Understanding the Unique Requirements of Industrial IoT in Manufacturing
Harsh Environmental Conditions
One of the primary challenges in designing electronics for Industrial IoT in manufacturing is the harsh environmental conditions that these devices must withstand. Manufacturing facilities often have:
- High temperatures
- Vibrations
- Dust and debris
- Electromagnetic interference (EMI)
PCB designers must ensure that their designs can operate reliably under these conditions, which may require the use of specialized components, protective coatings, and robust packaging.
Real-time Data Processing and Communication
Industrial IoT devices in manufacturing must be capable of processing and communicating data in real-time to enable timely decision-making and process optimization. This requires:
- High-speed data processing capabilities
- Reliable wireless communication protocols
- Low latency networks
PCB designers should select components and design their boards to support these requirements, ensuring that the devices can handle the necessary data throughput and communicate effectively with other systems.
Scalability and Interoperability
As manufacturing facilities adopt more IoT devices, scalability and interoperability become critical concerns. PCB designers should consider:
- Standardized communication protocols
- Modular design approaches
- Compatibility with existing systems
By designing electronics that can easily integrate with other devices and systems, PCB designers can facilitate the growth and expansion of Industrial IoT networks in manufacturing.
Key Considerations for PCB Design in Industrial IoT Manufacturing
Component Selection
Selecting the right components is crucial for ensuring the reliability and performance of Industrial IoT devices in manufacturing. PCB designers should consider:
- Temperature ratings
- Vibration resistance
- Power consumption
- Electromagnetic compatibility (EMC)
By choosing components that are designed for industrial environments and meet the specific requirements of the application, PCB designers can minimize the risk of device failure and ensure optimal performance.
Circuit Protection
Given the harsh conditions in manufacturing environments, circuit protection is essential for preventing damage to sensitive components and ensuring device longevity. PCB designers should incorporate:
- Transient voltage suppression (TVS) diodes
- Fuses and resettable fuses (PTC)
- Electromagnetic interference (EMI) filters
- Electrostatic discharge (ESD) protection
By implementing appropriate circuit protection measures, PCB designers can safeguard their designs against electrical disturbances, surges, and other potential hazards.
Thermal Management
High temperatures in manufacturing environments can lead to component failure and reduced device lifespan. PCB designers must implement effective thermal management strategies, such as:
- Proper component placement and spacing
- Use of thermal vias and heat sinks
- Selection of materials with good thermal conductivity
- Incorporation of temperature sensors for monitoring
By managing heat dissipation and ensuring that components operate within their specified temperature ranges, PCB designers can improve the reliability and longevity of Industrial IoT devices in manufacturing.
Wireless Connectivity
Wireless connectivity is a critical aspect of Industrial IoT in manufacturing, enabling devices to communicate and exchange data seamlessly. PCB designers must consider:
- Antenna design and placement
- RF shielding and grounding
- Compliance with wireless standards (e.g., Wi-Fi, Bluetooth, LoRaWAN)
- Coexistence of multiple wireless technologies
By optimizing wireless connectivity, PCB designers can ensure that Industrial IoT devices can communicate effectively and reliably within the manufacturing environment.
Power Management
Efficient power management is essential for ensuring the long-term operation of Industrial IoT devices in manufacturing. PCB designers should consider:
- Low-power component selection
- Power supply design and regulation
- Battery management and charging circuits
- Energy harvesting techniques
By implementing smart power management strategies, PCB designers can extend the battery life of devices, reduce maintenance requirements, and improve overall system efficiency.
Security Considerations
As Industrial IoT devices become more interconnected, security becomes a paramount concern. PCB designers should incorporate:
- Secure boot and firmware authentication
- Hardware-based encryption and key storage
- Tamper detection and prevention mechanisms
- Secure communication protocols
By designing with security in mind, PCB designers can help protect Industrial IoT devices and networks from unauthorized access, data breaches, and other security threats.
Best Practices for PCB Layout in Industrial IoT Manufacturing
Signal Integrity and EMC
Ensuring signal integrity and electromagnetic compatibility (EMC) is crucial for the reliable operation of Industrial IoT devices in manufacturing. PCB designers should:
- Minimize crosstalk and signal distortion
- Implement proper grounding and shielding techniques
- Adhere to EMC standards and regulations
- Conduct thorough testing and validation
By following best practices for signal integrity and EMC, PCB designers can minimize interference, improve signal quality, and ensure that devices perform as intended in the manufacturing environment.
Design for Manufacturing (DFM)
Designing for manufacturability is essential for ensuring the cost-effective and reliable production of Industrial IoT devices. PCB designers should:
- Adhere to manufacturing tolerances and constraints
- Minimize the use of complex or custom components
- Incorporate testability features for automated testing
- Collaborate closely with manufacturing partners
By considering manufacturing requirements early in the design process and following DFM principles, PCB designers can streamline production, reduce costs, and improve the overall quality of Industrial IoT devices.
Firmware Development and Integration
Firmware development and integration are critical aspects of Industrial IoT device design. PCB designers should:
- Work closely with firmware developers to ensure hardware-software compatibility
- Provide adequate resources (e.g., memory, processing power) for firmware functionality
- Implement firmware update and remote management capabilities
- Conduct thorough testing and validation of firmware-hardware integration
By collaborating effectively with firmware developers and ensuring seamless integration, PCB designers can create Industrial IoT devices that are feature-rich, reliable, and easy to maintain.
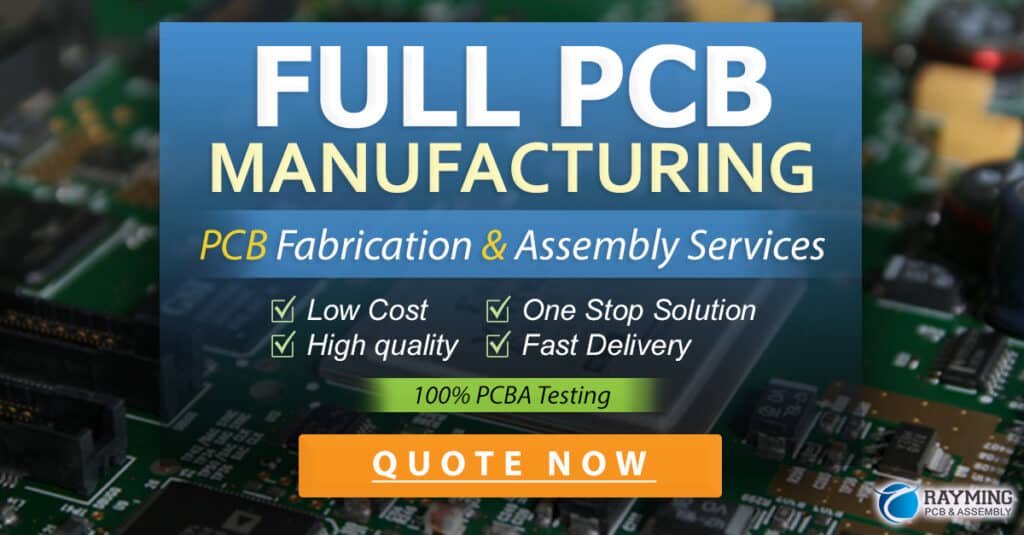
Frequently Asked Questions (FAQ)
1. What are the most important considerations when selecting components for Industrial IoT devices in manufacturing?
When selecting components for Industrial IoT devices in manufacturing, the most important considerations are:
– Temperature ratings: Components must be able to withstand the high temperatures often found in manufacturing environments.
– Vibration resistance: Components should be resistant to the vibrations and shocks common in industrial settings.
– Power consumption: Low-power components are essential for ensuring long battery life and reducing maintenance requirements.
– Electromagnetic compatibility (EMC): Components must be designed to minimize electromagnetic interference and comply with relevant EMC standards.
2. How can PCB designers ensure the reliable wireless connectivity of Industrial IoT devices in manufacturing?
To ensure reliable wireless connectivity, PCB designers should:
– Optimize antenna design and placement for the specific environment and application.
– Implement proper RF shielding and grounding techniques to minimize interference.
– Ensure compliance with relevant wireless standards, such as Wi-Fi, Bluetooth, or LoRaWAN.
– Consider the coexistence of multiple wireless technologies and design to minimize cross-technology interference.
3. What are some effective thermal management strategies for Industrial IoT devices in manufacturing?
Effective thermal management strategies for Industrial IoT devices in manufacturing include:
– Proper component placement and spacing to minimize heat buildup and ensure adequate airflow.
– Use of thermal vias and heat sinks to dissipate heat away from sensitive components.
– Selection of materials with good thermal conductivity, such as copper or aluminum, for PCB substrates and heat spreaders.
– Incorporation of temperature sensors for monitoring and real-time adjustment of thermal management systems.
4. How can PCB designers address security concerns in Industrial IoT devices for manufacturing?
To address security concerns in Industrial IoT devices for manufacturing, PCB designers should:
– Implement secure boot and firmware authentication mechanisms to prevent unauthorized firmware modifications.
– Use hardware-based encryption and secure key storage to protect sensitive data and communications.
– Incorporate tamper detection and prevention mechanisms to alert operators of physical tampering attempts and prevent unauthorized access.
– Ensure that communication protocols are secure and resistant to common attacks, such as eavesdropping or man-in-the-middle attacks.
5. What are the benefits of following Design for Manufacturing (DFM) principles when creating Industrial IoT devices for manufacturing?
The benefits of following Design for Manufacturing (DFM) principles when creating Industrial IoT devices for manufacturing include:
– Reduced production costs by minimizing the use of complex or custom components and adhering to manufacturing tolerances.
– Improved reliability and quality by designing devices that are easily manufacturable and testable.
– Faster time-to-market by streamlining the production process and minimizing the need for design revisions.
– Enhanced collaboration between design and manufacturing teams, leading to more efficient problem-solving and innovation.
Conclusion
Designing electronics for Industrial IoT in manufacturing presents unique challenges and opportunities for PCB designers. By understanding the specific requirements of the manufacturing environment, selecting appropriate components, implementing robust circuit protection and thermal management strategies, and ensuring reliable wireless connectivity and security, PCB designers can create Industrial IoT devices that are reliable, efficient, and secure.
Moreover, by following best practices for PCB layout, such as ensuring signal integrity and EMC compliance, designing for manufacturability, and collaborating closely with firmware developers, PCB designers can streamline the development process and create devices that are well-suited for the demands of modern manufacturing.
As the adoption of Industrial IoT in manufacturing continues to grow, PCB designers who are well-versed in these principles and best practices will be well-positioned to contribute to the development of innovative and transformative solutions that drive efficiency, quality, and competitiveness in the manufacturing sector.
No responses yet