What is a Digital PCB?
A Digital PCB is a specialized type of printed circuit board designed to handle binary digital signals. Unlike analog signals, which can take on a continuous range of values, digital signals operate on a discrete set of values, typically represented as 0s and 1s. Digital PCBs are optimized to transmit and process these binary signals, ensuring reliable and high-speed communication between digital components.
Binary Digital Signals
Binary digital signals form the foundation of digital electronics. In a binary system, information is represented using only two states: 0 and 1. These states can be interpreted as:
- Low voltage (0) and high voltage (1)
- Off (0) and On (1)
- False (0) and True (1)
Digital circuits process and transmit data using these binary states, allowing for efficient and error-resistant communication.
Designing Digital PCBs
Designing a Digital PCB requires careful consideration of various factors to ensure optimal performance and reliability. Let’s explore some key aspects of Digital PCB design.
Signal Integrity
Signal integrity is of utmost importance in Digital PCB design. As digital signals traverse the PCB, they can be subject to various issues such as crosstalk, reflections, and noise. To maintain signal integrity, designers must consider:
- Impedance matching: Ensuring proper impedance matching between the signal source, transmission lines, and receiver to minimize reflections and signal distortion.
- Trace routing: Carefully routing signal traces to minimize crosstalk and interference between adjacent traces.
- Grounding and shielding: Implementing proper grounding and shielding techniques to reduce electromagnetic interference (EMI) and maintain signal quality.
High-Speed Design Considerations
Digital PCBs often operate at high frequencies, necessitating special design considerations. High-speed designs must account for:
- Transmission line effects: As signal frequencies increase, traces on the PCB behave like transmission lines. Designers must consider impedance matching, termination, and trace geometry to ensure signal integrity.
- Power delivery: High-speed digital components require clean and stable power supplies. Decoupling capacitors and power plane design are crucial to minimize power supply noise and ensure reliable operation.
- Clock distribution: Synchronous digital systems rely on precise clock distribution. Designers must ensure low-skew clock routing and implement techniques like balanced clock trees and clock buffering.
Component Placement and Routing
Proper component placement and routing are essential for optimal Digital PCB performance. Designers should consider:
- Component proximity: Placing related components close together to minimize signal path lengths and reduce parasitic effects.
- Signal routing: Routing signal traces efficiently to minimize trace lengths, avoid unnecessary crossings, and maintain signal integrity.
- Thermal management: Placing heat-generating components strategically and providing adequate thermal dissipation measures to prevent overheating.
Manufacturing Digital PCBs
Manufacturing Digital PCBs involves several processes to transform the PCB design into a physical board. Let’s explore the key steps involved.
PCB Fabrication
PCB fabrication begins with the creation of the PCB substrate, typically made of FR-4 material. The substrate is laminated with copper foil on one or both sides. The copper layer is then patterned using photolithography and etching techniques to create the desired circuit traces and pads.
Surface Mount Technology (SMT)
Surface Mount Technology (SMT) is widely used in Digital PCB assembly. SMT involves placing and soldering surface mount components directly onto the PCB surface. The process typically involves:
- Solder paste application: A precise amount of solder paste is applied to the component pads using a stencil or screen printing process.
- Component placement: Surface mount components are placed onto the solder paste using pick-and-place machines.
- Reflow soldering: The PCB is heated in a reflow oven, melting the solder paste and creating a permanent electrical and mechanical connection between the components and the PCB.
Through-Hole Technology (THT)
Through-Hole Technology (THT) involves mounting components with leads that are inserted into drilled holes on the PCB. The leads are then soldered to the PCB on the opposite side. THT is often used for larger components or those requiring higher mechanical strength.
Quality Control and Testing
Quality control and testing are critical steps in Digital PCB manufacturing. Various methods are employed to ensure the reliability and functionality of the manufactured PCBs:
- Automated Optical Inspection (AOI): AOI systems use high-resolution cameras and image processing algorithms to detect manufacturing defects such as missing components, incorrect component placement, or solder bridging.
- In-Circuit Testing (ICT): ICT involves using specialized test fixtures to verify the electrical connectivity and functionality of individual components on the PCB.
- Functional Testing: Functional testing subjects the PCB to its intended operating conditions to validate its overall performance and functionality.
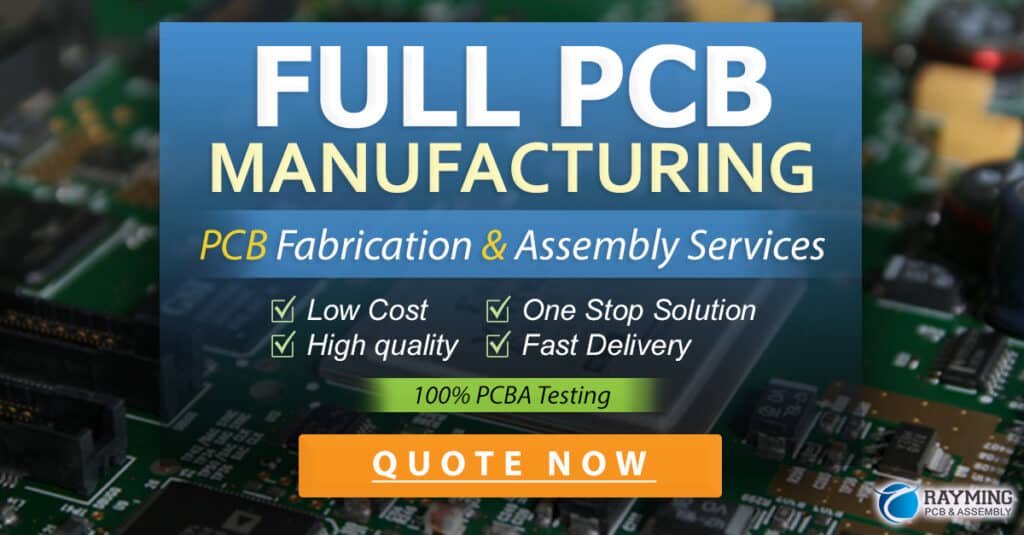
Applications of Digital PCBs
Digital PCBs find applications in a wide range of electronic devices and systems. Some common applications include:
-
Computer hardware: Digital PCBs are extensively used in computer motherboards, graphics cards, memory modules, and storage devices.
-
Telecommunications: Digital PCBs are essential in telecommunications equipment such as routers, switches, and modems.
-
Consumer electronics: Digital PCBs are found in smartphones, tablets, televisions, gaming consoles, and other consumer electronic devices.
-
Industrial automation: Digital PCBs play a crucial role in industrial automation systems, including programmable logic controllers (PLCs), sensors, and control panels.
-
Automotive electronics: Digital PCBs are used in various automotive electronic systems, such as engine control units (ECUs), infotainment systems, and advanced driver assistance systems (ADAS).
Frequently Asked Questions (FAQ)
1. What is the difference between a Digital PCB and an Analog PCB?
Digital PCBs are designed to handle binary digital signals, which operate on discrete values (0s and 1s). Analog PCBs, on the other hand, are designed to handle continuous signals that can vary in amplitude and frequency. Digital PCBs focus on maintaining signal integrity and high-speed transmission, while Analog PCBs prioritize preserving signal fidelity and minimizing noise.
2. What materials are commonly used for Digital PCB substrates?
FR-4 is the most commonly used material for Digital PCB substrates. It is a glass-reinforced epoxy laminate that offers good mechanical strength, electrical insulation, and thermal stability. Other materials, such as high-frequency laminates (e.g., Rogers) or flexible substrates (e.g., polyimide), may be used for specific applications that require enhanced performance or flexibility.
3. How do you ensure signal integrity in high-speed Digital PCBs?
To ensure signal integrity in high-speed Digital PCBs, designers employ various techniques:
– Impedance matching: Ensuring proper impedance matching between signal source, transmission lines, and receiver.
– Trace routing: Minimizing crosstalk and interference by carefully routing signal traces.
– Grounding and shielding: Implementing proper grounding and shielding to reduce electromagnetic interference (EMI).
– Termination: Using appropriate termination techniques to minimize reflections and signal distortions.
4. What is the role of solder mask on Digital PCBs?
Solder mask is a protective layer applied to the copper traces on a Digital PCB. It serves several purposes:
– Insulation: Solder mask provides electrical insulation between adjacent traces, preventing short circuits.
– Protection: It protects the copper traces from oxidation, corrosion, and physical damage.
– Solder control: Solder mask defines the areas where solder should be applied during the assembly process, preventing solder bridges and improving manufacturing yield.
5. How do you test and validate Digital PCBs?
Digital PCBs are tested and validated using various methods:
– Automated Optical Inspection (AOI): AOI systems use cameras and image processing to detect manufacturing defects.
– In-Circuit Testing (ICT): ICT employs specialized test fixtures to verify the electrical connectivity and functionality of individual components.
– Functional Testing: Functional testing involves subjecting the PCB to its intended operating conditions to validate its overall performance and functionality.
– Boundary Scan Testing: Boundary scan testing, also known as JTAG testing, allows for testing of individual components and interconnects on the PCB using a standard interface.
Conclusion
Digital PCBs are the backbone of modern electronic devices, enabling reliable and high-speed communication between digital components. Understanding the design, manufacturing, and testing processes of Digital PCBs is crucial for engineers and technicians working in the electronics industry.
By considering factors such as signal integrity, high-speed design, component placement, and routing, designers can create robust and efficient Digital PCBs. Manufacturing processes like PCB fabrication, SMT, and THT assembly, along with rigorous quality control and testing, ensure the production of high-quality Digital PCBs.
As technology continues to advance, the importance of Digital PCBs will only grow. From consumer electronics to industrial automation, Digital PCBs will remain at the forefront of electronic design and innovation, powering the digital world we live in.
No responses yet