Introduction to Embedded Passives Technology
Embedded passives technology has revolutionized the electronics industry by integrating passive components, such as resistors and capacitors, directly into the substrate of printed circuit boards (PCBs). This innovative approach offers numerous advantages, including reduced board size, improved signal integrity, and enhanced reliability. In this article, we will delve into the world of embedded passives technology, focusing on resistors and capacitors, with insights from Bruce Mahler, a leading expert from Ohmega Technologies.
The Need for Embedded Passives
As electronic devices continue to shrink in size while increasing in functionality, the demand for more compact and efficient PCB designs has never been greater. Traditional surface-mount technology (SMT) has limitations in terms of component density and signal integrity, which can be addressed by embedding passive components within the PCB substrate.
Benefits of Embedded Passives
-
Space Savings: By embedding resistors and capacitors into the PCB substrate, designers can significantly reduce the overall board size, allowing for more compact and lightweight electronic devices.
-
Improved Signal Integrity: Embedded passives minimize the distance between components, reducing parasitic inductance and capacitance, which leads to improved signal integrity and reduced electromagnetic interference (EMI).
-
Enhanced Reliability: With fewer solder joints and connections, embedded passives technology offers increased reliability compared to traditional SMT components, reducing the risk of failure due to mechanical stress or thermal cycling.
-
Cost Reduction: Although the initial fabrication costs may be higher, embedded passives can lead to overall cost savings by reducing the number of components, simplifying assembly processes, and improving yield rates.
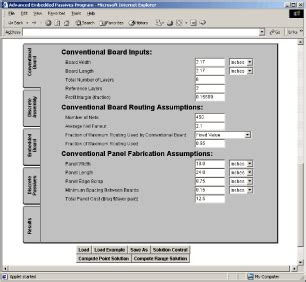
Embedded Resistor Technology
Embedded resistor technology allows for the integration of resistive elements directly into the PCB substrate. Ohmega Technologies, a leading provider of embedded resistor solutions, offers a proprietary process called OhmegaPly®.
OhmegaPly® Embedded Resistors
OhmegaPly® is a thin, resistive material that can be embedded into the inner layers of a PCB. This material is composed of a specialized polymer thick film (PTF) that is screen-printed onto a copper foil substrate. The PTF material is then cured and laminated with other PCB layers using standard fabrication processes.
Property | Value |
---|---|
Sheet Resistance Range | 10 Ω/sq to 1 MΩ/sq |
Tolerance | ±5%, ±10%, ±20% |
Temperature Coefficient (TCR) | ±100 ppm/°C, ±250 ppm/°C |
Power Dissipation | Up to 2 W/in² (31 mW/cm²) |
Voltage Rating | Up to 500 V |
OhmegaPly® embedded resistors offer several advantages over traditional SMT resistors:
-
Planar Geometry: The planar design of OhmegaPly® resistors allows for better heat dissipation and improved power handling capabilities compared to cylindrical SMT resistors.
-
Customizable Resistance Values: By adjusting the resistor geometry and material composition, designers can achieve a wide range of resistance values to meet specific circuit requirements.
-
Reduced Parasitics: Embedded resistors minimize parasitic inductance and capacitance, which is particularly beneficial for high-frequency applications.
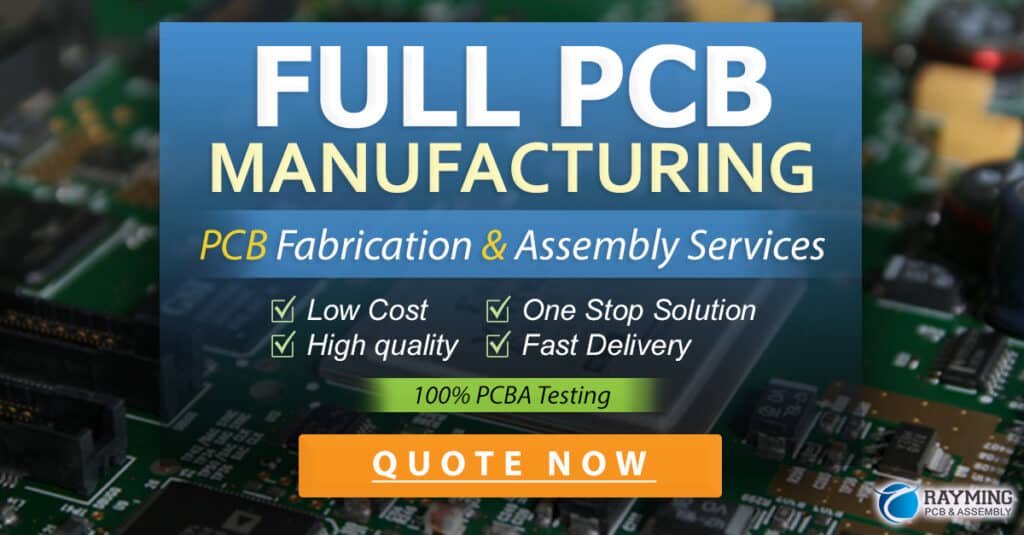
Embedded Capacitor Technology
Embedded capacitor technology enables the integration of capacitive elements within the PCB substrate, offering similar benefits to embedded resistors in terms of space savings, signal integrity, and reliability.
Dielectric Materials for Embedded Capacitors
Several dielectric materials can be used for embedded capacitors, each with its own set of properties and advantages:
-
Ceramic-Filled Polymers: These materials offer high dielectric constants (typically 10-50) and can be applied using standard PCB fabrication processes, such as screen printing or inkjet printing.
-
High-K Laminates: High-K laminates are specialized PCB materials that have a high dielectric constant (typically 50-500) and can be used to create embedded capacitors with high capacitance densities.
-
Thin Film Dielectrics: Thin film dielectrics, such as barium titanate (BaTiO3) or strontium titanate (SrTiO3), offer ultra-high dielectric constants (1000-5000) and can be deposited using advanced fabrication techniques like sputtering or chemical vapor deposition (CVD).
Material | Dielectric Constant | Capacitance Density | Processing Method |
---|---|---|---|
Ceramic-Filled Polymers | 10-50 | 0.1-1 nF/cm² | Screen printing, inkjet |
High-K Laminates | 50-500 | 1-10 nF/cm² | Standard PCB fabrication |
Thin Film Dielectrics | 1000-5000 | 10-100 nF/cm² | Sputtering, CVD |
Design Considerations for Embedded Capacitors
When designing embedded capacitors, several factors must be considered to ensure optimal performance and reliability:
-
Capacitance Value: The desired capacitance value will determine the choice of dielectric material, layer thickness, and capacitor geometry.
-
Voltage Rating: The embedded capacitor must be designed to withstand the expected voltage levels in the circuit, considering both the dielectric strength of the material and the spacing between conductive layers.
-
Frequency Response: The embedded capacitor’s frequency response should be evaluated to ensure it meets the requirements of the intended application, taking into account factors such as self-resonance frequency and quality factor (Q).
-
Thermal Stability: The dielectric material’s temperature coefficient of capacitance (TCC) should be considered to ensure stable performance over the expected operating temperature range.
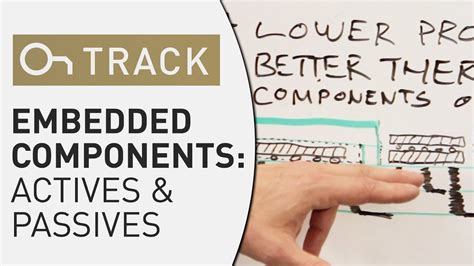
Applications of Embedded Passives Technology
Embedded passives technology finds applications in a wide range of industries and products, including:
-
Consumer Electronics: Smartphones, tablets, wearables, and other compact consumer devices benefit from the space savings and performance improvements offered by embedded passives.
-
Automotive Electronics: Embedded passives enable the development of more reliable and space-efficient automotive control modules, sensors, and infotainment systems.
-
Aerospace and Defense: Embedded passives technology is crucial for developing compact, lightweight, and robust electronic systems for aerospace and defense applications, such as avionics, satellite communications, and radar.
-
Medical Devices: Embedded passives help miniaturize medical implants, diagnostic equipment, and monitoring devices while ensuring high reliability and signal integrity.
-
Internet of Things (IoT): As IoT devices continue to proliferate, embedded passives technology enables the development of smaller, more energy-efficient, and cost-effective sensor nodes and communication modules.
Future Trends and Challenges
As embedded passives technology continues to evolve, several trends and challenges are expected to shape its future development:
-
Higher Capacitance Densities: Researchers are exploring new dielectric materials and fabrication techniques to achieve even higher capacitance densities, enabling further miniaturization and performance improvements.
-
Integration with Active Components: The integration of embedded passives with active components, such as transistors and ICs, is an area of active research, aiming to create highly integrated and efficient system-in-package (SiP) solutions.
-
3D Integration: The development of 3D embedded passives technology, where passive components are integrated vertically within the PCB stack, offers the potential for even greater space savings and design flexibility.
-
Standardization and Design Automation: The development of industry-wide standards and design automation tools for embedded passives will be crucial for wider adoption and more efficient design processes.
-
Manufacturing Challenges: As embedded passives technology becomes more complex, manufacturers will need to address challenges related to material compatibility, process control, and testing to ensure high yields and reliability.
Frequently Asked Questions (FAQ)
-
What are embedded passives?
Embedded passives are resistors, capacitors, and inductors that are integrated directly into the substrate of a printed circuit board (PCB) instead of being mounted on the surface as discrete components. -
What are the benefits of using embedded passives technology?
The benefits of embedded passives technology include reduced board size, improved signal integrity, enhanced reliability, and potential cost savings through simplified assembly processes and higher yield rates. -
What materials are used for embedded resistors?
Embedded resistors are typically made using thin film materials, such as nichrome (NiCr) or tantalum nitride (TaN), or polymer thick film (PTF) materials, like the OhmegaPly® technology offered by Ohmega Technologies. -
What are the dielectric materials used for embedded capacitors?
Embedded capacitors can be fabricated using ceramic-filled polymers, high-K laminates, or thin film dielectrics, such as barium titanate (BaTiO3) or strontium titanate (SrTiO3), depending on the desired capacitance density and performance characteristics. -
What are some of the industries and applications that benefit from embedded passives technology?
Embedded passives technology finds applications in various industries, including consumer electronics, automotive electronics, aerospace and defense, medical devices, and the Internet of Things (IoT), where miniaturization, reliability, and performance are critical factors.
Conclusion
Embedded passives technology, particularly embedded resistors and capacitors, offers a promising solution for the ever-increasing demands of electronic miniaturization and performance. By integrating passive components directly into the PCB substrate, designers can achieve significant space savings, improved signal integrity, and enhanced reliability.
As highlighted by Bruce Mahler from Ohmega Technologies, advancements in materials science and fabrication processes, such as the OhmegaPly® embedded resistor technology, are enabling the development of more sophisticated and efficient embedded passive solutions.
Looking ahead, the continued evolution of embedded passives technology, along with trends such as higher capacitance densities, integration with active components, and 3D integration, will play a crucial role in shaping the future of electronics design and manufacturing.
However, to fully realize the potential of embedded passives, the industry must address challenges related to standardization, design automation, and manufacturing processes. By collaborating and innovating, companies like Ohmega Technologies and the broader electronics community can overcome these hurdles and unlock new possibilities for the next generation of electronic devices.
No responses yet