Understanding DC Motor Speed Control
Before diving into the various speed control methods, it is crucial to understand the basics of DC motor speed control. The speed of a DC motor is directly proportional to the voltage applied to its armature. By varying the voltage, we can effectively control the motor’s speed. There are two primary approaches to DC motor speed control:
-
Voltage Control: This method involves varying the voltage supplied to the motor’s armature to control its speed. It can be achieved through techniques such as pulse-width modulation (PWM) or using a variable voltage source.
-
Current Control: In this approach, the current flowing through the motor’s armature is regulated to control the speed. Current control is often employed in applications that require precise speed regulation under varying load conditions.
Pulse-Width Modulation (PWM) for DC Motor Speed Control
Pulse-width modulation (PWM) is a popular technique for controlling the speed of DC motors. It involves generating a square wave signal with a variable duty cycle to adjust the average voltage supplied to the motor. By varying the duty cycle, we can effectively control the motor’s speed.
PWM Speed Control Circuit
Here’s a simple PWM-based DC motor speed control circuit:
+12V
|
|
+-+
| |
| | R1
| | 10k
+-+
|
|
+----+
| |
| |
+-+ +-+
| | | |
| | | | R2
| | | | 1k
+-+ +-+
| |
| |
+----+
|
|
+-+
| |
| | Q1
| | BJT (e.g., 2N2222)
+-+
|
|
+-+
| |
| | Motor
| |
+-+
|
|
GND
In this circuit:
– R1 is a potentiometer that controls the duty cycle of the PWM signal.
– R2 is a current-limiting resistor for the BJT transistor (Q1).
– Q1 acts as a switch, turning on and off rapidly based on the PWM signal.
– The motor is connected to the collector of Q1 and ground.
By adjusting the potentiometer (R1), we can vary the duty cycle of the PWM signal, which in turn controls the average voltage supplied to the motor, thus regulating its speed.
Advantages of PWM Speed Control
- Simple and cost-effective implementation
- Efficient power utilization
- Wide speed range control
- Smooth speed regulation
Disadvantages of PWM Speed Control
- May introduce electromagnetic interference (EMI) due to high-frequency switching
- Requires additional filtering components to minimize EMI
Variable Voltage Speed Control
Another approach to DC motor speed control is by using a variable voltage source. By adjusting the voltage supplied to the motor’s armature, we can directly control its speed. This method is straightforward and easy to implement.
Variable Voltage Speed Control Circuit
Here’s a basic variable voltage speed control circuit:
+12V
|
|
+-+
| |
| | R1
| | 10k
+-+
|
|
+----+
| |
| |
+-+ +-+
| | | |
| | | | R2
| | | | 1k
+-+ +-+
| |
| |
+----+
|
|
+-+
| |
| | Q1
| | Power MOSFET (e.g., IRF540)
+-+
|
|
+-+
| |
| | Motor
| |
+-+
|
|
GND
In this circuit:
– R1 is a potentiometer that controls the voltage supplied to the motor.
– R2 is a current-limiting resistor for the MOSFET transistor (Q1).
– Q1 acts as a variable resistor, regulating the voltage across the motor based on the potentiometer setting.
– The motor is connected to the drain of Q1 and ground.
By adjusting the potentiometer (R1), we can vary the voltage supplied to the motor, thereby controlling its speed.
Advantages of Variable Voltage Speed Control
- Simple and straightforward implementation
- Smooth speed control
- Suitable for applications with consistent load conditions
Disadvantages of Variable Voltage Speed Control
- Limited speed range compared to PWM control
- Inefficient power utilization at lower speeds
- May require additional heat dissipation for the voltage-regulating component (e.g., MOSFET)
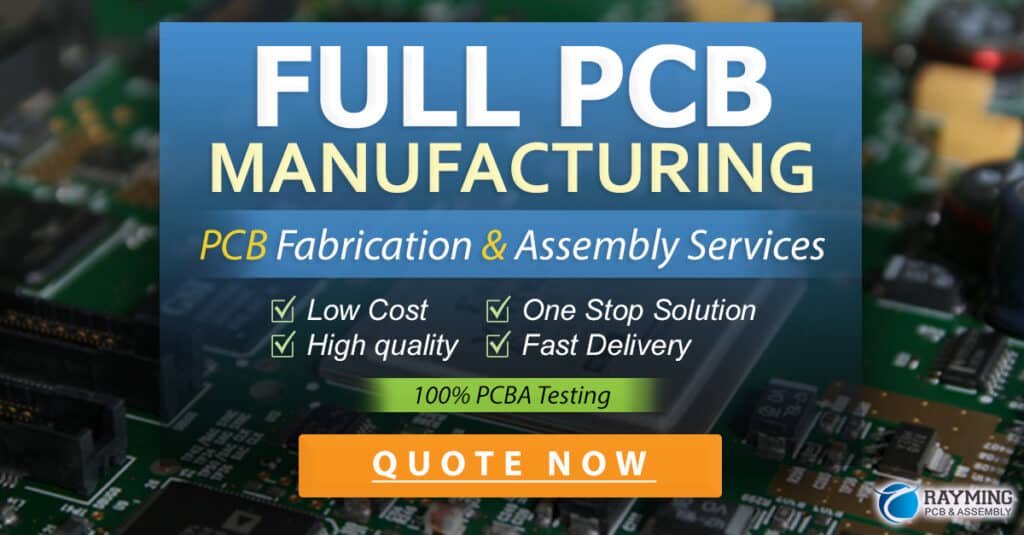
PID Control for Precise Speed Regulation
In applications that demand precise speed regulation, especially under varying load conditions, proportional-integral-derivative (PID) control can be employed. PID control continuously monitors the motor’s speed and adjusts the control signal accordingly to maintain the desired speed.
PID Control Circuit
Implementing a PID control system requires a microcontroller or a dedicated PID controller IC. Here’s a high-level block diagram of a PID-based DC motor speed control system:
+--------+
| |
| Speed |
| Sensor |
| |
+---+----+
|
|
+---+----+
| |
| PID |
|Controller|
| |
+---+----+
|
|
+---+----+
| |
| Motor |
| Driver |
| |
+---+----+
|
|
Motor
In this system:
– The speed sensor (e.g., encoder or tachometer) measures the actual speed of the motor.
– The PID controller compares the measured speed with the desired speed and generates an appropriate control signal.
– The motor driver (e.g., H-bridge or PWM driver) applies the control signal to the motor.
The PID controller continuously adjusts the control signal based on the difference between the desired and actual speeds, ensuring precise speed regulation.
Advantages of PID Control
- Precise speed regulation under varying load conditions
- Adaptability to different motor characteristics
- Suitable for applications requiring critical speed control
Disadvantages of PID Control
- Increased complexity compared to PWM or variable voltage control
- Requires tuning of PID parameters for optimal performance
- Higher implementation cost due to additional components (e.g., speed sensor, microcontroller)
Choosing the Right Speed Control Method
When selecting a DC motor speed control method, consider the following factors:
- Application Requirements:
- Speed range and resolution
- Load conditions (constant or varying)
-
Precision and stability requirements
-
Motor Characteristics:
- Rated voltage and current
- Power rating
-
Speed-torque characteristics
-
Control System Complexity:
- Available resources (e.g., microcontroller, driver ICs)
-
Development time and cost constraints
-
Efficiency and Power Consumption:
- Power dissipation in the control circuit
- Heat generation and cooling requirements
Based on these factors, choose the speed control method that best suits your application and design constraints.
Frequently Asked Questions (FAQ)
-
Q: What is the difference between open-loop and closed-loop speed control?
A: Open-loop speed control relies on predefined control signals without feedback from the motor’s actual speed. Closed-loop control, such as PID, incorporates feedback from a speed sensor to continuously adjust the control signal based on the difference between the desired and actual speeds. -
Q: Can I use a microcontroller to implement PWM speed control?
A: Yes, most microcontrollers have built-in PWM capabilities. You can generate PWM signals using the microcontroller’s timers and control the motor speed by varying the duty cycle of the PWM signal. -
Q: How do I select the appropriate components for my DC motor speed control circuit?
A: When selecting components, consider the motor’s rated voltage and current, the desired speed range, and the power dissipation requirements. Choose components with suitable ratings and ensure proper heat dissipation to prevent overheating. -
Q: Can I control multiple DC motors with a single speed control circuit?
A: Yes, you can control multiple DC motors with a single speed control circuit by using separate driver stages for each motor. However, ensure that the power supply and control circuit can handle the combined current draw of all the motors. -
Q: What are some common applications of DC motor speed control?
A: DC motor speed control is widely used in various applications, such as: - Robotics and automation
- Automotive systems (e.g., windshield wipers, fan control)
- Industrial machinery and conveyors
- Home appliances (e.g., blenders, sewing machines)
- Precision positioning systems
Conclusion
DC motor speed control is crucial for achieving precise and efficient operation in various applications. By understanding the different speed control methods, such as PWM, variable voltage control, and PID control, you can select the most suitable approach for your specific requirements. Consider factors like application demands, motor characteristics, control system complexity, and efficiency when making your choice. With the right speed control circuit and proper implementation, you can effectively regulate the speed of your DC motor and optimize its performance.
No responses yet