What is a Flex PCB?
A flex PCB, also known as a flexible printed circuit board, is a type of PCB that consists of a thin, flexible plastic substrate with conductive copper traces. Unlike traditional rigid PCBs, flex PCBs can bend, twist, and fold to fit into tight spaces or conform to unique shapes. This makes them ideal for applications where flexibility and space constraints are important factors.
Flex PCBs are commonly used in a wide range of industries, including:
- Consumer electronics (smartphones, wearables, cameras)
- Medical devices (implantable devices, diagnostic equipment)
- Automotive (dashboard displays, sensors)
- Aerospace (avionics, satellite systems)
- Industrial (robotics, automation)
The main advantages of flex PCBs include:
-
Space savings: Flex PCBs can be folded or bent to fit into compact spaces, reducing the overall size of electronic devices.
-
Weight reduction: The thin, lightweight nature of flex PCBs helps to reduce the overall weight of electronic products.
-
Increased reliability: Flex PCBs eliminate the need for connectors and wires, which are common points of failure in electronic systems. This improves reliability and durability.
-
Enhanced design flexibility: The ability to bend and fold flex PCBs allows for more creative and efficient product designs.
-
Improved signal integrity: The shorter signal paths and reduced noise interference in flex PCBs lead to better signal integrity compared to traditional wire assemblies.
Types of Flex PCBs
There are three main types of flex PCBs:
-
Single-sided flex PCBs: These have conductive traces on only one side of the flexible substrate. They are the simplest and most cost-effective type of flex PCB.
-
Double-sided flex PCBs: These have conductive traces on both sides of the substrate, allowing for more complex circuit designs and higher component density.
-
Multi-layer flex PCBs: These consist of multiple layers of flexible substrate with conductive traces, separated by insulating layers. They offer the highest density and complexity but are also the most expensive type of flex PCB.
In addition to these main types, there are also rigid-flex PCBs, which combine rigid and flexible sections in a single board. This allows for even greater design flexibility and the ability to integrate complex electronic systems into a single, compact package.
Flex PCB Manufacturing Process
The manufacturing process for flex PCBs is similar to that of rigid PCBs, but with some key differences to account for the flexible nature of the substrate. The main steps in the flex PCB manufacturing process are:
-
Substrate preparation: The flexible substrate, typically a polyimide or polyester material, is cleaned and treated to improve adhesion of the copper traces.
-
Copper lamination: A thin layer of copper is laminated onto the substrate using heat and pressure.
-
Circuit pattern imaging: The desired circuit pattern is transferred onto the copper layer using photolithography. This involves applying a photoresist layer, exposing it to UV light through a photomask, and developing the resist to remove the unexposed areas.
-
Etching: The exposed copper is etched away using a chemical solution, leaving only the desired circuit pattern.
-
Coverlay application: A protective coverlay is applied over the circuit pattern to insulate and protect the traces.
-
Cutting and drilling: The flex PCB is cut to its final shape and size, and any necessary holes or slots are drilled.
-
Surface finishing: The exposed copper pads are finished with a protective coating, such as gold or tin, to prevent oxidation and improve solderability.
-
Quality control: The finished flex PCB undergoes rigorous testing and inspection to ensure it meets the required specifications and quality standards.
Table: Comparison of Rigid and Flex PCB Manufacturing
Manufacturing Step | Rigid PCB | Flex PCB |
---|---|---|
Substrate Material | FR-4 (glass-reinforced epoxy) | Polyimide or polyester |
Copper Lamination | High pressure and temperature | Lower pressure and temperature |
Circuit Imaging | Photolithography | Photolithography |
Etching | Chemical etching | Chemical etching |
Protective Layer | Solder mask | Coverlay |
Cutting | Mechanical routing or punching | Die cutting or laser cutting |
Drilling | Mechanical drilling | Mechanical drilling or laser drilling |
Surface Finishing | HASL, ENIG, OSP, etc. | ENIG, OSP, immersion gold, etc. |
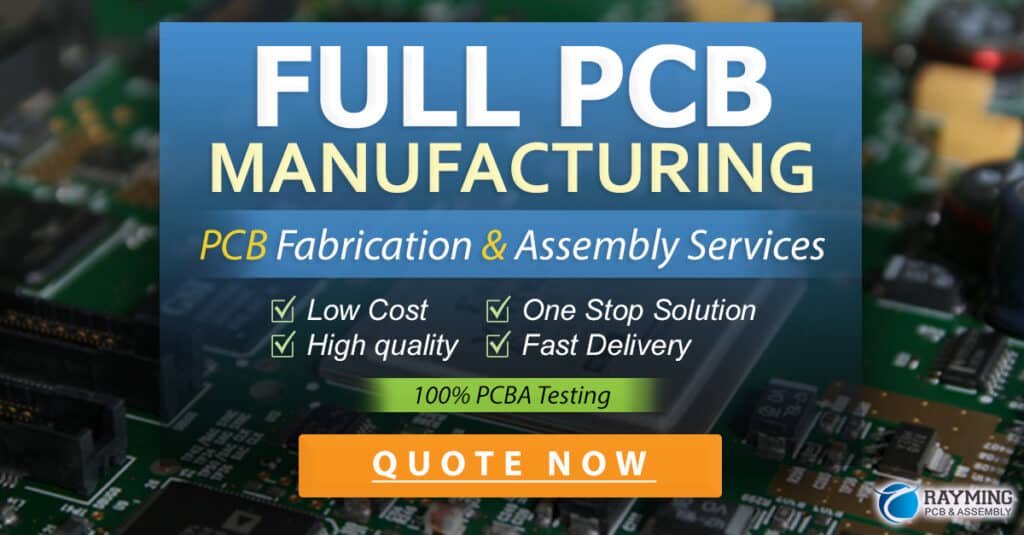
Choosing a Flex PCB Manufacturer
When selecting a flex PCB manufacturer, there are several key factors to consider to ensure you receive high-quality products that meet your specific requirements. These factors include:
-
Experience and expertise: Look for a manufacturer with a proven track record of producing high-quality flex PCBs and experience in your specific industry or application.
-
Manufacturing capabilities: Ensure that the manufacturer has the necessary equipment, processes, and certifications to produce the type and complexity of flex PCBs you require.
-
Quality control: Choose a manufacturer with robust quality control processes and certifications, such as ISO 9001, ISO 14001, and UL.
-
Lead times and pricing: Consider the manufacturer’s lead times and pricing structure to ensure they align with your project timeline and budget.
-
Customer support: Select a manufacturer that offers responsive and knowledgeable customer support to help you through the design and manufacturing process.
Some top flex PCB manufacturers include:
- Flexcom
- Printed Circuits
- Epec Engineered Technologies
- Flexible Circuit Technologies
- All Flex
Flex PCB Design Considerations
Designing a flex PCB requires careful consideration of several factors to ensure optimal performance, reliability, and manufacturability. Some key design considerations include:
-
Bend radius: The minimum bend radius of a flex PCB depends on the substrate material, thickness, and copper weight. It is essential to design the PCB to accommodate the required bend radius without causing damage or affecting performance.
-
Copper weight and trace width: The copper weight and trace width should be selected based on the electrical requirements of the circuit, as well as the mechanical stresses the PCB will experience during bending and flexing.
-
Adhesive selection: The adhesive used to bond the copper to the substrate must be compatible with the substrate material and able to withstand the expected mechanical and environmental stresses.
-
Coverlay design: The coverlay should be designed to provide adequate insulation and protection for the copper traces while allowing for the necessary flexibility.
-
Stiffener placement: Stiffeners can be added to specific areas of the flex PCB to provide additional support and stability where needed.
-
Panelization: Flex PCBs are often panelized to maximize manufacturing efficiency. The panel layout should be designed to minimize waste and ensure proper registration of the individual boards.
Advantages of Working with a Flex PCB Manufacturer
Partnering with an experienced flex PCB manufacturer offers several advantages for your project, including:
-
Design support: Many flex PCB manufacturers offer design assistance and guidance to help optimize your PCB layout for manufacturability and performance.
-
Prototyping services: Manufacturers can provide rapid prototyping services to help you test and validate your design before committing to full-scale production.
-
Cost savings: By working directly with a manufacturer, you can often achieve cost savings through volume pricing, design optimization, and reduced shipping costs.
-
Faster time-to-market: Experienced manufacturers can help streamline the design and production process, reducing lead times and helping you bring your product to market faster.
-
Access to the latest technologies: Flex PCB manufacturers invest in state-of-the-art equipment and processes to stay at the forefront of the industry, giving you access to the latest technologies and capabilities.
FAQ
- What is the typical lead time for flex PCB manufacturing?
-
Lead times can vary depending on the complexity of the design, the selected manufacturer, and the order quantity. Typical lead times range from 2-4 weeks for prototypes and 4-8 weeks for production orders.
-
How do I determine the appropriate bend radius for my flex PCB?
-
The minimum bend radius depends on factors such as the substrate material, thickness, and copper weight. As a general rule, the minimum bend radius should be at least 6 times the thickness of the PCB. Your manufacturer can provide guidance based on your specific design.
-
Can flex PCBs be used in high-temperature environments?
-
Yes, certain substrate materials, such as polyimide, are suitable for high-temperature applications up to 150°C or more. Be sure to discuss your specific temperature requirements with your manufacturer to select the appropriate materials.
-
Are there any limitations on the number of layers in a flex PCB?
-
While there is no theoretical limit to the number of layers in a flex PCB, practical considerations such as thickness, flexibility, and cost typically limit designs to 12 layers or fewer. Consult with your manufacturer to determine the optimal layer count for your application.
-
How do I select the right surface finish for my flex PCB?
- The choice of surface finish depends on factors such as the intended use environment, soldering requirements, and cost. Common surface finishes for flex PCBs include ENIG (Electroless Nickel Immersion Gold), OSP (Organic Solderability Preservative), and immersion gold. Your manufacturer can recommend the best surface finish for your specific application.
Conclusion
Flex PCBs offer a versatile and reliable solution for a wide range of electronic applications, enabling smaller, lighter, and more flexible product designs. By partnering with an experienced flex PCB manufacturer, you can access the expertise, capabilities, and support needed to bring your products to market quickly and cost-effectively.
When selecting a manufacturer, be sure to consider factors such as experience, manufacturing capabilities, quality control, lead times, pricing, and customer support. By carefully evaluating your options and working closely with your chosen manufacturer, you can ensure a successful flex PCB design and manufacturing experience.
No responses yet