What is Electronic Contract Manufacturing?
Electronic contract manufacturing, also known as electronics manufacturing services (EMS), involves outsourcing the production of electronic components, assemblies, and finished products to a specialized third-party manufacturer. ECM providers offer a range of services, including:
- Printed circuit board (PCB) assembly
- Cable and wire harness assembly
- Box build assembly
- Testing and quality control
- Supply chain management
- Design and engineering support
By partnering with an ECM provider, medical device companies can focus on their core competencies, such as research and development, marketing, and sales, while leaving the manufacturing process to experts in the field.
Why Use Electronic Contract Manufacturing for Medical Devices?
The medical devices industry is highly regulated, with strict requirements for quality, reliability, and safety. Medical devices must meet rigorous standards, such as those set by the U.S. Food and Drug Administration (FDA) and the European Union’s Medical Device Regulation (MDR). ECM providers that specialize in the medical devices industry have the expertise and certifications necessary to ensure compliance with these standards.
In addition to regulatory compliance, there are several other reasons why medical device companies choose to work with ECM providers:
Cost Savings
Outsourcing electronic manufacturing can significantly reduce costs compared to in-house production. ECM providers have economies of scale, allowing them to purchase components and materials at lower prices. They also have the necessary infrastructure, equipment, and skilled labor in place, eliminating the need for medical device companies to invest in their own manufacturing facilities.
Access to Advanced Technology
ECM providers invest in state-of-the-art manufacturing equipment and processes to stay competitive in the industry. Medical device companies can leverage this advanced technology without having to make significant capital investments themselves. This access to cutting-edge capabilities enables the development of more complex and innovative medical devices.
Flexibility and Scalability
Partnering with an ECM provider allows medical device companies to quickly ramp up or down production based on market demand. This flexibility is especially important in the medical devices industry, where product life cycles can be short, and demand can fluctuate based on factors such as regulatory approvals and reimbursement decisions.
Improved Time-to-Market
ECM providers have streamlined processes and expertise that can help medical device companies bring products to market faster. By leveraging the ECM provider’s supply chain relationships, design and engineering support, and manufacturing capabilities, medical device companies can reduce development timelines and accelerate product launches.
Choosing the Right Electronic Contract Manufacturer
When selecting an ECM provider for a medical device project, there are several key factors to consider:
Medical Device Experience
Look for an ECM provider with a proven track record in the medical devices industry. They should have experience manufacturing products similar to yours and a deep understanding of the regulatory requirements and quality standards specific to medical devices.
Quality Management System
Ensure that the ECM provider has a robust quality management system (QMS) in place that is certified to relevant standards, such as ISO 13485 for medical devices. The QMS should cover all aspects of the manufacturing process, from incoming material inspections to final product testing and release.
Manufacturing Capabilities
Assess the ECM provider’s manufacturing capabilities to ensure they can meet your specific product requirements. This includes their ability to handle the necessary volumes, component technologies, and assembly processes. Consider their experience with printed circuit board assembly, cable and wire harness assembly, and box build assembly for medical devices.
Design and Engineering Support
Some ECM providers offer design and engineering services to help optimize product designs for manufacturability, reliability, and cost-effectiveness. This value-added support can be particularly beneficial for medical device companies looking to innovate and improve their products.
Supply Chain Management
A strong ECM provider will have established relationships with component suppliers and a robust supply chain management process. They should be able to source high-quality components, manage inventory levels, and mitigate supply chain risks to ensure consistent and reliable production.
Communication and Collaboration
Effective communication and collaboration are essential for a successful partnership with an ECM provider. Look for a provider that values transparency, responsiveness, and proactive problem-solving. They should be willing to work closely with your team to understand your requirements, provide regular progress updates, and address any issues that arise.
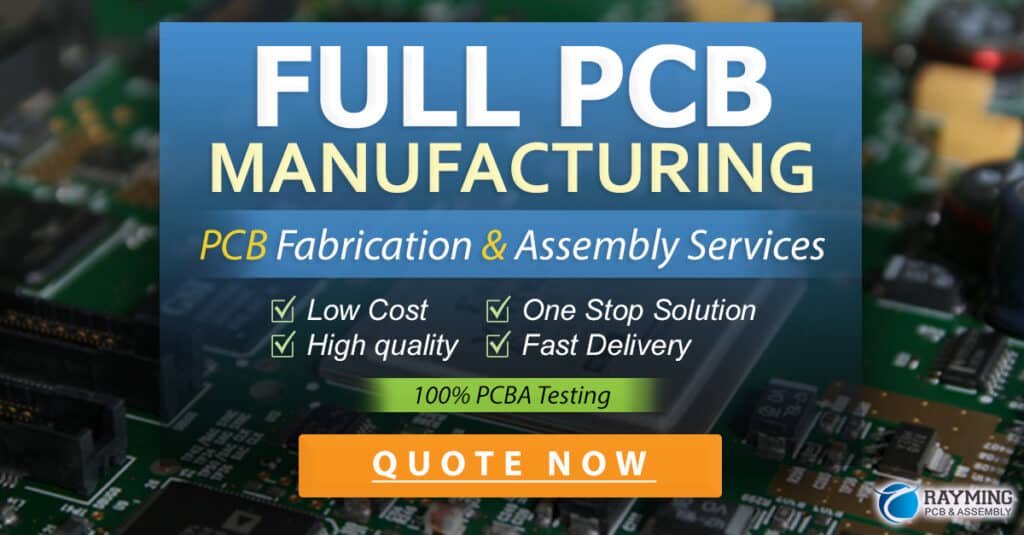
The ECM Process for Medical Devices
The electronic contract manufacturing process for medical devices typically involves the following steps:
-
Design and Engineering: The medical device company provides the product design files and specifications to the ECM provider. The ECM provider’s engineering team reviews the design for manufacturability, identifies potential improvements, and collaborates with the medical device company to finalize the design.
-
Prototyping and Testing: The ECM provider builds prototypes of the electronic assemblies and conducts initial testing to validate the design and identify any issues. This step helps to refine the design and ensure it meets the required performance and quality standards.
-
Component Sourcing: The ECM provider sources the necessary electronic components and materials from qualified suppliers. They manage the procurement process, ensure the quality of incoming materials, and maintain appropriate inventory levels to support production.
-
PCB Assembly: The ECM provider assembles the printed circuit boards using automated surface mount technology (SMT) and/or through-hole assembly processes. They follow strict process controls and use advanced inspection techniques to ensure the quality of the assembled PCBs.
-
Cable and Wire Harness Assembly: If the medical device requires custom cable and wire harness assemblies, the ECM provider will build these components according to the specifications provided. This step involves cutting, stripping, crimping, and soldering wires and connectors to create the desired assemblies.
-
Box Build Assembly: The ECM provider integrates the assembled PCBs, cable and wire harnesses, and other components into the final product enclosure or housing. This step may involve mechanical assembly, labeling, and packaging according to the medical device company’s requirements.
-
Testing and Quality Control: Throughout the manufacturing process, the ECM provider conducts rigorous testing and quality control checks to ensure the products meet the required performance, safety, and reliability standards. This may include in-circuit testing, functional testing, burn-in testing, and final inspection.
-
Packaging and Shipping: Once the final products have passed all quality checks, the ECM provider packages them according to the medical device company’s specifications and ships them to the designated location. They may also provide logistics support and manage the distribution process.
Regulatory Compliance for Medical Device ECM
Medical device ECM providers must comply with a range of regulations and standards to ensure the safety and effectiveness of the products they manufacture. Some of the key regulatory requirements include:
-
FDA Quality System Regulation (QSR): In the United States, medical device manufacturers must follow the FDA’s Quality System Regulation (21 CFR Part 820), which outlines requirements for design controls, document controls, purchasing controls, process controls, and corrective and preventive actions (CAPA).
-
ISO 13485: This international standard specifies requirements for a quality management system specific to the medical devices industry. It is harmonized with the FDA QSR and is widely recognized as a benchmark for medical device quality.
-
European Medical Device Regulation (MDR): In the European Union, medical devices must comply with the Medical Device Regulation (MDR) (EU) 2017/745, which sets requirements for the design, manufacture, and post-market surveillance of medical devices.
-
Good Manufacturing Practices (GMP): GMP guidelines outline best practices for manufacturing processes, facility design, equipment maintenance, and personnel training to ensure consistent product quality and safety.
ECM providers must maintain detailed documentation, conduct regular audits, and undergo inspections by regulatory bodies to demonstrate compliance with these requirements. They must also support medical device companies in their regulatory submissions, such as 510(k) premarket notifications or premarket approval applications (PMAs) in the United States.
The Benefits of Electronic Contract Manufacturing for Medical Devices
Partnering with an experienced and qualified electronic contract manufacturer offers numerous benefits for medical device companies:
Focus on Core Competencies
By outsourcing electronic manufacturing, medical device companies can focus on their core competencies, such as research and development, clinical trials, and marketing. This allows them to allocate resources more effectively and drive innovation in their products.
Cost Savings and Efficiency
ECM providers have optimized processes, economies of scale, and supply chain relationships that enable them to manufacture products more cost-effectively than in-house production. They can also help medical device companies reduce inventory costs by managing just-in-time delivery of components and finished products.
Access to Specialized Expertise
ECM providers have deep expertise in electronic manufacturing processes, quality control, and regulatory compliance specific to the medical devices industry. By leveraging this expertise, medical device companies can ensure their products are manufactured to the highest standards of quality and reliability.
Scalability and Flexibility
Outsourcing to an ECM provider allows medical device companies to scale production up or down based on market demand, without having to invest in additional equipment or personnel. This flexibility is particularly valuable in the dynamic and rapidly evolving medical devices industry.
Faster Time-to-Market
ECM providers can help medical device companies accelerate product development and commercialization timelines. By providing design and engineering support, managing the supply chain, and streamlining the manufacturing process, ECM providers can help bring new products to market faster.
Challenges and Risks in Medical Device ECM
While electronic contract manufacturing offers many benefits for medical device companies, there are also some challenges and risks to consider:
Intellectual Property Protection
Medical device companies must ensure their intellectual property is protected when outsourcing manufacturing to an ECM provider. This requires robust non-disclosure agreements (NDAs), intellectual property agreements, and secure data transfer protocols.
Communication and Coordination
Effective communication and coordination between the medical device company and the ECM provider are critical for successful outsourcing. Misunderstandings or lack of clarity in requirements can lead to delays, quality issues, or cost overruns.
Supply Chain Risks
Medical device companies rely on their ECM providers to manage the supply chain effectively. Disruptions in the supply of components or materials can impact production schedules and product availability. ECM providers must have robust risk management processes in place to mitigate supply chain risks.
Quality and Regulatory Compliance
Ensuring consistent quality and regulatory compliance is paramount in the medical devices industry. Medical device companies must conduct thorough due diligence on potential ECM partners, audit their quality management systems, and monitor their performance to mitigate quality and compliance risks.
The Future of Electronic Contract Manufacturing for Medical Devices
The medical devices industry is continually evolving, driven by advances in technology, changing healthcare needs, and regulatory developments. Electronic contract manufacturing will play an increasingly important role in supporting the industry’s growth and innovation:
Miniaturization and Complex Devices
As medical devices become smaller and more complex, ECM providers will need to invest in advanced manufacturing technologies and processes to support miniaturization and high-density electronic assemblies. This may include 3D printing, microelectronics assembly, and advanced packaging techniques.
Connected and Smart Devices
The growth of the Internet of Things (IoT) and connected health is driving the development of smart medical devices that can collect, transmit, and analyze data. ECM providers will need to develop capabilities in wireless technologies, sensors, and data security to support the production of these connected devices.
Personalized Medicine and Custom Devices
The trend towards personalized medicine and patient-specific treatments is creating demand for custom medical devices tailored to individual needs. ECM providers will need to be flexible and agile to support the manufacture of low-volume, high-mix products, while maintaining quality and cost-effectiveness.
Regulatory Harmonization
As medical device regulations continue to evolve and harmonize globally, ECM providers will need to stay up-to-date with the latest requirements and ensure their processes and documentation meet the necessary standards. Collaboration with medical device companies to navigate the regulatory landscape will be essential.
Sustainable and Eco-Friendly Manufacturing
There is growing pressure on the medical devices industry to adopt sustainable and eco-friendly manufacturing practices. ECM providers will need to incorporate environmental considerations into their processes, such as reducing waste, using renewable energy, and designing products for recyclability and disassembly.
FAQ
What is the difference between electronic contract manufacturing and in-house manufacturing for medical devices?
Electronic contract manufacturing involves outsourcing the production of electronic components and assemblies to a specialized third-party manufacturer. In-house manufacturing, on the other hand, means that the medical device company produces the components and assemblies themselves, using their own facilities, equipment, and personnel. Outsourcing to an ECM provider offers advantages such as cost savings, access to specialized expertise, and scalability, while in-house manufacturing provides greater control over the production process and intellectual property.
How do I choose the right electronic contract manufacturer for my medical device project?
When selecting an ECM provider for a medical device project, consider factors such as their experience in the medical devices industry, quality management system certifications, manufacturing capabilities, design and engineering support, supply chain management, and communication and collaboration practices. Conduct thorough due diligence, request references, and visit their facilities to assess their suitability for your project.
What regulations and standards apply to electronic contract manufacturing for medical devices?
Medical device ECM providers must comply with a range of regulations and standards, including the FDA Quality System Regulation (QSR), ISO 13485 for medical device quality management systems, the European Medical Device Regulation (MDR), and Good Manufacturing Practices (GMP) guidelines. Ensure your ECM partner has the necessary certifications and processes in place to meet these requirements.
How can I protect my intellectual property when outsourcing electronic manufacturing?
To protect your intellectual property when outsourcing to an ECM provider, implement robust non-disclosure agreements (NDAs), intellectual property agreements, and secure data transfer protocols. Clearly define ownership rights and confidentiality obligations in your contracts, and establish procedures for handling and storing sensitive information. Regular audits and monitoring can help ensure your ECM partner is adhering to the agreed-upon security measures.
What are the future trends in electronic contract manufacturing for medical devices?
The future of electronic contract manufacturing for medical devices is likely to be shaped by trends such as miniaturization and complex devices, connected and smart devices, personalized medicine and custom devices, regulatory harmonization, and sustainable and eco-friendly manufacturing. ECM providers will need to invest in advanced technologies, develop new capabilities, and adapt to the evolving needs of the medical devices industry to remain competitive and support innovation.
No responses yet