Understanding Military-grade PCB Requirements
Military-grade PCBs are designed to withstand extreme conditions, such as high temperatures, vibrations, shocks, and exposure to moisture and chemicals. These circuit boards must comply with strict military standards, such as MIL-PRF-31032, MIL-PRF-55110, and MIL-STD-810, which outline the requirements for materials, manufacturing processes, and testing procedures.
Key Military PCB Standards
Standard | Description |
---|---|
MIL-PRF-31032 | Defines the performance specifications for rigid printed wiring boards |
MIL-PRF-55110 | Outlines the requirements for flexible and rigid-flex printed wiring boards |
MIL-STD-810 | Establishes the environmental engineering considerations and laboratory tests for military equipment |
Factor 1: Material Selection
Choosing the right materials is crucial for designing a military-grade PCB. The substrate material must have excellent thermal stability, mechanical strength, and chemical resistance. Some of the most commonly used materials for military PCBs include:
- FR-4: A glass-reinforced epoxy laminate with good mechanical and electrical properties
- Polyimide: A high-temperature, flexible material with excellent chemical resistance
- PTFE (Teflon): A low-dielectric constant material with superior high-frequency performance
Comparison of PCB Substrate Materials
Material | Thermal Stability | Mechanical Strength | Chemical Resistance |
---|---|---|---|
FR-4 | Good | Good | Good |
Polyimide | Excellent | Good | Excellent |
PTFE | Excellent | Fair | Excellent |
Factor 2: Copper Thickness and Trace Width
The copper thickness and trace width of a military-grade PCB must be carefully designed to ensure optimal signal integrity and power handling capabilities. Thicker copper layers and wider traces can help reduce resistance and improve current carrying capacity, which is essential for high-power applications.
Recommended Copper Thickness and Trace Width
PCB Layer | Copper Thickness | Minimum Trace Width |
---|---|---|
Signal | 1 oz (35 μm) | 0.006″ (0.15 mm) |
Power | 2 oz (70 μm) | 0.010″ (0.25 mm) |
Ground | 2 oz (70 μm) | 0.010″ (0.25 mm) |
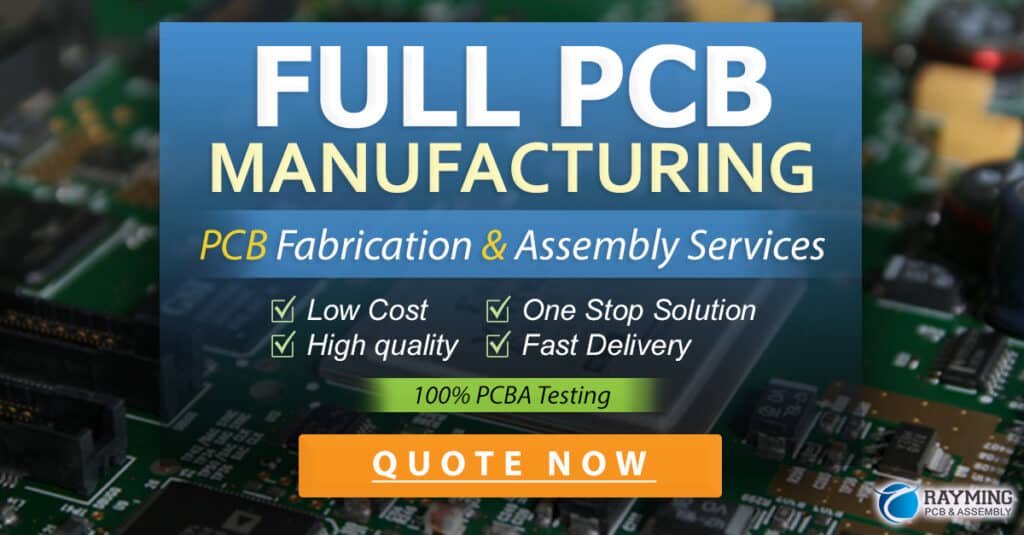
Factor 3: Soldermask and Silkscreen
A high-quality soldermask and silkscreen are essential for protecting the PCB from environmental factors and providing clear component labeling. The soldermask must have excellent adhesion, chemical resistance, and high-temperature stability. The silkscreen should be legible and durable, even after exposure to harsh conditions.
Factor 4: Via and Hole Plating
Vias and holes in a military-grade PCB must be properly plated to ensure reliable electrical connections and mechanical strength. The plating material should have excellent adhesion, thermal stability, and resistance to corrosion. Some common plating materials include:
- Copper: Provides good electrical conductivity and mechanical strength
- Gold: Offers excellent corrosion resistance and conductivity for high-reliability applications
- Silver: Has the highest electrical conductivity but is prone to tarnishing
Factor 5: Controlled Impedance
Designing controlled impedance traces is crucial for maintaining signal integrity in high-speed military PCBs. The characteristic impedance of a trace depends on factors such as the substrate material, copper thickness, trace width, and spacing between traces. Proper impedance matching helps minimize signal reflections and distortions, ensuring reliable data transmission.
Factor 6: Thermal Management
Military-grade PCBs often operate in high-temperature environments, making thermal management a critical design consideration. Proper thermal management helps prevent component failure and ensures reliable operation. Some techniques for improving thermal management include:
- Using high-thermal conductivity substrate materials
- Incorporating thermal vias and heat sinks
- Optimizing component placement and spacing
Factor 7: EMI/EMC Shielding
Electromagnetic interference (EMI) and electromagnetic compatibility (EMC) are significant concerns for military PCBs. Proper shielding helps prevent interference from external sources and ensures that the PCB does not emit excessive electromagnetic radiation. Some common EMI/EMC shielding techniques include:
- Incorporating ground planes and guard traces
- Using shielded enclosures and connectors
- Implementing proper grounding and filtering techniques
Frequently Asked Questions (FAQ)
1. What is the difference between a military-grade PCB and a commercial-grade PCB?
Military-grade PCBs are designed to withstand extreme environmental conditions and comply with strict military standards, while commercial-grade PCBs are designed for less demanding applications and may not have the same level of durability and reliability.
2. Can I use a commercial-grade PCB in a military application?
While it is possible to use a commercial-grade PCB in a military application, it is not recommended. Commercial-grade PCBs may not meet the stringent requirements for military equipment and could lead to system failures or reduced performance.
3. How do I choose the right substrate material for my military-grade PCB?
The choice of substrate material depends on the specific requirements of your application, such as operating temperature, mechanical stress, and chemical exposure. Consult with a PCB design expert or refer to military standards to select the most appropriate material for your project.
4. What is the importance of controlled impedance in military PCB design?
Controlled impedance is critical for maintaining signal integrity in high-speed military PCBs. Proper impedance matching helps minimize signal reflections and distortions, ensuring reliable data transmission and preventing system failures.
5. How can I ensure that my military-grade PCB meets the necessary EMI/EMC requirements?
To ensure that your military-grade PCB meets EMI/EMC requirements, incorporate proper shielding techniques such as ground planes, guard traces, shielded enclosures, and connectors. Additionally, implement appropriate grounding and filtering techniques to minimize electromagnetic interference.
Designing a military-grade PCB requires careful consideration of various factors, from material selection and copper thickness to thermal management and EMI/EMC shielding. By understanding and addressing these critical aspects, you can create a high-quality, reliable, and durable PCB that meets the demanding requirements of military applications.
No responses yet