What is a PCB Substrate?
A PCB substrate is the insulating material that forms the base of a printed circuit board. It provides mechanical support and electrical insulation between the conductive layers of the PCB. The substrate material is typically a dielectric, meaning it has a high resistance to electrical current flow. The choice of substrate material depends on various factors such as the intended application, operating environment, frequency range, and budget.
Importance of Choosing the Right PCB Substrate
Selecting the appropriate PCB substrate material is essential for several reasons:
-
Electrical Properties: The substrate material affects the electrical performance of the PCB, including dielectric constant, dissipation factor, and insulation resistance. These properties influence signal integrity, impedance control, and power handling capabilities.
-
Mechanical Strength: The substrate material should provide sufficient mechanical strength to withstand the stresses encountered during manufacturing, assembly, and operation. It should also have good dimensional stability to maintain the integrity of the conductive traces.
-
Thermal Management: The substrate material plays a role in heat dissipation and thermal management of the PCB. Some materials have better thermal conductivity than others, allowing for more efficient heat transfer and preventing excessive temperature rise.
-
Environmental Factors: The substrate material must be able to withstand the environmental conditions in which the PCB will operate. This includes factors such as temperature range, humidity, chemical exposure, and mechanical stress.
-
Cost: The choice of substrate material directly impacts the overall cost of the PCB. Some materials are more expensive than others, and the cost must be balanced against the required performance and reliability.
Common Types of PCB Substrate Materials
There are several types of PCB substrate materials available, each with its own set of characteristics and advantages. Let’s explore some of the most common options:
1. FR-4 (Flame Retardant 4)
FR-4 is the most widely used PCB substrate material. It is a composite material made of woven fiberglass cloth impregnated with an epoxy resin binder. FR-4 offers a good balance of electrical, mechanical, and thermal properties at a relatively low cost. It has a dielectric constant of approximately 4.5 and can operate in a temperature range of -55°C to +125°C. FR-4 is suitable for a wide range of applications, including consumer electronics, industrial controls, and telecommunications equipment.
2. High Tg FR-4
High Tg FR-4 is a variant of the standard FR-4 material with improved thermal properties. It has a higher glass transition temperature (Tg), typically around 170°C or higher, compared to the standard FR-4’s Tg of around 130°C. This enhanced thermal stability makes High Tg FR-4 suitable for applications that require higher operating temperatures or increased reliability in harsh environments. It is commonly used in automotive electronics, aerospace systems, and high-power applications.
3. Polyimide
Polyimide is a high-performance substrate material known for its excellent thermal stability, chemical resistance, and mechanical strength. It can withstand temperatures up to 260°C and has a low dielectric constant of around 3.5. Polyimide is often used in applications that demand high reliability, such as aerospace, military, and medical devices. However, it is more expensive than FR-4 and has a higher coefficient of thermal expansion (CTE), which can pose challenges in manufacturing and assembly.
4. PTFE (Polytetrafluoroethylene)
PTFE, also known as Teflon, is a fluoropolymer material with outstanding electrical properties. It has a very low dielectric constant (typically 2.1) and a low dissipation factor, making it ideal for high-frequency applications such as radar systems, microwave devices, and RF circuits. PTFE is also known for its excellent chemical resistance and low moisture absorption. However, it is more expensive than other substrate materials and can be challenging to process due to its non-stick properties.
5. Rogers Materials
Rogers Corporation offers a range of high-performance substrate materials specifically designed for demanding applications. Some popular Rogers materials include:
- RO4000 Series: These materials are glass-reinforced hydrocarbon/ceramic laminates with low dielectric constant and low loss tangent. They are suitable for high-frequency applications up to 30 GHz.
- RT/duroid: These PTFE-based materials offer excellent electrical properties, including low dielectric constant and low dissipation factor. They are commonly used in microwave and RF applications.
- RO3000 Series: These ceramic-filled PTFE composites provide a balance of electrical performance and ease of fabrication. They are suitable for high-frequency applications up to 77 GHz.
Rogers materials are known for their consistent dielectric properties, dimensional stability, and low moisture absorption. However, they come at a higher cost compared to standard FR-4.
6. Aluminum-based Substrates
Aluminum-based substrates, such as Aluminum-clad laminates and Insulated Metal Substrates (IMS), offer excellent thermal management capabilities. They consist of a dielectric layer bonded to an aluminum base, which acts as a heat spreader. These substrates are commonly used in high-power applications, such as power electronics, LED lighting, and automotive modules. They provide efficient heat dissipation, allowing for higher power densities and improved reliability. However, aluminum-based substrates are more expensive than FR-4 and require specialized manufacturing processes.
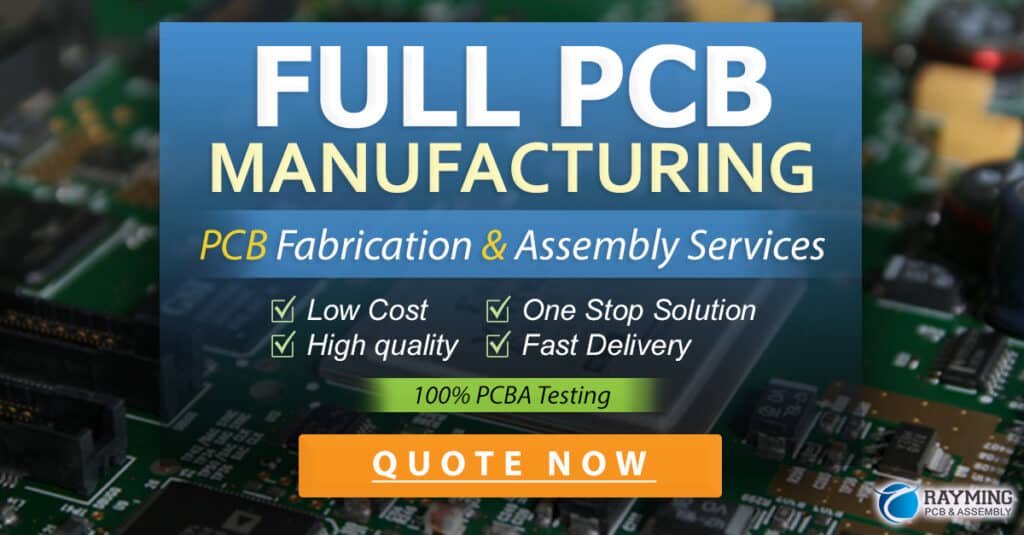
Comparison Table of PCB Substrate Materials
Material | Dielectric Constant | Dissipation Factor | Thermal Stability (Tg) | Typical Applications |
---|---|---|---|---|
FR-4 | 4.5 | 0.02 | 130°C | Consumer electronics, industrial controls |
High Tg FR-4 | 4.5 | 0.02 | 170°C or higher | Automotive, aerospace, high-power applications |
Polyimide | 3.5 | 0.002 | 260°C | Aerospace, military, medical devices |
PTFE | 2.1 | 0.0002 | 260°C | Radar systems, microwave devices, RF circuits |
Rogers RO4000 | 3.3 – 3.5 | 0.0027 – 0.0037 | 280°C | High-frequency applications up to 30 GHz |
Aluminum-based | Varies | Varies | Varies | High-power applications, LED lighting, automotive |
Factors to Consider When Choosing a PCB Substrate Material
When selecting a PCB substrate material for your project, consider the following factors:
-
Electrical Requirements: Evaluate the dielectric constant, dissipation factor, and insulation resistance required for your application. Consider the operating frequency range and signal integrity needs.
-
Thermal Management: Assess the thermal requirements of your PCB. If your application involves high power dissipation or operates in a high-temperature environment, choose a substrate material with good thermal conductivity and stability.
-
Mechanical Strength: Consider the mechanical stresses your PCB will encounter during manufacturing, assembly, and operation. Select a substrate material with sufficient strength and dimensional stability to withstand these stresses.
-
Environmental Factors: Evaluate the environmental conditions in which your PCB will operate. Consider factors such as temperature range, humidity, chemical exposure, and mechanical shock/vibration. Choose a substrate material that can withstand these conditions.
-
Cost: Assess the cost implications of different substrate materials. While some high-performance materials offer superior properties, they may come at a higher cost. Strike a balance between the required performance and the budget constraints of your project.
Frequently Asked Questions (FAQ)
-
Q: What is the most commonly used PCB substrate material?
A: FR-4 is the most widely used PCB substrate material. It offers a good balance of electrical, mechanical, and thermal properties at a relatively low cost, making it suitable for a wide range of applications. -
Q: Which PCB substrate material is best for high-frequency applications?
A: For high-frequency applications, PTFE (Teflon) and Rogers materials are popular choices. PTFE has a very low dielectric constant and low dissipation factor, making it ideal for applications such as radar systems, microwave devices, and RF circuits. Rogers materials, such as RO4000 series and RT/duroid, offer excellent electrical properties and are commonly used in high-frequency applications up to 77 GHz. -
Q: What is the difference between standard FR-4 and High Tg FR-4?
A: The main difference between standard FR-4 and High Tg FR-4 is the glass transition temperature (Tg). High Tg FR-4 has a higher Tg, typically around 170°C or higher, compared to the standard FR-4’s Tg of around 130°C. This higher Tg provides improved thermal stability, making High Tg FR-4 suitable for applications that require higher operating temperatures or increased reliability in harsh environments. -
Q: Are there any PCB substrate materials specifically designed for thermal management?
A: Yes, aluminum-based substrates, such as Aluminum-clad laminates and Insulated Metal Substrates (IMS), are specifically designed for thermal management. They consist of a dielectric layer bonded to an aluminum base, which acts as a heat spreader. These substrates are commonly used in high-power applications, such as power electronics, LED lighting, and automotive modules, where efficient heat dissipation is crucial. -
Q: How do I choose the right PCB substrate material for my project?
A: Choosing the right PCB substrate material depends on several factors. Consider the electrical requirements (dielectric constant, dissipation factor), thermal management needs, mechanical strength, environmental factors (temperature range, humidity, chemical exposure), and cost constraints of your project. Evaluate the specific requirements of your application and consult with PCB manufacturers or material suppliers to select the most suitable substrate material.
Conclusion
Selecting the appropriate PCB substrate material is a critical decision in the design and manufacturing of printed circuit boards. Each substrate material has its own unique properties and characteristics, making it suitable for specific applications and requirements. FR-4 is the most commonly used substrate material, offering a good balance of properties at a low cost. High Tg FR-4 provides improved thermal stability, while polyimide and PTFE are known for their excellent thermal and electrical properties. Rogers materials are specifically designed for high-frequency applications, and aluminum-based substrates offer superior thermal management capabilities.
When choosing a PCB substrate material, consider factors such as electrical requirements, thermal management, mechanical strength, environmental conditions, and cost. Evaluate the specific needs of your project and consult with PCB manufacturers or material suppliers to make an informed decision.
By understanding the different types of PCB substrate materials and their properties, you can select the most suitable option for your project, ensuring optimal performance, reliability, and cost-effectiveness.
No responses yet