Understanding High Frequency Signals
Before diving into the factors that affect high frequency PCB design, it is essential to understand the nature of high frequency signals. High frequency signals are characterized by their short wavelengths and high speeds, which make them more susceptible to various forms of interference and signal degradation.
Wavelength and Frequency
The relationship between wavelength and frequency is crucial in high frequency PCB design. As the frequency of a signal increases, its wavelength decreases. This relationship is described by the equation:
λ = c / f
Where:
– λ is the wavelength
– c is the speed of light (approximately 3 × 10^8 m/s)
– f is the frequency
For example, a signal with a frequency of 1 GHz has a wavelength of approximately 30 cm in free space.
Signal Integrity
Signal integrity is a critical concern in high frequency PCB design. As the frequency of a signal increases, it becomes more susceptible to various forms of signal degradation, such as:
- Reflection: When a signal encounters an impedance mismatch, a portion of the signal is reflected back to the source, causing signal distortion and power loss.
- Crosstalk: Crosstalk occurs when a signal from one trace induces an unwanted signal in an adjacent trace, leading to signal interference and degradation.
- Attenuation: As a signal travels through a PCB, it experiences attenuation due to dielectric losses, conductor losses, and radiation losses. Attenuation increases with frequency, making it a significant concern in high frequency PCB design.
PCB Material Selection
The choice of PCB materials plays a crucial role in high frequency PCB design. The dielectric constant (Dk) and dissipation factor (Df) of the substrate material directly impact the signal propagation and losses in the PCB.
Dielectric Constant (Dk)
The dielectric constant, also known as relative permittivity, is a measure of a material’s ability to store electrical energy. In high frequency PCB design, a lower dielectric constant is generally preferred, as it results in faster signal propagation and reduced capacitance between traces. Some common PCB materials and their dielectric constants are listed in the table below:
Material | Dielectric Constant (Dk) |
---|---|
FR-4 | 4.2 – 4.5 |
Rogers RO4350B | 3.48 |
Rogers RO4003C | 3.38 |
Isola I-Tera MT40 | 3.45 |
Panasonic Megtron 6 | 3.40 |
Dissipation Factor (Df)
The dissipation factor, also known as loss tangent, is a measure of a material’s ability to dissipate electrical energy as heat. A lower dissipation factor is desirable in high frequency PCB design, as it minimizes signal losses and maintains signal integrity. Some common PCB materials and their dissipation factors are listed in the table below:
Material | Dissipation Factor (Df) |
---|---|
FR-4 | 0.020 – 0.030 |
Rogers RO4350B | 0.0037 |
Rogers RO4003C | 0.0027 |
Isola I-Tera MT40 | 0.0030 |
Panasonic Megtron 6 | 0.0025 |
Material Thickness
The thickness of the PCB substrate material also influences high frequency performance. Thinner materials generally have lower dielectric losses and allow for tighter control of impedance. However, thinner materials may also be more prone to mechanical stress and warping. Designers must strike a balance between electrical performance and mechanical stability when selecting the appropriate material thickness for their high frequency PCB design.
Controlled Impedance
Controlling the impedance of PCB traces is essential for maintaining signal integrity and minimizing reflections in high frequency PCB design. The characteristic impedance of a trace is determined by its geometry, the dielectric constant of the substrate material, and the proximity of ground and power planes.
Trace Width and Spacing
The width and spacing of PCB traces directly impact their characteristic impedance. Wider traces have lower impedance, while narrower traces have higher impedance. The spacing between traces also affects impedance, with closer spacing resulting in higher capacitance and lower impedance.
To achieve a specific target impedance, designers can use impedance calculators or simulation tools to determine the appropriate trace width and spacing for a given substrate material and thickness. The table below provides some general guidelines for trace width and spacing based on common impedance values:
Impedance (Ω) | Trace Width (mm) | Trace Spacing (mm) |
---|---|---|
50 | 0.25 – 0.5 | 0.15 – 0.3 |
75 | 0.15 – 0.3 | 0.2 – 0.4 |
100 | 0.1 – 0.2 | 0.25 – 0.5 |
Ground and Power Planes
The presence and placement of ground and power planes in a high frequency PCB design significantly influence the impedance of traces. Ground planes provide a low-impedance return path for signals and help to minimize crosstalk and electromagnetic interference (EMI).
In high frequency PCB design, it is common to use a technique called “ground stitching” or “via shielding” to create a more robust ground plane. This involves placing numerous vias connecting the ground planes on different layers of the PCB, creating a more effective shield against EMI and reducing signal coupling between layers.
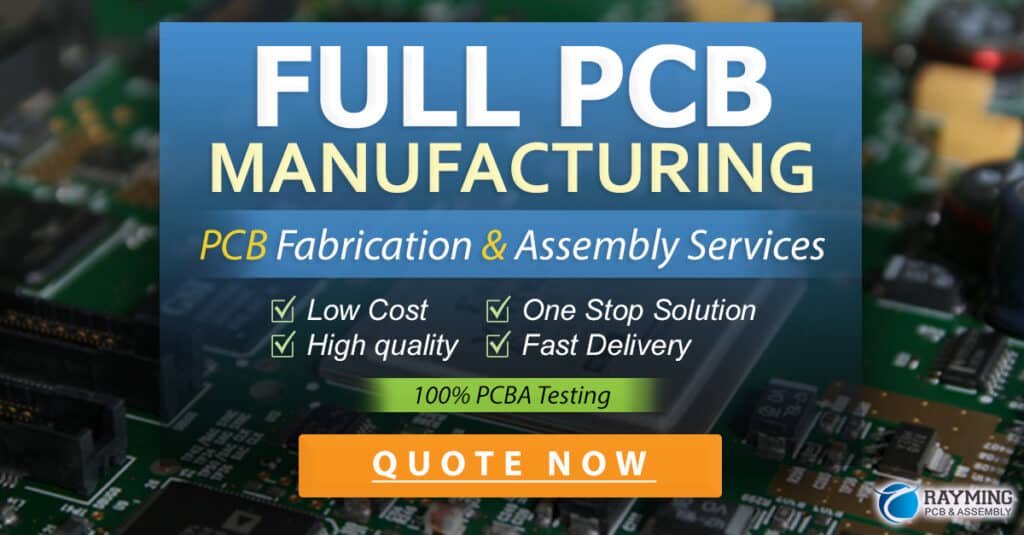
Routing Techniques
Proper routing techniques are crucial for maintaining signal integrity and minimizing interference in high frequency PCB design. Some key considerations include:
Trace Length Matching
In high-speed digital designs, it is essential to match the lengths of traces carrying related signals (e.g., clock and data lines) to ensure that the signals arrive at their destination at the same time. Trace length mismatch can lead to signal skew, which can cause timing errors and degrade system performance.
To minimize trace length mismatch, designers can employ various techniques, such as:
- Serpentine routing: Adding intentional bends or curves to traces to equalize their lengths.
- Delay lines: Using dedicated delay lines or serpentine traces to introduce a controlled amount of delay to shorter traces.
- T-junctions: Splitting a trace into two paths and rejoining them to equalize the lengths of the split traces.
Crosstalk Reduction
Crosstalk is a major concern in high frequency PCB design, as it can lead to signal degradation and interference. To minimize crosstalk, designers can employ several techniques, such as:
- Increasing trace spacing: Larger spacing between traces reduces the capacitive coupling between them, minimizing crosstalk.
- Orthogonal routing: Routing traces on adjacent layers at 90-degree angles to each other minimizes the coupling between them.
- Guard traces: Placing grounded traces between sensitive signals to provide shielding and reduce crosstalk.
- Differential signaling: Using differential pairs for high-speed signals, as they are less susceptible to crosstalk and EMI.
EMI Reduction
Electromagnetic interference (EMI) can cause signal degradation and interfere with the operation of nearby electronic devices. To minimize EMI in high frequency PCB design, designers can use techniques such as:
- Proper grounding: Ensuring a low-impedance ground plane and using ground stitching to minimize ground bounce and EMI.
- Shielding: Using shielded connectors, enclosures, and gaskets to contain EMI generated by the PCB.
- Filtering: Implementing power supply filtering and decoupling to minimize high-frequency noise and EMI.
- Spread-spectrum clocking: Using spread-spectrum clock generators to reduce the peak energy of clock signals and minimize EMI.
Stackup Design
The PCB stackup, which refers to the arrangement of conductive layers and dielectric materials in a PCB, plays a critical role in high frequency PCB design. A well-designed stackup can help to maintain signal integrity, minimize crosstalk, and reduce EMI.
Layer Arrangement
In a typical high frequency PCB stackup, the layers are arranged to provide a balance between signal routing, power distribution, and grounding. A common arrangement is as follows:
- Top layer: High-speed signals and components
- Ground plane
- Power plane
- Signal layers
- Ground plane
- Bottom layer: High-speed signals and components
This arrangement provides a solid ground reference for high-speed signals, minimizes crosstalk between layers, and allows for effective power distribution.
Dielectric Thickness
The thickness of the dielectric material between layers in a PCB stackup influences the impedance of traces and the overall signal integrity. In high frequency PCB design, thinner dielectrics are generally preferred, as they minimize signal propagation delay and reduce dielectric losses.
However, designers must also consider the manufacturing capabilities and cost implications when selecting dielectric thicknesses. The table below provides some common dielectric thicknesses used in high frequency PCB stackups:
Layer | Dielectric Thickness (mm) |
---|---|
Signal to Ground/Power | 0.1 – 0.2 |
Ground to Power | 0.2 – 0.3 |
Signal to Signal | 0.15 – 0.25 |
Simulation and Verification
Given the complexity of high frequency PCB design, simulation and verification tools are essential for ensuring the performance and reliability of the final product. These tools allow designers to analyze and optimize their designs before committing to production.
Signal Integrity Simulation
Signal integrity (SI) simulation tools, such as Mentor Graphics HyperLynx or Cadence Sigrity, enable designers to analyze the behavior of high-speed signals in their PCB design. These tools can help to identify issues such as reflections, crosstalk, and signal attenuation, and allow designers to optimize their design to minimize these effects.
SI simulation typically involves creating a model of the PCB stackup, defining the signal nets and their properties, and running simulations to analyze the signal behavior under various conditions. Designers can then modify their design based on the simulation results to improve signal integrity.
EMI Simulation
EMI simulation tools, such as Ansys SIwave or CST Studio Suite, allow designers to analyze the electromagnetic behavior of their PCB design and identify potential sources of EMI. These tools can simulate the radiation patterns of the PCB and help designers to optimize their design for EMI compliance.
EMI simulation typically involves creating a 3D model of the PCB, defining the material properties and boundary conditions, and running simulations to analyze the electromagnetic fields generated by the PCB. Designers can then modify their design to minimize EMI and ensure compliance with relevant EMC standards.
Design Rule Checking (DRC)
Design rule checking (DRC) is a process of verifying that a PCB design meets the specified design rules and constraints. In high frequency PCB design, DRC is particularly important for ensuring that the design adheres to the rules related to trace width, spacing, and impedance control.
Most PCB design software, such as Altium Designer or Cadence Allegro, includes built-in DRC tools that can automatically check the design against a set of predefined rules. Designers can also create custom rules to meet the specific requirements of their high frequency design.
FAQ
- What is the difference between high frequency and low frequency PCB design?
High frequency PCB design deals with signals that have shorter wavelengths and higher speeds compared to low frequency designs. This makes high frequency designs more susceptible to signal integrity issues, such as reflections, crosstalk, and attenuation. High frequency designs also require careful selection of materials, controlled impedance routing, and specific layout techniques to maintain signal integrity and minimize EMI.
- What are the most important factors to consider when selecting PCB materials for high frequency design?
The most important factors to consider when selecting PCB materials for high frequency design are the dielectric constant (Dk) and dissipation factor (Df) of the substrate material. A lower dielectric constant results in faster signal propagation and reduced capacitance between traces, while a lower dissipation factor minimizes signal losses and maintains signal integrity. The thickness of the substrate material also influences the dielectric losses and impedance control.
- How can I control the impedance of traces in my high frequency PCB design?
To control the impedance of traces in a high frequency PCB design, you need to consider factors such as trace width, trace spacing, substrate material properties, and the presence of ground and power planes. You can use impedance calculators or simulation tools to determine the appropriate trace geometry for a given target impedance. Additionally, using ground stitching and proper placement of ground and power planes can help to maintain a consistent impedance throughout the design.
- What is the purpose of ground stitching in high frequency PCB design?
Ground stitching, also known as via shielding, is a technique used in high frequency PCB design to create a more robust ground plane. It involves placing numerous vias connecting the ground planes on different layers of the PCB. This helps to create a more effective shield against electromagnetic interference (EMI) and reduces signal coupling between layers. Ground stitching also provides a low-impedance return path for high-speed signals, improving signal integrity.
- How can simulation tools help in high frequency PCB design?
Simulation tools are essential for analyzing and optimizing high frequency PCB designs before committing to production. Signal integrity (SI) simulation tools allow designers to analyze the behavior of high-speed signals in their PCB design, identify issues such as reflections, crosstalk, and attenuation, and optimize their design to minimize these effects. EMI simulation tools help designers to analyze the electromagnetic behavior of their PCB design, identify potential sources of EMI, and ensure compliance with relevant EMC standards. These tools can save significant time and cost by catching and correcting issues early in the design process.
No responses yet