Introduction to PCB Layout Design
Printed Circuit Board (PCB) layout design is a crucial step in the development of electronic devices. A well-designed PCB layout ensures that the electronic components function properly, minimizes signal interference, and maximizes the reliability and longevity of the device. In this comprehensive article, we will dive into the essential aspects of PCB layout design, providing you with the knowledge and best practices to create robust and efficient PCB layouts.
Understanding the Basics of PCB Layout
What is a PCB?
A PCB is a flat board made of insulating material, such as fiberglass or plastic, with conductive copper traces etched onto its surface. These traces connect various electronic components, such as resistors, capacitors, and integrated circuits (ICs), to form a complete electronic circuit.
Layers in a PCB
PCBs can have single or multiple layers, depending on the complexity of the circuit and the available space. The most common PCB layer configurations are:
Layers | Description |
---|---|
Single Layer | A PCB with conductive traces on only one side of the board. |
Double Layer | A PCB with conductive traces on both sides of the board. |
Multi-Layer | A PCB with conductive traces on multiple layers, separated by insulating material. |
Components of a PCB
A typical PCB consists of the following components:
- Substrate: The insulating material that forms the base of the PCB.
- Copper Traces: The conductive paths that connect the electronic components.
- Solder Mask: A protective layer that covers the copper traces, leaving only the component pads exposed.
- Silkscreen: A layer of text and symbols printed on the PCB for component identification and assembly instructions.
- Vias: Conductive holes that connect traces on different layers of the PCB.
PCB Layout Design Process
Schematic Design
The first step in PCB layout design is to create a schematic diagram of the electronic circuit. The schematic represents the logical connections between the components and serves as a blueprint for the PCB layout.
Component Placement
Once the schematic is complete, the next step is to place the components on the PCB. The placement should consider factors such as:
- Functionality: Group related components together to minimize trace lengths and improve signal integrity.
- Mechanical constraints: Ensure that components fit within the available space and do not interfere with each other or the enclosure.
- Thermal management: Place heat-generating components away from sensitive components and provide adequate cooling.
Routing
After component placement, the traces that connect the components must be routed. Routing involves creating the conductive paths that carry signals and power between the components. When routing, consider the following guidelines:
- Minimize trace lengths to reduce signal loss and interference.
- Avoid sharp angles and use smooth curves to improve signal integrity.
- Maintain appropriate trace widths based on the current requirements and PCB manufacturing capabilities.
- Provide adequate spacing between traces to minimize crosstalk and electromagnetic interference (EMI).
Ground and Power Planes
In multi-layer PCBs, dedicated layers are often used for ground and power distribution. These layers provide a low-impedance path for current flow and help reduce EMI. When designing ground and power planes, consider the following:
- Use a solid copper pour for the ground plane to minimize impedance and provide shielding.
- Divide the power plane into separate regions for different voltage levels to avoid interference.
- Provide adequate decoupling capacitors near power-consuming components to minimize voltage fluctuations.
Design Rule Check (DRC)
Before finalizing the PCB layout, it is essential to perform a Design Rule Check (DRC). The DRC verifies that the layout adheres to the manufacturing constraints and design guidelines specified by the PCB fabricator. This includes checking for minimum trace widths, clearances, and hole sizes.
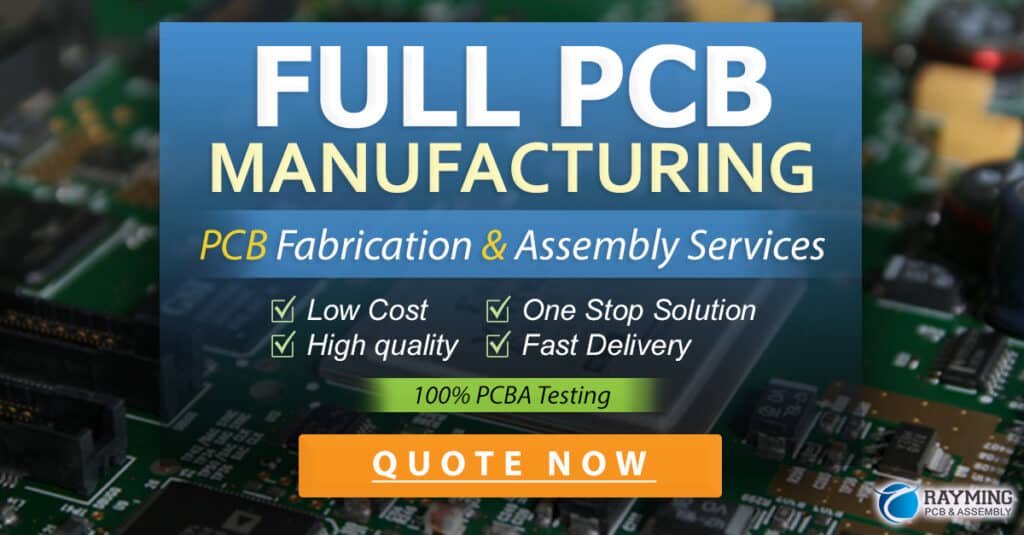
PCB Layout Best Practices
Component Orientation
Orient components in a consistent direction to facilitate assembly and reduce the likelihood of errors. For example, place all the resistors and capacitors in the same orientation, with their values facing the same direction.
Trace Width and Spacing
Determine the appropriate trace width based on the current carrying requirements and the PCB manufacturing capabilities. Provide adequate spacing between traces to minimize crosstalk and EMI. The following table provides general guidelines for trace width and spacing:
Current (A) | Trace Width (mm) | Trace Spacing (mm) |
---|---|---|
0.5 | 0.2 | 0.2 |
1.0 | 0.3 | 0.3 |
2.0 | 0.5 | 0.4 |
3.0 | 0.8 | 0.5 |
Via Placement
Place vias strategically to minimize the length of the traces and improve signal integrity. Avoid placing vias under components, as this can make soldering difficult and increase the risk of manufacturing defects.
Decoupling Capacitors
Place decoupling capacitors close to the power pins of ICs to minimize voltage fluctuations and provide a stable power supply. Use the appropriate capacitor values based on the frequency and current requirements of the circuit.
Electromagnetic Compatibility (EMC)
Design the PCB layout to minimize EMI and ensure electromagnetic compatibility. Some EMC best practices include:
- Provide a solid ground plane to minimize radiated emissions.
- Route high-speed signals away from sensitive analog circuits.
- Use shielding techniques, such as grounded copper pours or shielded cables, to contain EMI.
PCB Layout Software
There are several PCB layout software tools available to assist in the design process. Some popular options include:
- Altium Designer
- Cadence OrCAD
- Autodesk Eagle
- KiCad
These software tools provide a user-friendly interface for schematic capture, component placement, routing, and design rule checking.
Conclusion
Designing a PCB layout requires careful consideration of various factors, including component placement, routing, ground and power planes, and EMC. By following best practices and using appropriate software tools, you can create robust and efficient PCB layouts that ensure the proper functioning and reliability of your electronic devices.
Frequently Asked Questions (FAQ)
1. What is the difference between a single-layer and a multi-layer PCB?
A single-layer PCB has conductive traces on only one side of the board, while a multi-layer PCB has conductive traces on multiple layers separated by insulating material. Multi-layer PCBs offer higher component density and better signal integrity but are more expensive to manufacture.
2. How do I determine the appropriate trace width for my PCB layout?
The appropriate trace width depends on the current carrying requirements of the circuit and the PCB manufacturing capabilities. Refer to the trace width and spacing guidelines provided by your PCB fabricator or use general guidelines based on the expected current levels.
3. What is the purpose of a ground plane in a PCB layout?
A ground plane is a solid copper layer that provides a low-impedance path for current return and helps reduce EMI. It acts as a reference point for signals and provides shielding against external noise.
4. How can I minimize electromagnetic interference (EMI) in my PCB layout?
To minimize EMI in your PCB layout, follow these best practices:
- Provide a solid ground plane
- Route high-speed signals away from sensitive analog circuits
- Use shielding techniques, such as grounded copper pours or shielded cables
- Minimize trace lengths and loops
- Use appropriate decoupling capacitors
5. Can I design a PCB layout without using specialized software?
While it is possible to design a simple PCB layout manually, using specialized PCB layout software is highly recommended. These software tools provide features such as schematic capture, component libraries, design rule checking, and automatic routing, which greatly simplify the design process and ensure adherence to manufacturing constraints.
No responses yet