Table of Contents
- Introduction to Distance Sensors
- Types of Distance Sensors
- Ultrasonic Sensors
- Infrared Sensors
- Laser Rangefinders
- Time-of-Flight Sensors
- Factors to Consider When Choosing a Distance Sensor
- Range and Accuracy
- Resolution
- Response Time
- Environmental Factors
- Interface and Communication
- Applications of Distance Sensors
- Robotics and Automation
- Automotive Industry
- Security Systems
- Aerospace and Defense
- Industrial Monitoring
- Frequently Asked Questions (FAQ)
- Conclusion
- References
Introduction to Distance Sensors
Distance sensors are devices that measure the distance between the sensor and an object without physical contact. These sensors emit a signal, such as sound waves, light, or electromagnetic waves, which travels towards the object and is reflected back to the sensor. By measuring the time taken for the signal to travel to the object and return, the sensor can calculate the distance using the known speed of the signal.
Distance sensors have become increasingly important in various fields due to their ability to provide accurate and reliable distance measurements. They enable machines and systems to perceive their surroundings, detect obstacles, and make informed decisions based on the distance data.
Types of Distance Sensors
There are several types of distance sensors available, each with its own working principle, advantages, and limitations. Let’s explore the most common types of distance sensors:
Ultrasonic Sensors
Ultrasonic sensors use high-frequency sound waves to measure distance. They emit a short burst of ultrasonic waves and measure the time taken for the waves to bounce back from the object. By knowing the speed of sound in the medium (usually air), the sensor can calculate the distance using the time-of-flight principle.
Advantages of ultrasonic sensors:
– Non-contact measurement
– Insensitive to color, transparency, and surface reflectivity
– Relatively inexpensive
– Can detect objects of various materials
Limitations of ultrasonic sensors:
– Affected by environmental factors like temperature, humidity, and air pressure
– Limited range compared to other types of sensors
– Difficulty detecting soft or sound-absorbing materials
– Prone to interference from other ultrasonic sources
Infrared Sensors
Infrared (IR) sensors use infrared light to measure distance. They consist of an IR emitter that sends out a beam of infrared light and an IR receiver that detects the reflected light. The intensity of the reflected light is used to determine the distance to the object.
Advantages of infrared sensors:
– Non-contact measurement
– Fast response time
– Inexpensive compared to other types of sensors
– Suitable for short-range applications
Limitations of infrared sensors:
– Limited range (typically less than 1 meter)
– Affected by ambient light and reflective surfaces
– Difficulty detecting transparent or highly reflective objects
– Sensitivity to environmental factors like dust and fog
Laser Rangefinders
Laser rangefinders, also known as LIDAR (Light Detection and Ranging) sensors, use laser beams to measure distance. They emit a laser pulse towards the object and measure the time taken for the pulse to reflect back to the sensor. By calculating the time of flight and the speed of light, the sensor can determine the distance with high accuracy.
Advantages of laser rangefinders:
– High accuracy and precision
– Long-range measurement (up to several kilometers)
– Narrow beam width, enabling detection of small objects
– Suitable for outdoor applications
Limitations of laser rangefinders:
– Expensive compared to other types of sensors
– Eye safety concerns due to the use of lasers
– Affected by atmospheric conditions like fog, rain, and smoke
– Difficulty detecting highly reflective or transparent surfaces
Time-of-Flight Sensors
Time-of-Flight (ToF) sensors are a type of distance sensor that uses the time-of-flight principle to measure distance. They emit a modulated light signal, typically in the near-infrared range, and measure the phase shift between the emitted and reflected signals to calculate the distance.
Advantages of ToF sensors:
– High accuracy and precision
– Fast response time
– Suitable for short to medium-range applications
– Insensitive to ambient light
Limitations of ToF sensors:
– Limited range compared to laser rangefinders
– Affected by highly reflective or absorptive surfaces
– Interference from other ToF sensors or light sources
– Higher cost compared to ultrasonic and infrared sensors
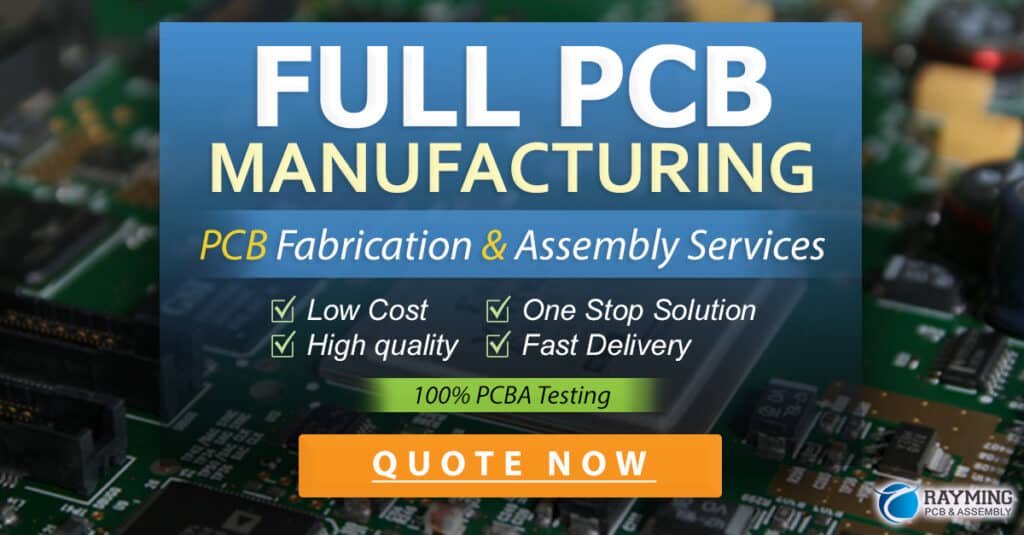
Factors to Consider When Choosing a Distance Sensor
When selecting a distance sensor for your application, several factors need to be considered to ensure optimal performance and reliability. Let’s discuss these factors in detail:
Range and Accuracy
The range and accuracy requirements of your application are crucial factors in choosing a distance sensor. Consider the minimum and maximum distances you need to measure and the level of accuracy required for your specific use case.
Sensor Type | Typical Range | Accuracy |
---|---|---|
Ultrasonic | 0.02m – 10m | ±1% – ±5% |
Infrared | 0.1m – 1m | ±5% – ±10% |
Laser Rangefinder | 0.1m – 1000m+ | ±0.1% – ±1% |
Time-of-Flight | 0.1m – 10m | ±1% – ±5% |
Resolution
Resolution refers to the smallest change in distance that a sensor can detect. Higher resolution sensors can provide more detailed and precise distance measurements. Consider the resolution requirements of your application and choose a sensor with appropriate resolution capabilities.
Response Time
Response time is the time taken by the sensor to provide a distance measurement after triggering. If your application requires real-time or high-speed measurements, opt for sensors with fast response times. Keep in mind that response time can be affected by factors like signal processing, data communication, and environmental conditions.
Environmental Factors
Distance sensors can be influenced by various environmental factors, such as temperature, humidity, dust, and ambient light. Consider the operating environment of your application and choose a sensor that can withstand and perform reliably in those conditions. Some sensors may require additional protection or enclosures to minimize the impact of environmental factors.
Interface and Communication
The interface and communication protocol of a distance sensor are important considerations for integration with your system. Common interfaces include analog voltage output, digital interfaces like I2C, SPI, or UART, and industrial protocols like RS-485 or CAN bus. Ensure that the chosen sensor is compatible with your system’s interface and communication requirements.
Applications of Distance Sensors
Distance sensors find applications in a wide range of industries and domains. Let’s explore some of the common applications:
Robotics and Automation
Distance sensors are extensively used in robotics and automation for obstacle detection, navigation, and collision avoidance. They enable robots to perceive their surroundings, map their environment, and make autonomous decisions based on distance information. Examples include mobile robots, automated guided vehicles (AGVs), and robotic arms in manufacturing.
Automotive Industry
In the automotive industry, distance sensors play a crucial role in advanced driver assistance systems (ADAS) and autonomous vehicles. They are used for features like adaptive cruise control, automatic emergency braking, parking assistance, and blind-spot detection. Sensors like ultrasonic, radar, and LIDAR are commonly employed in automotive applications.
Security Systems
Distance sensors are utilized in security systems for intrusion detection, perimeter monitoring, and access control. They can detect the presence and movement of objects or individuals within a specified range, triggering alarms or initiating appropriate actions. Infrared and ToF sensors are often used in security applications.
Aerospace and Defense
In the aerospace and defense sectors, distance sensors are employed for various purposes, such as altitude measurement, terrain mapping, and target tracking. High-precision laser rangefinders and radar systems are commonly used in these applications due to their long-range capabilities and accuracy.
Industrial Monitoring
Distance sensors find applications in industrial monitoring for level measurement, object detection, and process control. They can be used to monitor the level of liquids or solids in tanks, detect the presence of objects on conveyor belts, and ensure proper alignment in manufacturing processes. Ultrasonic and ToF sensors are frequently used in industrial settings.
Frequently Asked Questions (FAQ)
- What is the difference between accuracy and precision in distance sensors?
-
Accuracy refers to how close the measured distance is to the actual distance, while precision refers to the consistency of measurements over multiple readings. A sensor can be accurate but not precise, or precise but not accurate. Ideally, a distance sensor should have both high accuracy and high precision.
-
Can distance sensors work in outdoor environments?
-
Yes, distance sensors can work in outdoor environments, but their performance may be affected by factors like weather conditions, sunlight, and reflections. Some sensors, like laser rangefinders, are specifically designed for outdoor applications and can provide reliable measurements even in challenging environments.
-
How do I choose the right distance sensor for my application?
-
When choosing a distance sensor, consider factors like the required range, accuracy, resolution, response time, environmental conditions, and interface compatibility. Evaluate your specific application requirements and select a sensor that meets those criteria. It’s also important to consider the cost and availability of the sensor.
-
Can multiple distance sensors interfere with each other?
-
Yes, multiple distance sensors operating in close proximity can potentially interfere with each other, especially if they use the same technology and frequency. To mitigate interference, you can use sensors with different frequencies or technologies, implement proper shielding and filtering techniques, or employ time-division multiplexing to synchronize the operation of multiple sensors.
-
How do I integrate a distance sensor with my microcontroller or embedded system?
- The integration process depends on the specific sensor and microcontroller or embedded system you are using. Most distance sensors provide either analog or digital output signals that can be connected to the appropriate pins on your microcontroller. You may need to use libraries or write custom code to interface with the sensor and interpret the distance data. Refer to the sensor’s datasheet and application notes for detailed integration instructions.
Conclusion
Distance sensors are vital components in a wide range of applications, enabling machines and systems to perceive and measure distances accurately. By understanding the different types of distance sensors, their working principles, and the factors to consider when selecting a sensor, you can make informed decisions for your specific project requirements.
When choosing a distance sensor, consider the range, accuracy, resolution, response time, environmental factors, and interface compatibility. Each sensor technology has its own advantages and limitations, so it’s essential to evaluate your application needs and select the most suitable sensor accordingly.
With the advancements in sensor technology and the increasing demand for automation and intelligent systems, distance sensors will continue to play a crucial role in shaping the future of various industries. By leveraging the capabilities of these sensors, we can create smarter, safer, and more efficient solutions for a wide range of applications.
References
- Fraden, J. (2016). Handbook of modern sensors: physics, designs, and applications. Springer.
- Luo, R. C., & Su, K. L. (2007). A review of high-level multisensor fusion: approaches and applications. IEEE Transactions on Systems, Man, and Cybernetics, Part C (Applications and Reviews), 37(6), 1096-1114.
- Massa, D. P. (1999). Choosing an ultrasonic sensor for proximity or distance measurement. Sensors, 16(2), 1-6.
- Schwarz, B. (2010). LIDAR: Mapping the world in 3D. Nature Photonics, 4(7), 429-430.
- Webster, J. G. (Ed.). (1999). The measurement, instrumentation and sensors handbook. CRC press.
No responses yet