Understanding Obsolescence management
Obsolescence management is a critical aspect of electronic parts procurement and maintenance. It involves proactively addressing the challenges posed by the inevitable obsolescence of electronic components, which can have significant impacts on the longevity, reliability, and cost-effectiveness of electronic systems.
What is Electronic Parts Obsolescence?
Electronic parts obsolescence occurs when a component is no longer manufactured or supported by its original supplier. This can happen for various reasons, such as:
- Technological advancements rendering the part outdated
- Changes in market demand
- Supplier business decisions
- Regulatory changes (e.g., RoHS, REACH)
When a part becomes obsolete, it can be difficult or impossible to procure, which can lead to issues such as:
- Increased costs for replacement parts
- Reduced system reliability
- Extended downtime for repairs
- Redesign requirements
The Importance of Obsolescence Management
Effective obsolescence management is essential for organizations that rely on electronic systems, particularly those with long lifecycles or critical applications. By proactively addressing obsolescence issues, organizations can:
- Minimize the risk of system failures due to obsolete parts
- Reduce the costs associated with part procurement and system maintenance
- Extend the useful life of electronic systems
- Ensure the availability of replacement parts when needed
- Maintain system performance and reliability
Key Strategies for Obsolescence Management
There are several strategies that organizations can employ to effectively manage electronic parts obsolescence. These include:
1. Proactive Monitoring and Forecasting
One of the most important aspects of obsolescence management is staying informed about the status of electronic components. This involves:
- Monitoring supplier product discontinuation notices (PDNs)
- Tracking part lifecycles and estimated years to end-of-life
- Forecasting future obsolescence risks based on market trends and technological advancements
By proactively monitoring and forecasting obsolescence risks, organizations can identify potential issues early and take appropriate action to mitigate them.
2. Strategic Part Selection
When designing new electronic systems or upgrading existing ones, it’s important to consider obsolescence risks during the part selection process. This involves:
- Choosing parts with longer lifecycles and more stable supply chains
- Avoiding parts that are near end-of-life or have limited sources
- Considering alternative parts or technologies that may be more future-proof
By strategically selecting parts with lower obsolescence risks, organizations can reduce the likelihood of facing obsolescence issues down the line.
3. Inventory Management
Maintaining an appropriate inventory of critical electronic parts can help mitigate the impact of obsolescence. This involves:
- Identifying critical parts and determining appropriate stock levels
- Balancing the costs of holding inventory with the risks of part shortages
- Regularly reviewing and adjusting inventory levels based on obsolescence forecasts
Effective inventory management ensures that organizations have the necessary parts on hand to maintain and repair electronic systems, even if those parts become obsolete.
4. Aftermarket Sourcing
When a part becomes obsolete, organizations may need to turn to aftermarket sources to procure replacement parts. This involves:
- Identifying reliable aftermarket suppliers
- Verifying the quality and authenticity of aftermarket parts
- Negotiating pricing and delivery terms
Aftermarket sourcing can be a valuable strategy for maintaining electronic systems when original parts are no longer available, but it’s important to carefully vet suppliers and parts to ensure quality and reliability.
5. Design for Obsolescence
When designing new electronic systems, organizations can proactively address obsolescence risks by incorporating design strategies such as:
- Modular design to allow for easier part replacements
- Use of standard interfaces and protocols
- Incorporation of programmable logic devices (PLDs) or field-programmable gate arrays (FPGAs)
- Designing for backward compatibility
By designing systems with obsolescence in mind, organizations can reduce the impact of part obsolescence and extend the useful life of their electronic systems.
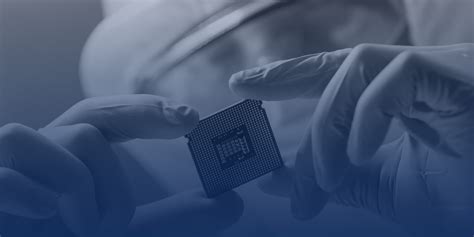
Implementing an Obsolescence Management Plan
To effectively manage electronic parts obsolescence, organizations should develop and implement a comprehensive obsolescence management plan. This plan should include:
1. Obsolescence Risk Assessment
The first step in developing an obsolescence management plan is to assess the risks posed by part obsolescence. This involves:
- Identifying critical electronic systems and their associated parts
- Analyzing the lifecycles and supply chains of those parts
- Assessing the potential impact of part obsolescence on system performance, reliability, and cost
By conducting a thorough risk assessment, organizations can prioritize their obsolescence management efforts and allocate resources accordingly.
2. Obsolescence Monitoring and Forecasting
As discussed earlier, proactive monitoring and forecasting are essential components of an effective obsolescence management plan. Organizations should establish processes and tools for:
- Regularly monitoring supplier PDNs and other obsolescence notifications
- Tracking part lifecycles and estimated years to end-of-life
- Forecasting future obsolescence risks based on market trends and technological advancements
This information should be regularly reviewed and updated to ensure that the obsolescence management plan remains current and effective.
3. Obsolescence Mitigation Strategies
Based on the results of the risk assessment and ongoing monitoring and forecasting, organizations should develop and implement appropriate obsolescence mitigation strategies. These may include:
- Strategic part selection for new designs or upgrades
- Inventory management to ensure the availability of critical parts
- Aftermarket sourcing to procure replacement parts when necessary
- Design for obsolescence to reduce the impact of part obsolescence over time
The specific strategies employed will depend on the unique needs and constraints of each organization and electronic system.
4. Obsolescence Management Policies and Procedures
To ensure consistent and effective obsolescence management, organizations should establish clear policies and procedures for:
- Roles and responsibilities of personnel involved in obsolescence management
- Communication and coordination between departments (e.g., engineering, procurement, maintenance)
- Documentation and record-keeping requirements
- Training and awareness programs for personnel
These policies and procedures should be regularly reviewed and updated to ensure they remain relevant and effective.
5. Continuous Improvement
Obsolescence management is an ongoing process, and organizations should continually assess and improve their obsolescence management plans. This involves:
- Regularly reviewing the effectiveness of obsolescence mitigation strategies
- Analyzing the impact of obsolescence events and identifying lessons learned
- Updating policies, procedures, and strategies based on new information and experiences
By embracing a continuous improvement mindset, organizations can ensure that their obsolescence management plans remain effective over time.
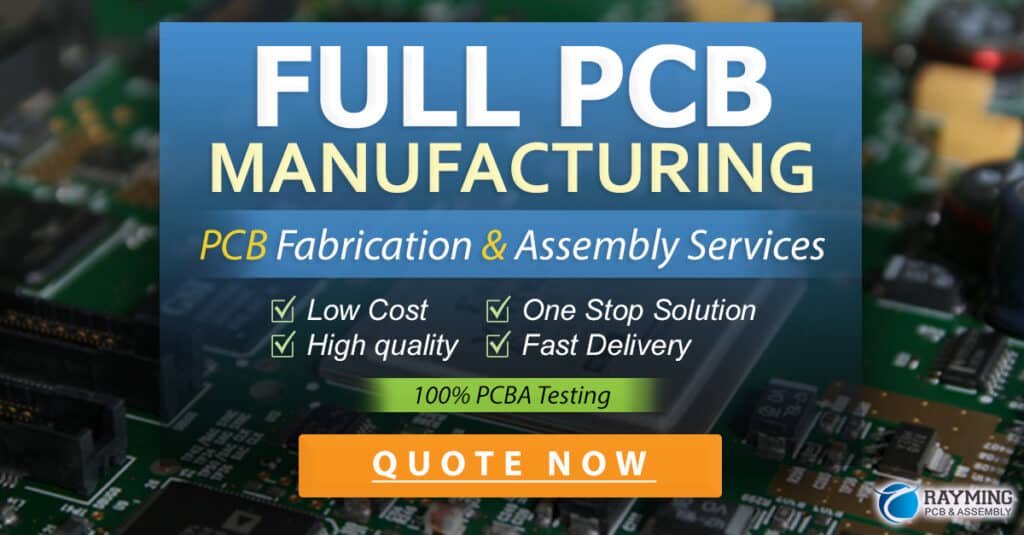
The Role of Collaboration in Obsolescence Management
Effective obsolescence management often requires collaboration between various stakeholders, both within and outside of an organization. This includes:
Internal Collaboration
Obsolescence management requires coordination and communication between various departments within an organization, such as:
- Engineering: Responsible for designing and maintaining electronic systems
- Procurement: Responsible for sourcing and purchasing electronic parts
- Maintenance: Responsible for repairing and servicing electronic systems
- Supply Chain: Responsible for managing inventory and logistics
By fostering collaboration and information sharing between these departments, organizations can ensure a more coordinated and effective approach to obsolescence management.
External Collaboration
Organizations may also need to collaborate with external stakeholders to effectively manage obsolescence, such as:
- Suppliers: Provide information on part lifecycles, discontinuations, and alternative parts
- Aftermarket Providers: Offer solutions for sourcing obsolete or hard-to-find parts
- Industry Associations: Provide resources, best practices, and networking opportunities related to obsolescence management
- Government Agencies: May offer guidance or requirements related to obsolescence management, particularly for industries such as aerospace and defense
By engaging with these external stakeholders, organizations can access valuable information, resources, and solutions to help manage obsolescence risks.
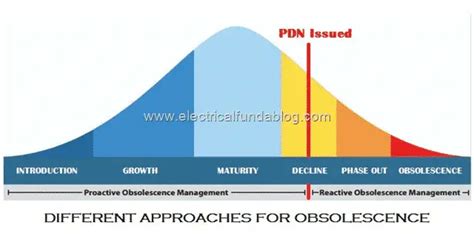
Best Practices for Obsolescence Management
To maximize the effectiveness of obsolescence management efforts, organizations should consider the following best practices:
1. Start Early
Obsolescence management should be incorporated into the design and planning stages of electronic systems, rather than being an afterthought. By considering obsolescence risks early on, organizations can make more informed decisions about part selection, design strategies, and lifecycle planning.
2. Prioritize Critical Systems and Parts
Not all electronic systems and parts pose the same level of obsolescence risk. Organizations should prioritize their obsolescence management efforts based on the criticality of each system and part, considering factors such as:
- Impact on system performance and reliability
- Cost and availability of replacement parts
- Safety and regulatory implications
By focusing on the most critical systems and parts first, organizations can ensure that their obsolescence management efforts are targeted and effective.
3. Use Data and Analytics
Effective obsolescence management requires accurate and timely data on part lifecycles, supply chain risks, and market trends. Organizations should invest in tools and processes for collecting, analyzing, and sharing this data, such as:
- Part databases and lifecycle management software
- Supply chain risk assessment tools
- Market intelligence and forecasting services
By leveraging data and analytics, organizations can make more informed decisions about obsolescence risks and mitigation strategies.
4. Foster a Culture of Obsolescence Awareness
Obsolescence management is not just the responsibility of a single department or individual. It requires a culture of awareness and collaboration across the entire organization. This can be fostered through:
- Regular training and education programs on obsolescence risks and management strategies
- Clear communication channels for sharing obsolescence-related information and concerns
- Recognition and incentives for proactive obsolescence management efforts
By embedding obsolescence awareness into the culture of the organization, obsolescence management can become a shared responsibility and priority.
5. Continuously Monitor and Adapt
Obsolescence risks and management strategies are not static. They evolve over time based on changes in technology, markets, and supply chains. Organizations should continuously monitor these changes and adapt their obsolescence management plans accordingly. This may involve:
- Regularly reviewing and updating risk assessments and mitigation strategies
- Adjusting inventory levels and sourcing strategies based on changing part availability and pricing
- Incorporating new technologies or design strategies to reduce obsolescence risks
By staying agile and adaptive, organizations can ensure that their obsolescence management efforts remain effective over the long term.
Frequently Asked Questions (FAQ)
1. What are the main causes of electronic parts obsolescence?
The main causes of electronic parts obsolescence include:
- Technological advancements that render parts outdated
- Changes in market demand for specific parts or technologies
- Supplier business decisions to discontinue certain parts or product lines
- Regulatory changes that restrict the use of certain materials or components
2. How can organizations predict and plan for electronic parts obsolescence?
Organizations can predict and plan for electronic parts obsolescence by:
- Monitoring supplier product discontinuation notices and other obsolescence notifications
- Tracking part lifecycles and estimated years to end-of-life
- Forecasting future obsolescence risks based on market trends and technological advancements
- Conducting regular obsolescence risk assessments and developing mitigation strategies
3. What are some strategies for mitigating the impact of electronic parts obsolescence?
Some strategies for mitigating the impact of electronic parts obsolescence include:
- Strategic part selection to choose components with longer lifecycles and more stable supply chains
- Inventory management to ensure the availability of critical parts
- Aftermarket sourcing to procure replacement parts when necessary
- Design for obsolescence to reduce the impact of part obsolescence over time
4. How can organizations ensure the quality and reliability of aftermarket parts?
Organizations can ensure the quality and reliability of aftermarket parts by:
- Carefully vetting aftermarket suppliers and their quality control processes
- Requesting and verifying documentation such as certificates of conformance and test reports
- Conducting incoming inspections and testing to verify part authenticity and performance
- Establishing clear quality requirements and communication channels with aftermarket suppliers
5. What role does collaboration play in effective obsolescence management?
Collaboration plays a crucial role in effective obsolescence management by:
- Fostering communication and coordination between internal departments such as engineering, procurement, and maintenance
- Enabling information sharing and problem-solving with external stakeholders such as suppliers, aftermarket providers, and industry associations
- Facilitating the development of industry-wide standards and best practices for obsolescence management
- Encouraging the sharing of resources and solutions to common obsolescence challenges
By working together, organizations can more effectively predict, plan for, and mitigate the risks posed by electronic parts obsolescence.
Conclusion
Electronic parts obsolescence is an inevitable challenge for organizations that rely on electronic systems. However, by proactively managing obsolescence risks through strategies such as monitoring, forecasting, strategic part selection, inventory management, aftermarket sourcing, and design for obsolescence, organizations can minimize the impact of obsolescence on system performance, reliability, and cost.
Effective obsolescence management requires a comprehensive plan that includes risk assessment, mitigation strategies, policies and procedures, and continuous improvement. It also requires collaboration and communication between various internal and external stakeholders, as well as a culture of obsolescence awareness and shared responsibility.
By embracing best practices such as starting early, prioritizing critical systems and parts, using data and analytics, fostering a culture of obsolescence awareness, and continuously monitoring and adapting, organizations can stay ahead of obsolescence risks and ensure the long-term viability of their electronic systems.
Ultimately, effective obsolescence management is not just a technical challenge, but a strategic imperative for organizations that want to maximize the value and longevity of their electronic systems. By making obsolescence management a priority and taking proactive steps to address it, organizations can position themselves for success in an ever-changing technological landscape.
No responses yet