Introduction to ENEPIG
ENEPIG (Electroless Nickel Electroless Palladium Immersion Gold) is a robust and versatile surface finish for printed circuit boards (PCBs) and electronic components. This advanced plating technology offers superior protection against corrosion, wear, and environmental factors while providing excellent solderability and wire bonding capabilities. ENEPIG has gained popularity in various industries, including telecommunications, automotive, aerospace, and medical devices, due to its high performance and reliability.
What is ENEPIG?
ENEPIG is a multi-layer metal plating finish that consists of three distinct layers:
- Electroless Nickel (Ni): The first layer is a thin, uniform coating of nickel that provides a barrier against copper diffusion and enhances the adhesion of subsequent layers.
- Electroless Palladium (Pd): The second layer is a thin, uniform coating of palladium that prevents the formation of nickel oxide and improves solderability.
- Immersion Gold (Au): The final layer is a thin, uniform coating of gold that protects the underlying layers from oxidation and enhances wire bonding capabilities.
Advantages of ENEPIG
ENEPIG offers several advantages over other surface finishes, such as ENIG (Electroless Nickel Immersion Gold) and HASL (Hot Air Solder Leveling):
- Enhanced solderability: The combination of palladium and gold layers provides excellent wettability and solderability, ensuring reliable solder joints.
- Improved wire bonding: The gold layer enables strong and stable wire bonds, making ENEPIG suitable for applications that require wire bonding, such as semiconductor packaging.
- Increased durability: The nickel layer provides a strong barrier against copper diffusion, while the palladium and gold layers protect against oxidation and corrosion, resulting in a more durable surface finish.
- Compatibility with lead-free soldering: ENEPIG is compatible with lead-free soldering processes, making it an ideal choice for RoHS-compliant products.
- Extended shelf life: The multi-layer structure of ENEPIG ensures a longer shelf life compared to other surface finishes, reducing the risk of oxidation and contamination during storage.
ENEPIG Plating Process
The ENEPIG plating process involves several steps to achieve the desired multi-layer structure and properties. The following table outlines the typical steps in the ENEPIG plating process:
Step | Description |
---|---|
1. Cleaning | The PCB or component surface is cleaned to remove contaminants and ensure good adhesion of the subsequent layers. |
2. Microetching | The copper surface is microetched to create a uniform and active surface for plating. |
3. Electroless Nickel Plating | A thin, uniform layer of nickel is deposited onto the copper surface using an electroless plating process. |
4. Electroless Palladium Plating | A thin, uniform layer of palladium is deposited onto the nickel layer using an electroless plating process. |
5. Immersion Gold Plating | A thin, uniform layer of gold is deposited onto the palladium layer using an immersion plating process. |
6. Rinsing and Drying | The plated surface is rinsed with deionized water and dried to remove any residual chemicals. |
Electroless Nickel Plating
Electroless nickel plating is a chemical reduction process that deposits a uniform layer of nickel onto the copper surface without the use of an external electric current. The nickel layer serves as a barrier against copper diffusion and provides a strong foundation for the subsequent palladium and gold layers.
The electroless nickel plating process involves the following key components:
- Nickel source: A soluble nickel salt, such as nickel sulfate or nickel chloride, provides the nickel ions for plating.
- Reducing agent: A reducing agent, such as sodium hypophosphite, is used to reduce the nickel ions to metallic nickel.
- Complexing agents: Complexing agents, such as organic acids or amines, are used to control the reaction rate and maintain the stability of the plating bath.
- pH regulators: pH regulators, such as sodium hydroxide or sulfuric acid, are used to maintain the optimal pH range for the plating reaction.
- Stabilizers: Stabilizers, such as lead or bismuth compounds, are used to prevent the spontaneous decomposition of the plating bath.
The electroless nickel plating process is typically carried out at a temperature range of 80-90°C and a pH range of 4.5-5.5. The thickness of the nickel layer can be controlled by adjusting the plating time and bath composition, with typical thicknesses ranging from 3-8 µm.
Electroless Palladium Plating
Electroless palladium plating is a chemical reduction process that deposits a thin, uniform layer of palladium onto the nickel layer. The palladium layer serves as a barrier against nickel oxidation and provides excellent solderability and wire bonding capabilities.
The electroless palladium plating process involves the following key components:
- Palladium source: A soluble palladium salt, such as palladium chloride or palladium sulfate, provides the palladium ions for plating.
- Reducing agent: A reducing agent, such as sodium hypophosphite or dimethylamine borane, is used to reduce the palladium ions to metallic palladium.
- Complexing agents: Complexing agents, such as ethylenediamine or ammonia, are used to control the reaction rate and maintain the stability of the plating bath.
- pH regulators: pH regulators, such as sodium hydroxide or sulfuric acid, are used to maintain the optimal pH range for the plating reaction.
- Stabilizers: Stabilizers, such as thiourea or mercaptobenzothiazole, are used to prevent the spontaneous decomposition of the plating bath.
The electroless palladium plating process is typically carried out at a temperature range of 50-70°C and a pH range of 7.0-9.0. The thickness of the palladium layer is usually very thin, ranging from 0.05-0.2 µm, to minimize the risk of embrittlement and ensure good solderability.
Immersion Gold Plating
Immersion gold plating is a displacement reaction that deposits a thin, uniform layer of gold onto the palladium layer. The gold layer serves as a protective barrier against oxidation and contamination and provides excellent wire bonding capabilities.
The immersion gold plating process involves the following key components:
- Gold source: A soluble gold salt, such as potassium gold cyanide or sodium gold sulfite, provides the gold ions for plating.
- Complexing agents: Complexing agents, such as citric acid or ethylenediaminetetraacetic acid (EDTA), are used to control the reaction rate and maintain the stability of the plating bath.
- pH regulators: pH regulators, such as potassium hydroxide or sulfuric acid, are used to maintain the optimal pH range for the plating reaction.
- Stabilizers: Stabilizers, such as 2-mercaptobenzimidazole or thiourea, are used to prevent the spontaneous decomposition of the plating bath.
The immersion gold plating process is typically carried out at a temperature range of 60-80°C and a pH range of 5.0-7.0. The thickness of the gold layer is usually very thin, ranging from 0.05-0.2 µm, to ensure good solderability and wire bonding capabilities.
ENEPIG Applications
ENEPIG has found widespread use in various industries due to its superior performance and reliability. Some of the key applications of ENEPIG include:
Telecommunications
ENEPIG is widely used in the telecommunications industry for the production of high-frequency PCBs and components. The excellent solderability and wire bonding capabilities of ENEPIG make it an ideal choice for applications such as:
- 5G networks: ENEPIG-plated PCBs and components are used in the production of 5G base stations, antennas, and mobile devices, ensuring reliable high-speed data transmission.
- Fiber optic networks: ENEPIG is used in the production of optical transceivers, splitters, and connectors, providing a durable and corrosion-resistant surface finish for long-term reliability.
- Satellite communication: ENEPIG-plated components are used in satellite communication systems, where high reliability and resistance to harsh environmental conditions are critical.
Automotive
ENEPIG has gained popularity in the automotive industry due to its compatibility with lead-free soldering processes and its ability to withstand harsh environmental conditions. Some of the key automotive applications of ENEPIG include:
- Advanced driver assistance systems (ADAS): ENEPIG-plated PCBs and components are used in the production of ADAS, such as adaptive cruise control, lane departure warning, and automatic emergency braking systems.
- Infotainment systems: ENEPIG is used in the production of automotive infotainment systems, providing a reliable and durable surface finish for touchscreens, displays, and audio components.
- Electric vehicles (EVs): ENEPIG-plated components are used in the production of EV power electronics, such as inverters, converters, and battery management systems, ensuring high performance and reliability.
Aerospace
ENEPIG is widely used in the aerospace industry due to its ability to withstand extreme temperatures, vibrations, and corrosive environments. Some of the key aerospace applications of ENEPIG include:
- Avionics: ENEPIG-plated PCBs and components are used in the production of aircraft avionics systems, such as flight control computers, navigation systems, and communication equipment.
- Satellite systems: ENEPIG is used in the production of satellite components, such as solar panels, power systems, and communication modules, providing a durable and reliable surface finish for long-term operation in space.
- Defense systems: ENEPIG-plated components are used in the production of military aerospace systems, such as radar, electronic warfare, and missile guidance systems, ensuring high performance and reliability in hostile environments.
Medical Devices
ENEPIG has found applications in the medical device industry due to its biocompatibility, durability, and resistance to sterilization processes. Some of the key medical device applications of ENEPIG include:
- Implantable devices: ENEPIG-plated components are used in the production of implantable medical devices, such as pacemakers, defibrillators, and neurostimulators, providing a biocompatible and corrosion-resistant surface finish.
- Diagnostic equipment: ENEPIG is used in the production of medical diagnostic equipment, such as ultrasound machines, X-ray systems, and MRI scanners, ensuring reliable performance and long-term durability.
- Surgical instruments: ENEPIG-plated components are used in the production of surgical instruments, such as endoscopes, laparoscopic tools, and electrosurgical devices, providing a durable and sterilization-resistant surface finish.
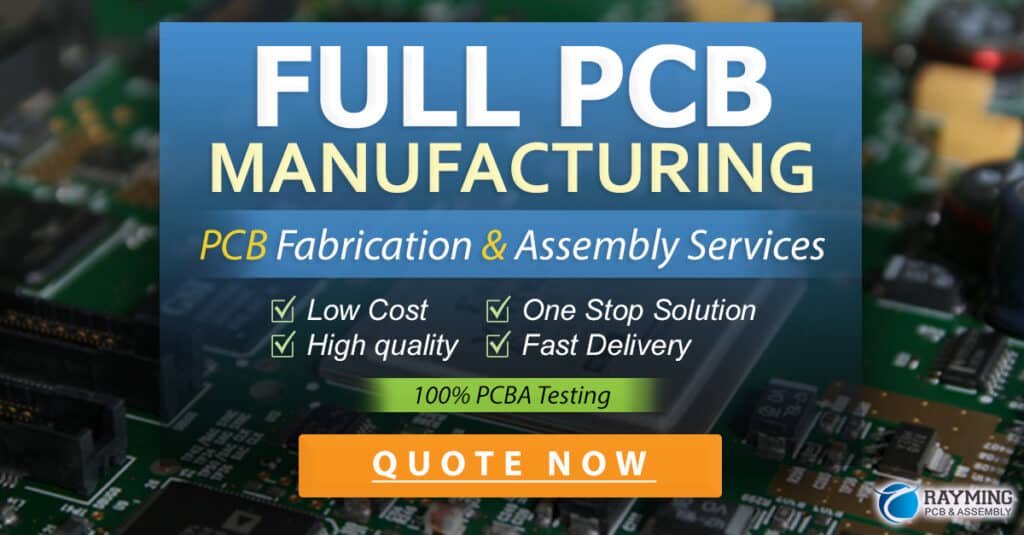
ENEPIG vs. Other Surface Finishes
ENEPIG offers several advantages over other common surface finishes, such as ENIG, HASL, and OSP (Organic Solderability Preservative). The following table compares the key properties of ENEPIG with these surface finishes:
Property | ENEPIG | ENIG | HASL | OSP |
---|---|---|---|---|
Solderability | Excellent | Good | Good | Fair |
Wire Bonding | Excellent | Fair | Poor | Poor |
Durability | Excellent | Good | Fair | Poor |
Shelf Life | 12+ months | 6-12 months | 3-6 months | 1-3 months |
Lead-Free Compatibility | Excellent | Good | Fair | Good |
Cost | High | Medium | Low | Low |
As evident from the table, ENEPIG surpasses other surface finishes in terms of solderability, wire bonding capabilities, durability, and shelf life. However, it is also the most expensive option due to the multi-layer plating process and the use of precious metals like palladium and gold.
Frequently Asked Questions (FAQ)
- Q: What is the typical thickness of the ENEPIG plating layers?
A: The typical thicknesses of the ENEPIG plating layers are: - Electroless Nickel (Ni): 3-8 µm
- Electroless Palladium (Pd): 0.05-0.2 µm
-
Immersion Gold (Au): 0.05-0.2 µm
-
Q: Is ENEPIG compatible with lead-free soldering processes?
A: Yes, ENEPIG is fully compatible with lead-free soldering processes, making it an ideal choice for RoHS-compliant products. -
Q: Can ENEPIG be used for wire bonding applications?
A: Yes, ENEPIG provides excellent wire bonding capabilities due to the presence of the gold layer, making it suitable for applications that require wire bonding, such as semiconductor packaging. -
Q: How does ENEPIG compare to ENIG in terms of cost?
A: ENEPIG is generally more expensive than ENIG due to the additional palladium layer and the more complex plating process. However, the superior performance and reliability of ENEPIG often justify the higher cost in critical applications. -
Q: What is the typical shelf life of ENEPIG-plated PCBs and components?
A: ENEPIG-plated PCBs and components typically have a shelf life of 12 months or more, depending on the storage conditions. The multi-layer structure of ENEPIG provides excellent protection against oxidation and contamination, ensuring a longer shelf life compared to other surface finishes.
Conclusion
ENEPIG is a high-performance surface finish that offers superior solderability, wire bonding capabilities, durability, and shelf life compared to other common surface finishes. The multi-layer structure of ENEPIG, consisting of electroless nickel, electroless palladium, and immersion gold, provides a robust and reliable protection against corrosion, wear, and environmental factors.
The wide range of applications for ENEPIG, spanning telecommunications, automotive, aerospace, and medical devices, demonstrates its versatility and ability to meet the demanding requirements of various industries. As electronic devices continue to become more complex and operate in increasingly harsh environments, the adoption of ENEPIG is expected to grow further.
While ENEPIG is more expensive than other surface finishes, its superior performance and reliability often justify the higher cost in critical applications. As the electronics industry continues to prioritize product quality, reliability, and environmental sustainability, ENEPIG is poised to remain a preferred choice for high-performance PCBs and components.
No responses yet