What is Flex Board Manufacturing?
Flex board manufacturing, also known as flexible printed circuit board (PCB) manufacturing, is the process of creating flexible electronic circuits on thin, flexible substrates such as polyimide or polyester films. Unlike traditional rigid PCBs, flex boards can bend, twist, and conform to various shapes, making them ideal for applications that require flexibility, durability, and space efficiency.
Flex boards are widely used in various industries, including:
- Consumer electronics (smartphones, wearables, cameras)
- Medical devices (implantable devices, diagnostic equipment)
- Automotive (dashboard displays, sensors)
- Aerospace (avionics, satellite systems)
- Industrial (robotics, automation)
The flex board manufacturing process involves several steps, including:
- Circuit design and layout
- Substrate selection and preparation
- Copper foil lamination
- Photolithography and etching
- Coverlay or solder mask application
- Surface finish (e.g., ENIG, HASL, OSP)
- Cutting and forming
- Testing and inspection
Advantages of Flex Board Manufacturing
Flex boards offer several advantages over traditional rigid PCBs:
Flexibility and Durability
Flex boards can withstand repeated bending and twisting without breaking or losing electrical connectivity. This makes them ideal for applications that require flexing, folding, or rolling, such as wearable devices, foldable displays, or cable assemblies.
Space and Weight Reduction
By eliminating the need for bulky connectors and wires, flex boards can significantly reduce the size and weight of electronic assemblies. This is particularly important in aerospace and automotive applications, where every gram counts.
Improved Signal Integrity
Flex boards can be designed with controlled impedance and shorter signal paths, reducing signal loss, crosstalk, and electromagnetic interference (EMI). This is crucial for high-speed applications, such as 5G networks and high-performance computing.
Cost Efficiency
Although the initial setup costs for flex board manufacturing may be higher than rigid PCBs, the overall cost can be lower due to reduced assembly time, fewer components, and less material waste. Flex boards also enable more efficient automation and testing, further reducing manufacturing costs.
Flex Board Materials and Constructions
Substrates
The most common substrates used in flex board manufacturing are:
- Polyimide (PI): High temperature resistance, excellent mechanical and electrical properties
- Polyester (PET): Lower cost, good flexibility, suitable for low-temperature applications
- Liquid Crystal Polymer (LCP): Ultra-thin, low moisture absorption, excellent high-frequency performance
Copper Foils
Flex boards typically use rolled annealed (RA) copper foils, which are more ductile and less prone to cracking than electrodeposited (ED) copper foils used in rigid PCBs. The copper thickness can range from 9 µm to 70 µm, depending on the current carrying capacity and mechanical requirements.
Coverlays and Solder Masks
Coverlays are thin, flexible insulating films that protect the copper traces and provide electrical insulation. They are typically made of polyimide or polyester and can be applied using adhesive or heat bonding.
Solder masks are used to selectively expose the copper pads for soldering and protect the rest of the circuit from oxidation and contamination. Flex boards often use flexible solder masks, such as photoimageable polyimide or liquid photoimageable solder mask (LPSM).
Stiffeners and Adhesives
Stiffeners are used to selectively reinforce certain areas of the flex board, such as connector zones or component mounting sites. They can be made of rigid materials, such as FR-4, aluminum, or stainless steel, and are attached using pressure-sensitive adhesives (PSA) or thermosetting adhesives.
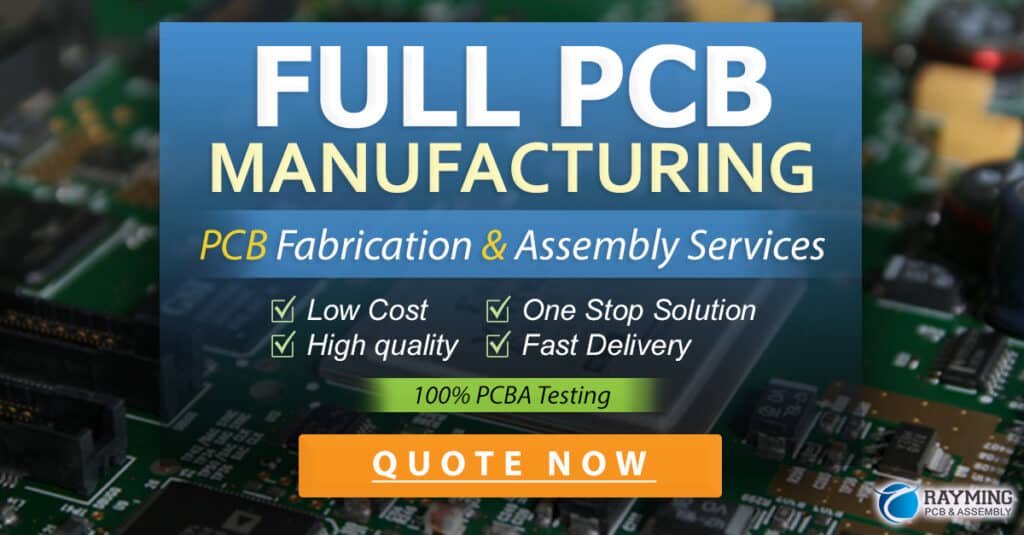
Flex Board Design Considerations
Designing flex boards requires careful consideration of several factors:
Bend Radius and Flexibility
The minimum bend radius depends on the substrate thickness, copper thickness, and coverlay material. As a general rule, the minimum bend radius should be at least 6 times the total thickness of the flex board. Designers should also consider the number of bending cycles and the bend angle to ensure long-term reliability.
Copper Trace Routing
Copper traces on flex boards should be routed perpendicular to the bend axis to minimize stress and prevent cracking. The trace width and spacing should be optimized for flexibility and current carrying capacity. Teardrops and filleted corners can be used to reinforce trace-to-pad connections and prevent copper lifting.
Component Placement
Components should be placed on the neutral axis of the flex board to minimize stress during bending. Stiffeners can be used to support heavy or tall components. Designers should also consider the thermal expansion mismatch between the components and the substrate to prevent solder joint failures.
Interconnections
Flex boards can be connected to rigid boards or other flex boards using various methods, such as:
- Zero Insertion Force (ZIF) connectors
- Flexible Printed Circuit (FPC) connectors
- Soldered connections
- Pressure-sensitive adhesives (PSA)
- Anisotropic Conductive Film (ACF) bonding
The choice of interconnection method depends on the application requirements, such as mating cycles, current carrying capacity, and mechanical stability.
Flex Board Testing and Reliability
Flex boards undergo rigorous testing to ensure their functionality, reliability, and durability. Some common tests include:
Continuity and Isolation Testing
Continuity testing verifies that all the intended connections are present and have low resistance. Isolation testing checks that there are no unintended short circuits between adjacent traces or layers.
Flexing and Bending Tests
Flex boards are subjected to repeated bending cycles to simulate real-world use conditions. The number of cycles and the bend radius are chosen based on the application requirements. The boards are then inspected for cracks, delamination, or other defects.
Environmental Testing
Flex boards are exposed to various environmental stresses, such as:
- Temperature cycling
- Humidity exposure
- Vibration and shock
- Salt spray corrosion
These tests ensure that the flex boards can withstand the expected operating conditions without degradation or failure.
Microsectioning and Cross-Sectional Analysis
Microsectioning involves cutting the flex board along a cross-section and examining the internal structure under a microscope. This technique can reveal any manufacturing defects, such as voids, delamination, or insufficient copper thickness.
Flex Board Manufacturing Process Control
To ensure consistent quality and reliability, flex board manufacturers implement various process control measures:
Design Rule Checking (DRC)
DRC software automatically checks the flex board design against a set of predefined rules, such as minimum trace width, minimum clearance, and copper thickness. This helps catch design errors before manufacturing and prevents costly rework.
Automated Optical Inspection (AOI)
AOI systems use high-resolution cameras and image processing algorithms to inspect the flex boards for defects, such as missing components, solder bridges, or incorrect polarity. AOI can detect defects that are difficult to see with the naked eye and improve the overall quality of the final product.
Statistical Process Control (SPC)
SPC involves collecting and analyzing process data, such as etch rates, copper thickness, or impedance values, to monitor the manufacturing process and identify any trends or anomalies. This helps maintain process stability and reduce variability.
Traceability and Documentation
Flex board manufacturers maintain detailed records of the materials, processes, and test results for each production lot. This traceability enables quick root cause analysis and corrective action in case of any quality issues or customer complaints.
FAQ
Q1: What is the difference between flex boards and rigid PCBs?
A1: Flex boards are made on thin, flexible substrates and can bend and twist without breaking, while rigid PCBs are made on rigid, fiberglass-reinforced substrates and cannot bend. Flex boards offer advantages such as flexibility, durability, space and weight reduction, and improved signal integrity.
Q2: What materials are used in flex board manufacturing?
A2: The most common materials used in flex board manufacturing are polyimide (PI), polyester (PET), and liquid crystal polymer (LCP) for substrates; rolled annealed (RA) copper foils for conductors; and polyimide, polyester, or liquid photoimageable solder mask (LPSM) for coverlays and solder masks.
Q3: How are flex boards connected to other boards or components?
A3: Flex boards can be connected using various methods, such as Zero Insertion Force (ZIF) connectors, Flexible Printed Circuit (FPC) connectors, soldered connections, pressure-sensitive adhesives (PSA), or Anisotropic Conductive Film (ACF) bonding. The choice depends on the application requirements.
Q4: What tests are performed on flex boards to ensure reliability?
A4: Flex boards undergo various tests, such as continuity and isolation testing, flexing and bending tests, environmental testing (temperature cycling, humidity, vibration, shock, salt spray), and microsectioning and cross-sectional analysis. These tests ensure that the flex boards meet the expected performance and durability requirements.
Q5: What are some process control measures used in flex board manufacturing?
A5: Flex board manufacturers use process control measures such as Design Rule Checking (DRC) to catch design errors, Automated Optical Inspection (AOI) to detect manufacturing defects, Statistical Process Control (SPC) to monitor process stability, and traceability and documentation to enable quick root cause analysis and corrective action.
Conclusion
Flex board manufacturing is a complex and demanding process that requires specialized materials, designs, and process controls to ensure reliable and high-performance products. By understanding the advantages, materials, design considerations, testing methods, and process control measures involved in flex board manufacturing, engineers and designers can create innovative and robust solutions for a wide range of applications.
As the demand for smaller, lighter, and more flexible electronic devices continues to grow, flex board manufacturing will play an increasingly important role in enabling the next generation of technology. With continuous advancements in materials, processes, and automation, flex board manufacturers are well-positioned to meet the evolving needs of their customers and drive innovation across various industries.
Characteristic | Flex Boards | Rigid PCBs |
---|---|---|
Substrate | Polyimide, Polyester, LCP | FR-4, Ceramic, Metal |
Flexibility | High | Low |
Durability | High | Moderate |
Space and Weight | Low | High |
Signal Integrity | High | Moderate |
Cost | Moderate to High | Low to Moderate |
Applications | Wearables, Medical, Automotive, Aerospace | Consumer Electronics, Industrial, Telecommunications |
No responses yet