Introduction to Millimeter-Wave PCB Design
Millimeter-wave (mm-wave) frequencies, typically defined as the range from 30 GHz to 300 GHz, have gained significant attention in recent years due to their potential for high-speed wireless communication, radar, and imaging applications. Designing printed circuit boards (PCBs) for mm-wave frequencies presents unique challenges compared to lower frequency designs. This article explores the design considerations for microstrip, coplanar, and stripline structures when working with mm-wave frequencies.
Fundamentals of mm-Wave PCB Design
Wavelength and PCB Dimensions
At mm-wave frequencies, the wavelengths become extremely small, necessitating careful consideration of PCB dimensions. The wavelength (λ) can be calculated using the following equation:
λ = c / (f * √(εr))
Where:
– c is the speed of light in vacuum (approximately 3 x 10^8 m/s)
– f is the frequency in Hz
– εr is the relative permittivity (dielectric constant) of the substrate material
For example, at a frequency of 60 GHz and using a substrate with a relative permittivity of 4, the wavelength is approximately 2.5 mm.
Substrate Material Selection
The choice of substrate material is crucial for mm-wave PCB design. The substrate should have low dielectric loss, low moisture absorption, and stable properties over temperature variations. Some commonly used substrate materials for mm-wave applications include:
Material | Dielectric Constant (εr) | Loss Tangent (tan δ) |
---|---|---|
Rogers RO3003 | 3.0 | 0.0013 |
Rogers RO4003C | 3.38 | 0.0027 |
Rogers RT/duroid 5880 | 2.2 | 0.0009 |
Teflon (PTFE) | 2.1 | 0.0002 |
Skin Effect and Surface Roughness
At mm-wave frequencies, the skin effect becomes more pronounced, resulting in current flow being confined to a thin layer near the surface of the conductor. The skin depth (δ) can be calculated using the following equation:
δ = √(ρ / (π * f * μ))
Where:
– ρ is the resistivity of the conductor material
– f is the frequency in Hz
– μ is the permeability of the conductor material
Surface roughness of the conductor can also impact the performance at mm-wave frequencies. Rough surfaces can increase conductor losses and cause signal integrity issues. Therefore, it is essential to use smooth conductor surfaces and consider the skin effect when designing mm-wave PCBs.
Microstrip Structures
Microstrip is a popular transmission line structure for mm-wave PCB design due to its simplicity and ease of fabrication. It consists of a conducting strip separated from a ground plane by a dielectric substrate.
Characteristic Impedance
The characteristic impedance (Z0) of a microstrip line can be calculated using the following equations:
For W/H ≤ 1:
Z0 = (60 / √εe) * ln(8H / W + W / (4H))
For W/H > 1:
Z0 = (120π / √εe) / (W/H + 1.393 + 0.667 * ln(W/H + 1.444))
Where:
– W is the width of the microstrip line
– H is the thickness of the dielectric substrate
– εe is the effective dielectric constant
Dielectric and Conductor Losses
Dielectric losses in microstrip lines can be minimized by using low-loss substrate materials. Conductor losses can be reduced by using wider microstrip lines and thicker conductors. However, increasing the line width may result in higher radiation losses at mm-wave frequencies.
Discontinuities and Transitions
Discontinuities in microstrip lines, such as bends, junctions, and transitions, can cause reflections and degrade signal integrity at mm-wave frequencies. Careful design and optimization of these discontinuities are necessary to minimize their impact. Smooth transitions, such as tapered lines or radial bends, can help reduce reflections.
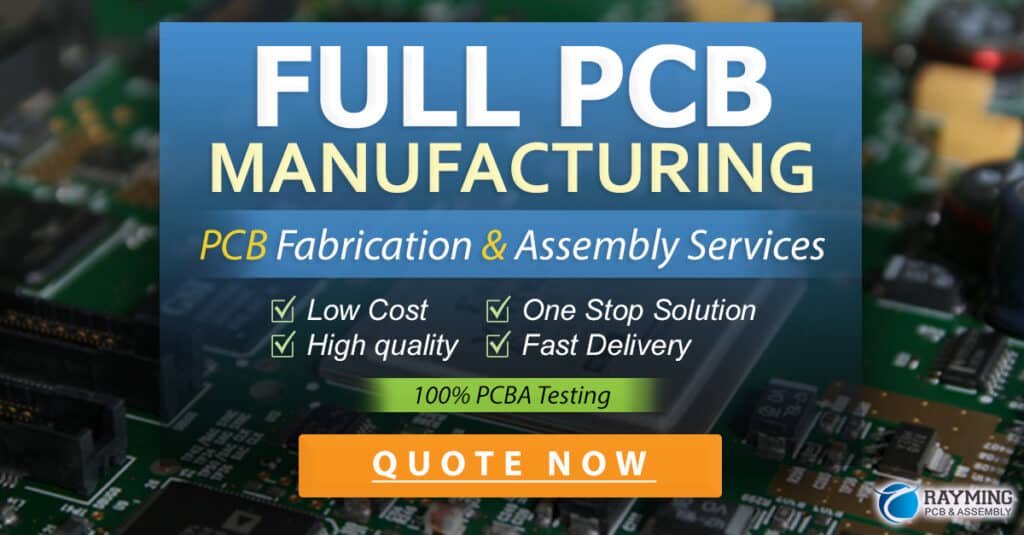
Coplanar Structures
Coplanar waveguide (CPW) and coplanar stripline (CPS) are alternative transmission line structures for mm-wave PCB design. They offer several advantages over microstrip, including lower dispersion, easier integration with active devices, and better isolation between adjacent lines.
Coplanar Waveguide (CPW)
CPW consists of a center conductor with ground planes on either side, all on the same plane. The characteristic impedance of a CPW can be calculated using the following equations:
For W/S ≤ 1:
Z0 = (30π / √εe) * K(k) / K(k’)
For W/S > 1:
Z0 = (60π / √εe) * K(k’) / K(k)
Where:
– W is the width of the center conductor
– S is the gap between the center conductor and ground planes
– K(k) and K(k’) are elliptic integrals
– k = S / (S + 2W)
– k’ = √(1 – k^2)
Coplanar Stripline (CPS)
CPS is similar to CPW but without ground planes. It consists of two parallel conductors on the same plane. The characteristic impedance of a CPS can be calculated using the same equations as CPW, with S representing the gap between the two conductors.
Mode Suppression and Grounding
One challenge with coplanar structures is the potential for unwanted modes, such as the coupled slotline mode in CPW. To suppress these modes, periodic grounding techniques, such as air bridges or via fences, can be used. Proper grounding is essential to maintain signal integrity and prevent mode conversion.
Stripline Structures
Stripline is another transmission line structure suitable for mm-wave PCB design. It consists of a conductor strip sandwiched between two ground planes and embedded in a dielectric substrate. Stripline offers excellent isolation and low radiation losses.
Characteristic Impedance
The characteristic impedance of a stripline can be calculated using the following equation:
Z0 = (60 / √εr) * ln(4H / (0.67πW * (1 – r^2)))
Where:
– W is the width of the stripline conductor
– H is the distance between the ground planes
– εr is the relative permittivity of the substrate
– r is the ratio of the conductor thickness to the substrate thickness (r = T / H)
Dielectric and Conductor Losses
Stripline structures have lower dielectric losses compared to microstrip due to the confinement of the electric field within the substrate. Conductor losses can be minimized by using wider stripline conductors and selecting low-loss substrate materials.
Transitions and Multilayer Structures
Transitions from stripline to other structures, such as microstrip or coplanar waveguide, require careful design to minimize discontinuities and reflections. Multilayer stripline structures can be used to increase circuit density and implement complex routing. However, proper grounding and via placement are crucial to maintain signal integrity.
Simulation and Optimization
Simulating and optimizing mm-wave PCB designs is essential to ensure proper performance and minimize losses. Electromagnetic (EM) simulation tools, such as Ansys HFSS, CST Studio Suite, or Keysight ADS, can be used to model and analyze the structures. These tools allow for the optimization of dimensions, materials, and transitions to achieve the desired performance.
Manufacturing Considerations
Manufacturing mm-wave PCBs requires tight tolerances and specialized fabrication processes. Some key considerations include:
- Choosing a fabrication vendor with experience in mm-wave PCB manufacturing
- Specifying tight tolerances for line widths, gaps, and substrate thickness
- Using smooth copper surfaces to minimize conductor losses
- Ensuring proper plating and surface finish to maintain signal integrity
- Implementing controlled impedance techniques during fabrication
Frequently Asked Questions (FAQ)
1. What are the main challenges in designing PCBs for mm-wave frequencies?
The main challenges in designing PCBs for mm-wave frequencies include:
– Small wavelengths requiring precise dimensions and tight tolerances
– Increased dielectric and conductor losses
– Potential for unwanted modes and radiation losses
– Difficulty in maintaining signal integrity due to discontinuities and transitions
2. Which substrate materials are commonly used for mm-wave PCB design?
Commonly used substrate materials for mm-wave PCB design include:
– Rogers RO3003
– Rogers RO4003C
– Rogers RT/duroid 5880
– Teflon (PTFE)
These materials have low dielectric loss, low moisture absorption, and stable properties over temperature variations.
3. How does the skin effect impact mm-wave PCB design?
At mm-wave frequencies, the skin effect becomes more pronounced, causing current to flow in a thin layer near the surface of the conductor. This leads to increased conductor losses and requires the use of smooth conductor surfaces and consideration of the skin depth when designing mm-wave PCBs.
4. What are the advantages of coplanar structures (CPW and CPS) over microstrip for mm-wave PCB design?
Coplanar structures, such as CPW and CPS, offer several advantages over microstrip for mm-wave PCB design:
– Lower dispersion
– Easier integration with active devices
– Better isolation between adjacent lines
– Ability to implement periodic grounding techniques for mode suppression
5. Why is simulation and optimization important for mm-wave PCB design?
Simulation and optimization are crucial for mm-wave PCB design to ensure proper performance and minimize losses. Electromagnetic (EM) simulation tools allow for the modeling and analysis of structures, enabling the optimization of dimensions, materials, and transitions to achieve the desired performance before fabrication.
Conclusion
Designing PCBs for mm-wave frequencies presents unique challenges due to the small wavelengths, increased losses, and potential for signal integrity issues. Understanding the design considerations for microstrip, coplanar, and stripline structures is essential for successful mm-wave PCB design. Careful selection of substrate materials, consideration of the skin effect and surface roughness, and proper design of discontinuities and transitions are crucial. Simulation and optimization tools play a vital role in ensuring the desired performance of mm-wave PCBs. By following these design guidelines and working with experienced fabrication vendors, designers can successfully implement high-performance mm-wave PCBs for various applications.
No responses yet