Introduction to Buck Converters
A buck converter, also known as a step-down converter, is a type of DC-to-DC power converter that efficiently reduces the voltage from a higher level to a lower level. It is widely used in various electronic applications, such as battery-powered devices, power supplies, and voltage regulation circuits. In this comprehensive tutorial, we will dive into the world of buck converters, understanding their principles, components, and how to build your own DIY buck converter.
What is a Buck Converter?
A buck converter is a switch-mode power supply (SMPS) that steps down the input voltage to a lower output voltage while maintaining high efficiency. It consists of several key components, including an inductor, a capacitor, a diode, and a switching element (usually a MOSFET or transistor). By controlling the switching element’s duty cycle, the buck converter regulates the output voltage to the desired level.
Buck Converter Applications
Buck converters find applications in a wide range of electronic devices and systems, such as:
- Battery-powered devices (smartphones, laptops, portable electronics)
- Voltage regulation in power supplies
- LED drivers
- Automotive electronics
- Renewable energy systems (solar panels, wind turbines)
How Does a Buck Converter Work?
To understand how a buck converter works, let’s break down its operation into two phases: the ON phase and the OFF phase.
ON Phase
During the ON phase, the switching element (MOSFET) is turned on, allowing current to flow through the inductor. The inductor stores energy in its magnetic field, and the capacitor charges up. The diode is reverse-biased and does not conduct during this phase.
OFF Phase
When the switching element turns off, the inductor’s magnetic field collapses, and the stored energy is released. The diode becomes forward-biased, providing a path for the inductor current to continue flowing. The capacitor discharges, supplying current to the load.
By continuously switching between the ON and OFF phases at a high frequency, the buck converter maintains a constant output voltage. The duty cycle, which is the ratio of the ON time to the total switching period, determines the output voltage level.
Buck Converter Components
To build a DIY buck converter, you’ll need the following components:
- Inductor
- Capacitor
- Diode
- MOSFET (or transistor)
- Resistors
- Control circuit (PWM generator, feedback network)
Let’s discuss each component in detail.
Inductor
The inductor is a crucial component in a buck converter. It stores energy during the ON phase and releases it during the OFF phase, smoothing out the current ripple. The inductor’s value is determined by factors such as the switching frequency, desired output voltage, and current ripple.
Capacitor
The capacitor serves as an energy storage element and helps reduce the output voltage ripple. It charges during the ON phase and discharges during the OFF phase, providing a stable output voltage to the load. The capacitor’s value is chosen based on the desired output voltage ripple and the switching frequency.
Diode
The diode acts as a rectifier in the buck converter circuit. It provides a path for the inductor current to flow during the OFF phase and prevents reverse current flow. Schottky diodes are commonly used in buck converters due to their low forward voltage drop and fast switching characteristics.
MOSFET (or Transistor)
The MOSFET (Metal-Oxide-Semiconductor Field-Effect Transistor) or transistor acts as the switching element in the buck converter. It is controlled by a PWM (Pulse-Width Modulation) signal, which determines the duty cycle and, consequently, the output voltage. MOSFETs are preferred over bipolar transistors due to their higher efficiency and faster switching speeds.
Resistors
Resistors are used in the feedback network of the buck converter to sense the output voltage and provide a reference voltage for the control circuit. They also help set the desired output voltage level.
Control Circuit
The control circuit is responsible for generating the PWM signal that controls the switching element. It consists of a PWM generator and a feedback network. The feedback network senses the output voltage and compares it with a reference voltage, adjusting the duty cycle to maintain a constant output voltage.
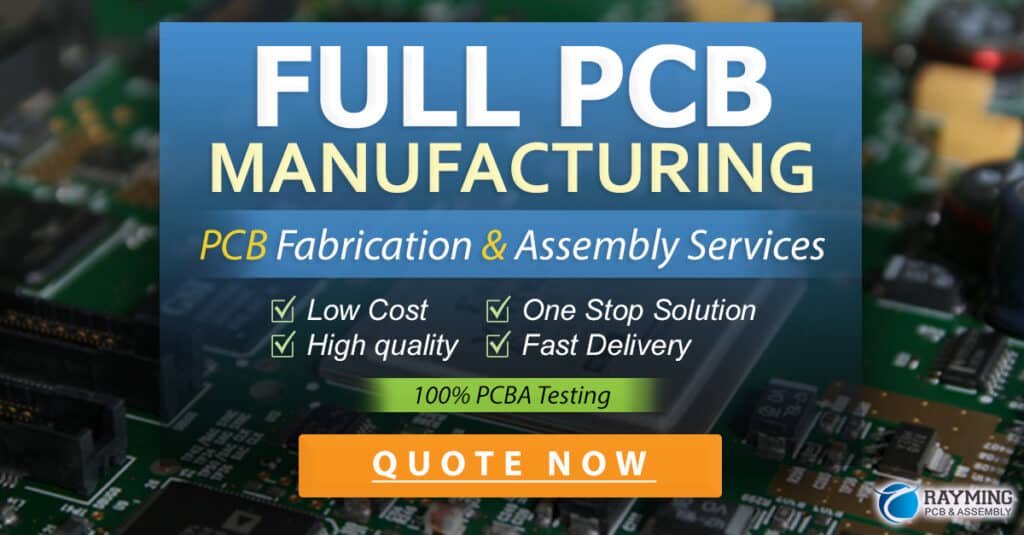
Designing a Buck Converter
Designing a buck converter involves choosing the appropriate component values based on the desired input voltage, output voltage, output current, and switching frequency. Here are the key steps in designing a buck converter:
- Determine the input voltage range and the desired output voltage.
- Select the switching frequency. Higher frequencies allow for smaller component sizes but may increase switching losses.
- Calculate the duty cycle using the formula: Duty Cycle = V_out / V_in
- Choose the inductor value based on the desired current ripple and the switching frequency.
- Select the capacitor value to achieve the desired output voltage ripple.
- Choose the appropriate diode and MOSFET based on the voltage and current ratings.
- Design the feedback network and control circuit to regulate the output voltage.
Here’s an example of a buck converter design:
Parameter | Value |
---|---|
Input Voltage (V_in) | 12V |
Output Voltage (V_out) | 5V |
Output Current (I_out) | 1A |
Switching Frequency (f) | 100kHz |
Inductor (L) | 33uH |
Capacitor (C) | 220uF |
Diode | 1N5819 |
MOSFET | IRF540N |
Building a DIY Buck Converter
Now that we have covered the theory and design aspects of buck converters, let’s dive into building your own DIY buck converter.
Step 1: Gather the Components
Collect all the necessary components based on your design calculations. Make sure to choose components with appropriate voltage and current ratings.
Step 2: Assemble the Circuit
Assemble the buck converter circuit on a breadboard or a printed circuit board (PCB). Follow the schematic diagram and ensure proper connections between components.
Step 3: Test and Troubleshoot
Apply the input voltage to the buck converter and measure the output voltage using a multimeter. Verify that the output voltage matches your desired value. If the output voltage is not as expected, troubleshoot the circuit by checking the connections, component values, and control circuit.
Step 4: Optimize and Enhance
Once your DIY buck converter is functioning correctly, you can optimize its performance by fine-tuning the component values, improving the PCB layout, and adding features such as overcurrent protection, short-circuit protection, and soft-start functionality.
Buck Converter Efficiency and Losses
Buck converters are known for their high efficiency, typically ranging from 80% to 95%. However, several factors contribute to power losses in a buck converter, including:
- Conduction losses in the inductor, MOSFET, and diode
- Switching losses in the MOSFET
- Core losses in the inductor
- Capacitor ESR (Equivalent Series Resistance) losses
To maximize efficiency, it’s important to select components with low parasitic resistances, use high-quality inductors and capacitors, and optimize the PCB layout to minimize stray inductance and capacitance.
Buck Converter Troubleshooting
If you encounter issues with your DIY buck converter, here are some common problems and their possible solutions:
- No output voltage:
- Check the input voltage and ensure it is within the specified range.
- Verify the connections and check for any short circuits or open connections.
-
Ensure the control circuit is functioning properly and generating the PWM signal.
-
Output voltage is too low or too high:
- Verify the component values, especially the inductor and capacitor.
- Check the feedback network and ensure the reference voltage is set correctly.
-
Adjust the duty cycle by modifying the control circuit or the feedback network.
-
Excessive output voltage ripple:
- Increase the capacitor value or use a capacitor with a lower ESR.
- Increase the switching frequency to reduce the current ripple.
-
Check for any loose connections or damaged components.
-
Overheating:
- Ensure proper heat dissipation for the MOSFET and diode.
- Use components with appropriate current ratings.
- Optimize the PCB layout to improve thermal management.
Frequently Asked Questions (FAQ)
- What is the difference between a buck converter and a linear regulator?
-
A buck converter is a switch-mode power supply that efficiently steps down the voltage, while a linear regulator is a linear power supply that reduces the voltage by dissipating excess power as heat. Buck converters are more efficient but have higher complexity and noise, while linear regulators are simpler but less efficient.
-
Can a buck converter step up the voltage?
-
No, a buck converter can only step down the voltage. To step up the voltage, you would need a Boost Converter or a buck-boost converter.
-
What is the purpose of the inductor in a buck converter?
-
The inductor stores energy during the ON phase and releases it during the OFF phase, smoothing out the current ripple and helping to maintain a constant output voltage.
-
How do I select the appropriate MOSFET for my buck converter?
-
Choose a MOSFET with a voltage rating higher than the maximum input voltage and a current rating sufficient for the expected load current. Consider the MOSFET’s on-resistance (R_DS(on)) and gate charge (Q_g) to minimize conduction and switching losses.
-
Can I use a buck converter for battery charging?
- Yes, buck converters can be used for battery charging by regulating the charging current and voltage. However, additional circuitry, such as a charge controller and protection features, may be required to ensure safe and efficient battery charging.
Conclusion
In this comprehensive tutorial, we explored the world of buck converters, understanding their principles, components, and how to build your own DIY buck converter. Buck converters are efficient and versatile power converters that find applications in a wide range of electronic devices and systems.
By following the design steps, selecting the appropriate components, and carefully assembling the circuit, you can create your own DIY buck converter and regulate voltage levels efficiently. Remember to consider factors such as efficiency, losses, and troubleshooting to ensure optimal performance.
Building a DIY buck converter is an excellent way to enhance your power electronics skills and dive deeper into the fascinating world of switch-mode power supplies. With the knowledge gained from this tutorial, you can confidently design and build buck converters for your future projects.
Happy building, and may your voltage conversions be smooth and efficient!
No responses yet