Introduction to FastPrintPCB
FastPrintPCB is a revolutionary technology that has transformed the PCB manufacturing industry. It enables the rapid production of high-quality printed circuit boards, significantly reducing lead times and costs. In this article, we will explore the key factors that contribute to creating the perfect FastPrintPCB.
The Importance of PCB Design
Designing for Manufacturability
To achieve the best results with FastPrintPCB, it is crucial to design your PCB with manufacturability in mind. This involves following design guidelines and best practices to ensure that your board can be efficiently manufactured using the FastPrintPCB process.
Using the Right Design Tools
Choosing the right PCB design software is essential for creating designs that are compatible with FastPrintPCB. Popular tools include:
- Altium Designer
- KiCad
- Eagle PCB
These tools offer features specifically tailored for FastPrintPCB, such as design rule checks (DRC) and automated manufacturing file generation.
Optimizing Component Placement
Proper component placement is key to achieving a perfect FastPrintPCB. Consider the following factors:
- Component orientation
- Spacing between components
- Thermal considerations
- Signal integrity
By optimizing component placement, you can minimize manufacturing issues and improve the overall quality of your PCB.
Material Selection for FastPrintPCB
Substrate Materials
The choice of substrate material plays a significant role in the performance and reliability of your FastPrintPCB. Common substrate materials include:
Material | Characteristics |
---|---|
FR-4 | Most widely used, cost-effective, good thermal and mechanical properties |
Rogers | High-frequency applications, low dielectric loss, excellent thermal stability |
Polyimide | Flexible PCBs, high temperature resistance, good chemical stability |
Copper Thickness
The copper thickness of your FastPrintPCB affects its current carrying capacity and signal integrity. Typical copper thicknesses range from 0.5 oz to 3 oz. Choose the appropriate thickness based on your design requirements and power demands.
Solder Mask and Silkscreen
Solder mask and silkscreen are important elements of your FastPrintPCB. Solder mask protects the copper traces from oxidation and prevents short circuits, while silkscreen provides component labels and markings for easy assembly and debugging.
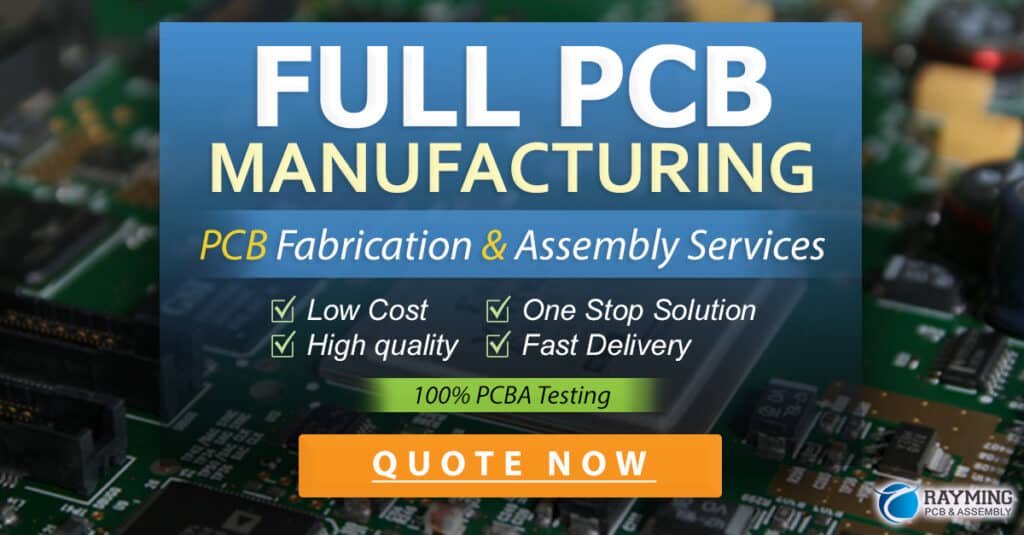
Manufacturing Process Optimization
Panelization Techniques
Panelization is the process of arranging multiple PCB designs on a single panel for efficient manufacturing. Proper panelization techniques can maximize material utilization and minimize waste. Consider the following factors:
- Panel size and shape
- Tooling holes and fiducials
- Spacing between boards
- Depaneling methods
Automated Optical Inspection (AOI)
AOI is a crucial step in the FastPrintPCB manufacturing process. It uses high-resolution cameras and advanced algorithms to detect manufacturing defects such as:
- Solder bridges
- Open circuits
- Missing components
- Incorrect component placement
Implementing AOI ensures the highest quality standards and reduces the risk of defective boards reaching the end-user.
Electrical Testing
Electrical testing is performed to verify the functionality and performance of your FastPrintPCB. Common electrical tests include:
- Continuity testing
- Insulation resistance testing
- High-voltage testing
- Functional testing
By conducting thorough electrical testing, you can identify and address any issues before the boards are shipped to customers.
Quality Control and Assurance
Implementing Quality Management Systems
To consistently produce perfect FastPrintPCBs, it is essential to implement a robust quality management system (QMS). A QMS encompasses all the processes, procedures, and policies necessary to ensure the highest quality standards are met. Key elements of a QMS include:
- Documentation control
- Process control
- Traceability
- Continuous improvement
Certifications and Standards
Adhering to industry-recognized certifications and standards demonstrates your commitment to quality and reliability. Some important certifications and standards for FastPrintPCB include:
- ISO 9001: Quality Management Systems
- IPC-A-600: Acceptability of Printed Boards
- UL 94: Standard for Safety of Flammability of Plastic Materials
- RoHS: Restriction of Hazardous Substances
By achieving these certifications and complying with relevant standards, you can instill confidence in your customers and differentiate yourself from competitors.
Continuous Improvement and Lean Manufacturing
Continuous improvement is a fundamental principle of quality management. By constantly seeking ways to enhance your processes and eliminate waste, you can achieve higher levels of efficiency and quality in your FastPrintPCB production. Lean manufacturing techniques, such as:
- 5S: Sort, Set in Order, Shine, Standardize, Sustain
- Kaizen: Continuous Improvement
- Just-in-Time (JIT) Production
- Value Stream Mapping
These techniques can help you streamline your operations, reduce lead times, and improve overall product quality.
Frequently Asked Questions (FAQ)
-
What is FastPrintPCB?
FastPrintPCB is an advanced PCB manufacturing technology that enables the rapid production of high-quality printed circuit boards, reducing lead times and costs compared to traditional manufacturing methods. -
What are the benefits of using FastPrintPCB?
The main benefits of using FastPrintPCB include faster turnaround times, lower production costs, improved design flexibility, and the ability to produce high-quality PCBs consistently. -
What design considerations should I keep in mind for FastPrintPCB?
When designing for FastPrintPCB, it is important to follow design guidelines and best practices, such as optimizing component placement, selecting appropriate materials, and adhering to manufacturing constraints. Using the right design tools and performing thorough design reviews can help ensure the best results. -
How can I ensure the quality of my FastPrintPCBs?
To ensure the highest quality of your FastPrintPCBs, implement a robust quality management system, adhere to industry standards and certifications, and employ techniques such as automated optical inspection (AOI) and electrical testing. Continuously seeking ways to improve your processes and eliminate waste can also contribute to enhanced quality. -
What are the common applications of FastPrintPCB?
FastPrintPCB is widely used in various industries, including consumer electronics, automotive, aerospace, medical devices, and telecommunications. Its ability to quickly produce high-quality PCBs makes it suitable for prototyping, low-volume production, and even high-volume manufacturing.
Conclusion
Creating the perfect FastPrintPCB requires a holistic approach that encompasses design, material selection, manufacturing process optimization, and quality control. By following best practices, using the right tools, and continuously improving your processes, you can consistently produce high-quality PCBs that meet the demands of your customers and the ever-evolving electronics industry.
Embracing the power of FastPrintPCB technology can give you a competitive edge, enabling you to bring innovative products to market faster and more cost-effectively. As the electronics industry continues to advance, staying at the forefront of PCB manufacturing techniques will be crucial to your success.
By implementing the factors discussed in this article, you can unlock the full potential of FastPrintPCB and deliver perfect printed circuit boards that exceed expectations and drive your business forward.
No responses yet