Why Custom Shielding Matters
Custom shielding plays a crucial role in protecting sensitive electronic components and ensuring the proper functioning of devices. Here are some key reasons why custom shielding is important:
Protection against EMI and RFI
Electromagnetic interference (EMI) and radio frequency interference (RFI) can cause significant disruptions to electronic devices, leading to malfunctions, data loss, and reduced performance. Custom shielding helps to mitigate these issues by creating a barrier that blocks or attenuates electromagnetic waves, preventing them from interfering with the device’s operation.
Compliance with Industry Standards
Many industries have specific standards and regulations regarding electromagnetic compatibility (EMC) and electromagnetic interference (EMI). Custom shielding helps companies meet these requirements by providing tailored solutions that adhere to the necessary specifications, ensuring compliance with industry standards and avoiding potential legal and financial repercussions.
Improved Device Performance
By effectively shielding electronic components from external interference, custom shielding can significantly enhance the performance of devices. This is particularly important in applications where precision and reliability are critical, such as medical equipment, aerospace systems, and telecommunications infrastructure.
Cost-effective Solutions
While off-the-shelf shielding products may be available, they often fail to address the specific needs of a given application. Custom shielding allows for the creation of cost-effective solutions that are optimized for the device’s unique requirements, reducing unnecessary expenses associated with overengineered or inadequate shielding.
Materials Used in Custom Shielding
Various materials can be used in the creation of custom shielding, each with its own properties and advantages. Some of the most common materials include:
Metals
Metals are the most widely used materials in custom shielding due to their excellent conductivity and ability to block electromagnetic waves. Some popular choices include:
- Aluminum: Lightweight, cost-effective, and easy to work with, aluminum is a common choice for custom shielding applications.
- Copper: Known for its exceptional conductivity, copper provides superior shielding performance but is more expensive than aluminum.
- Steel: Steel is often used in applications requiring structural strength in addition to shielding properties.
- Nickel: Nickel and nickel-based alloys offer good shielding performance and corrosion resistance, making them suitable for harsh environments.
Metal | Conductivity (S/m) | Shielding Effectiveness (dB) | Cost |
---|---|---|---|
Aluminum | 3.5 × 10^7 | 60-80 | Low |
Copper | 5.96 × 10^7 | 80-100 | High |
Steel | 1.0 × 10^7 | 40-60 | Medium |
Nickel | 1.43 × 10^7 | 60-80 | High |
Conductive Polymers
Conductive polymers are increasingly being used in custom shielding applications due to their lightweight nature, flexibility, and ease of processing. These materials are created by incorporating conductive fillers, such as carbon nanotubes or metal particles, into a polymer matrix. Some advantages of conductive polymers include:
- Lightweight: Conductive polymers are significantly lighter than metals, making them ideal for applications where weight is a concern.
- Flexibility: These materials can be easily molded or formed into complex shapes, allowing for greater design freedom.
- Corrosion resistance: Conductive polymers are inherently resistant to corrosion, making them suitable for use in harsh environments.
- Cost-effective: In some cases, conductive polymers can be more cost-effective than metals, especially for high-volume production.
Composite Materials
Composite materials combine the properties of multiple constituents to achieve desired shielding characteristics. These materials often consist of a polymer matrix reinforced with conductive fibers or particles, such as carbon fiber, metal-coated fibers, or metal mesh. Composite materials offer several benefits:
- Customizable properties: The properties of composite materials can be tailored by adjusting the type and amount of reinforcement used, allowing for the creation of shielding solutions that meet specific requirements.
- Multifunctional performance: Composite materials can provide shielding while also offering other desirable properties, such as structural strength, thermal insulation, or fire resistance.
- Lightweight: Compared to metals, composite materials can offer significant weight savings, which is particularly important in aerospace and automotive applications.
Techniques for Creating Custom Shielding
Several techniques are used in the creation of custom shielding, depending on the materials used and the specific application requirements. Some common techniques include:
Stamping and Forming
Stamping and forming are widely used techniques for creating custom shielding from metal sheets. This process involves using dies and presses to cut, bend, and shape the metal into the desired geometry. Stamping and forming offer several advantages:
- High production rates: Stamping and forming can produce large quantities of shielding components quickly and efficiently.
- Consistency: This technique ensures consistent quality and dimensions across multiple components.
- Cost-effective: For high-volume production, stamping and forming can be a cost-effective solution.
Injection Molding
Injection molding is a popular technique for creating custom shielding components from conductive polymers. This process involves injecting molten polymer into a mold cavity, where it cools and solidifies into the desired shape. Injection molding offers several benefits:
- Complex geometries: Injection molding allows for the creation of intricate and complex shielding components that would be difficult or impossible to achieve with other techniques.
- High production rates: Once the mold is created, injection molding can produce large quantities of shielding components quickly and efficiently.
- Consistency: Injection molding ensures consistent quality and dimensions across multiple components.
3D Printing
3D printing, also known as additive manufacturing, is an increasingly popular technique for creating custom shielding components. This process involves building up the component layer by layer using a digital model as a guide. 3D printing offers several advantages:
- Rapid prototyping: 3D printing allows for the quick creation of prototypes and proof-of-concept models, enabling faster iteration and design optimization.
- Complex geometries: Like injection molding, 3D printing can create intricate and complex shielding components that would be difficult to achieve with traditional manufacturing methods.
- Customization: 3D printing enables the creation of highly customized shielding solutions tailored to specific applications.
Applying Conductive Coatings
Applying conductive coatings to non-conductive materials is another technique for creating custom shielding. This process involves depositing a thin layer of conductive material, such as metal or conductive polymer, onto the surface of the substrate material. Some common coating methods include:
- Electroplating: This process involves depositing a metal layer onto the substrate using an electric current.
- Vapor deposition: Physical vapor deposition (PVD) and chemical vapor deposition (CVD) techniques are used to deposit thin films of conductive materials onto the substrate.
- Conductive Paints and sprays: These materials can be applied to the substrate surface using traditional painting or spraying methods, providing a conductive coating.
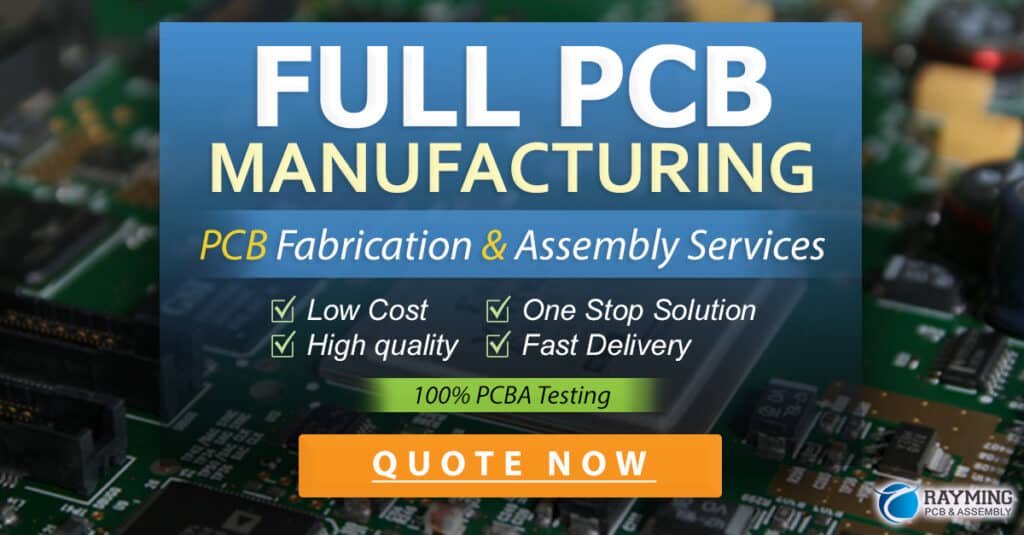
Best Practices for Implementing Custom Shielding
To ensure the effectiveness of custom shielding solutions, consider the following best practices:
Conduct a Thorough EMI/RFI Analysis
Before designing a custom shielding solution, it is crucial to conduct a thorough analysis of the electromagnetic environment in which the device will operate. This analysis should identify the sources and frequencies of EMI/RFI, as well as the potential impact on the device’s performance. This information will guide the selection of materials and design of the shielding solution.
Consider Shielding Effectiveness and Frequency Range
When selecting materials and designing custom shielding, it is essential to consider the required shielding effectiveness and the frequency range of the interference. Different materials and configurations offer varying levels of shielding effectiveness across different frequency ranges. Ensure that the chosen solution provides adequate protection for the specific application.
Optimize Shielding Geometry
The geometry of the shielding component plays a significant role in its effectiveness. When designing custom shielding, consider factors such as the size and shape of apertures, the thickness of the shielding material, and the overall coverage of the component. Optimize the geometry to minimize leakage and ensure maximum shielding performance.
Ensure Proper Grounding
Proper grounding is critical for the effectiveness of custom shielding. Ensure that the shielding component is adequately grounded to the device’s chassis or ground plane, using low-impedance connections. Improper grounding can lead to leakage and reduced shielding performance.
Test and Validate Shielding Performance
After implementing a custom shielding solution, it is crucial to test and validate its performance. Conduct EMC testing to ensure that the device meets the required industry standards and regulations. Additionally, perform functional testing to verify that the shielding does not adversely affect the device’s operation or performance.
Frequently Asked Questions
1. How do I determine the required shielding effectiveness for my application?
To determine the required shielding effectiveness, consider the following factors:
– The electromagnetic environment in which the device will operate
– The sensitivity of the device to EMI/RFI
– The frequency range of the interference
– The applicable industry standards and regulations
Conduct a thorough EMI/RFI analysis and consult with shielding experts to determine the appropriate shielding effectiveness for your application.
2. Can custom shielding be retrofit to existing devices?
Yes, custom shielding can be retrofit to existing devices. However, the feasibility and effectiveness of the retrofit will depend on the specific device and its design. In some cases, modifications to the device may be necessary to accommodate the shielding solution. It is essential to carefully assess the device and consult with shielding experts to determine the best approach for retrofitting custom shielding.
3. How do I choose between metal and conductive polymer shielding materials?
The choice between metal and conductive polymer shielding materials depends on several factors, including:
– The required shielding effectiveness
– The weight and size constraints of the application
– The environmental conditions (e.g., temperature, humidity, corrosion)
– The production volume and cost considerations
In general, metals offer higher shielding effectiveness but are heavier and more expensive. Conductive polymers are lightweight and cost-effective but may have lower shielding effectiveness. Consider the specific requirements of your application and consult with shielding experts to select the most appropriate material.
4. How can I ensure proper grounding of custom shielding components?
To ensure proper grounding of custom shielding components, follow these best practices:
– Use low-impedance connections between the shielding component and the device’s chassis or ground plane
– Minimize the length of grounding connections to reduce inductance
– Use multiple grounding points to provide redundancy and improve shielding performance
– Ensure that the grounding connections are robust and can withstand the expected environmental conditions
Consult with shielding experts and follow industry guidelines for grounding practices to ensure optimal shielding performance.
5. What are the cost considerations for implementing custom shielding?
The cost of implementing custom shielding depends on several factors, including:
– The material selection (e.g., metals, conductive polymers, composites)
– The manufacturing technique (e.g., stamping, injection molding, 3D printing)
– The complexity of the shielding geometry and design
– The production volume and tooling requirements
In general, custom shielding can be more expensive than off-the-shelf solutions due to the need for specialized design, tooling, and manufacturing. However, the long-term benefits of improved device performance, regulatory compliance, and customer satisfaction can outweigh the initial costs. Consider the total cost of ownership and consult with shielding experts to determine the most cost-effective solution for your application.
Conclusion
Custom shielding is a critical aspect of ensuring the proper functioning and performance of electronic devices in various industries. By understanding the materials, techniques, and best practices involved in creating and implementing custom shielding, companies can develop effective solutions that meet their specific application requirements.
When designing custom shielding, it is essential to consider factors such as shielding effectiveness, frequency range, geometry, grounding, and cost. Conducting thorough EMI/RFI analyses, selecting appropriate materials, and optimizing shielding designs can help ensure the success of custom shielding implementations.
As technology continues to advance and the electromagnetic environment becomes increasingly complex, the importance of custom shielding will only continue to grow. By staying informed about the latest developments in materials, techniques, and best practices, companies can remain at the forefront of custom shielding innovation and ensure the long-term success of their products.
No responses yet