Understanding Drill File Basics
Before diving into generating drill files, it’s important to understand some key concepts:
Types of Drill Holes
PCBs require several different types of drilled holes:
Hole Type | Description |
---|---|
Through hole | Go completely through the PCB, used for mounting through-hole components |
Blind via | Start on an outer layer and terminate in an inner layer |
Buried via | Both start and end in inner layers, not visible from outside the PCB |
Drill File Formats
There are two main formats for drill files:
- Excellon format (.txt, .drl, .exc) – most commonly used
- Sieb & Meyer format (.txt, .ncd) – less common
Both formats use ASCII text to represent drill data. The specific commands and syntax vary between the two.
Units and Coordinates
Drill files specify hole locations using absolute (x,y) coordinates and hole diameters. The units are typically either:
- Inches (more common)
- Millimeters
Coordinates are specified as integers, with the number of digits determining the precision. For example, a coordinate specified as 01000 in inches translates to 0.1000″.
Setting Up Your EDA Software
To generate drill files, you’ll need to use electronic design automation (EDA) software. Popular options include:
- Altium Designer
- KiCad
- Eagle
- OrCAD
- Cadence Allegro
The specific steps for generating drill files vary between software. However, the general process is:
- Complete your PCB design, including placing and routing all components
- Define pad/via sizes and drill pairs
- Specify drill symbols and hole sizes
- Generate drill files
- Verify drill files
Consult your EDA software documentation for detailed instructions. Many offer step-by-step guides or video tutorials walking through the process.
Defining Pad/Via Sizes and Drill Pairs
For plated through holes, you need to define the pad (annular ring) and drill size. The pad must be larger than the drill. Typical pad to drill size ratios range from 1.5:1 to 2:1.
Common sizes for standard vias are:
Finished Hole Size | Drill Size | Pad Size |
---|---|---|
0.010″ | 0.014″ | 0.024″ |
0.015″ | 0.019″ | 0.029″ |
0.020″ | 0.024″ | 0.034″ |
Your manufacturer can advise on recommended pad/drill sizes based on your PCB requirements. Smaller sizes are more challenging to manufacture.
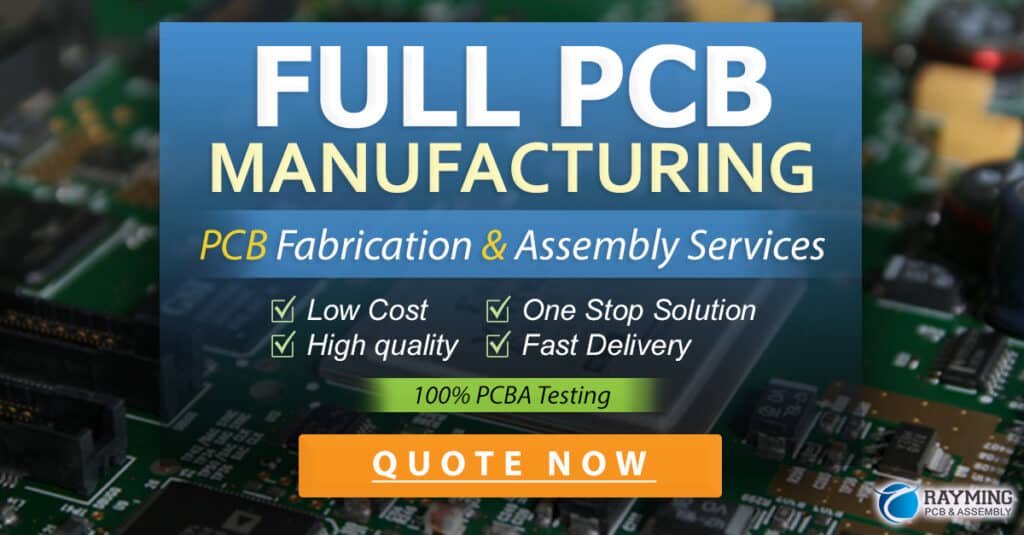
Specifying Drill Symbols and Holes Sizes
In your EDA software, you’ll need to specify the drill symbol and finished hole size for each pad/via. Common drill symbols include:
- “+” for plated through holes
- “X” for non-plated through holes
- “O” for holes that aren’t drilled (just punched)
The specific syntax for specifying drill symbols varies by software. Refer to the documentation for details.
Hole sizes are typically specified in 1/10,000th of an inch or 1/100th of a mm. For example:
- 0.0240″ = 2400
- 0.60mm = 6000
Again, confirm the units and number of digits your manufacturer expects. They may have specific requirements.
Generating Drill Files
With pad/via sizes and drill symbols defined, you’re ready to generate your drill files. The specifics vary by software, but look for options like:
- “Generate manufacturing files”
- “Create NC drill files”
- “Export drill files”
You may be prompted to select options like:
- Format (Excellon or Sieb & Meyer)
- Units
- Number of digits for coordinates
- Which layers to include holes from
- Drill symbol usage
Select the options that match your manufacturer’s requirements. If in doubt, ask them for guidance.
Verifying Drill Files
Before sending drill files to your manufacturer, it’s critical to verify them for accuracy. Common checks include:
- Comparing hole locations and sizes to your design
- Checking for missing holes
- Confirming the correct number of digits are used
- Validating the format matches what your manufacturer expects
Many EDA software include built-in drill file verification. You can also manually review the generated files in a text editor.
If you find any issues, update your design or generation settings and recreate the drill files. Don’t send files to manufacturing until you’ve confirmed they’re error-free.
Tips for Avoiding Drill File Errors
Generating accurate drill files is essential for manufacturing success. To avoid problems:
- Make sure you’re using your manufacturer’s recommended settings for file format, units, etc. Don’t assume defaults will work.
- Double-check all pad/via sizes and drill pairs. Mismatches here are a common source of errors.
- Pay close attention to drill symbols. Make sure plated, non-plated holes are correctly defined.
- Always verify your generated drill files before releasing them. Check and double-check!
- If you’re unsure about anything, ask your manufacturer. They can provide guidance on their requirements and help troubleshoot issues.
Frequently Asked Questions
What’s the most common drill file format?
Excellon format (.txt, .drl, .exc) is the most widely used. It’s considered the standard for the PCB industry. Sieb & Meyer format is also used but is less common.
What units should I use for drill files?
This depends on your manufacturer’s requirements. Inches are more commonly used, but some manufacturers may prefer millimeters. Always confirm with your manufacturer before generating files.
What precision should I use for drill coordinates and sizes?
This also depends on your manufacturer. Coordinates and sizes are typically specified to 4-5 digits of precision. More precision is possible but not always necessary. Consult your manufacturer for their recommendations.
What’s the best pad to drill size ratio?
Typical pad to drill size ratios range from 1.5:1 to 2:1. So for a 0.020″ finished hole size, the pad size might be 0.030-0.040″. Your manufacturer can advise on the optimal sizes for your design based on the PCB materials, layer count, etc.
How do I verify my drill files are accurate?
Most EDA software includes built-in tools for verifying drill files. These compare the generated files to your PCB design and flag any discrepancies. You can also manually review the drill files in a text editor. Compare the coordinates and sizes to your design to confirm they match. If you find errors, regenerate the files and reverify before sending to your manufacturer.
Conclusion
Generating accurate drill files is a crucial step in PCB manufacturing. By understanding the fundamentals of drill file formats, units, and coordinates, and carefully defining pad/via sizes and drill symbols in your EDA software, you can create drill files that will result in a successful PCB build. Always verify your generated files and don’t hesitate to consult your manufacturer for guidance. With attention to detail and following best practices, you can ensure your drill files will lead to a functional, high-quality PCB.
No responses yet