Introduction to Gold Finger Plating
Gold finger plating is a crucial process in the manufacturing of edge connectors, which are widely used in various electronic devices, such as computers, smartphones, and gaming consoles. The term “gold finger” refers to the gold-plated contact pads on the edge of a printed circuit board (PCB) that allow for reliable electrical connections when inserted into a corresponding socket or slot. The gold plating provides excellent conductivity, corrosion resistance, and durability, ensuring optimal performance and longevity of the electronic device.
What is Edge Connector Beveling?
Edge connector beveling is a process that involves creating a smooth, angled transition on the edges of the PCB where the gold fingers are located. This beveling process serves several purposes:
- Facilitates smooth insertion and removal of the edge connector into the mating socket or slot
- Reduces stress on the gold fingers during insertion and removal, preventing damage or delamination
- Improves the overall aesthetic appearance of the PCB
The beveling process is typically performed using specialized equipment, such as a PCB beveling machine or a CNC router, which can precisely control the angle and depth of the bevel cut.
Importance of Gold Finger Plating
Gold finger plating is essential for several reasons:
- Conductivity: Gold is an excellent conductor of electricity, ensuring reliable and efficient signal transmission between the edge connector and the mating socket or slot.
- Corrosion resistance: Gold is highly resistant to corrosion, which helps maintain the integrity of the electrical connections over time, even in harsh environmental conditions.
- Durability: Gold-plated contacts can withstand numerous insertion and removal cycles without significant wear or degradation, extending the lifespan of the electronic device.
- Low contact resistance: Gold-plated contacts exhibit low contact resistance, which minimizes signal loss and ensures optimal performance of the electronic device.
Gold Finger Plating Process
The gold finger plating process involves several steps to ensure a high-quality, durable finish on the edge connector contacts. The process typically includes the following stages:
1. PCB Fabrication and Preparation
Before the gold finger plating process can begin, the PCB must be fabricated according to the desired design specifications. This includes creating the necessary circuit traces, solder mask, and silk screen layers. Once the PCB is fabricated, it undergoes a cleaning process to remove any contaminants or debris that may interfere with the plating process.
2. Nickel Plating (Optional)
In some cases, a layer of nickel may be plated onto the copper contacts before the gold plating process. Nickel plating serves as a barrier layer between the copper and gold, preventing the formation of intermetallic compounds that can weaken the bond between the two metals. Additionally, nickel plating can improve the wear resistance and durability of the gold-plated contacts.
3. Gold Plating
The gold plating process is typically performed using an electroplating method, which involves the following steps:
- The PCB is immersed in a gold plating solution, which contains gold ions suspended in an electrolyte.
- An electrical current is applied to the PCB, causing the gold ions to be attracted to the exposed copper contacts on the edge of the board.
- As the gold ions reach the copper contacts, they are reduced to metallic gold, forming a thin, uniform layer on the surface of the contacts.
The thickness of the gold plating is carefully controlled to ensure optimal performance and durability of the edge connector. Typical gold plating thicknesses range from 0.05 to 0.30 micrometers (2 to 12 microinches).
4. Post-Plating Processes
After the gold plating process is complete, the PCB undergoes several post-plating processes to ensure a high-quality finish:
- Rinsing: The PCB is rinsed with deionized water to remove any residual plating solution or contaminants.
- Drying: The PCB is dried using hot air or an oven to remove any moisture that may have accumulated during the plating process.
- Inspection: The gold-plated contacts are inspected for uniformity, thickness, and any defects that may affect the performance of the edge connector.
Factors Affecting Gold Finger Plating Quality
Several factors can influence the quality and performance of gold-plated edge connector contacts:
1. Gold Plating Thickness
The thickness of the gold plating is a critical factor in determining the durability and performance of the edge connector. Insufficient gold plating thickness can lead to premature wear and exposure of the underlying copper, while excessive gold plating thickness can result in increased costs and potential issues with contact mating. The optimal gold plating thickness depends on the specific application and the expected number of insertion and removal cycles.
2. Gold Purity
The purity of the gold used in the plating process can also affect the performance of the edge connector. Higher purity gold (99.9% or greater) provides better conductivity and corrosion resistance compared to lower purity gold. However, higher purity gold is also more expensive, so a balance must be struck between cost and performance requirements.
3. Surface Finish
The surface finish of the gold-plated contacts can impact the reliability and longevity of the edge connector. A smooth, uniform surface finish ensures optimal contact mating and minimizes wear over time. Surface imperfections, such as pits, nodules, or scratches, can lead to increased contact resistance and reduced durability.
4. Edge Beveling Quality
The quality of the edge beveling process can also affect the performance of the gold-plated contacts. A well-executed edge bevel provides a smooth, gradual transition that facilitates easy insertion and removal of the edge connector. Poor edge beveling can result in abrupt edges that can cause damage to the gold fingers or the mating socket during insertion and removal.
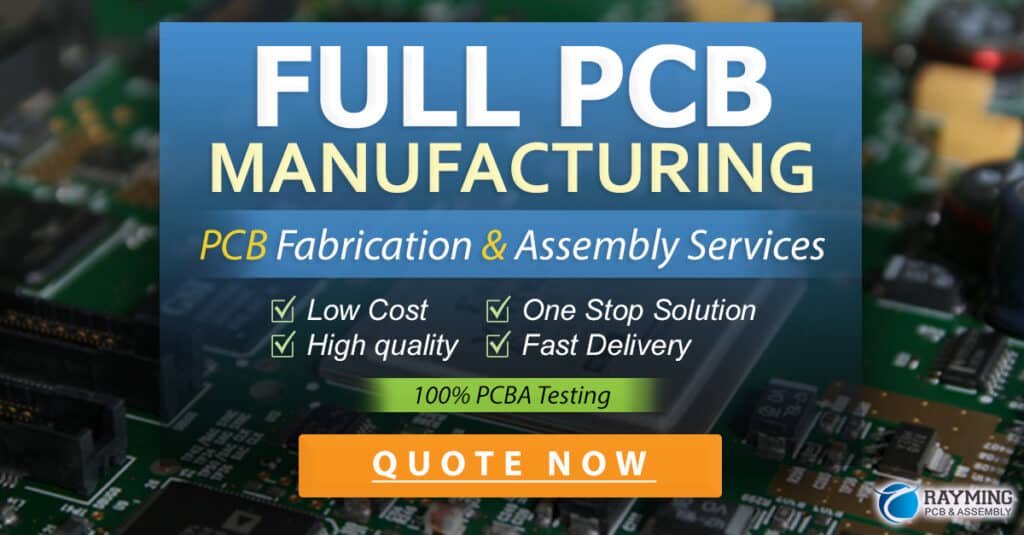
Testing and Qualification of Gold-Plated Edge Connectors
To ensure the reliability and performance of gold-plated edge connectors, several testing and qualification methods are employed:
1. Visual Inspection
Visual inspection is performed to assess the overall quality of the gold plating and edge beveling. This includes checking for uniformity, surface defects, and proper alignment of the gold fingers.
2. Thickness Measurement
The thickness of the gold plating is measured using non-destructive methods, such as X-ray fluorescence (XRF) or beta backscatter, to ensure compliance with the specified plating thickness requirements.
3. Contact Resistance Measurement
Contact resistance is measured between the gold-plated contacts and a mating connector to ensure low resistance and optimal signal transmission. High contact resistance can indicate issues with the gold plating quality or surface finish.
4. Insertion and Removal Testing
Insertion and removal testing is performed to evaluate the durability and reliability of the gold-plated edge connector over multiple mating cycles. This test simulates the expected use conditions and helps identify any potential issues with the gold fingers or edge beveling.
5. Environmental Testing
Gold-plated edge connectors may be subjected to various environmental tests, such as temperature cycling, humidity exposure, and corrosion testing, to assess their performance and reliability under different operating conditions.
Advantages of Gold Finger Plating for Edge Connectors
Gold finger plating offers several advantages for edge connectors in electronic devices:
- Reliable electrical connections: Gold-plated contacts provide reliable, low-resistance electrical connections, ensuring optimal signal transmission and device performance.
- Durability: Gold plating offers excellent wear resistance, allowing edge connectors to withstand numerous insertion and removal cycles without significant degradation.
- Corrosion resistance: Gold is highly resistant to corrosion, which helps maintain the integrity of the electrical connections in various environmental conditions.
- Compatibility: Gold-plated edge connectors are compatible with a wide range of mating sockets and slots, making them suitable for use in various electronic devices.
- Aesthetics: Gold finger plating provides an attractive, professional appearance to the edge connector, enhancing the overall aesthetics of the electronic device.
Conclusion
Gold finger plating is a critical process in the manufacturing of edge connectors for electronic devices. The combination of gold plating and edge beveling ensures reliable, durable, and high-performance electrical connections between the PCB and the mating socket or slot. By understanding the gold finger plating process, factors affecting plating quality, and testing methods, manufacturers can produce high-quality edge connectors that meet the demanding requirements of modern electronic devices.
FAQ
1. What is the typical thickness of gold plating on edge connectors?
The typical thickness of gold plating on edge connectors ranges from 0.05 to 0.30 micrometers (2 to 12 microinches), depending on the specific application and performance requirements.
2. Why is nickel plating sometimes used before gold plating?
Nickel plating is sometimes used as a barrier layer between the copper contacts and the gold plating to prevent the formation of intermetallic compounds that can weaken the bond between the two metals. Additionally, nickel plating can improve the wear resistance and durability of the gold-plated contacts.
3. What is the purpose of edge beveling in gold finger plating?
Edge beveling creates a smooth, angled transition on the edges of the PCB where the gold fingers are located. This facilitates smooth insertion and removal of the edge connector, reduces stress on the gold fingers, and improves the overall aesthetic appearance of the PCB.
4. How does gold purity affect the performance of gold-plated edge connectors?
Higher purity gold (99.9% or greater) provides better conductivity and corrosion resistance compared to lower purity gold. However, higher purity gold is also more expensive, so a balance must be struck between cost and performance requirements.
5. What environmental tests are performed on gold-plated edge connectors?
Gold-plated edge connectors may be subjected to various environmental tests, such as temperature cycling, humidity exposure, and corrosion testing, to assess their performance and reliability under different operating conditions.
No responses yet