What is Solder?
Solder is a fusible metal alloy used to create a permanent bond between metal surfaces. It is melted and applied to the joint, where it solidifies and forms a strong electrical and mechanical connection. The most common types of solder are composed of tin (Sn) and lead (Pb), although lead-free alternatives are increasingly popular due to environmental and health concerns.
Solder Alloy Compositions
Tin-Lead (Sn-Pb) Solder
Tin-lead solder is the most traditional and widely used type of solder. The most common compositions are:
- 63/37 (63% tin, 37% lead): Eutectic composition with a melting point of 183°C (361°F)
- 60/40 (60% tin, 40% lead): Near-eutectic composition with a melting range of 183-190°C (361-374°F)
- 50/50 (50% tin, 50% lead): Used for higher-temperature applications, melting range of 183-216°C (361-421°F)
Tin-lead solder offers excellent wetting properties, making it ideal for electronics assembly and repair.
Lead-Free Solder
Due to environmental and health concerns surrounding lead, lead-free solder alloys have been developed. Common lead-free solder compositions include:
- SAC (Tin-Silver-Copper): Typically contains 3-4% silver and 0.5-0.7% copper, with the remainder being tin. Popular compositions include SAC305 and SAC387.
- Tin-Copper (Sn-Cu): Consists of 99.3% tin and 0.7% copper, with a melting point of 227°C (441°F).
- Tin-Silver (Sn-Ag): Contains 3.5-4% silver, with the remainder being tin. Melting range of 221-229°C (430-444°F).
Lead-free solders have higher melting points compared to tin-lead solders, requiring adjustments in soldering processes and equipment.
Other Solder Alloys
Some specialized applications may require other solder alloys, such as:
- Indium-based solders: Used for low-temperature soldering and bonding to glass or ceramic surfaces.
- Bismuth-based solders: Offer low melting points and are used in step soldering processes.
- High-temperature solders: Contain metals like gold, silver, or palladium for high-temperature applications.
Solder Forms and Packaging
Solder is available in various forms and packaging options to suit different applications and soldering methods.
Solder Wire
Solder wire is the most common form of solder used in electronics. It consists of a core of solder alloy surrounded by a rosin or acid flux. The flux helps to remove oxides and promote wetting during the soldering process. Solder wire is available in different diameters, alloy compositions, and flux types (e.g., no-clean, water-soluble, or rosin-activated).
Solder Paste
Solder paste is a mixture of powdered solder alloy and flux. It is used in surface mount technology (SMT) for reflow soldering. The paste is applied to the PCB pads using a stencil or syringe, and the components are placed on top. During the reflow process, the solder melts and forms a connection between the component leads and the PCB pads.
Solder Bar or Ingot
Solder bars or ingots are used for wave soldering or dip soldering processes. They are melted in a solder pot, and the molten solder is used to create a solder wave or bath into which the PCB is dipped to form solder joints.
Solder Preforms
Solder preforms are pre-shaped pieces of solder designed for specific applications. They can be in the form of rings, discs, or custom shapes and are often used in high-volume production or for soldering large components.
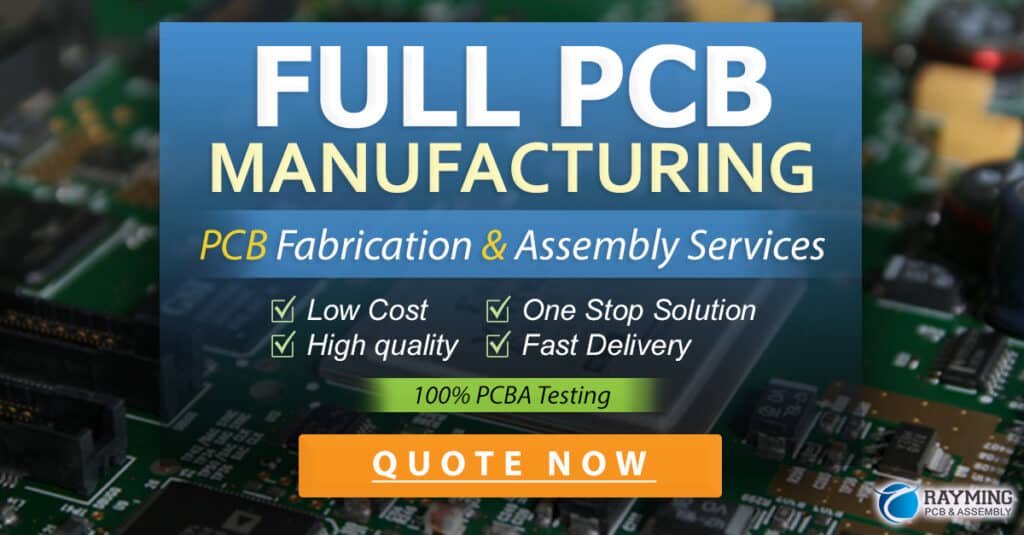
Flux Types and Classifications
Flux is a crucial component in the soldering process, as it helps to remove oxides from the metal surfaces, prevent oxidation during soldering, and promote wetting of the solder. There are several types of flux, each with its own characteristics and applications.
Rosin Flux
Rosin flux is a natural, non-corrosive flux derived from pine resin. It is available in three activity levels:
- R: Rosin (mildest)
- RMA: Rosin Mildly Activated
- RA: Rosin Activated (most active)
Rosin flux is commonly used in electronics soldering and is available in liquid, paste, or solid forms.
Water-Soluble Flux
Water-soluble flux is a highly active, organic acid-based flux that requires cleaning after soldering. It is often used in high-volume production and for soldering difficult-to-wet surfaces.
No-Clean Flux
No-clean flux is designed to leave minimal, non-corrosive residue after soldering, eliminating the need for post-soldering cleaning. This type of flux is popular in electronics assembly, as it simplifies the production process and reduces costs.
Soldering Techniques and Applications
Different soldering techniques are employed based on the type of components, the scale of production, and the specific requirements of the application.
Hand Soldering
Hand soldering is a manual technique using a soldering iron to heat the solder and the components being joined. This method is suitable for low-volume production, prototyping, and repairs.
Wave Soldering
Wave soldering is an automated process used for through-hole components. The PCB is passed over a wave of molten solder, which wets the component leads and forms solder joints.
Reflow Soldering
Reflow soldering is used for surface mount components. Solder paste is applied to the PCB pads, and the components are placed on top. The assembly is then heated in a reflow oven, melting the solder and forming the joints.
Selective Soldering
Selective soldering is a process that combines the automation of wave soldering with the precision of hand soldering. It is used for soldering specific components or areas on a PCB, often in mixed-technology assemblies.
Solder Selection Factors
When choosing a solder for a specific application, several factors should be considered:
- Melting temperature: The solder alloy should have a suitable melting temperature for the components and substrate materials being used.
- Wetting ability: The solder should be able to wet the surfaces being joined effectively.
- Mechanical strength: The solder joint should provide adequate mechanical strength for the application.
- Electrical conductivity: For electronics applications, the solder should have good electrical conductivity.
- Environmental and health considerations: Lead-free solders are preferred where environmental and health regulations apply.
- Compatibility with the soldering process: The solder form and packaging should be suitable for the soldering technique being used.
Frequently Asked Questions (FAQ)
-
What is the most common solder alloy used in electronics?
The most common solder alloy used in electronics is 63/37 tin-lead (Sn-Pb) solder, which has a eutectic composition and a melting point of 183°C (361°F). -
Why are lead-free solders becoming more popular?
Lead-free solders are becoming more popular due to environmental and health concerns surrounding the use of lead. Many countries have implemented regulations restricting the use of lead in electronics. -
What is flux, and why is it important in soldering?
Flux is a chemical compound used in soldering to remove oxides from the metal surfaces, prevent oxidation during the soldering process, and promote wetting of the solder. It is essential for achieving strong, reliable solder joints. -
Can different types of solder be mixed?
It is generally not recommended to mix different types of solder, as they may have different melting temperatures, wetting properties, and mechanical characteristics. Mixing solders can result in weak or unreliable solder joints. -
How do I choose the right solder for my application?
When selecting a solder, consider factors such as the melting temperature, wetting ability, mechanical strength, electrical conductivity, environmental and health considerations, and compatibility with the soldering process. Consult with a solder manufacturer or supplier for guidance on selecting the most suitable solder for your specific application.
Conclusion
Understanding the different types of solder and their properties is essential for achieving strong, reliable solder joints in various applications. From traditional tin-lead solders to lead-free alternatives, solder alloys are available in a range of compositions, forms, and packaging options to suit different soldering techniques and requirements. By considering factors such as melting temperature, wetting ability, mechanical strength, and compatibility with the soldering process, you can select the most appropriate solder for your specific needs. As environmental and health concerns drive the adoption of lead-free solders, it is crucial to stay informed about the latest developments and regulations in the field of soldering.
Comparison Table: Common Solder Alloy Compositions
Solder Alloy | Composition | Melting Point/Range (°C) | Applications |
---|---|---|---|
63/37 Sn-Pb | 63% Sn, 37% Pb | 183 | Electronics assembly and repair |
60/40 Sn-Pb | 60% Sn, 40% Pb | 183-190 | Electronics assembly and repair |
SAC305 | 96.5% Sn, 3% Ag, 0.5% Cu | 217-220 | Lead-free electronics assembly |
Sn-Cu | 99.3% Sn, 0.7% Cu | 227 | Lead-free electronics assembly |
Sn-Ag | 96.5% Sn, 3.5% Ag | 221-229 | Lead-free electronics assembly |
By providing a comprehensive overview of Solder Types, their properties, and applications, this article aims to serve as a valuable resource for professionals and enthusiasts in the fields of electronics manufacturing, metalworking, and beyond. With the right knowledge and selection of solder, you can ensure the creation of strong, reliable, and long-lasting solder joints in your projects.
No responses yet