What is ENEPIG?
ENEPIG is a surface finish that consists of three layers: an electroless nickel base layer, an electroless palladium middle layer, and an immersion gold top layer. The nickel layer provides a barrier against copper diffusion, while the palladium layer enhances solderability and acts as a barrier between the nickel and gold layers. The immersion gold layer protects the palladium from oxidation and provides a surface that is easy to solder.
Advantages of ENEPIG
- Excellent solderability
- High durability and wear resistance
- Suitable for multiple reflow cycles
- Compatible with a wide range of soldering methods, including lead-free and low-temperature soldering
- Stable contact resistance
- Resistant to black pad formation
Disadvantages of ENEPIG
- Higher cost compared to ENIG
- More complex manufacturing process
- Potential for palladium corrosion in high-sulfur environments
- Possible nickel corrosion in acidic environments
What is ENIG?
ENIG is a surface finish that consists of two layers: an electroless nickel base layer and an immersion gold top layer. The nickel layer provides a barrier against copper diffusion and enhances the mechanical strength of the surface, while the immersion gold layer protects the nickel from oxidation and provides a solderable surface.
Advantages of ENIG
- Good solderability
- Lower cost compared to ENEPIG
- Simpler manufacturing process
- Suitable for most soldering methods
- Resistant to oxidation and corrosion
- Suitable for wire bonding and tape automated bonding (TAB)
Disadvantages of ENIG
- Limited number of reflow cycles
- Potential for black pad formation
- Possible nickel corrosion in acidic environments
- Reduced shelf life compared to ENEPIG
Comparison of ENEPIG and ENIG
To better understand the differences between ENEPIG and ENIG, let’s compare their key characteristics:
Characteristic | ENEPIG | ENIG |
---|---|---|
Layers | Nickel, Palladium, Gold | Nickel, Gold |
Solderability | Excellent | Good |
Durability | High | Moderate |
Reflow Cycles | Multiple | Limited |
Cost | Higher | Lower |
Shelf Life | Longer | Shorter |
Black Pad Resistance | High | Low |
Corrosion Resistance | High (except high-sulfur environments) | Moderate |
As shown in the table, ENEPIG offers superior solderability, durability, and resistance to black pad formation compared to ENIG. However, these benefits come at a higher cost and require a more complex manufacturing process.
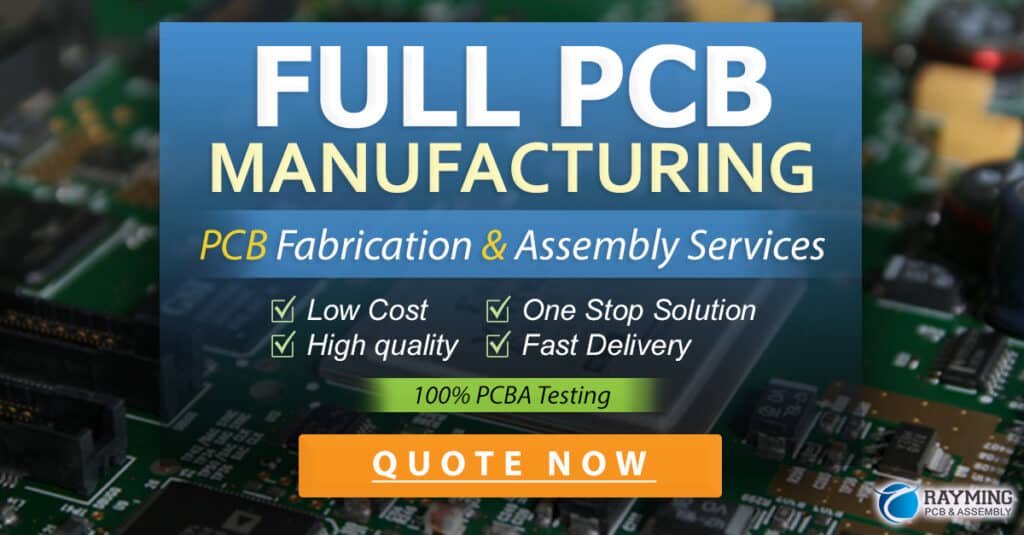
Applications of ENEPIG and ENIG
Both ENEPIG and ENIG are widely used in various electronics applications, including:
ENEPIG Applications
- High-reliability products (e.g., aerospace, medical, and military)
- Devices requiring multiple reflow cycles
- Fine-pitch components and high-density interconnects (HDI)
- Applications requiring stable contact resistance
- Automotive electronics
ENIG Applications
- Consumer electronics
- Telecommunications equipment
- Industrial control systems
- Devices with limited reflow cycles
- Applications requiring wire bonding or TAB
Selecting the Right Surface Finish
When choosing between ENEPIG and ENIG, consider the following factors:
- Application requirements (e.g., reliability, solderability, and shelf life)
- Manufacturing process complexity and cost
- Compatibility with soldering methods and components
- Environmental factors (e.g., exposure to high-sulfur or acidic environments)
In general, ENEPIG is the preferred choice for high-reliability applications that require multiple reflow cycles and stable contact resistance. ENIG, on the other hand, is a cost-effective option for less demanding applications with limited reflow cycles.
FAQ
1. What is the main difference between ENEPIG and ENIG?
The main difference between ENEPIG and ENIG is the presence of an additional electroless palladium layer in ENEPIG. This layer enhances solderability and acts as a barrier between the nickel and gold layers, resulting in superior performance compared to ENIG.
2. Is ENEPIG always the better choice?
No, ENEPIG is not always the better choice. While it offers superior performance in terms of solderability, durability, and resistance to black pad formation, it also comes at a higher cost and requires a more complex manufacturing process. The choice between ENEPIG and ENIG depends on the specific application requirements and budget constraints.
3. Can ENIG be used for high-reliability applications?
Yes, ENIG can be used for high-reliability applications, but it may not be the optimal choice. ENEPIG is generally preferred for high-reliability applications due to its superior performance and resistance to black pad formation.
4. What is black pad formation, and how does it affect surface finishes?
Black pad formation is a defect that occurs when the nickel layer becomes corroded or oxidized, resulting in a dark appearance and poor solderability. This defect is more common in ENIG surface finishes and can lead to joint failures. ENEPIG is more resistant to black pad formation due to the presence of the palladium layer.
5. Can ENEPIG and ENIG be used interchangeably?
While both ENEPIG and ENIG can be used for a wide range of applications, they are not always interchangeable. The choice between the two surface finishes depends on the specific requirements of the application, such as solderability, durability, and cost. In some cases, one finish may be more suitable than the other.
Conclusion
Choosing the right surface finish is crucial for ensuring the reliability, performance, and cost-effectiveness of PCBs. ENEPIG and ENIG are both popular options, each with its own advantages and disadvantages. By understanding the key differences between these surface finishes and considering the specific requirements of your application, you can make an informed decision and select the best option for your needs.
No responses yet