What are Fiberglass Laminates?
Fiberglass laminates are engineered materials that combine the strength and stiffness of fiberglass fabric with the durability and chemical resistance of a polymer resin. The fiberglass fabric acts as the reinforcement, providing the laminate with its structural properties, while the polymer matrix binds the fibers together and protects them from environmental factors.
Fiberglass laminates are widely used in various industries, including:
- Aerospace
- Automotive
- Marine
- Construction
- Wind energy
- Sports equipment
The choice of fiberglass fabric style depends on the specific requirements of the application, such as strength, stiffness, impact resistance, and surface finish.
Types of Fiberglass Fabric Styles
There are several types of fiberglass fabric styles used in laminates, each with its own unique properties and benefits. The most common fiberglass fabric styles include:
Plain Weave
Plain weave is the simplest and most common fiberglass fabric style. It consists of warp and weft fibers that are interlaced in a regular pattern, creating a checkerboard-like appearance. Plain weave fabrics are known for their stability, good drapeability, and balanced mechanical properties.
Property | Description |
---|---|
Weave pattern | Simple, regular pattern |
Drapeability | Good |
Stability | High |
Mechanical properties | Balanced |
Plain weave fabrics are often used in general-purpose applications, such as:
- Boat hulls
- Automotive body panels
- Recreational equipment
- Tanks and containers
Twill Weave
Twill weave fabrics have a diagonal pattern created by the warp fibers passing over two or more weft fibers before going under one. This weave style offers better drapeability and a more aesthetically pleasing surface compared to plain weave fabrics. Twill weave fabrics also provide good mechanical properties and resistance to tear and impact.
Property | Description |
---|---|
Weave pattern | Diagonal |
Drapeability | Excellent |
Stability | Good |
Mechanical properties | Good |
Twill weave fabrics are commonly used in applications that require a combination of strength and aesthetics, such as:
- Aerospace components
- High-performance sports equipment
- Decorative panels
- Furniture
Satin Weave
Satin weave fabrics have a smooth, lustrous surface due to the long float of the warp fibers over several weft fibers. This weave style offers excellent drapeability and conformability, making it suitable for complex shapes and contours. Satin weave fabrics also provide good mechanical properties in the warp direction.
Property | Description |
---|---|
Weave pattern | Smooth, lustrous surface |
Drapeability | Excellent |
Stability | Moderate |
Mechanical properties | Good in warp direction |
Satin weave fabrics are often used in applications that require a high-quality surface finish and good conformability, such as:
- Aerospace components
- Wind turbine blades
- High-performance sports equipment
- Decorative panels
Unidirectional Fabric
Unidirectional (UD) fabrics consist of parallel fibers oriented in a single direction, providing exceptional strength and stiffness in that direction. UD fabrics are often used in combination with other fabric styles to create laminates with tailored mechanical properties.
Property | Description |
---|---|
Fiber orientation | Parallel, single direction |
Drapeability | Poor |
Stability | Low |
Mechanical properties | Excellent in fiber direction |
UD fabrics are commonly used in applications that require high strength and stiffness in a specific direction, such as:
- Aerospace components
- Wind turbine blades
- Pressure vessels
- Structural reinforcement
Multiaxial Fabric
Multiaxial fabrics consist of multiple layers of unidirectional fibers stitched together at various angles, typically 0°, 45°, -45°, and 90°. This fabric style offers excellent mechanical properties in multiple directions and reduces the labor involved in layup compared to using individual UD layers.
Property | Description |
---|---|
Fiber orientation | Multiple angles |
Drapeability | Moderate |
Stability | Good |
Mechanical properties | Excellent in multiple directions |
Multiaxial fabrics are often used in applications that require high strength and stiffness in multiple directions, such as:
- Wind turbine blades
- Pressure vessels
- Automotive components
- Structural reinforcement
Factors Influencing Fabric Style Selection
When selecting a fiberglass fabric style for a laminate, several factors must be considered to ensure the desired performance and properties are achieved. These factors include:
Mechanical Properties
The required mechanical properties, such as strength, stiffness, and impact resistance, will influence the choice of fabric style. For example, applications requiring high strength and stiffness in a specific direction may benefit from UD fabrics, while those needing balanced properties may use plain or twill weave fabrics.
Drapeability and Conformability
The ability of the fabric to conform to complex shapes and contours is essential for many applications. Satin weave and twill weave fabrics offer excellent drapeability, making them suitable for parts with intricate geometries.
Surface Finish
The desired surface finish of the laminate can also influence the fabric style selection. Satin weave fabrics provide a smooth, lustrous surface, while plain weave fabrics have a more textured appearance.
Cost and Production Efficiency
The cost of the fabric and the efficiency of the laminate production process must also be considered. Multiaxial fabrics, for example, can reduce labor costs by eliminating the need to lay up individual UD layers.
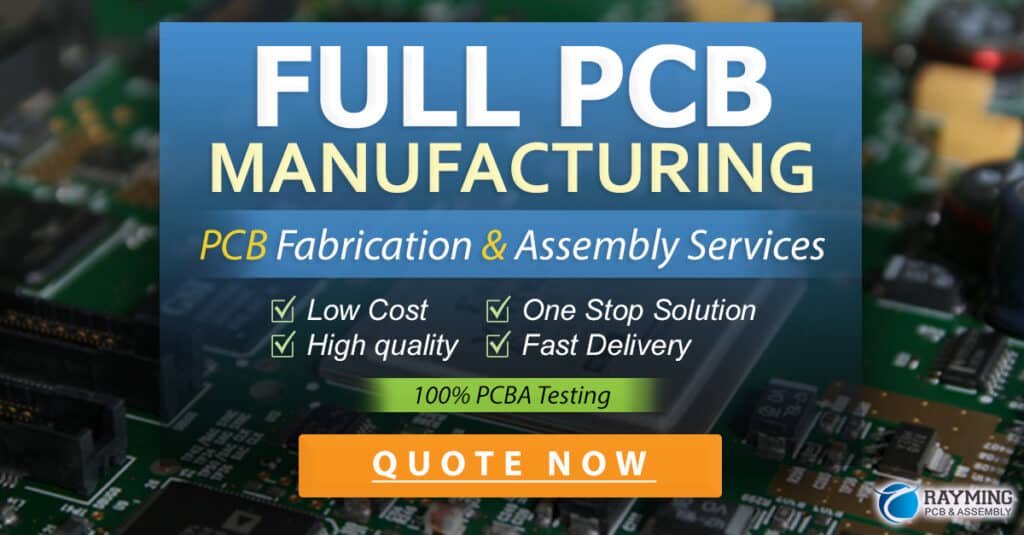
Laminate Fabrication Processes
Fiberglass laminates can be fabricated using various processes, depending on the application, production volume, and required properties. Some common laminate fabrication processes include:
Hand Layup
Hand layup is a manual process in which the fiberglass fabric is placed in a mold, and the polymer resin is applied using rollers or brushes. This process is suitable for low-volume production and complex shapes.
Spray Layup
Spray layup involves spraying a mixture of chopped fiberglass fibers and resin onto a mold using a specialized spray gun. This process is faster than hand layup and suitable for larger parts and higher production volumes.
Vacuum Infusion
Vacuum infusion is a process in which the fiberglass fabric is placed in a mold, and the resin is drawn into the fabric using a vacuum. This process results in high-quality, void-free laminates with consistent resin distribution.
Resin Transfer Molding (RTM)
RTM is a closed-mold process in which the fiberglass fabric is placed in a two-part mold, and the resin is injected under pressure. This process produces high-quality, consistent laminates with excellent surface finish on both sides.
Quality Control and Testing
To ensure the quality and performance of fiberglass laminates, various quality control measures and testing methods are employed. These include:
Visual Inspection
Visual inspection is used to identify surface defects, such as voids, dry spots, and fiber misalignment.
Non-Destructive Testing (NDT)
NDT methods, such as ultrasonic testing and thermography, are used to detect internal defects and inconsistencies in the laminate.
Mechanical Testing
Mechanical testing, such as tensile, flexural, and impact tests, is performed to evaluate the laminate’s strength, stiffness, and toughness.
Physical Property Testing
Physical property tests, such as density, fiber volume fraction, and void content, are conducted to ensure the laminate meets the specified requirements.
Frequently Asked Questions (FAQ)
-
What is the difference between plain weave and twill weave fabrics?
Plain weave fabrics have a simple, checkerboard-like pattern, while twill weave fabrics have a diagonal pattern. Twill weave fabrics offer better drapeability and a more aesthetically pleasing surface compared to plain weave fabrics. -
When should I use unidirectional fabrics in my laminate?
Unidirectional fabrics are best used when high strength and stiffness are required in a specific direction. They are often used in combination with other fabric styles to create laminates with tailored mechanical properties. -
What are the benefits of using multiaxial fabrics?
Multiaxial fabrics offer excellent mechanical properties in multiple directions and reduce the labor involved in layup compared to using individual unidirectional layers. They are often used in applications that require high strength and stiffness in multiple directions. -
How do I choose the right fiberglass fabric style for my application?
When selecting a fiberglass fabric style, consider factors such as the required mechanical properties, drapeability and conformability, desired surface finish, cost, and production efficiency. Consult with a composites expert or supplier to determine the best fabric style for your specific application. -
What quality control measures are used to ensure the performance of fiberglass laminates?
Quality control measures for fiberglass laminates include visual inspection, non-destructive testing (NDT), mechanical testing, and physical property testing. These methods help identify defects, inconsistencies, and ensure that the laminate meets the specified requirements.
Conclusion
Fiberglass fabric styles play a crucial role in determining the mechanical properties, appearance, and performance of fiberglass laminates. By understanding the characteristics and applications of different fabric styles, such as plain weave, twill weave, satin weave, unidirectional, and multiaxial fabrics, engineers and designers can select the most appropriate style for their specific application.
When choosing a fiberglass fabric style, it is essential to consider factors such as mechanical properties, drapeability, surface finish, cost, and production efficiency. By carefully selecting the right fabric style and employing appropriate quality control measures, manufacturers can produce high-quality fiberglass laminates that meet the demanding requirements of various industries, including aerospace, automotive, marine, and wind energy.
As technology advances and new applications emerge, the development of innovative fiberglass fabric styles and laminate fabrication processes will continue to drive the growth and expansion of the composites industry.
No responses yet