Table of Contents
- Introduction to Printed Circuit Boards
- PCB Design Software
- Schematic Capture
- PCB Layout
- PCB Fabrication
- PCB Assembly
- Testing and Troubleshooting
- Advanced PCB Techniques
- Frequently Asked Questions (FAQ)
- Conclusion
Introduction to Printed Circuit Boards
Printed Circuit Boards (PCBs) are the backbone of modern electronics. They provide a reliable and efficient means of connecting electronic components in a compact and organized manner. PCBs consist of a non-conductive substrate, typically made of fiberglass or other composite materials, with conductive copper traces etched onto the surface to form the desired circuit pattern.
PCBs offer several advantages over traditional point-to-point wiring:
– Compact and space-efficient design
– Improved reliability and durability
– Reduced electromagnetic interference (EMI)
– Easier mass production and assembly
– Standardized layouts for common circuit designs
Types of PCBs
PCBs can be categorized based on the number of conductive layers and their construction:
PCB Type | Layers | Description |
---|---|---|
Single-sided | 1 | Conductive traces on one side of the substrate |
Double-sided | 2 | Conductive traces on both sides of the substrate |
Multi-layer | 3+ | Multiple conductive layers separated by insulating layers |
Rigid | – | Standard PCB with a solid, non-flexible substrate |
Flexible | – | PCB with a flexible substrate, often used in compact devices |
Rigid-Flex | – | Combination of rigid and flexible sections in a single PCB |
PCB Design Software
To create your own PCBs, you’ll need to use specialized PCB design software. There are several options available, ranging from free and open-source to paid commercial solutions:
Free and Open-Source
- KiCad
- EAGLE (free version available)
- gEDA
- FreePCB
Commercial
- Altium Designer
- OrCAD
- PADS
- Mentor Graphics PADS
When choosing a PCB design software, consider factors such as ease of use, available features, community support, and compatibility with your preferred fabrication and assembly services.
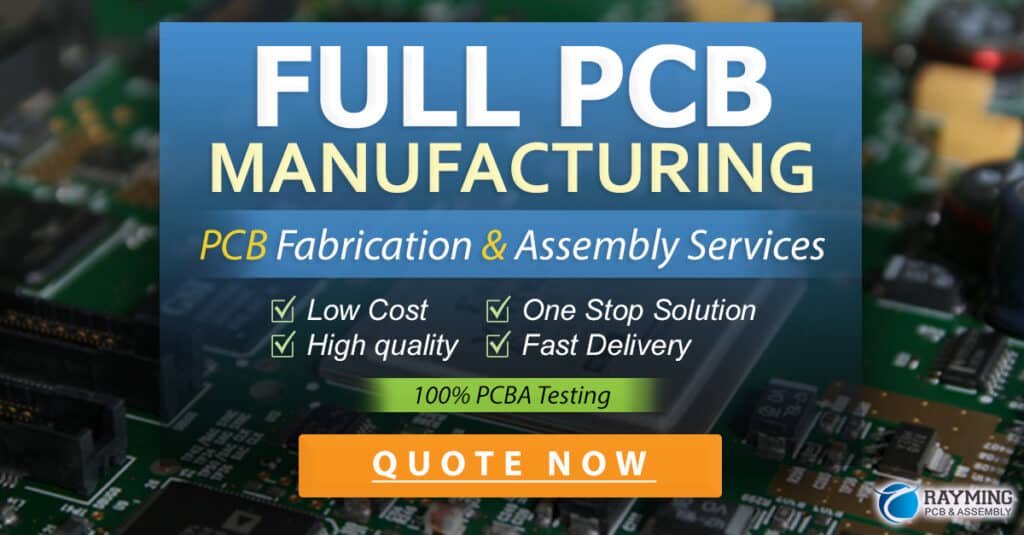
Schematic Capture
The first step in creating a PCB is to design the schematic diagram of your circuit. A schematic is a graphical representation of the electrical connections between components in your circuit. It uses standardized symbols to represent components and shows how they are interconnected.
Schematic Capture Process
- Create a new schematic document in your chosen PCB design software.
- Place component symbols from the available libraries or create custom symbols if necessary.
- Connect the components using wires or nets, following your circuit diagram.
- Assign unique reference designators (e.g., R1, C2, U3) to each component for easy identification.
- Add power and ground symbols to represent the power supply connections.
- Annotate the schematic with relevant information, such as component values and part numbers.
- Perform a design rule check (DRC) to ensure the schematic is free of errors.
PCB Layout
Once your schematic is complete, you can proceed to the PCB layout stage. In this step, you’ll arrange the physical components on the PCB and route the copper traces to form the desired electrical connections.
PCB Layout Process
- Create a new PCB layout document and import the netlist generated from your schematic.
- Define the PCB dimensions, layer stackup, and design rules (e.g., minimum trace width, clearance, via size).
- Place the components on the PCB, considering factors such as component size, orientation, and thermal requirements.
- Route the traces between the components, following the connections defined in the schematic.
- Add copper fills or planes for power distribution and EMI reduction.
- Place mounting holes, fiducials, and other mechanical features as needed.
- Perform a design rule check (DRC) to ensure the layout meets the specified design rules.
- Generate the Gerber files and drill files required for PCB fabrication.
PCB Layout Tips
- Keep traces as short and direct as possible to minimize signal integrity issues.
- Avoid sharp angles in traces to reduce reflections and signal distortion.
- Use appropriate trace widths based on the current carrying requirements of the circuit.
- Provide adequate clearance between traces and components to prevent short circuits.
- Consider the placement of decoupling capacitors close to ICs for optimal power supply filtering.
- Use ground planes to provide a low-impedance return path and reduce EMI.
- Be mindful of component placement and orientation for ease of assembly and maintenance.
PCB Fabrication
After completing the PCB layout, you’ll need to send the Gerber files and drill files to a PCB fabrication service. There are numerous online and local PCB manufacturers that offer various options for PCB fabrication, such as:
- Material selection (e.g., FR-4, Rogers, aluminum)
- Copper weight (e.g., 1 oz, 2 oz)
- Solder mask color (e.g., green, red, black)
- Silkscreen color (e.g., white, black)
- Surface finish (e.g., HASL, ENIG, OSP)
- Minimum feature size (e.g., trace width, clearance)
When choosing a PCB fabrication service, consider factors such as cost, turnaround time, quality, and minimum order quantity (MOQ).
PCB Assembly
Once your PCBs are fabricated, you’ll need to assemble the components onto the board. There are two main methods for PCB assembly:
Through-Hole Assembly
Through-hole components have long leads that are inserted through holes drilled in the PCB and soldered on the opposite side. This method is suitable for larger components and is easier for manual assembly.
Surface-Mount Assembly
Surface-mount components have small leads or pads that are soldered directly onto the surface of the PCB. This method allows for smaller component sizes and higher component density but requires more precise soldering techniques.
PCB Assembly Process
- Gather the necessary components, tools, and supplies (e.g., soldering iron, solder, flux, tweezers).
- Apply a small amount of solder paste or flux to the pads on the PCB.
- Place the components onto the PCB, aligning them with the corresponding pads.
- Solder the components to the PCB using the appropriate soldering technique (e.g., hand soldering, reflow soldering).
- Inspect the solder joints for quality and ensure there are no short circuits or bridged connections.
- Clean the PCB to remove any flux residue or debris.
Testing and Troubleshooting
After assembling your PCB, it’s essential to test and verify its functionality. This process involves:
- Visual inspection: Check for any visible defects, such as incorrect component placement, solder bridges, or damaged components.
- Continuity testing: Use a multimeter to ensure there are no short circuits or open connections between the components and traces.
- Power-on testing: Apply power to the PCB and verify that it functions as expected, such as proper voltage levels and signal integrity.
- Functional testing: Test the specific functionality of your circuit, such as input/output response, communication, or data processing.
If you encounter any issues during testing, you may need to troubleshoot the PCB:
– Recheck the schematic and PCB layout for design errors.
– Verify the component values and orientations.
– Inspect the solder joints for quality and rework if necessary.
– Use an oscilloscope or logic analyzer to analyze signal integrity and timing.
– Consult the component datasheets and application notes for specific troubleshooting guidelines.
Advanced PCB Techniques
As you gain more experience with PCB design and assembly, you may want to explore advanced techniques to improve the performance and functionality of your circuits:
High-Speed PCB Design
When designing PCBs for high-speed applications (e.g., gigahertz frequencies), consider factors such as:
– Impedance control: Match the trace impedance to the source and load impedances to minimize reflections.
– Length matching: Ensure that critical signal paths have equal lengths to maintain signal integrity.
– Differential signaling: Use differential pairs for high-speed signals to reduce noise and crosstalk.
Flexible PCBs
Flexible PCBs offer unique advantages in applications that require compact packaging or dynamic flexing:
– Material selection: Choose flexible substrates such as polyimide or polyester.
– Bend radius: Consider the minimum bend radius of the PCB to avoid damage or signal integrity issues.
– Strain relief: Incorporate strain relief features to protect the PCB and components from mechanical stress.
Wireless PCB Design
When designing PCBs for wireless applications (e.g., Bluetooth, Wi-Fi, NFC), consider factors such as:
– Antenna design: Select the appropriate antenna type and size based on the frequency and range requirements.
– Impedance matching: Ensure proper impedance matching between the antenna and the transceiver to maximize power transfer.
– Shielding: Use shielding techniques to minimize electromagnetic interference (EMI) and ensure regulatory compliance.
Frequently Asked Questions (FAQ)
- What is the difference between a schematic and a PCB layout?
-
A schematic is a graphical representation of the electrical connections between components, while a PCB layout shows the physical arrangement of components and traces on the PCB.
-
Can I design a PCB without using specialized software?
-
While it is possible to design simple PCBs using general-purpose graphics software, using dedicated PCB design software is highly recommended for accurate and efficient design.
-
How do I choose the appropriate trace width for my PCB?
-
Trace width depends on factors such as the current carrying requirements, the desired resistance, and the PCB fabrication capabilities. Consult the IPC-2221 standard or use online trace width calculators for guidance.
-
What is the purpose of a solder mask on a PCB?
-
A solder mask is a protective layer applied to the PCB that prevents accidental short circuits and helps to contain the solder to the desired areas during assembly.
-
How can I reduce electromagnetic interference (EMI) in my PCB design?
- To reduce EMI, use techniques such as proper grounding, shielding, filtering, and appropriate component placement. Additionally, follow best practices for high-speed PCB design, such as using ground planes and minimizing loop areas.
Conclusion
Designing and fabricating your own PCBs can be a rewarding and educational experience for electronics enthusiasts. By following this comprehensive guide, you should now have a solid understanding of the PCB design process, from schematic capture to PCB layout, fabrication, and assembly.
Remember to start with simple designs and gradually work your way up to more complex projects as you gain experience. Don’t be discouraged if your first attempts are not perfect – PCB design is an iterative process that requires practice and patience.
As you continue to develop your skills, explore advanced techniques and stay up-to-date with the latest industry trends and best practices. With dedication and perseverance, you’ll be able to create professional-quality PCBs for your electronic projects.
Happy PCB designing!
No responses yet