Introduction to SchematicLayout
When designing a printed circuit board (PCB), the schematic is the first step in the process. It defines the electrical connections and components that make up the circuit. Once the schematic is complete, the next step is to create the layout, which is the physical representation of the circuit on the PCB. The layout determines where the components will be placed and how the traces will be routed to connect them.
Creating the layout from the schematic can be a complex process, but with the right tools and techniques, it can be done efficiently and effectively. In this article, we will explore the key steps involved in creating the layout from your schematic.
Understanding the Schematic
Before you can begin creating the layout, it is essential to have a thorough understanding of the schematic. The schematic is a graphical representation of the electrical connections and components in the circuit. It uses standardized symbols to represent the various components, such as resistors, capacitors, and Integrated Circuits.
Each component in the schematic has a unique reference designator, which is used to identify it in the layout. The schematic also shows the connections between the components, which are represented by lines or wires.
Key Elements of a Schematic
- Components: The schematic includes symbols for each component in the circuit, such as resistors, capacitors, and integrated circuits.
- Reference Designators: Each component has a unique reference designator, which is used to identify it in the layout.
- Connections: The schematic shows the electrical connections between the components, represented by lines or wires.
- Power and Ground: The schematic indicates the power and ground connections for the circuit.
Interpreting the Schematic
To create an accurate layout, it is crucial to correctly interpret the schematic. This involves understanding the function of each component and how they are connected. Some key things to look for when interpreting the schematic include:
- Component values: The schematic will specify the values for components such as resistors and capacitors.
- Polarity: Some components, such as electrolytic capacitors and diodes, have a specific polarity that must be observed in the layout.
- Connections: Pay close attention to how the components are connected in the schematic, as this will determine how they are placed and routed in the layout.
Planning the Layout
Once you have a solid understanding of the schematic, the next step is to plan the layout. This involves determining the size and shape of the PCB, as well as the placement of the components and routing of the traces.
Determining PCB Size and Shape
The size and shape of the PCB will depend on the requirements of the project. Some factors to consider include:
- Enclosure: If the PCB will be housed in an enclosure, the size and shape of the PCB must fit within the available space.
- Mounting: The PCB may need to be mounted to other components or surfaces, which will affect its size and shape.
- Cost: Larger PCBs are generally more expensive to manufacture, so it is important to keep the size as small as possible while still meeting the requirements of the project.
Component Placement
The placement of the components on the PCB is a critical aspect of the layout. Some key considerations for component placement include:
- Functionality: Components should be placed in a way that maximizes the functionality of the circuit.
- Routing: The placement of the components will affect the routing of the traces, so it is important to consider how the traces will be routed when placing the components.
- Thermal Management: Some components, such as power regulators and transistors, generate heat and may require additional thermal management techniques, such as heatsinks or Thermal Vias.
Trace Routing
The routing of the traces on the PCB is another critical aspect of the layout. The traces are the copper pathways that connect the components and carry the electrical signals. Some key considerations for trace routing include:
- Signal Integrity: The routing of the traces can affect the signal integrity of the circuit, so it is important to follow best practices for trace routing, such as avoiding sharp angles and minimizing the length of the traces.
- Crosstalk: Traces that are too close together can result in crosstalk, which can cause interference and degrade the performance of the circuit.
- Impedance: The impedance of the traces must be carefully controlled to ensure proper signal propagation and to minimize reflections.
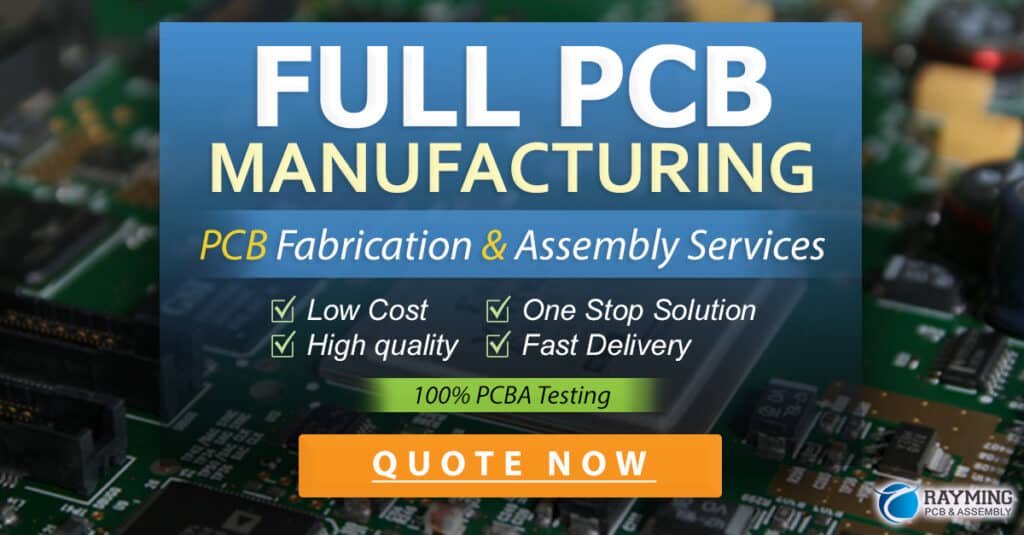
Creating the Layout
With the planning complete, the next step is to create the actual layout. This involves using specialized software to place the components and route the traces on the PCB.
Choosing the Right Software
There are many different software options available for creating PCB Layouts, ranging from free open-source tools to high-end commercial packages. Some popular options include:
Software | Description | Cost |
---|---|---|
KiCad | Open-source EDA software suite for PCB design | Free |
Eagle | Popular PCB Design Software for hobbyists and professionals | Paid |
Altium Designer | High-end PCB design software for professional use | Paid |
When choosing software for creating your layout, consider factors such as ease of use, features, and cost.
Placing Components
The first step in creating the layout is to place the components on the PCB. This involves importing the schematic into the layout software and then placing the components according to the planned layout.
Some key considerations when placing components include:
- Orientation: Components should be placed in the correct orientation, with pin 1 facing the correct direction.
- Spacing: Components should be spaced appropriately to allow for proper routing and to avoid interference.
- Mounting Holes: If the PCB will be mounted using screws or standoffs, be sure to include mounting holes in the appropriate locations.
Routing Traces
Once the components are placed, the next step is to route the traces between them. This involves creating the copper pathways that will carry the electrical signals between the components.
Some key considerations when routing traces include:
- Width: The width of the traces should be appropriate for the current carrying requirements of the circuit.
- Spacing: Traces should be spaced appropriately to avoid crosstalk and interference.
- Vias: Vias are used to connect traces on different layers of the PCB. Be sure to use the appropriate via size and spacing for your design.
Design Rule Checking
Once the layout is complete, it is important to perform a design rule check (DRC) to ensure that the layout meets all of the necessary design rules and constraints. The DRC will check for issues such as trace spacing violations, component clearance violations, and more.
Most layout software includes built-in DRC tools that can be used to check the layout against a set of predefined rules. It is important to carefully review the results of the DRC and make any necessary changes to the layout to ensure that it is fully compliant.
Outputting the Layout
Once the layout is complete and has passed the DRC, the next step is to output the necessary files for manufacturing. This typically involves generating Gerber files, which are the industry standard format for PCB manufacturing.
Most layout software includes tools for generating Gerber files automatically based on the layout. It is important to carefully review the generated files to ensure that they are correct and complete.
In addition to the Gerber files, you may also need to generate other manufacturing files, such as drill files and pick-and-place files. These files provide additional information to the manufacturer about how to fabricate and assemble the PCB.
Best Practices for Creating Layouts
Creating a high-quality PCB layout requires careful attention to detail and adherence to best practices. Some key best practices to keep in mind when creating your layout include:
- Keep it simple: Avoid unnecessary complexity in your layout, and strive for a clean and straightforward design.
- Plan ahead: Take the time to carefully plan your layout before beginning the actual design process.
- Use a grid: Using a grid can help to ensure that components are placed accurately and consistently.
- Follow the datasheet: Be sure to carefully review the datasheet for each component to ensure that you are using it correctly and adhering to its specifications.
- Test and iterate: Once your layout is complete, be sure to thoroughly test it and make any necessary revisions to ensure optimal performance.
By following these best practices and taking a methodical approach to creating your layout, you can ensure that your PCB will function correctly and meet the requirements of your project.
Frequently Asked Questions
- What is the difference between a schematic and a layout?
-
A schematic is a graphical representation of the electrical connections and components in a circuit, while a layout is the physical representation of the circuit on a PCB.
-
Can I create a layout without a schematic?
-
While it is technically possible to create a layout without a schematic, it is not recommended. The schematic provides important information about the circuit that is necessary for creating an accurate and functional layout.
-
What software should I use for creating my layout?
-
There are many different software options available for creating PCB layouts, ranging from free open-source tools to high-end commercial packages. Some popular options include KiCad, Eagle, and Altium Designer. Ultimately, the best software for you will depend on your specific needs and budget.
-
How important is component placement in the layout?
-
Component placement is a critical aspect of the layout, as it can affect the functionality, routing, and thermal management of the circuit. It is important to carefully consider the placement of each component to ensure optimal performance.
-
What are some common mistakes to avoid when creating a layout?
- Some common mistakes to avoid when creating a layout include failing to adhere to design rules and constraints, not carefully planning the layout before beginning the design process, and not thoroughly testing the completed layout. By following best practices and taking a methodical approach, you can avoid these mistakes and create a high-quality PCB layout.
Conclusion
Creating a layout from a schematic is a critical step in the PCB design process. By carefully planning the layout, placing components, and routing traces, you can create a high-quality PCB that meets the requirements of your project.
To create a successful layout, it is important to have a thorough understanding of the schematic, choose the right software tools, and adhere to best practices and design rules. By taking a methodical approach and paying attention to detail, you can ensure that your PCB will function correctly and meet the needs of your project.
No responses yet