What is ENEPIG?
ENEPIG is a surface finish that consists of three layers: electroless nickel, electroless palladium, and immersion gold. The nickel layer provides a barrier between the copper substrate and the other layers, preventing diffusion and oxidation. The palladium layer enhances the solderability and wire bondability of the surface finish, while the gold layer protects the palladium from oxidation and contamination.
Advantages of ENEPIG
- Excellent solderability
- High reliability
- Good wire bondability
- Suitable for fine-pitch applications
- Resistant to multiple reflow cycles
Disadvantages of ENEPIG
- Higher cost compared to ENIG
- Longer processing time
- Potential for palladium corrosion in harsh environments
What is ENIG?
ENIG is a surface finish that consists of two layers: electroless nickel and immersion gold. Like ENEPIG, the nickel layer acts as a barrier between the copper substrate and the gold layer, preventing diffusion and oxidation. The gold layer protects the nickel from oxidation and provides a solderable surface.
Advantages of ENIG
- Lower cost compared to ENEPIG
- Shorter processing time
- Good solderability
- Suitable for most applications
- Widely available
Disadvantages of ENIG
- Limited shelf life due to nickel oxidation
- Potential for black pad formation
- Not suitable for Wire Bonding
- May require additional surface preparation for fine-pitch applications
Comparing ENEPIG and ENIG
To better understand the differences between ENEPIG and ENIG, let’s compare them based on several key factors:
Factor | ENEPIG | ENIG |
---|---|---|
Solderability | Excellent | Good |
Wire Bondability | Good | Poor |
Reliability | High | Moderate |
Cost | Higher | Lower |
Processing Time | Longer | Shorter |
Shelf Life | Longer | Limited |
Fine-Pitch Suitability | Excellent | May require additional preparation |
Reflow Resistance | High | Moderate |
As shown in the table above, ENEPIG generally outperforms ENIG in terms of solderability, wire bondability, reliability, and suitability for fine-pitch applications. However, ENIG has the advantage of lower cost and shorter processing time.
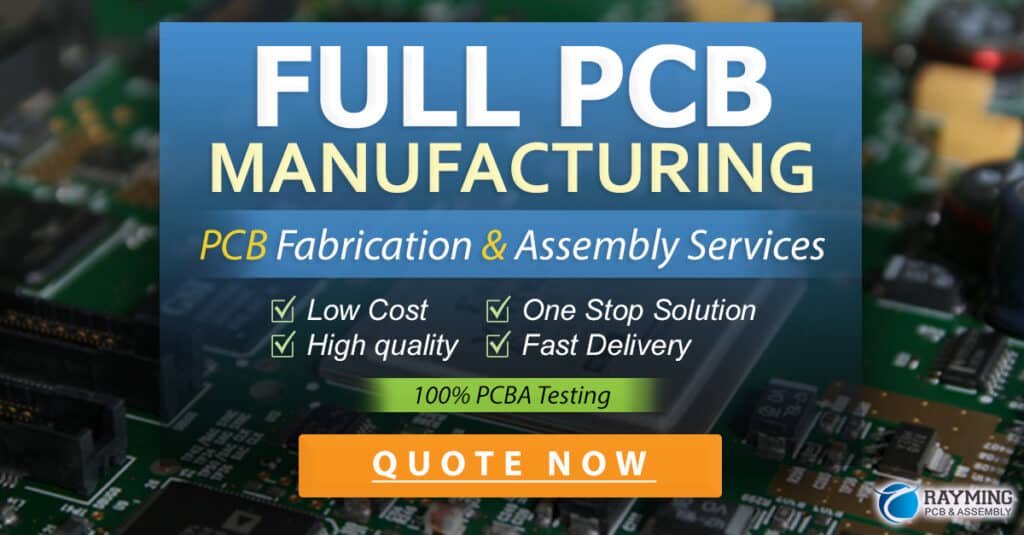
Application-Specific Considerations
When choosing between ENEPIG and ENIG, it’s essential to consider the specific requirements of your application. Here are some factors to keep in mind:
Solderability
If your application requires excellent solderability, ENEPIG is the better choice. The palladium layer in ENEPIG enhances the wetting and spreading of solder, resulting in more reliable solder joints.
Wire Bonding
For applications that require wire bonding, ENEPIG is the clear winner. The palladium layer in ENEPIG provides a suitable surface for wire bonding, whereas ENIG is not recommended for wire bonding due to the potential for nickel oxidation and poor adhesion.
Cost
If cost is a primary concern, ENIG may be the better option. ENEPIG is generally more expensive than ENIG due to the additional palladium layer and longer processing time.
Shelf Life
ENEPIG has a longer shelf life compared to ENIG. The palladium layer in ENEPIG protects the nickel from oxidation, whereas the nickel in ENIG is susceptible to oxidation over time, leading to a limited shelf life.
Fine-Pitch Applications
For fine-pitch applications, ENEPIG is the preferred choice. The palladium layer in ENEPIG provides a smooth, even surface that is suitable for fine-pitch components. ENIG may require additional surface preparation for fine-pitch applications.
Environmental Considerations
In addition to application-specific factors, it’s important to consider the environmental impact of the surface finish. Both ENEPIG and ENIG use chemicals that can be harmful to the environment if not properly managed.
ENEPIG uses a palladium bath, which can contain hazardous substances such as palladium chloride and hydrochloric acid. Proper disposal and treatment of the palladium bath are essential to minimize environmental impact.
ENIG uses a gold bath that may contain cyanide compounds, which are highly toxic. Proper handling, storage, and disposal of the gold bath are crucial to ensure the safety of workers and the environment.
When choosing a surface finish, it’s important to work with a reputable PCB manufacturer that adheres to environmental regulations and best practices.
Frequently Asked Questions (FAQ)
-
Q: Can ENEPIG be used for both leaded and lead-free soldering?
A: Yes, ENEPIG is suitable for both leaded and lead-free soldering processes. -
Q: Is ENIG suitable for high-temperature applications?
A: ENIG is suitable for most high-temperature applications, but its performance may degrade after multiple reflow cycles. ENEPIG is a better choice for applications that require resistance to multiple reflow cycles. -
Q: Can ENEPIG be used for aluminum wire bonding?
A: Yes, ENEPIG is suitable for aluminum wire bonding due to the palladium layer, which provides a compatible surface for bonding. -
Q: How does the shelf life of ENEPIG compare to ENIG?
A: ENEPIG has a longer shelf life compared to ENIG. The palladium layer in ENEPIG protects the nickel from oxidation, whereas the nickel in ENIG is susceptible to oxidation over time, leading to a limited shelf life. -
Q: Is it possible to rework components on ENEPIG and ENIG surface finishes?
A: Yes, both ENEPIG and ENIG allow for component rework. However, the rework process may be more challenging on ENEPIG due to the presence of the palladium layer.
Conclusion
In conclusion, both ENEPIG and ENIG have their advantages and disadvantages. ENEPIG offers superior solderability, wire bondability, and reliability, making it the better choice for applications that require these properties. However, ENIG is a lower-cost option with a shorter processing time, making it suitable for most general-purpose applications.
When deciding between ENEPIG and ENIG, it’s crucial to consider the specific requirements of your application, including solderability, wire bonding, cost, shelf life, and fine-pitch suitability. Additionally, environmental factors and the reputation of the PCB manufacturer should be taken into account.
By understanding the differences between ENEPIG and ENIG and considering the factors discussed in this article, you can make an informed decision on which surface finish is better suited for your specific application.
No responses yet