What is Design Rule Check (DRC)?
Design Rule Check, commonly referred to as DRC, is an essential step in the integrated circuit (IC) design process. It is an automated verification tool that ensures the layout of an IC adheres to a set of predefined design rules. These rules are established by the semiconductor foundry or fabrication facility and are based on the limitations and capabilities of their manufacturing process.
The primary purpose of DRC is to identify and flag any potential design rule violations that could lead to manufacturing issues or device malfunctions. By running DRC, designers can catch and rectify these issues early in the design process, saving time and resources that would otherwise be wasted on fabricating faulty designs.
Key Aspects of DRC
-
Design Rules: The foundation of DRC lies in the design rules set by the semiconductor foundry. These rules define the minimum feature sizes, spacing requirements, and other geometric constraints that must be adhered to for successful fabrication.
-
Layout Verification: DRC tools analyze the physical layout of an IC, checking each layer and the interactions between layers to ensure compliance with the design rules.
-
Error Reporting: When DRC detects a design rule violation, it generates an error report that pinpoints the location and nature of the violation. This allows designers to quickly identify and address the issues.
-
Iterative Process: DRC is typically run multiple times throughout the design process, as the layout undergoes refinements and modifications. It is crucial to ensure that the final layout is free of any design rule violations before proceeding to fabrication.
Why is DRC Important?
DRC plays a vital role in the IC design process for several reasons:
-
Manufacturing Yield: By ensuring that the layout adheres to the design rules, DRC helps to maximize the manufacturing yield. Violations of design rules can lead to defects during fabrication, resulting in non-functional or subpar devices.
-
Reliability: Adherence to design rules contributes to the overall reliability of the manufactured ICs. Proper spacing, feature sizes, and other geometric constraints help to prevent issues such as short circuits, open circuits, and signal integrity problems.
-
Time and Cost Savings: Catching design rule violations early in the design process saves time and costs associated with fabricating faulty designs. It is far more efficient to identify and fix issues at the design stage rather than discovering them after manufacturing.
-
Design Optimization: DRC can provide insights into areas where the layout can be optimized for better performance, power efficiency, or area utilization. By analyzing the layout and identifying potential improvements, designers can refine their designs for optimal results.
DRC Process Flow
The DRC process typically follows these steps:
-
Design Rule Definition: The semiconductor foundry provides a set of design rules that define the geometric constraints and requirements for the specific manufacturing process.
-
Layout Design: The IC layout is created using electronic design automation (EDA) tools, such as layout editors or place-and-route tools.
-
DRC Setup: The DRC tool is configured with the appropriate design rules and settings specific to the manufacturing process and the design requirements.
-
DRC Execution: The DRC tool analyzes the layout, checking each layer and the interactions between layers for any design rule violations. This process can be time-consuming, especially for large and complex designs.
-
Error Reporting: If the DRC tool detects any design rule violations, it generates an error report that lists the specific violations and their locations within the layout.
-
Layout Modification: Based on the error report, designers modify the layout to resolve the design rule violations. This may involve adjusting the placement of components, modifying the routing, or resizing certain features.
-
Iterative DRC: After making the necessary modifications, the DRC process is repeated to ensure that the changes have not introduced any new violations. This iterative process continues until the layout is free of design rule violations.
-
DRC Sign-off: Once the layout passes the DRC without any violations, it is considered ready for the next stages of the design process, such as layout versus schematic (LVS) checks and extraction.
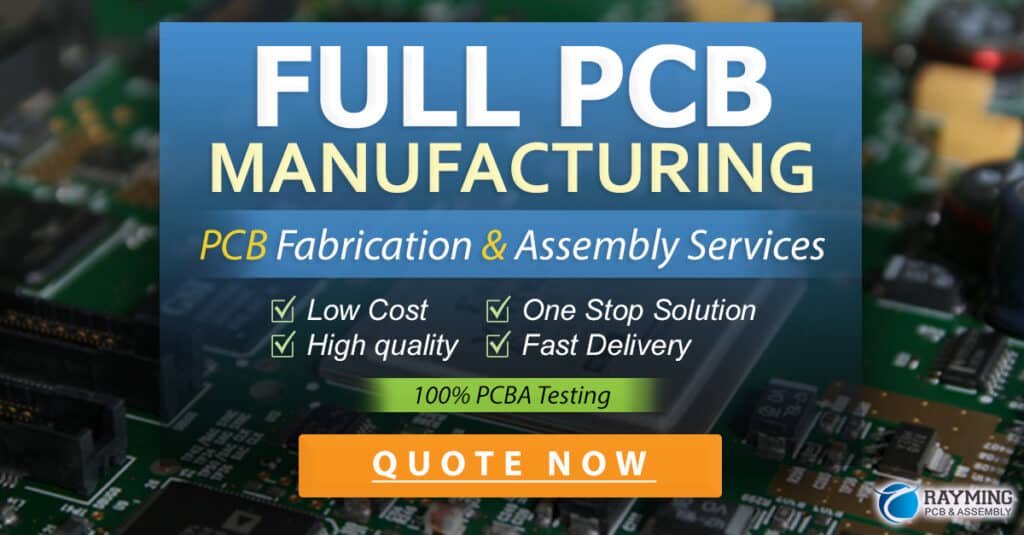
Common Design Rule Categories
Design rules can be categorized into several key areas:
-
Minimum Feature Size: This defines the smallest allowable dimensions for various features in the layout, such as transistor gate lengths, wire widths, and contact sizes.
-
Spacing Rules: These rules specify the minimum distances required between different features in the layout. For example, the spacing between adjacent wires, the distance between a wire and a transistor gate, or the spacing between contacts.
-
Enclosure Rules: Enclosure rules define the minimum amount of overlap required between different layers in the layout. This ensures proper connectivity and helps to prevent issues like open circuits.
-
Density Rules: Density rules specify the minimum and maximum densities allowed for certain features in the layout. This helps to ensure uniform distribution and prevent manufacturing issues related to uneven etching or planarization.
-
Antenna Rules: Antenna rules are designed to prevent damage to transistor gates during the fabrication process. They limit the maximum allowable ratio between the metal interconnect area and the transistor gate area.
-
Electrical Rules: Electrical rules take into account the electrical characteristics of the design, such as maximum current density, electromigration limits, and IR drop constraints.
Here’s an example table summarizing some common design rule categories:
Design Rule Category | Description |
---|---|
Minimum Feature Size | Defines the smallest allowable dimensions for features |
Spacing Rules | Specifies minimum distances between features |
Enclosure Rules | Defines minimum overlap required between layers |
Density Rules | Specifies minimum and maximum feature densities |
Antenna Rules | Limits the ratio between metal interconnect and transistor gate areas |
Electrical Rules | Considers electrical characteristics like current density and IR drop |
DRC Tools and Methodologies
There are several DRC tools and methodologies used in the industry:
-
Commercial DRC Tools: Many EDA vendors offer commercial DRC tools as part of their IC design software suites. These tools are highly optimized and provide comprehensive rule decks for various manufacturing processes. Examples include Cadence Pegasus, Synopsys IC Validator, and Mentor Graphics Calibre.
-
Foundry-Provided DRC: Semiconductor foundries often provide their own DRC rule decks and tools tailored to their specific manufacturing processes. These rule decks ensure that the designs are compatible with the foundry’s fabrication capabilities.
-
Hierarchical DRC: Hierarchical DRC is a technique used to manage the complexity of large designs. Instead of running DRC on the entire layout at once, the layout is divided into smaller hierarchical blocks, and DRC is performed on each block separately. This approach can significantly reduce DRC runtime and memory usage.
-
Multi-Threading and Distributed DRC: Modern DRC tools leverage multi-threading and distributed computing to accelerate the DRC process. By utilizing multiple CPU cores or distributing the workload across multiple machines, DRC runtime can be significantly reduced.
-
Incremental DRC: Incremental DRC is a technique that focuses on running DRC only on the modified portions of the layout, rather than the entire design. This approach saves time by avoiding redundant checks on unchanged areas.
Best Practices for DRC
To ensure a smooth and efficient DRC process, consider the following best practices:
-
Early DRC Runs: Perform DRC checks early and frequently throughout the design process. This allows for early detection and correction of design rule violations, saving time and effort in the long run.
-
Hierarchical Design: Use a hierarchical design approach to manage the complexity of large designs. This enables more efficient DRC runs and helps to localize the scope of violations.
-
Parameterized Layout: Utilize parameterized layout techniques to create reusable and scalable layout blocks. This promotes design consistency and reduces the likelihood of introducing design rule violations.
-
DRC-Aware Layout: Incorporate DRC considerations into the layout process itself. By being mindful of design rules while creating the layout, designers can proactively avoid violations and reduce the number of DRC iterations required.
-
Continuous Integration: Integrate DRC into the continuous integration and continuous delivery (CI/CD) flow. Automate DRC checks as part of the design validation process to ensure that changes to the layout do not introduce new violations.
-
Collaboration and Communication: Foster collaboration and communication between the design team, the DRC team, and the foundry. Regular discussions and feedback loops can help to clarify design rule requirements, resolve ambiguities, and streamline the DRC process.
FAQ
What happens if a layout fails DRC?
If a layout fails DRC, it means that there are design rule violations present in the layout. The DRC tool will generate an error report that lists the specific violations and their locations within the layout. Designers must then modify the layout to resolve these violations before the design can proceed to the next stages of the IC design flow.
How long does DRC take to run?
The runtime of DRC depends on various factors, such as the complexity of the design, the number of layers, the size of the layout, and the computing resources available. For large and complex designs, DRC can take several hours or even days to complete. However, the use of hierarchical DRC, multi-threading, and distributed computing can significantly reduce the DRC runtime.
Can DRC guarantee a manufacturable layout?
While DRC is an essential step in ensuring the manufacturability of a layout, it is not a guarantee. DRC checks the layout against a set of predefined design rules, but there may be other factors that can affect manufacturability, such as process variations, yield issues, or unforeseen interactions between layout features. Therefore, it is important to consider DRC as one of several verification steps in the overall IC design flow.
How often should DRC be run during the design process?
DRC should be run frequently throughout the design process, especially after significant changes or modifications to the layout. It is recommended to perform DRC checks early and often to catch and resolve design rule violations as soon as possible. This iterative approach helps to minimize the accumulation of violations and reduces the overall design cycle time.
Can DRC be customized for specific design requirements?
Yes, DRC can be customized to accommodate specific design requirements or constraints. Foundries often provide baseline design rule decks, but these can be modified or extended to include additional rules specific to a particular design or application. However, any customization of DRC rules should be done in consultation with the foundry to ensure compatibility with their manufacturing process.
Conclusion
Design Rule Check (DRC) is a critical step in the integrated circuit design process that ensures the layout of an IC adheres to the manufacturing process’s design rules. By identifying and flagging potential design rule violations early in the design cycle, DRC helps to maximize manufacturing yield, improve reliability, save time and costs, and optimize the overall design.
Understanding the key aspects of DRC, such as design rules, layout verification, error reporting, and the iterative nature of the process, is essential for IC designers. Familiarity with common design rule categories, DRC tools, and methodologies, as well as best practices for efficient DRC execution, can greatly streamline the design process and minimize the risk of manufacturability issues.
As the complexity of IC designs continues to grow and manufacturing processes become more advanced, the role of DRC in ensuring the success of IC fabrication remains paramount. By leveraging the power of DRC and following best practices, designers can create robust, reliable, and manufacturable ICs that meet the ever-increasing demands of the electronics industry.
No responses yet