Table of Contents
- Introduction to Eagle PCB
- Key Features of Eagle PCB
- Getting Started with Eagle PCB
- Schematic Capture in Eagle PCB
- PCB Layout in Eagle PCB
- Eagle PCB Routing Techniques
- Simulating and Verifying Designs in Eagle PCB
- Preparing Files for PCB Manufacturing
- Eagle PCB Tips and Best Practices
- Eagle PCB Full Version Free Download Crack
- Frequently Asked Questions (FAQ)
- Conclusion
Introduction to Eagle PCB
Eagle PCB, which stands for “Easily Applicable Graphical Layout Editor,” is a versatile software package for designing printed circuit boards. Developed by CadSoft Computer GmbH (now owned by Autodesk), Eagle PCB has become a go-to choice for electronics enthusiasts, students, and professionals due to its user-friendly interface, extensive component libraries, and powerful design tools.
Eagle PCB supports the entire PCB design workflow, from creating schematics to laying out the physical board and generating manufacturing files. The software is available for Windows, macOS, and Linux operating systems, making it accessible to a wide range of users.
Key Features of Eagle PCB
Eagle PCB offers a comprehensive set of features that enable users to design high-quality PCBs efficiently. Some of the key features include:
-
Schematic Capture: Eagle PCB provides a user-friendly schematic editor for creating and editing circuit diagrams. The editor supports hierarchical designs, allowing users to create modular and reusable circuit blocks.
-
PCB Layout: The PCB layout editor in Eagle PCB offers a range of tools for placing components, routing traces, and defining board shapes. The editor supports multi-layer designs and includes features like auto-routing, design rule checking (DRC), and real-time clearance checking.
-
Extensive Component Libraries: Eagle PCB comes with a vast collection of pre-built component libraries, including symbols, footprints, and 3D models for common electronic components. Users can also create custom libraries or import libraries from third-party sources.
-
Design Rule Checking (DRC): Eagle PCB includes a built-in DRC tool that automatically checks the PCB design for potential issues, such as short circuits, overlapping traces, or violations of manufacturing constraints. DRC helps ensure the design is error-free and ready for production.
-
Simulation and Verification: The software integrates with popular simulation tools like SPICE, allowing users to simulate and verify the performance of their circuits before committing to a physical prototype.
-
Manufacturing File Generation: Eagle PCB can generate industry-standard manufacturing files, such as Gerber files, drill files, and pick-and-place files, making it easy to send designs to PCB fabrication and assembly services.
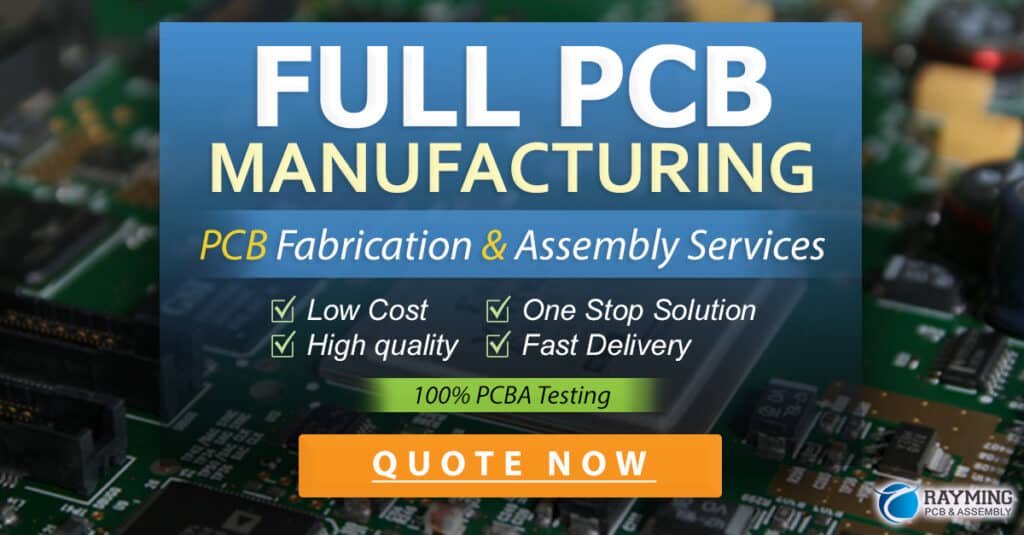
Getting Started with Eagle PCB
To start using Eagle PCB, follow these steps:
-
Installation: Download and install Eagle PCB on your computer. You can obtain a free version or use a download crack for the full version (more on this later).
-
Create a New Project: Launch Eagle PCB and create a new project by selecting “File” > “New” > “Project.” Choose a name and location for your project.
-
Set Up Design Rules: Before starting your design, set up the appropriate design rules for your PCB. Go to “Tools” > “DRC…” and configure the design rules based on your PCB manufacturer’s specifications.
-
Create a Schematic: Start by creating a schematic diagram of your circuit. Use the schematic editor to place components, draw wires, and define net names.
-
Create a Board: Once your schematic is complete, switch to the board editor to lay out the physical PCB. Place components, route traces, and define the board outline.
-
Verify and Manufacture: Run DRC to check for design errors, generate manufacturing files, and send your design to a PCB fabrication service.
Schematic Capture in Eagle PCB
Creating a schematic in Eagle PCB involves placing components and connecting them with wires to define the electrical connections in your circuit. Here’s a step-by-step guide to schematic capture in Eagle PCB:
-
Add Components: Use the “Add” tool to place components from libraries onto your schematic. You can search for components by name or browse through the available libraries.
-
Draw Wires: Use the “Wire” tool to connect the pins of your components. Click on a pin, then click on the destination pin to create a connection.
-
Name Nets: Assign meaningful names to your nets using the “Name” tool. This helps in identifying signals when you move to the board layout stage.
-
Create Buses: For circuits with many similar signals, you can use buses to simplify your schematic. Use the “Bus” tool to create a bus, then use the “Net” tool to connect signals to the bus.
-
Add Power and Ground Symbols: Use the “Add” tool to place power and ground symbols in your schematic. Connect these symbols to the appropriate nets.
-
Check and Annotate: Use the “ERC” (Electrical Rule Check) tool to check for errors in your schematic. Then, use the “Annotate” tool to assign unique designators to your components.
PCB Layout in Eagle PCB
Once your schematic is complete, you can move on to the PCB layout stage. Here’s how to lay out your PCB in Eagle PCB:
-
Switch to Board View: Click the “Board” icon or select “File” > “Switch to Board” to enter the board layout editor.
-
Define Board Outline: Use the “Wire” tool to draw the outline of your PCB. You can also use the “Rectangle” tool for simple rectangular boards.
-
Place Components: Use the “Move” tool to place your components on the board. Pay attention to the component orientation and ensure proper spacing between components.
-
Route Traces: Use the “Route” tool to manually route traces between the pads of your components. You can also use the auto-router for more complex designs.
-
Define Copper Pours: Use the “Polygon” tool to create copper pours for power and ground planes. This helps reduce electromagnetic interference and improves signal integrity.
-
Add Silkscreen and Assembly Layers: Use the “Text” and “Circle” tools to add silkscreen labels and assembly information to your board.
-
Check Design Rules: Run DRC to ensure your board meets the design rules specified earlier. Make any necessary adjustments to your layout.
Eagle PCB Routing Techniques
Routing is a critical aspect of PCB design, as it determines the signal integrity and manufacturability of your board. Here are some routing techniques to keep in mind when using Eagle PCB:
-
Manual Routing: For simple designs or critical signals, manual routing gives you complete control over the trace paths. Use the “Route” tool and follow the design rules for trace width, spacing, and via size.
-
Auto-Routing: Eagle PCB’s auto-router can save time on complex designs. Set up the auto-router parameters, such as via costs and routing directions, then run the auto-router. Review the results and make manual adjustments as needed.
-
Differential Pair Routing: When routing high-speed differential pairs, use the “Route” tool’s differential pair mode to ensure proper spacing and length matching between the traces.
-
Ground Planes: Use copper pours or dedicated layers for ground planes to provide a low-impedance return path for signals. This helps reduce electromagnetic interference and improves signal integrity.
-
Trace Width and Spacing: Follow the recommended trace width and spacing guidelines for your PCB’s copper thickness and signal requirements. Wider traces have lower resistance and can carry more current, while proper spacing helps prevent crosstalk and short circuits.
Simulating and Verifying Designs in Eagle PCB
Before sending your design for manufacturing, it’s essential to simulate and verify its performance. Eagle PCB integrates with popular simulation tools like SPICE to help you catch potential issues early in the design process.
-
Create a Simulation Schematic: Create a separate schematic for simulation purposes, including the necessary simulation models for your components.
-
Set Up Simulation Parameters: Define the simulation parameters, such as input signals, output loads, and analysis types (e.g., transient, AC, DC).
-
Run the Simulation: Execute the simulation and analyze the results. Look for any unexpected behavior or potential issues.
-
Verify Signal Integrity: Check for signal integrity issues, such as overshoot, undershoot, or ringing. Adjust your design as needed to mitigate these issues.
-
Verify Power Integrity: Ensure your power distribution network can deliver the required current to all components without excessive voltage drop or noise.
Preparing Files for PCB Manufacturing
Once your design is finalized and verified, you need to generate the necessary files for PCB manufacturing. Eagle PCB makes this process straightforward:
-
Generate Gerber Files: Go to “File” > “CAM Processor” and select the appropriate Gerber file settings for your PCB manufacturer. Generate the Gerber files for each layer of your board.
-
Generate Drill Files: In the CAM Processor, select the drill file settings and generate the drill files, which specify the locations and sizes of the holes in your board.
-
Generate Pick-and-Place Files: If your PCB will be assembled by a pick-and-place machine, generate the pick-and-place files, which provide the component locations and orientations.
-
Generate Bill of Materials (BOM): Create a BOM that lists all the components used in your design, including their quantities, part numbers, and descriptions.
-
Package and Send Files: Package the Gerber, drill, pick-and-place, and BOM files together and send them to your PCB manufacturer for fabrication and assembly.
Eagle PCB Tips and Best Practices
To make the most of Eagle PCB and create high-quality PCB designs, consider the following tips and best practices:
-
Keep Your Schematic Clean: Use consistent naming conventions, organize your components logically, and minimize wire crossings to keep your schematic easy to read and understand.
-
Use a Grid: Set up a grid in both the schematic and board editors to help align components and ensure consistent spacing.
-
Follow Design Rules: Always follow the design rules provided by your PCB manufacturer to ensure your board can be fabricated and assembled reliably.
-
Keep Components on the Grid: When placing components on your board, snap them to the grid to maintain a neat and organized layout.
-
Route Critical Signals First: Start by routing the most critical signals, such as high-speed data lines or sensitive analog signals, to ensure they have the optimal path.
-
Minimize Via Count: Vias add complexity and cost to your PCB. Minimize the number of vias in your design by careful component placement and efficient routing.
-
Use Copper Pours: Implement copper pours for power and ground planes to improve signal integrity and reduce electromagnetic interference.
-
Document Your Design: Include clear silkscreen labels, assembly notes, and a detailed README file to help others understand and work with your design.
Eagle PCB Full Version Free Download Crack
While Eagle PCB offers a free version for non-commercial use, some advanced features and larger board sizes are only available in the paid versions. However, it is possible to obtain a full version of Eagle PCB for free using a download crack.
Please note that using a cracked version of Eagle PCB is illegal and against the software’s terms of service. We do not condone or support software piracy. It is always best to support the developers by purchasing a legitimate license.
If you still choose to use a download crack, be aware of the risks involved, such as potential malware, lack of support, and legal consequences. Proceed at your own risk.
Frequently Asked Questions (FAQ)
-
Is Eagle PCB free?
Eagle PCB offers a free version for non-commercial use, which includes limited features and board sizes. For commercial use or access to advanced features, a paid license is required. -
Can I use Eagle PCB on multiple operating systems?
Yes, Eagle PCB is available for Windows, macOS, and Linux operating systems, allowing you to use the software on your preferred platform. -
Does Eagle PCB support multi-layer PCBs?
Yes, Eagle PCB supports the design of multi-layer PCBs. The software can handle various layer stackups and allows you to route signals on different layers. -
Can I import and export designs from other PCB software?
Eagle PCB supports importing and exporting designs in various formats, such as Gerber, DXF, and IDF. This enables collaboration with users of other PCB design software. -
How can I learn to use Eagle PCB effectively?
Autodesk, the company behind Eagle PCB, offers a comprehensive set of tutorials, guides, and documentation to help users learn the software. There are also numerous online resources, such as forums, video tutorials, and blogs, where you can find tips and tricks for using Eagle PCB effectively.
Conclusion
Eagle PCB is a powerful and versatile software package for designing printed circuit boards. With its user-friendly interface, extensive component libraries, and advanced routing and simulation capabilities, Eagle PCB streamlines the PCB design process from schematic capture through board layout and manufacturing preparation.
By following the steps and best practices outlined in this guide, you can create high-quality PCB designs using Eagle PCB. Remember to always adhere to design rules, keep your schematics and layouts organized, and verify your designs through simulation and thorough checking.
While it is possible to obtain a full version of Eagle PCB for free using a download crack, we strongly advise against it. Using cracked software is illegal and can expose you to various risks. Instead, consider supporting the developers by purchasing a legitimate license or using the free version for non-commercial purposes.
With dedication and practice, Eagle PCB can help you bring your electronic projects to life, from idea to manufactured PCB. Happy designing!
Feature | Free Version | Standard Version | Premium Version |
---|---|---|---|
Non-commercial use | Yes | Yes | Yes |
Commercial use | No | Yes | Yes |
Schematic sheets | 1 | 99 | 999 |
Board layers | 2 | 4 | 16 |
Board area | 80 cm² | 160 cm² | Unlimited |
Schematic editor | Yes | Yes | Yes |
PCB layout editor | Yes | Yes | Yes |
Autorouter | No | Yes | Yes |
3D visualization | No | No | Yes |
Price | Free | $99 | $499 |
No responses yet