Introduction to DRC in CAD Design
Design Rule Checking (DRC) is a critical step in the computer-aided design (CAD) process for printed circuit boards (PCBs) and integrated circuits (ICs). DRC involves using automated tools within a CAD software package to verify that a design meets all the required manufacturing and electrical rules before sending it for fabrication.
Properly configured DRC settings help catch potential issues early in the design phase when they are much easier and less costly to correct. This article will provide an overview of key DRC concepts and best practices for configuring DRC settings in popular CAD tools to ensure high-quality, manufacturable designs.
Importance of DRC in the Design Flow
Implementing DRC checks is essential for several reasons:
-
Manufacturing Reliability – DRC ensures a design can be reliably manufactured by checking against the fabrication capabilities and tolerances of the specific manufacturer or process.
-
Electrical Integrity – Checking for violations like insufficient clearances, trace widths, or via sizes helps avoid unintended short circuits, signal integrity issues, and other electrical failures.
-
Cost and Time Savings – Fixing design rule violations early avoids wasted time and expensive re-spins later due to designs that can’t be manufactured as intended.
-
Improved Yield – Designs that fully adhere to all DRC rules have a higher probability of successful fabrication with fewer defects, improving production yield rates.
Types of Design Rules to Check
There are numerous potential design rule checks that a CAD package may offer, depending on the PCB or IC technology and the manufacturing process. However, most DRC tools will include checks for some common categories of design rules:
Clearance and Spacing Rules
These rules define the minimum allowed spacing between different objects and layers in a design, such as:
- Clearance between traces, pads, vias, and other copper features
- Spacing between copper objects and the board edge
- Clearance of copper to drill holes and cut-outs
- Spacing of silkscreen, Solder Mask, and other markings from pads and vias
Trace Width and Thickness Rules
Trace width rules specify the minimum, maximum, and allowed increments for trace sizes. These depend on the current carrying and impedance requirements of the traces. Trace thickness rules define the copper weight or height.
Drill Hole and Via Rules
These rules cover the minimum, maximum, and incremental sizes for drills and vias allowed by the fabrication process. They also define required clearances and spacing from hole edges to traces and other copper.
Solder Mask and Paste Rules
Solder mask rules define expansion and contraction allowances as well as webbing and dam sizes for solder mask. Paste mask rules control the size and shape of openings for solder paste application.
Plane and Copper Pour Rules
These include checks for isolated or starved thermal spokes, acid traps, and sliver distances in copper pour and plane areas.
Silkscreen and Marking Rules
Silkscreen rules check text sizes, line widths, and spacing from other objects. Marking rules may define required fiducials or other production marks.
Configuring DRC Settings in CAD Tools
The exact process to configure DRC settings varies between different CAD packages, but the general concepts are similar. We’ll look at examples of configuring DRC in two popular PCB Design packages – Altium Designer and KiCAD.
DRC Setup in Altium Designer
In Altium Designer, DRC rules are configured in the PCB Rules and Constraints Editor window. To access this:
-
Open the PCB File and navigate to Design -> Rules
-
In the left pane, expand the Design Rules tree and select the category to configure
-
Adjust the rule priorities, scopes, and constraints
-
Click Apply and OK to save the rule changes
Here’s an example of configuring a clearance rule between objects in Altium:
Setting | Value |
---|---|
Name | Clearance_1 |
Scope | All |
First Object | InNet(‘GND’) |
Second Object | InNet(‘VCC’) |
Minimum Clearance | 10mil |
Preferred Clearance | 20mil |
Layer | All |
This sets a rule called “Clearance_1” that applies between GND and VCC nets on all layers, with a minimum spacing of 10 mils and a preferred spacing of 20 mils.
DRC Setup in KiCAD
In KiCAD’s PCBNew, DRC rules are managed in the Design Rules window. To configure this:
-
Open the PCB file and navigate to Inspect -> Design Rules Checker
-
Select the Global Design Rules tab
-
Adjust settings under the Constraints and MANUFACTURING sections
-
Click OK to save the changes
For example, to set a minimum trace width in KiCAD:
Setting | Value |
---|---|
Minimum track width | 6 mil |
This constrains all traces in the design to be at least 6 mils wide.
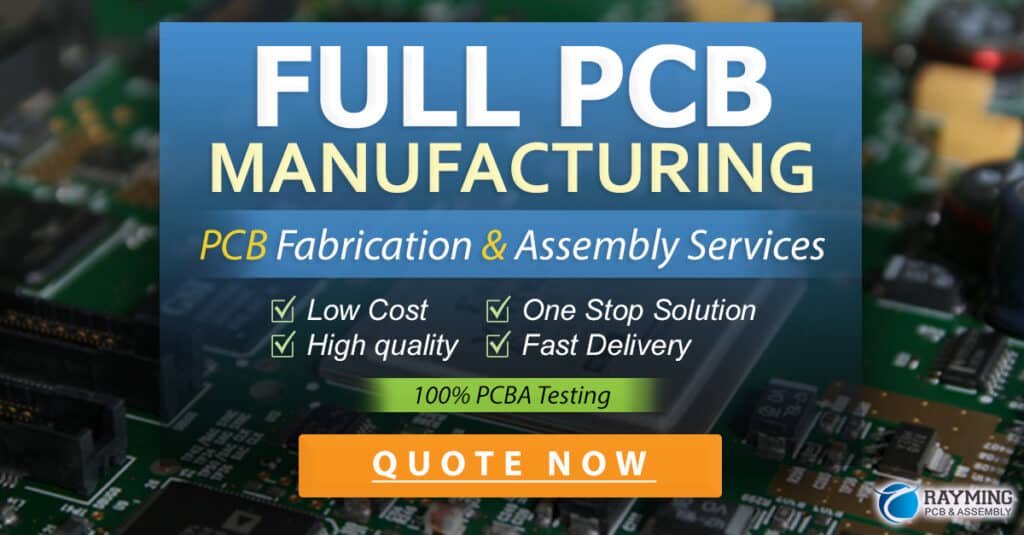
Running DRC and Interpreting Results
With the DRC rules defined, the next step is to run the checks and review the results. The specifics again depend on the CAD tool.
Running DRC in Altium
In Altium Designer, to run a DRC:
-
Navigate to Tools -> Design Rule Check
-
Select the rules to check and the violation report format
-
Click Run Design Rule Check
-
Review the results in the Messages panel and PCB workspace
Altium displays DRC violations directly on the relevant objects in the design workspace. The Messages panel provides a summary and detailed list of violation types and locations.
Running DRC in KiCAD
To perform a DRC in KiCAD’s PCBNew:
-
Go to Inspect -> Design Rules Checker
-
Click the Run DRC button
-
Review the results in the Problems/Markers tab and PCB workspace
Like Altium, KiCAD shows DRC violations with on-screen markers on the affected objects. The Problems/Markers list provides details on each violation type and location.
Resolving DRC Violations
After running DRC, the next step is to resolve any reported violations. Some general tips:
- Review and prioritize the violation list, tackling the most critical issues first
- Use the CAD tool’s zoom and highlight features to locate violations on the design
- Determine if the violation is due to an incorrect rule setup or an actual design issue
- Make needed adjustments to the design objects or constraints to clear the violation
- Re-run DRC after changes to ensure the violation is resolved and no new issues were introduced
Some violations may require manual review and verification, such as for complex design requirements not fully captured in the DRC rules.
Best Practices for DRC
To get the most benefit from DRC, some key best practices to follow include:
-
Consult with the manufacturer early to obtain their DRC rules and constraints to use as a starting point
-
Set up DRC rules at the start of the layout process so violations can be caught in real-time during design
-
Use hierarchical rule scopes to efficiently apply different constraints to specific areas like controlled impedance regions
-
Run DRC incrementally during layout to catch and fix issues as they arise
-
Perform a final comprehensive DRC before generating manufacturing files
Following these practices helps ensure a high quality, manufacturable design that can avoid expensive and time-consuming redesigns.
FAQs About DRC Settings and Usage
Q: How do I determine what DRC rules to use for my design?
A: Consult with your PCB Manufacturer and get their DRC rules as a starting point. Adjust settings as needed for your specific electrical and manufacturing requirements.
Q: What happens if DRC violations are left uncorrected?
A: Unresolved DRC errors can result in boards that are non-manufacturable or that have functional and reliability issues due to problems like short circuits, broken traces, or out-of-spec features.
Q: How often should I run DRC during layout?
A: Run DRC incrementally as you work to catch violations in real-time. Always perform a final, full DRC before generating manufacturing files.
Q: What if I need to violate a DRC rule for a specific design requirement?
A: Most CAD tools allow for manual DRC waivers with an approval and note process to document violations made for valid engineering reasons. Use sparingly and verify with the manufacturer.
Q: Can I use the same DRC rules across different designs and manufacturers?
A: While some core DRC constraints may be similar, always check with each manufacturer for their specific rules. Different processes and tolerances may require targeted rule adjustments.
Conclusion
DRC is a powerful tool for ensuring high quality, manufacturable PCB and IC designs. By properly configuring DRC rules and consistently running checks throughout the layout process, designers can avoid costly re-spins and improve end product reliability.
The specific DRC settings and processes may vary between CAD tools, but the fundamental concepts of defining manufacturing and electrical constraints and verifying the design against them remains constant. Taking the time upfront to set up comprehensive DRC rules and following best practices for violation resolution pays dividends in the final design result.
No responses yet