technology (SMT) or through-hole mounting.
- Testing and Inspection: The completed flexible circuit undergoes rigorous testing and inspection to ensure proper functionality and reliability.
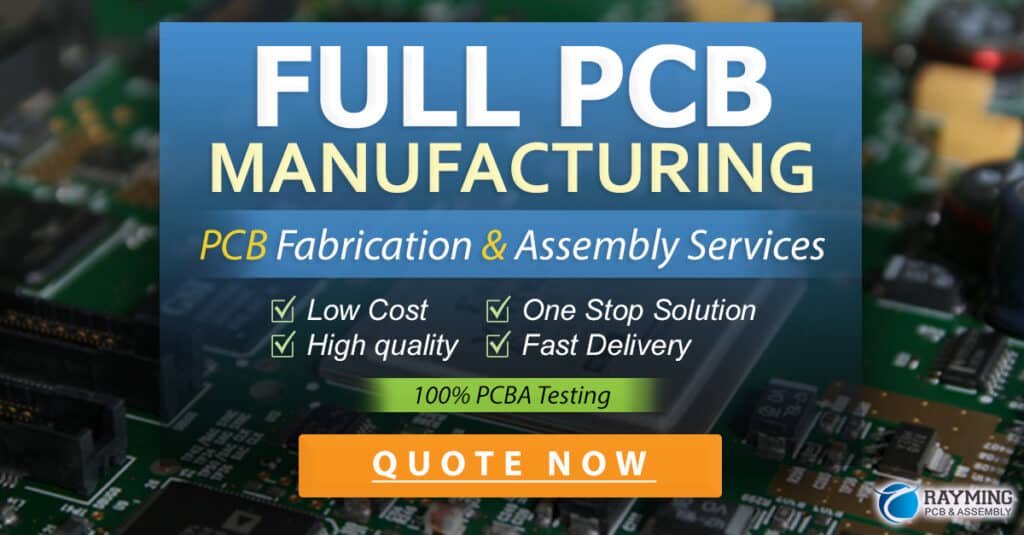
Advantages of Flexible Circuitry
Flexible circuitry offers numerous advantages over traditional rigid PCBs, making it an attractive choice for a wide range of applications. Some of the key benefits include:
- Space Savings: Flexible circuits can be folded, bent, and twisted to fit into tight spaces, allowing for more compact and lightweight electronic devices.
- Improved Reliability: The ability to bend and flex without breaking or losing electrical functionality makes flexible circuits more resistant to vibration, shock, and other mechanical stresses.
- Enhanced Design Freedom: The conformability of flexible circuits allows designers to create more innovative and ergonomic products that can adapt to various shapes and contours.
- Reduced Assembly Costs: Flexible circuits can simplify the assembly process by reducing the number of connectors and wires needed, leading to lower assembly costs and faster production times.
- Increased Durability: Flexible circuits are highly resistant to extreme temperatures, chemicals, and other environmental factors, making them suitable for use in harsh conditions.
- Better Signal Integrity: The shorter signal paths and reduced noise interference in flexible circuits can lead to improved signal integrity and higher-speed performance.
Applications of Flexible Circuitry
Flexible circuitry has found its way into a wide range of industries and applications, thanks to its unique properties and advantages. Some of the most common applications include:
- Wearable Electronics: Flexible circuits are essential for creating comfortable, form-fitting wearable devices such as smartwatches, fitness trackers, and medical monitoring devices.
- Medical Devices: The biocompatibility and flexibility of certain substrate materials make flexible circuits ideal for use in implantable medical devices, such as pacemakers, hearing aids, and drug delivery systems.
- Automotive Electronics: Flexible circuits are used in various automotive applications, such as instrument clusters, seat sensors, and infotainment systems, where space constraints and reliability are critical factors.
- Aerospace and Defense: The lightweight and durable nature of flexible circuits makes them suitable for use in aerospace and defense applications, such as satellite systems, aircraft avionics, and military communications equipment.
- Consumer Electronics: Flexible circuits are increasingly used in consumer electronic devices, such as smartphones, tablets, and laptops, to enable slimmer designs and improved functionality.
- Industrial Automation: Flexible circuits are used in industrial automation systems, such as robotics and machine vision, where their ability to withstand harsh environments and mechanical stresses is critical.
Future of Flexible Circuitry
As technology continues to advance, the demand for flexible circuitry is expected to grow significantly. Some of the key trends and developments that are shaping the future of flexible circuitry include:
- Advanced Materials: Researchers are continually developing new substrate materials with improved flexibility, durability, and electrical properties, opening up new possibilities for Flexible Circuit Design.
- Stretchable Electronics: The development of stretchable conductive materials and substrates is enabling the creation of even more conformable and adaptable electronic devices.
- 3D Printing: The integration of 3D printing technology with flexible circuit manufacturing is allowing for the rapid prototyping and production of complex, three-dimensional flexible circuits.
- Internet of Things (IoT): The growing demand for connected devices in the IoT ecosystem is driving the need for more compact, flexible, and reliable electronic components, including flexible circuits.
- Sustainable Electronics: The use of biodegradable and recyclable materials in flexible circuit manufacturing is becoming increasingly important as the industry moves towards more sustainable and eco-friendly practices.
Frequently Asked Questions (FAQ)
-
What is the difference between flexible circuits and rigid PCBs?
Flexible circuits are made from thin, flexible substrates that can bend and twist without breaking or losing electrical functionality, while rigid PCBs are made from rigid, non-flexible materials such as fiberglass or epoxy. -
Can flexible circuits be repaired if damaged?
Yes, flexible circuits can be repaired, but the process is more complex than repairing rigid PCBs. Specialized equipment and techniques are required to ensure proper bonding and electrical functionality. -
How long do flexible circuits last?
The lifespan of a flexible circuit depends on various factors, such as the materials used, the application environment, and the level of mechanical stress experienced. With proper design and manufacturing, flexible circuits can last for many years, even in harsh conditions. -
Are flexible circuits more expensive than rigid PCBs?
In general, flexible circuits are more expensive than rigid PCBs due to the specialized materials and manufacturing processes required. However, the cost difference can be offset by the benefits of increased design flexibility, reduced assembly costs, and improved reliability. -
What are the environmental considerations when using flexible circuits?
The use of certain substrate materials and manufacturing processes in flexible circuits can have environmental implications. However, the industry is moving towards more sustainable practices, such as using biodegradable and recyclable materials, and implementing eco-friendly manufacturing processes.
Conclusion
Flexible circuitry is a cutting-edge technology that has revolutionized the electronics industry, enabling the creation of more compact, lightweight, and versatile devices. With its unique ability to bend, twist, and conform to various shapes and sizes, flexible circuitry offers numerous advantages over traditional rigid PCBs, including space savings, improved reliability, enhanced design freedom, and reduced assembly costs.
As technology continues to advance and the demand for more innovative and adaptable electronic devices grows, the importance of flexible circuitry will only continue to increase. From wearable electronics and medical devices to automotive and aerospace applications, flexible circuits are becoming an essential component in a wide range of industries.
By understanding the basics of flexible circuitry, its manufacturing process, advantages, and applications, you can better appreciate the significance of this technology and its potential to shape the future of electronics. As new materials, manufacturing techniques, and design approaches emerge, the possibilities for flexible circuitry will continue to expand, driving innovation and progress in the ever-evolving world of electronics.
No responses yet