Understanding Electrostatic Discharge (ESD)
What is ESD?
Electrostatic discharge (ESD) is the sudden flow of electricity between two electrically charged objects caused by contact, an electrical short, or dielectric breakdown. ESD occurs when the difference in electrical potential between two objects is high enough to overcome the resistance of the medium between them, such as air or a dielectric material.
The Dangers of ESD
ESD can cause significant damage to sensitive electronic components, such as integrated circuits, transistors, and other semiconductor devices. Even a small amount of static electricity can be sufficient to destroy or degrade these components, leading to device failure, reduced performance, or intermittent issues.
Common Sources of ESD
ESD can be generated by various sources, including:
– Human body: The human body can accumulate a significant amount of static charge, especially when walking on carpeted floors or wearing synthetic clothing.
– Ungrounded equipment: Electronic devices and equipment that are not properly grounded can accumulate static charge and become a source of ESD.
– Packaging materials: Some packaging materials, such as plastic bags and foam, can generate static charges through triboelectric charging.
– Environmental factors: Low humidity and high temperatures can increase the likelihood of ESD events.
Creating an Anti-Static Environment
ESD-Safe Workstations
One of the most effective ways to create an anti-static environment is by using ESD-safe workstations. These workstations are designed to dissipate static charges and prevent the buildup of static electricity. Key components of an ESD-safe workstation include:
-
ESD-safe work surfaces: These surfaces are made from materials that are conductive or dissipative, such as stainless steel, laminate, or rubber. They help to drain static charges away from sensitive components and prevent the accumulation of static electricity.
-
Grounding: All conductive elements of the workstation, including the work surface, operators, and equipment, should be properly grounded to a common ground point. This ensures that any static charges are safely dissipated to ground, preventing ESD events.
-
Personnel grounding: Operators should wear ESD-safe wrist straps or heel grounders to ensure that they are properly grounded when handling sensitive components. These devices provide a safe path for static charges to dissipate from the operator’s body to ground.
-
Ionizers: Ionizers, also known as air ionizers, are devices that generate positive and negative ions to neutralize static charges in the air. They help to reduce the buildup of static electricity on surfaces and components, minimizing the risk of ESD events.
ESD-Safe Flooring and Footwear
In addition to ESD-safe workstations, the flooring and footwear used in an anti-static environment play a crucial role in ESD Protection. ESD-safe flooring materials, such as conductive or dissipative vinyl, epoxy, or rubber, help to dissipate static charges and prevent the buildup of static electricity. When used in conjunction with ESD-safe footwear, such as conductive or dissipative shoes or shoe covers, operators can maintain a continuous ground path, minimizing the risk of ESD events.
ESD-Safe Packaging and Handling
Proper packaging and handling of sensitive components are essential for maintaining an anti-static environment. ESD-safe packaging materials, such as static shielding bags, conductive foam, and conductive tapes, help to protect components from static charges during storage and transport. When handling sensitive components, operators should follow ESD-safe practices, such as:
- Using ESD-safe gloves or finger cots to prevent direct contact with components.
- Handling components by their edges or leads, avoiding contact with sensitive areas.
- Storing components in ESD-safe containers or packaging when not in use.
- Minimizing the movement of components and operators to reduce the generation of static charges.
ESD Training and Auditing
To ensure the effectiveness of an anti-static environment, it is essential to provide proper ESD training to all personnel involved in handling sensitive components. ESD training should cover topics such as:
- The basics of ESD and its impact on electronic components.
- ESD-safe handling procedures and best practices.
- Proper use and maintenance of ESD-safe equipment and materials.
- Recognizing and reporting ESD events or issues.
Regular auditing and monitoring of the anti-static environment are also necessary to maintain its effectiveness over time. This may include:
- Conducting periodic ESD tests on work surfaces, operators, and equipment to ensure proper grounding and dissipation of static charges.
- Monitoring environmental conditions, such as temperature and humidity, to ensure they remain within acceptable ranges for ESD protection.
- Inspecting ESD-safe materials and equipment for wear, damage, or contamination, and replacing them as needed.
ESD Protection Standards and Guidelines
Several international standards and guidelines have been developed to provide guidance on ESD protection and the creation of anti-static environments. Some of the most widely recognized standards include:
-
ANSI/ESD S20.20: This standard provides requirements for the development, implementation, and maintenance of an ESD control program to protect electronic components and assemblies.
-
IEC 61340-5-1: This standard specifies requirements for the protection of electronic devices from ESD events and the implementation of ESD control programs.
-
JEDEC JESD625B: This standard provides guidelines for the handling, packaging, and testing of ESD-sensitive devices to ensure their protection during manufacturing, assembly, and shipping.
Adhering to these standards and guidelines can help ensure the effectiveness of an anti-static environment and minimize the risk of ESD-related damage to sensitive components.
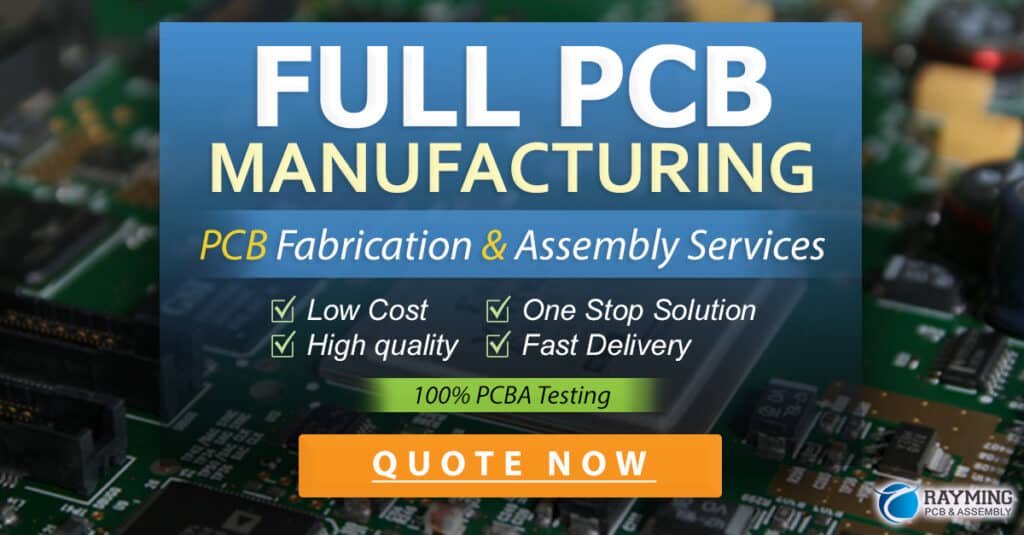
Frequently Asked Questions (FAQ)
-
What is the difference between conductive and dissipative materials in ESD protection?
Conductive materials have a lower electrical resistance and can quickly dissipate static charges to ground. Dissipative materials have a higher resistance and allow for a slower, controlled dissipation of static charges. Both types of materials are used in ESD protection, depending on the specific application and requirements. -
How often should ESD-safe equipment and materials be tested and replaced?
The frequency of testing and replacement of ESD-safe equipment and materials depends on factors such as the level of usage, environmental conditions, and the sensitivity of the components being handled. As a general guideline, ESD-safe materials should be tested at least once per year, and replaced when they show signs of wear, damage, or loss of effectiveness. However, more frequent testing and replacement may be necessary for high-risk or high-volume applications. -
Can ESD damage occur even if there is no visible spark or sensation?
Yes, ESD damage can occur without any visible or tangible signs. In fact, many ESD events are below the threshold of human perception, meaning they can occur without a visible spark or a sensory shock. This is why it is essential to maintain a comprehensive ESD protection program, even if ESD events are not readily apparent. -
How can I test the effectiveness of my anti-static environment?
There are several methods to test the effectiveness of an anti-static environment, including: - Surface resistance testing: Measuring the electrical resistance of ESD-safe surfaces to ensure they fall within acceptable ranges.
- Personnel grounding testing: Verifying that operators are properly grounded through wrist straps or heel grounders.
- Electrostatic field meter testing: Measuring the strength of electrostatic fields in the environment to identify potential sources of ESD.
-
Charged plate monitor testing: Assessing the ability of ionizers and other ESD control measures to neutralize static charges.
-
What should I do if I suspect that an ESD event has occurred?
If you suspect that an ESD event has occurred, it is important to take immediate action to minimize the potential for damage: - Stop work and notify a supervisor or ESD coordinator.
- Isolate the affected components or devices and label them as potentially ESD-damaged.
- Document the details of the event, including the date, time, location, and any relevant environmental or operational factors.
- Conduct a thorough investigation to identify the root cause of the ESD event and implement corrective actions to prevent future occurrences.
- If necessary, send the affected components for testing or evaluation to determine the extent of any damage.
By understanding the principles of ESD protection and implementing a comprehensive anti-static environment, manufacturers, and assemblers can significantly reduce the risk of ESD-related damage to sensitive electronic components. This, in turn, helps to improve product quality, reliability, and customer satisfaction, while also reducing costs associated with rework, repairs, and warranty claims.
No responses yet