Introduction to BGA Design
Ball Grid Array (BGA) packages have become increasingly popular in modern Electronic Design due to their high density, improved electrical performance, and reduced package size. However, designing with BGAs requires careful consideration of manufacturability and cost factors to ensure a successful product. In this article, we will explore the key aspects of BGA design, focusing on techniques to optimize manufacturability and minimize costs.
Understanding BGA Packages
What is a BGA?
A BGA is a surface-mount package that utilizes an array of solder balls on the bottom of the package to provide electrical connections to the printed circuit board (PCB). The solder balls are arranged in a grid pattern, allowing for a high density of interconnects in a compact package size.
Advantages of BGA Packages
- High density interconnects
- Improved electrical performance
- Reduced package size
- Better thermal dissipation
Challenges in BGA Design
- Manufacturability concerns
- Increased design complexity
- Thermal management
- Cost considerations
BGA Design Considerations
Pad Layout and Pitch
The pad layout and pitch are critical factors in BGA design. The pitch, which is the distance between the centers of adjacent solder balls, determines the density of the package. Common BGA pitches include:
Pitch (mm) | Description |
---|---|
1.27 | Low density |
1.00 | Medium density |
0.80 | High density |
0.65 | Very high density |
When selecting the appropriate pitch, consider the PCB manufacturing capabilities, routing requirements, and the package size constraints.
Solder Ball Size and Composition
The size and composition of the solder balls play a significant role in BGA manufacturability and reliability. Commonly used solder ball sizes include:
Diameter (mm) | Description |
---|---|
0.50 | Standard |
0.40 | Fine pitch |
0.30 | Ultra-fine pitch |
Solder ball composition affects the melting temperature, wetting characteristics, and reliability of the BGA package. Lead-free solder alloys, such as SAC305 (96.5% Sn, 3.0% Ag, 0.5% Cu), have become the preferred choice due to environmental regulations.
PCB Design and Routing
Designing the PCB for a BGA package requires careful planning and attention to detail. Consider the following factors:
- Via placement and size
- Trace width and spacing
- Signal integrity and Impedance Control
- Power and Ground Plane design
- Thermal management
Use PCB design tools with BGA-specific features, such as automatic via generation and fan-out pattern creation, to streamline the design process and ensure manufacturability.
Thermal Management
BGAs generate significant heat due to their high density and power dissipation. Effective thermal management is essential to ensure reliable operation and prevent premature failure. Consider the following techniques:
- Thermal vias and heat spreaders
- Copper pours and Thermal Pads
- Airflow and cooling solutions
- Thermal interface materials (TIMs)
Conduct thermal simulations and testing to validate the thermal performance of the BGA design and make necessary adjustments.
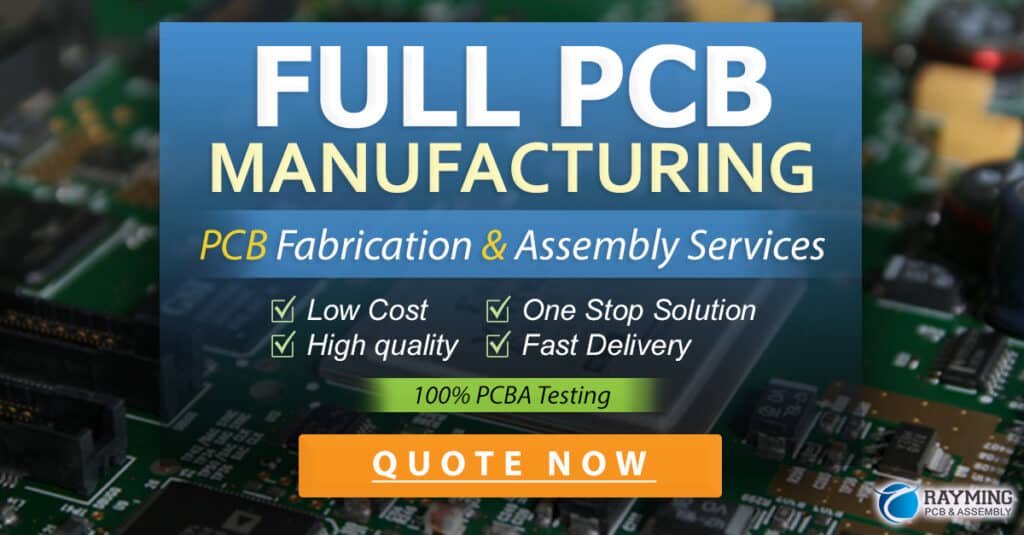
Manufacturing Considerations
Assembly Process
The assembly process for BGA packages requires specialized equipment and techniques. The key steps include:
- Solder paste printing
- Component placement
- Reflow soldering
- Inspection and testing
Ensure that the manufacturing facility has the necessary capabilities and experience in handling BGA packages to minimize defects and improve yield.
Reflow Profile Optimization
Developing an optimal reflow profile is crucial for achieving reliable BGA solder joints. The reflow profile should consider the following factors:
- Solder paste characteristics
- Component thermal mass
- PCB Thickness and layer count
- Oven capabilities
Follow the solder paste manufacturer’s guidelines and conduct process validation to fine-tune the reflow profile for the specific BGA package and PCB design.
Inspection and Testing
Thorough inspection and testing are essential to ensure the quality and reliability of BGA assemblies. Common inspection methods include:
- X-ray inspection
- Automated optical inspection (AOI)
- Boundary scan testing
- Functional testing
Implement a comprehensive inspection and testing strategy to identify and address any manufacturing issues early in the process.
Cost Optimization Strategies
Component Selection
Careful component selection can significantly impact the overall cost of a BGA design. Consider the following factors:
- BGA package availability and pricing
- Pin count and ball pitch
- Packaging options (e.g., trays, tape and reel)
- Minimum order quantities (MOQs)
Collaborate with component suppliers and distributors to identify cost-effective BGA solutions that meet the design requirements.
Design for Manufacturing (DFM)
Incorporating DFM principles into the BGA design process can help reduce manufacturing costs and improve yield. Key DFM considerations include:
- Standardizing component sizes and pitches
- Avoiding tight tolerances and complex geometries
- Providing adequate clearances and spacing
- Minimizing the number of unique components
Conduct DFM reviews with the manufacturing team to identify and address potential issues early in the design cycle.
Supply Chain Management
Effective supply chain management is essential for controlling costs and ensuring the availability of BGA components. Consider the following strategies:
- Establishing long-term relationships with suppliers
- Negotiating volume discounts and favorable terms
- Implementing just-in-time (JIT) inventory management
- Monitoring market trends and anticipating supply disruptions
Collaborate with the procurement and logistics teams to develop a robust supply chain strategy that supports the BGA design and manufacturing process.
Frequently Asked Questions (FAQ)
- What is the difference between a BGA and a QFN package?
-
A BGA package uses an array of solder balls on the bottom of the package for electrical connections, while a QFN (Quad Flat No-lead) package has exposed pads on the bottom surface without solder balls.
-
Can BGAs be reworked or repaired?
-
Yes, BGAs can be reworked or repaired using specialized equipment and techniques, such as hot air rework stations and reballing processes. However, rework should be minimized through proper design and manufacturing practices.
-
How do I select the appropriate BGA package for my design?
-
When selecting a BGA package, consider factors such as pin count, pitch, thermal requirements, electrical performance, and cost. Consult with component suppliers and review their product datasheets to identify suitable options.
-
What is the impact of voids in BGA solder joints?
-
Voids in BGA solder joints can reduce the mechanical strength and thermal conductivity of the joint, potentially leading to reliability issues. Proper process control, including solder paste selection and reflow profile optimization, can help minimize void formation.
-
How can I minimize the risk of BGA manufacturing defects?
- To minimize the risk of BGA manufacturing defects, follow best practices such as implementing DFM guidelines, optimizing the reflow profile, conducting thorough inspections and testing, and collaborating closely with the manufacturing team throughout the design and production process.
Conclusion
Designing with BGAs for manufacturability and cost requires a comprehensive approach that considers various factors, including package selection, PCB design, manufacturing processes, and supply chain management. By following best practices and collaborating with cross-functional teams, designers can create BGA-based products that are reliable, cost-effective, and manufacturable at scale.
As BGA technology continues to evolve, staying updated with the latest advancements and industry standards is essential for successful BGA design. By embracing a proactive and holistic approach to BGA design, companies can unlock the full potential of this packaging technology while minimizing risks and optimizing costs.
No responses yet