What is Defined Impedance?
Defined impedance, also known as controlled impedance or specified impedance, refers to the precise control and matching of impedance values in electrical transmission lines, circuit boards, connectors, and cabling systems. Impedance, measured in ohms (Ω), is the total opposition a circuit presents to alternating current (AC) at a given frequency. It consists of resistance and reactance.
In high-speed digital systems and radio frequency (RF) applications, it is crucial to maintain consistent impedance across interconnections to ensure optimal signal integrity, minimize reflections, and reduce electromagnetic interference (EMI). Defined impedance is achieved through careful design and manufacturing techniques that tightly control the physical dimensions and materials of the conducting traces and dielectrIC Substrates.
Common Defined Impedance Values
The most common defined impedance values used in various applications are:
Impedance (Ω) | Application |
---|---|
50 | Coaxial cables, RF systems, telecommunications |
75 | Video transmission, CATV, satellite communication |
90 | Differential signaling (e.g., LVDS, PECL) |
100 | Ethernet (10BASE-T, 100BASE-TX), twisted pair cables |
110 | Twisted pair cables for telephony and data communication |
120 | Differential signaling (e.g., USB, HDMI, DisplayPort) |
These values have been standardized to ensure compatibility and optimal performance across different systems and components.
Factors Affecting Defined Impedance
Several factors influence the impedance of a transmission line or interconnect:
-
Conductor geometry: The width, thickness, and spacing of the conducting traces impact the impedance. Wider traces generally result in lower impedance, while narrower traces yield higher impedance.
-
Dielectric constant: The dielectric constant (Dk) of the insulating substrate material affects the impedance. Higher Dk values result in lower impedance, while lower Dk values lead to higher impedance.
-
Dielectric thickness: The thickness of the dielectric layer between the conductor and the reference plane (e.g., ground or power plane) influences the impedance. Thicker dielectrics increase impedance, while thinner dielectrics decrease it.
-
Frequency: Impedance is frequency-dependent due to the reactive components (capacitance and inductance) of the transmission line. As frequency increases, the effect of these reactive components becomes more pronounced.
-
Surrounding environment: The presence of nearby conductors, Ground Planes, or other components can affect the impedance through electromagnetic coupling and parasitic effects.
Impedance Control in PCB Design
Printed circuit board (PCB) designers must carefully consider and control impedance to ensure proper signal integrity and electromagnetic compatibility (EMC). This involves:
-
Stack-up design: Selecting appropriate layer arrangements, dielectric materials, and thicknesses to achieve the desired impedance.
-
Trace width and spacing: Calculating and adjusting trace widths and spacing based on the target impedance, dielectric constant, and thickness.
-
Reference planes: Providing uninterrupted reference planes (ground or power) beneath or adjacent to the signal traces to maintain consistent impedance.
-
Termination: Using proper termination techniques, such as matched resistors or source termination, to minimize reflections and maintain signal integrity.
-
Simulation and modeling: Employing electromagnetic simulation tools and mathematical models to predict and optimize impedance behavior.
Impedance Matching
Impedance matching is the practice of designing the impedance of the source, transmission line, and load to be equal to minimize signal reflections and power loss. When impedances are mismatched, a portion of the signal energy is reflected back to the source, leading to signal distortion, reduced power transfer efficiency, and potential EMI issues.
Reflection Coefficient and Return Loss
The reflection coefficient (Γ) quantifies the amount of signal reflection at an impedance mismatch:
Γ = (ZL – Z0) / (ZL + Z0)
Where:
– ZL is the load impedance
– Z0 is the characteristic impedance of the transmission line
A reflection coefficient of 0 indicates a perfect match, while a value of 1 or -1 represents total reflection.
Return loss (RL), expressed in decibels (dB), is a measure of the reflected power relative to the incident power:
RL = -20 log10(|Γ|)
Higher return loss values indicate better impedance matching and less reflected power.
Impedance Matching Techniques
Several techniques can be employed to achieve impedance matching:
-
Series and shunt matching: Adding series or shunt reactive components (inductors or capacitors) to transform the load impedance to match the source impedance.
-
Quarter-wave transformers: Using transmission line sections with a specific characteristic impedance and length (quarter-wavelength at the operating frequency) to transform the load impedance.
-
Tapered lines: Gradually changing the impedance along the length of the transmission line to provide a smooth transition between mismatched impedances.
-
Impedance matching networks: Designing networks of reactive components (e.g., L-networks, Pi-networks, T-networks) to match complex impedances over a specific frequency range.
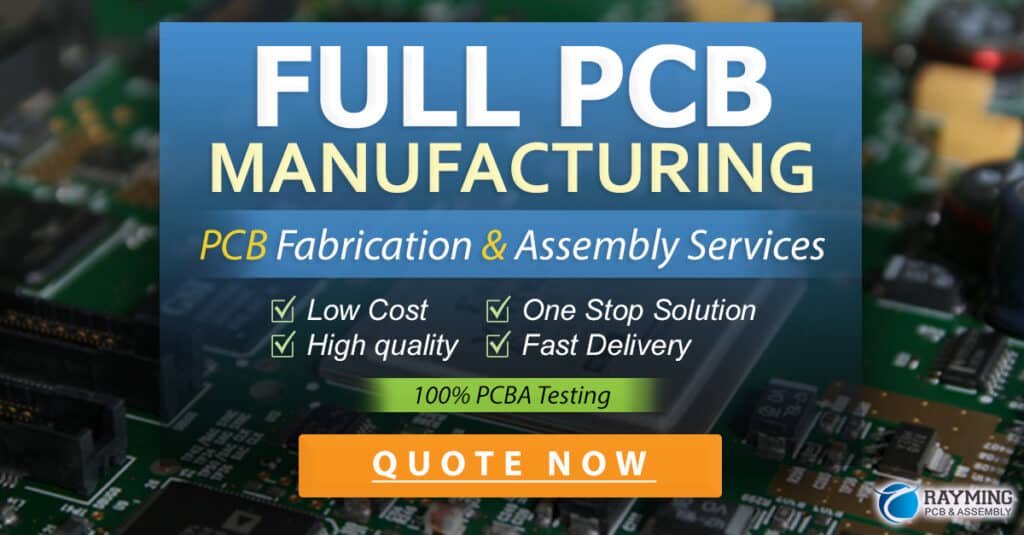
Testing and Measurement
Verifying and validating defined impedance in manufactured products is essential to ensure compliance with design specifications and performance requirements. Various techniques and instruments are used for impedance testing and measurement:
-
Time Domain Reflectometry (TDR): TDR measures impedance by sending a fast-rising pulse down the transmission line and analyzing the reflected signal. It provides a graphical representation of impedance variations along the line.
-
Vector Network Analyzer (VNA): VNAs measure the complex impedance, return loss, and insertion loss of a device under test (DUT) over a wide frequency range. They provide accurate and detailed impedance information.
-
Impedance Analyzers: Impedance analyzers are specialized instruments that directly measure the complex impedance of a component or network at specific frequencies.
-
Spectrometers: High-frequency spectrometers can be used to measure the frequency-dependent impedance of materials and substrates.
-
Simulation and Modeling: Electromagnetic simulation software and mathematical models can predict and analyze impedance behavior, helping to validate designs before physical testing.
Applications
Defined impedance is crucial in various applications where signal integrity, power efficiency, and electromagnetic compatibility are critical:
-
High-speed digital systems: Controlled impedance is essential in high-speed digital circuits, such as memory interfaces (DDR), serial communication (USB, PCIe), and networking (Ethernet).
-
RF and wireless communication: Impedance matching is vital in RF systems, including antennas, filters, amplifiers, and transmitters, to maximize power transfer and minimize signal reflections.
-
Aerospace and defense: Defined impedance is critical in aerospace and defense applications, where reliable and robust signal transmission is paramount, such as radar systems, avionics, and satellite communication.
-
Automotive: As vehicles incorporate more advanced electronics and communication systems, defined impedance becomes increasingly important for ensuring reliable and interference-free operation.
-
Medical devices: Controlled impedance is essential in medical devices that rely on precise signal transmission and reception, such as imaging systems, patient monitoring equipment, and implantable devices.
FAQ
-
What is the difference between impedance and resistance?
Resistance is the opposition to the flow of direct current (DC), while impedance is the total opposition to the flow of alternating current (AC). Impedance consists of both resistance and reactance (capacitive and inductive components). -
Why is 50Ω a common impedance value in RF systems?
50Ω has become a standard impedance value in RF systems because it provides a good compromise between power handling capability and signal loss. It also allows for the use of readily available connectors, cables, and components designed for 50Ω systems. -
How does the dielectric constant affect impedance?
The dielectric constant (Dk) of the insulating material influences the impedance of a transmission line. A higher Dk value results in a lower impedance, as it increases the capacitance between the conductor and the reference plane. Conversely, a lower Dk value leads to a higher impedance. -
What is the importance of impedance matching in RF systems?
Impedance matching is crucial in RF systems to maximize power transfer, minimize signal reflections, and reduce power loss. When impedances are mismatched, a portion of the signal energy is reflected back to the source, leading to signal distortion, reduced efficiency, and potential EMI issues. -
How can I measure the impedance of a PCB trace?
Time Domain Reflectometry (TDR) is a common method for measuring the impedance of PCB Traces. TDR sends a fast-rising pulse down the trace and analyzes the reflected signal to determine the impedance variations along the length of the trace. Other methods include using a Vector Network Analyzer (VNA) or an impedance analyzer.
No responses yet