Introduction to ESC Circuits
An Electronic Speed Controller (ESC) is an essential component in radio-controlled (RC) vehicles, drones, and other robotic applications. It acts as the brain of the system, controlling the speed and direction of the motor based on the inputs received from the user or an external controller. ESC circuits are responsible for converting the battery’s DC power into the AC power required by the motor, allowing precise control over the motor’s speed and direction.
In this comprehensive guide, we’ll dive into the world of ESC circuits, exploring their components, working principles, and practical applications. Whether you’re a hobbyist, a student, or a professional, this guide will provide you with the knowledge and tools to get started with ESC circuits and take your projects to the next level.
Understanding the Components of an ESC Circuit
To grasp the functioning of an ESC circuit, it’s essential to understand its key components. Let’s take a closer look at each of these components and their roles in the overall system.
Microcontroller
The microcontroller is the heart of the ESC circuit. It receives input signals from the user or an external controller, processes them, and generates the appropriate output signals to control the motor. The microcontroller is typically a small, programmable integrated circuit that can be customized to suit the specific requirements of the application.
Some popular microcontrollers used in ESC circuits include:
- Arduino (e.g., Arduino Uno, Arduino Nano)
- Atmega (e.g., Atmega328, Atmega2560)
- PIC (e.g., PIC16F877A, PIC18F4550)
The choice of microcontroller depends on factors such as processing power, memory, I/O capabilities, and ease of programming.
MOSFET (Metal-Oxide-Semiconductor Field-Effect Transistor)
MOSFETs are the power switches that control the flow of current to the motor. They are responsible for converting the battery’s DC power into the AC power required by the motor. MOSFETs are voltage-controlled devices, meaning that they can be turned on or off by applying a voltage to their gate terminal.
In an ESC circuit, MOSFETs are typically arranged in a configuration called an “H-bridge.” This arrangement allows the ESC to control the direction of the motor by selectively turning on and off the appropriate MOSFETs.
Some commonly used MOSFETs in ESC circuits include:
- IRFZ44N
- IRF3205
- IRLB3034
Gate Driver
The gate driver is a crucial component that interfaces the microcontroller with the MOSFETs. It amplifies the low-power control signals from the microcontroller to drive the high-power MOSFETs efficiently. Gate drivers ensure that the MOSFETs are switched on and off quickly and cleanly, minimizing power losses and improving overall system efficiency.
Popular gate driver ICs used in ESC circuits include:
- IR2101
- IR2110
- TC4420
Capacitors and Inductors
Capacitors and inductors play a vital role in filtering and smoothing the power supply to the ESC circuit. They help reduce electrical noise, minimize voltage spikes, and maintain a stable power supply to the components.
-
Capacitors: Ceramic and electrolytic capacitors are commonly used in ESC circuits. They store electrical energy and release it when needed, helping to stabilize the voltage and reduce ripple.
-
Inductors: Inductors are used in conjunction with capacitors to form LC filters, which further smooth the power supply and reduce high-frequency noise.
Connectors and Wiring
Connectors and wiring are the essential elements that link the various components of the ESC circuit together. They ensure reliable and secure connections between the battery, microcontroller, MOSFETs, and motor.
-
Battery Connector: The battery connector, typically a high-current connector like an XT60 or Deans, connects the ESC to the battery pack.
-
Motor Connector: The motor connector, often a bullet or banana connector, connects the ESC to the motor.
-
Signal Connector: The signal connector, usually a standard servo connector (JR, Futaba, or Universal), connects the ESC to the receiver or external controller.
High-quality, properly gauged wiring is essential to minimize power losses and ensure reliable operation of the ESC circuit.
How an ESC Circuit Works
Now that we’ve explored the key components of an ESC circuit let’s dive into how these components work together to control the motor.
PWM (Pulse Width Modulation)
PWM is a technique used by the microcontroller to control the speed of the motor. It works by rapidly switching the MOSFETs on and off, creating a series of pulses. The width of these pulses determines the average voltage applied to the motor, which in turn controls its speed.
By varying the pulse width, the ESC can achieve smooth and precise speed control, from zero to maximum speed. The microcontroller generates the PWM signals based on the input received from the user or external controller.
H-Bridge Configuration
The H-bridge configuration of the MOSFETs allows the ESC to control the direction of the motor. It consists of four MOSFETs arranged in a configuration that resembles the letter “H.” By selectively turning on and off the appropriate MOSFETs, the ESC can reverse the polarity of the voltage applied to the motor, causing it to rotate in the opposite direction.
Here’s a simple representation of an H-bridge configuration:
+Battery
|
+-----------+
| M1 |
| Gate |
| Driver | M3
| | |
+----+---+ |
| |
+--------+
|
M2
|
+-----------+
| M4 |
| Gate |
| Driver |
| |
+----+---+
|
|
GND
In this diagram, M1, M2, M3, and M4 represent the four MOSFETs. By turning on M1 and M4 while keeping M2 and M3 off, the current flows from the battery through M1, the motor, and M4 to ground, causing the motor to rotate in one direction. Conversely, by turning on M2 and M3 while keeping M1 and M4 off, the current flows in the opposite direction, causing the motor to rotate in the other direction.
Commutation
Commutation is the process of correctly energizing the motor’s windings to create a rotating magnetic field, which causes the rotor to turn. In brushless DC motors (BLDCs), which are commonly used with ESCs, the commutation is performed electronically by the ESC.
The ESC uses feedback from the motor, typically in the form of back EMF (electromotive force) or Hall Effect Sensors, to determine the rotor’s position. Based on this information, the ESC energizes the appropriate motor windings in the correct sequence to maintain smooth and efficient rotation.
Throttle Calibration
Throttle calibration is an essential step in setting up an ESC circuit. It involves teaching the ESC the minimum and maximum throttle positions, which correspond to the lowest and highest speeds of the motor.
To calibrate the throttle, the user typically follows these steps:
- Turn on the transmitter and set the throttle stick to the maximum position.
- Connect the battery to the ESC, which will enter calibration mode (often indicated by a specific motor tone).
- Move the throttle stick to the minimum position and wait for the ESC to confirm the calibration (usually with another motor tone).
After calibration, the ESC will map the input throttle signal to the appropriate motor speed, ensuring smooth and predictable control.
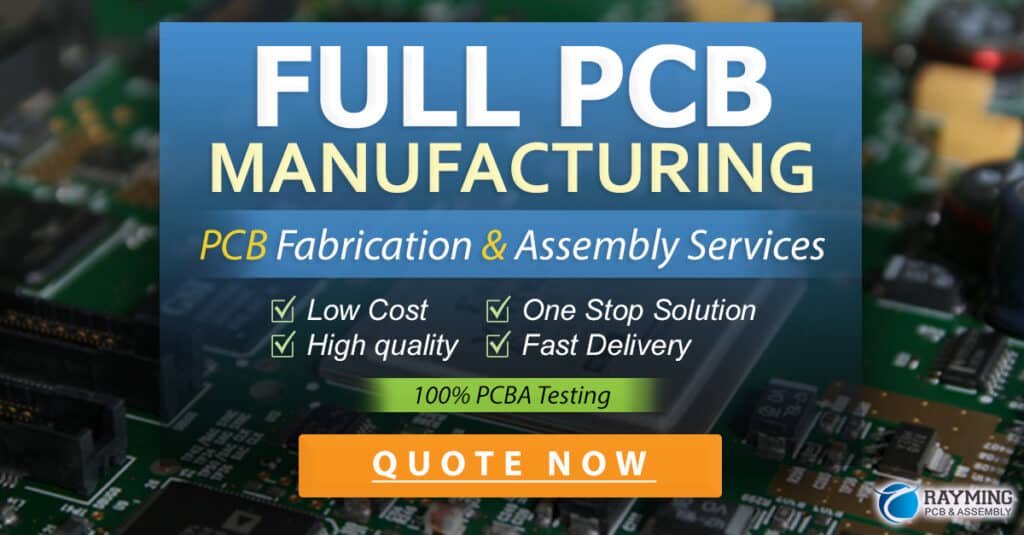
Practical Applications of ESC Circuits
ESC circuits find widespread use in various applications that require precise motor speed and direction control. Some common applications include:
Radio-Controlled Vehicles
ESCs are an integral part of radio-controlled vehicles, such as cars, boats, and airplanes. They enable smooth and responsive control of the vehicle’s motor(s), allowing users to adjust speed and direction in real-time.
In RC cars, for example, the ESC controls the main drive motor, while in RC airplanes, it may control multiple motors for propulsion and steering.
Drones and Quadcopters
Drones and quadcopters rely heavily on ESCs to control their brushless DC motors, which provide the necessary thrust for flight. Each motor is typically controlled by a dedicated ESC, which receives commands from the flight controller.
The flight controller calculates the required motor speeds based on user input and sensor data (e.g., accelerometers, gyroscopes) and sends the appropriate signals to the ESCs. The ESCs then adjust the motor speeds accordingly, enabling stable and controlled flight.
Robotics
ESCs are widely used in robotic applications, such as autonomous vehicles, industrial robots, and educational platforms. They provide precise control over the motors, allowing robots to perform tasks that require accurate speed and position control.
In mobile robots, ESCs control the drive motors, enabling smooth navigation and trajectory tracking. In robotic arms, ESCs may control the joint motors, allowing precise positioning and motion control.
ESC Circuit Design Considerations
When designing an ESC circuit, several key factors must be considered to ensure optimal performance, reliability, and safety.
Voltage and Current Ratings
The voltage and current ratings of the ESC components must match the requirements of the motor and the battery. The MOSFETs should be selected based on their maximum drain-source voltage and continuous current ratings, ensuring they can handle the expected load.
Similarly, the capacitors and inductors should have appropriate voltage and current ratings to withstand the electrical stresses in the circuit.
Heat Dissipation
ESCs generate heat during operation, primarily due to power losses in the MOSFETs. Proper heat dissipation is crucial to prevent overheating and ensure long-term reliability.
Heat sinks, cooling fans, and thermally conductive materials can be used to improve heat dissipation. The PCB layout should also be designed to minimize thermal resistance and promote airflow.
PCB Layout
A well-designed PCB layout is essential for optimal ESC performance. The layout should minimize parasitic inductances and capacitances, which can cause voltage spikes and ringing in the circuit.
The power and ground planes should be adequately sized to handle the expected currents, and the signal traces should be properly routed to avoid interference. Proper grounding techniques, such as star grounding or ground planes, should be employed to minimize ground loops and reduce noise.
Firmware Development
The microcontroller in the ESC circuit requires firmware to function properly. The firmware implements the control algorithms, handles communication with the external controller, and manages the MOSFETs and other peripherals.
Firmware development involves writing code in a language supported by the microcontroller, such as C or C++. The code should be optimized for performance and reliability, and it should include safety features like over-current protection and thermal shutdown.
There are several open-source firmware projects available for popular ESC microcontrollers, such as BLHeli and SimonK, which provide a good starting point for custom firmware development.
Frequently Asked Questions (FAQ)
1. Can I use any brushless DC motor with an ESC?
Not all brushless DC motors are compatible with every ESC. The motor’s voltage and current ratings must match the ESC’s specifications. Additionally, the number of poles and the kV rating of the motor should be considered when selecting an ESC.
2. How do I choose the right ESC for my application?
When choosing an ESC, consider the following factors:
- Voltage and current ratings: Ensure the ESC can handle the voltage and current requirements of your motor and battery.
- Continuous and peak current ratings: Select an ESC that can deliver the necessary continuous and peak currents for your application.
- Programming features: Look for an ESC with the desired programming options, such as adjustable timing, braking, and throttle calibration.
- Size and weight: Choose an ESC that fits within the space constraints of your application and minimizes weight for optimal performance.
3. What is the difference between a brushed and brushless ESC?
Brushed ESCs are designed to control brushed DC motors, while brushless ESCs are designed for brushless DC motors. Brushed ESCs are generally simpler and less expensive, but brushless ESCs offer higher efficiency, better performance, and longer motor life.
4. How do I troubleshoot an ESC that isn’t working properly?
If your ESC isn’t working as expected, try the following troubleshooting steps:
- Check the wiring and connections to ensure they are secure and free from damage.
- Verify that the battery is fully charged and supplying the correct voltage.
- Recalibrate the throttle to ensure the ESC is receiving the correct input signals.
- Check the ESC and motor for signs of overheating or physical damage.
- Consult the ESC manual or manufacturer’s support resources for specific troubleshooting guidelines.
5. Can I program my ESC to customize its performance?
Many modern ESCs support programming features that allow users to customize their performance. These features may include adjustable timing, braking strength, throttle calibration, and more. Programming is typically done using a specialized programming card or through a computer interface.
Before attempting to program your ESC, consult the manufacturer’s documentation to ensure compatibility and follow the provided instructions carefully.
Conclusion
ESC circuits play a crucial role in controlling brushless DC motors in various applications, from radio-controlled vehicles to drones and robotics. By understanding the components, working principles, and design considerations of ESC circuits, you can effectively select, implement, and troubleshoot these systems in your projects.
This ultimate guide has provided you with a comprehensive overview of ESC circuits, covering their key components, operation, practical applications, and frequently asked questions. Armed with this knowledge, you are now well-equipped to dive into the world of ESC circuits and take your motor control projects to new heights.
Remember to always prioritize safety, follow best practices in circuit design and firmware development, and consult manufacturer documentation and support resources when needed. With dedication and experimentation, you’ll soon master the art of ESC circuits and unlock a wide range of exciting possibilities in the realm of motor control.
No responses yet