Introduction to PCB Assurance
PCB (Printed Circuit Board) assurance is a critical aspect of electronics manufacturing that ensures the quality, reliability, and functionality of the final product. In today’s highly competitive market, where consumer expectations are high and product life cycles are short, PCB assurance has become more important than ever. This article will delve into the various aspects of PCB assurance, including design, fabrication, assembly, testing, and quality control, to provide a comprehensive guide on how to ensure effective PCB assurance.
The Importance of PCB Assurance
Ensuring Product Quality and Reliability
One of the primary goals of PCB assurance is to ensure that the final product meets the desired quality and reliability standards. This involves implementing strict quality control measures throughout the PCB manufacturing process, from design to assembly and testing. By ensuring product quality and reliability, manufacturers can reduce the risk of product failures, recalls, and customer complaints, which can have a significant impact on their reputation and bottom line.
Reducing Costs and Time-to-Market
Effective PCB assurance can also help manufacturers reduce costs and time-to-market. By identifying and addressing potential issues early in the design and fabrication process, manufacturers can avoid costly rework and delays later on. Additionally, by implementing standardized processes and utilizing automation where possible, manufacturers can streamline their operations and reduce the overall cost of production.
Meeting Regulatory Requirements
Depending on the industry and application, PCBs may be subject to various regulatory requirements, such as RoHS (Restriction of Hazardous Substances), REACH (Registration, Evaluation, Authorization, and Restriction of Chemicals), and UL (Underwriters Laboratories) standards. Effective PCB assurance helps manufacturers ensure compliance with these requirements, avoiding potential legal and financial consequences.
PCB Design Assurance
Design for Manufacturability (DFM)
Design for Manufacturability (DFM) is a crucial aspect of PCB design assurance. DFM involves designing the PCB in a way that facilitates efficient and reliable manufacturing. This includes considering factors such as component placement, trace routing, and pad sizes, as well as adhering to industry-standard design rules and guidelines. By implementing DFM principles, manufacturers can reduce the risk of manufacturing defects and improve the overall quality of the final product.
Design Verification and Validation
Design verification and validation are essential steps in ensuring that the PCB design meets the required specifications and functions as intended. This involves conducting various analyses, such as signal integrity analysis, thermal analysis, and electromagnetic compatibility (EMC) analysis, to identify and address potential issues before the design is sent for fabrication. Additionally, design reviews and simulations can help verify the functionality and performance of the PCB design.
Component Selection and Management
Selecting the right components is critical to ensuring the quality and reliability of the final PCB. This involves considering factors such as component availability, reliability, and compatibility with the overall design. Effective component management, including properly storing and handling components, can help prevent issues such as component obsolescence and counterfeit parts.
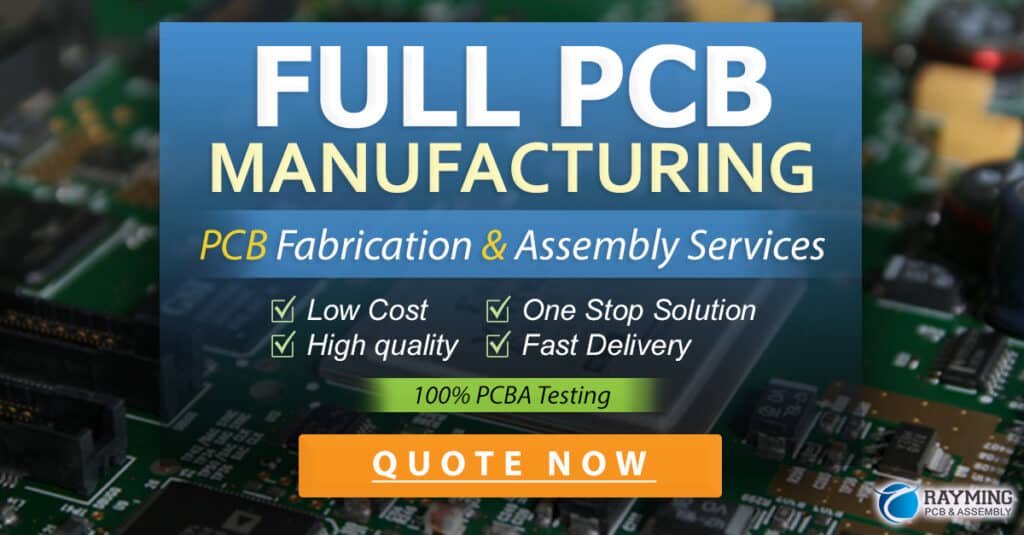
PCB Fabrication Assurance
Material Selection and Qualification
The selection and qualification of PCB materials, such as the substrate, copper foil, and solder mask, play a significant role in ensuring the quality and reliability of the final product. Manufacturers should choose materials that meet the specific requirements of the application, such as temperature range, dielectric constant, and mechanical strength. Additionally, proper material qualification, including testing and certification, can help ensure that the materials meet the required standards and specifications.
Process Control and Monitoring
Effective process control and monitoring are essential to ensuring the quality and consistency of the PCB fabrication process. This involves implementing statistical process control (SPC) techniques to monitor key process parameters, such as etching, plating, and lamination, and making adjustments as necessary to maintain process stability. Additionally, regular equipment maintenance and calibration can help prevent process deviations and ensure consistent results.
Inspection and Testing
Inspection and testing are critical components of PCB fabrication assurance. This includes both in-process and final inspections to identify and address any defects or deviations from the specified requirements. Common inspection methods include visual inspection, automated optical inspection (AOI), and X-ray inspection. Electrical testing, such as continuity and insulation resistance testing, can also help verify the functionality and performance of the fabricated PCB.
PCB Assembly Assurance
Surface Mount Technology (SMT) Process Control
Surface Mount Technology (SMT) is the most common method for assembling PCBs, and effective process control is essential to ensuring the quality and reliability of the assembled product. This involves monitoring and controlling key process parameters, such as solder paste printing, component placement, and reflow soldering, to ensure consistent and repeatable results. Additionally, regular equipment maintenance and calibration can help prevent process deviations and ensure optimal performance.
Soldering Quality Control
Soldering is a critical aspect of PCB assembly, and poor soldering quality can lead to reliability issues and product failures. Effective soldering quality control involves implementing best practices, such as using the appropriate solder alloy and flux, controlling the soldering temperature and time, and ensuring proper cleaning and inspection of the soldered joints. Additionally, regular training and certification of soldering operators can help ensure consistent and high-quality soldering results.
Conformal Coating and Potting
Conformal coating and potting are methods used to protect PCBs from environmental factors, such as moisture, dust, and chemicals. Effective conformal coating and potting assurance involves selecting the appropriate materials and application methods, as well as conducting regular inspections and testing to ensure proper coverage and adhesion. Additionally, proper curing and storage conditions can help ensure the long-term effectiveness of the protective coatings.
PCB Testing and Quality Control
In-Circuit Testing (ICT)
In-Circuit Testing (ICT) is a method used to verify the functionality and performance of individual components on the assembled PCB. ICT involves using a bed-of-nails fixture to make electrical contact with the PCB and conducting various tests, such as continuity, resistance, and capacitance measurements. Effective ICT assurance involves designing the PCB with testability in mind, as well as regularly maintaining and calibrating the test equipment to ensure accurate and reliable results.
Functional Testing
Functional testing is a method used to verify that the assembled PCB performs as intended in its final application. This involves subjecting the PCB to various stimuli, such as power, input signals, and environmental conditions, and measuring its response and output. Effective functional testing assurance involves designing comprehensive test plans and procedures, as well as using appropriate test equipment and fixtures to simulate the actual operating conditions of the PCB.
Reliability Testing
Reliability testing is a method used to assess the long-term performance and durability of the assembled PCB. This involves subjecting the PCB to various stress factors, such as temperature cycling, vibration, and humidity, and measuring its performance over time. Effective reliability testing assurance involves designing appropriate test plans and procedures, as well as using specialized test equipment and facilities to simulate the actual operating conditions of the PCB over its expected lifetime.
Frequently Asked Questions (FAQ)
1. What are the key elements of an effective PCB assurance program?
An effective PCB assurance program should include the following key elements:
– Design for Manufacturability (DFM) principles
– Design verification and validation
– Proper component selection and management
– Material selection and qualification
– Process control and monitoring
– Inspection and testing
– Soldering quality control
– Conformal coating and potting
– In-Circuit Testing (ICT)
– Functional testing
– Reliability testing
2. How can I ensure compliance with regulatory requirements for my PCBs?
To ensure compliance with regulatory requirements, you should:
– Identify the specific requirements applicable to your product and industry
– Select materials and components that meet the required standards and specifications
– Implement appropriate process controls and monitoring to ensure consistent compliance
– Conduct regular testing and certification to verify compliance
– Maintain accurate and up-to-date documentation of your compliance efforts
3. What are some common challenges in PCB assurance, and how can they be addressed?
Some common challenges in PCB assurance include:
– Design complexity and miniaturization: Implement DFM principles and conduct thorough design verification and validation
– Component availability and obsolescence: Establish a robust component management program and consider alternative sourcing options
– Process variability and consistency: Implement statistical process control (SPC) techniques and conduct regular equipment maintenance and calibration
– Time and cost constraints: Utilize automation where possible and implement a risk-based approach to prioritize assurance activities
4. How can I select the right PCB fabrication and assembly partners for my project?
When selecting PCB fabrication and assembly partners, consider the following factors:
– Technical capabilities and experience with similar projects
– Quality management systems and certifications (e.g., ISO 9001, AS9100)
– Capacity and lead times
– Communication and responsiveness
– Cost and value for money
– References and reputation in the industry
5. What are some best practices for PCB testing and quality control?
Some best practices for PCB testing and quality control include:
– Design for testability and manufacturability
– Develop comprehensive test plans and procedures
– Use appropriate test equipment and fixtures
– Conduct regular equipment maintenance and calibration
– Implement statistical process control (SPC) techniques
– Conduct root cause analysis and corrective action for any defects or failures
– Maintain accurate and up-to-date documentation of testing and quality control activities
Conclusion
Effective PCB assurance is critical to ensuring the quality, reliability, and functionality of electronic products in today’s competitive market. By implementing best practices in design, fabrication, assembly, testing, and quality control, manufacturers can reduce the risk of product failures, minimize costs and time-to-market, and ensure compliance with regulatory requirements.
This comprehensive guide has covered the various aspects of PCB assurance, including the importance of design for manufacturability, material selection and qualification, process control and monitoring, soldering quality control, and testing and quality control methods such as in-circuit testing, functional testing, and reliability testing.
By following the best practices and recommendations outlined in this article, manufacturers can develop and implement an effective PCB assurance program that meets the specific needs and requirements of their products and industries. Ultimately, investing in PCB assurance can help manufacturers build a reputation for quality and reliability, leading to increased customer satisfaction, loyalty, and long-term success in the marketplace.
No responses yet