The Fourth Industrial Revolution is Transforming Manufacturing
The manufacturing industry is undergoing a major transformation known as Industry 4.0 or the Fourth Industrial Revolution. Industry 4.0 refers to the current trend of automation, data exchange, and the integration of cyber-physical systems, the Internet of Things (IoT), cloud computing, and cognitive computing in manufacturing technologies.
According to Craig Arcuri, an Industry 4.0 expert and consultant, this new wave of industrial innovation is poised to dramatically change how products are designed, manufactured, delivered, and serviced. “Industry 4.0 is not just about incremental improvements in efficiency or productivity,” says Arcuri. “It represents a fundamental shift in how value is created and captured across the entire manufacturing ecosystem.”
Key Components of Industry 4.0
Arcuri identifies several key components that define Industry 4.0:
Component | Description |
---|---|
Cyber-Physical Systems | The integration of computation, networking, and physical processes, enabling real-time interaction between the digital and physical worlds. |
Internet of Things (IoT) | The interconnection of physical devices, vehicles, buildings, and other items embedded with electronics, software, sensors, and network connectivity, enabling these objects to collect and exchange data. |
Cloud Computing | The delivery of computing services—including servers, storage, databases, networking, software, analytics, and intelligence—over the internet (“the cloud”). |
Cognitive Computing | The simulation of human thought processes in a computerized model, often involving self-learning systems that use data mining, pattern recognition, and natural language processing to mimic the way the human brain works. |
“When you combine these technologies,” explains Arcuri, “you create a powerful framework for digitizing and optimizing every aspect of the manufacturing process, from design and engineering to production, logistics, and service.”
The Benefits of Industry 4.0
According to Arcuri, the potential benefits of Industry 4.0 are significant and wide-ranging. Some of the key advantages include:
1. Increased Efficiency and Productivity
By leveraging automation, data analytics, and real-time monitoring, manufacturers can streamline their operations, reduce downtime, and increase output. “With Industry 4.0 technologies, factories can operate 24/7 with minimal human intervention,” says Arcuri. “This not only boosts productivity but also frees up human workers to focus on higher-value tasks.”
2. Improved Quality and Consistency
Industry 4.0 technologies enable manufacturers to monitor and control every aspect of the production process, ensuring that products meet the highest standards of quality and consistency. “With real-time data collection and analysis, manufacturers can detect and correct defects before they become a problem,” explains Arcuri. “This leads to fewer recalls, less waste, and happier customers.”
3. Greater Flexibility and Customization
Industry 4.0 technologies enable manufacturers to quickly adapt to changing market demands and customer preferences. “With advanced manufacturing techniques like 3D printing and modular production lines, manufacturers can easily customize products to meet individual customer needs,” says Arcuri. “This level of flexibility is a key competitive advantage in today’s fast-paced, customer-centric marketplace.”
4. Enhanced Supply chain visibility
Industry 4.0 technologies provide end-to-end visibility into the supply chain, enabling manufacturers to track products from raw materials to final delivery. “With real-time data on inventory levels, production schedules, and logistics, manufacturers can optimize their supply chains for maximum efficiency and responsiveness,” explains Arcuri. “This not only reduces costs but also improves customer service and satisfaction.”
5. New Business Models and Revenue Streams
Industry 4.0 technologies are enabling manufacturers to develop new business models and revenue streams beyond traditional product sales. “With connected products and services, manufacturers can offer value-added services like predictive maintenance, remote monitoring, and performance optimization,” says Arcuri. “These services not only generate recurring revenue but also deepen customer relationships and loyalty.”
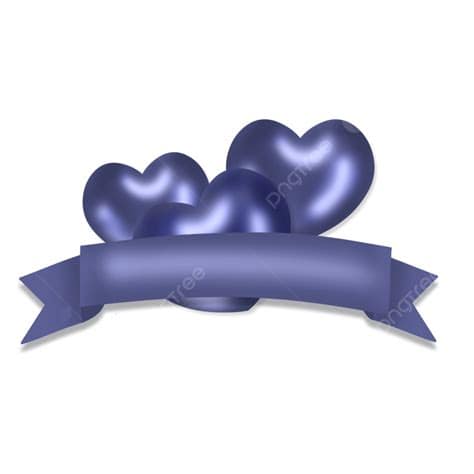
Challenges and Considerations
While the benefits of Industry 4.0 are significant, Arcuri also acknowledges that there are challenges and considerations that manufacturers must address:
1. Cybersecurity Risks
As manufacturing becomes more connected and data-driven, the risk of cyberattacks and data breaches increases. “Manufacturers must prioritize cybersecurity and invest in robust security measures to protect their systems, data, and intellectual property,” advises Arcuri. “This includes everything from secure network architectures and encryption to employee training and incident response planning.”
2. Workforce Upskilling and Reskilling
Industry 4.0 technologies require a workforce with new skills and competencies, such as data analytics, programming, and robotics. “Manufacturers must invest in upskilling and reskilling their existing workforce to meet the demands of Industry 4.0,” says Arcuri. “This may involve partnering with educational institutions, offering on-the-job training, or developing internal training programs.”
3. Integration and Interoperability
Industry 4.0 technologies involve the integration of multiple systems and devices, which can be challenging given the diversity of manufacturers’ existing technology stacks. “Manufacturers must ensure that their Industry 4.0 technologies can seamlessly integrate with their existing systems and processes,” explains Arcuri. “This requires a careful assessment of current capabilities and a roadmap for phased implementation.”
4. Change Management and Culture
Implementing Industry 4.0 technologies requires significant changes to organizational culture, processes, and ways of working. “Manufacturers must actively manage the change process and engage employees at all levels to ensure buy-in and adoption,” advises Arcuri. “This involves clear communication, training, and incentives to support the transition to a more digitized and data-driven manufacturing environment.”
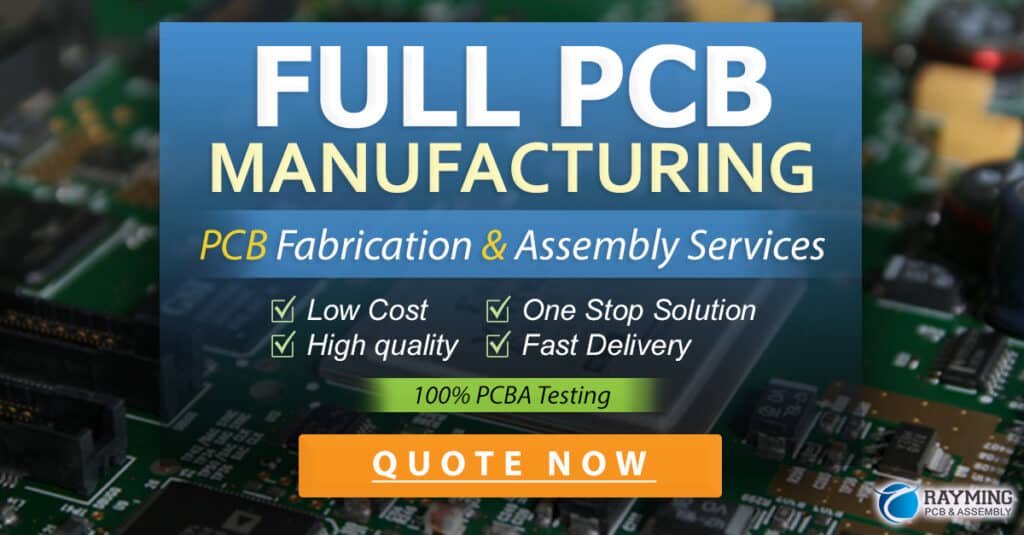
Case Studies and Examples
To illustrate the impact of Industry 4.0, Arcuri points to several real-world examples:
1. Siemens
Siemens, a global leader in industrial automation and digitalization, has fully embraced Industry 4.0 in its own manufacturing operations. The company’s “Digital Enterprise” strategy involves the end-to-end digitalization of its entire value chain, from product design and engineering to production, logistics, and service.
One example is Siemens’ “Smart Factory” in Amberg, Germany, which produces programmable logic controllers (PLCs). The factory is highly automated and connected, with over 75% of the production process handled by machines and robots. The factory also collects and analyzes vast amounts of data to optimize performance and predict maintenance needs. As a result, the Amberg Smart Factory has achieved a 99.99% perfect order measurement and a 10x increase in productivity.
2. Boeing
Boeing, the world’s largest aerospace company, is using Industry 4.0 technologies to transform its manufacturing operations. One example is the company’s “Fuselage Automated Upright Build” (FAUB) process, which uses robots to assemble the fuselage of its 777 aircraft.
The FAUB process involves the use of automated guided vehicles (AGVs) to transport fuselage sections to the assembly line, where robots then drill and fasten the sections together. The process is controlled by a central computer system that monitors every step of the assembly process and makes real-time adjustments as needed. As a result, the FAUB process has reduced the time required to assemble a 777 fuselage by 50% and improved quality and safety.
3. Johnson & Johnson
Johnson & Johnson, a global healthcare company, is using Industry 4.0 technologies to transform its supply chain and manufacturing operations. One example is the company’s “Digital Supply Chain” initiative, which involves the use of advanced analytics, artificial intelligence, and machine learning to optimize supply chain performance.
The Digital Supply Chain initiative includes the use of predictive analytics to forecast demand, optimize inventory levels, and reduce waste. It also involves the use of real-time monitoring and tracking to ensure product quality and integrity throughout the supply chain. As a result, Johnson & Johnson has achieved significant improvements in supply chain efficiency, agility, and responsiveness.
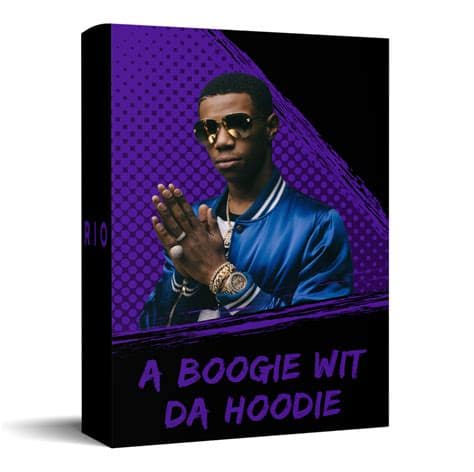
The Future of Industry 4.0
Looking ahead, Arcuri sees Industry 4.0 continuing to evolve and transform manufacturing in several key areas:
1. Autonomous Systems
As Industry 4.0 technologies mature, Arcuri expects to see the development of more fully autonomous systems that can operate with minimal human intervention. “We’re already seeing the emergence of autonomous factories, where robots and machines can independently plan, execute, and optimize production processes,” says Arcuri. “In the future, we may see entire supply chains that are largely autonomous, with humans primarily involved in strategic oversight and decision-making.”
2. Artificial Intelligence and Machine Learning
Artificial intelligence (AI) and machine learning (ML) are already playing a significant role in Industry 4.0, but Arcuri expects their impact to grow even further in the coming years. “AI and ML will enable manufacturers to unlock even greater insights from their data, optimize processes in real-time, and make more accurate predictions about future demand and performance,” explains Arcuri. “We may also see the emergence of more advanced AI systems that can design and develop new products and processes autonomously.”
3. 5G and Edge Computing
The rollout of 5G networks and the growth of edge computing are expected to have a significant impact on Industry 4.0 in the coming years. “5G will provide the high-speed, low-latency connectivity needed to support real-time data exchange and control in Industry 4.0 environments,” says Arcuri. “Edge computing will enable manufacturers to process and analyze data closer to the source, reducing latency and enabling faster decision-making.”
4. Sustainable Manufacturing
Industry 4.0 technologies also have the potential to enable more sustainable manufacturing practices. “By optimizing resource use, reducing waste, and enabling circular economy models, Industry 4.0 can help manufacturers reduce their environmental footprint and contribute to a more sustainable future,” explains Arcuri. “This includes everything from using renewable energy sources to power factories to designing products for reuse and recycling.”
Frequently Asked Questions (FAQ)
1. What is the difference between Industry 4.0 and the Industrial Internet of Things (IIoT)?
While Industry 4.0 and IIoT are often used interchangeably, they are not exactly the same thing. Industry 4.0 refers to the broader trend of digitalization and automation in manufacturing, which includes the use of IIoT technologies. IIoT specifically refers to the use of internet-connected devices and sensors to collect and exchange data in industrial settings. So while IIoT is a key component of Industry 4.0, it is not the only one.
2. How can small and medium-sized manufacturers get started with Industry 4.0?
Arcuri recommends that small and medium-sized manufacturers start by identifying specific use cases or pain points that Industry 4.0 technologies could address. “This could be anything from reducing downtime on a particular machine to improving quality control in a specific process,” explains Arcuri. “Once you have identified a use case, you can start small by piloting a specific technology or solution and then scale up from there.”
3. What are the key skills needed for Industry 4.0?
According to Arcuri, some of the key skills needed for Industry 4.0 include:
– Data analytics and data science
– Programming and software development
– Robotics and automation
– Cybersecurity and data privacy
– Change management and leadership
“Manufacturers will need to invest in upskilling and reskilling their workforce to ensure they have the necessary skills to thrive in an Industry 4.0 environment,” says Arcuri.
4. How can manufacturers ensure the security of their Industry 4.0 systems and data?
Arcuri emphasizes the importance of a multi-layered approach to cybersecurity in Industry 4.0 environments. “This includes everything from secure network architectures and encryption to regular security audits and employee training,” explains Arcuri. “Manufacturers should also have clear incident response plans in place to minimize the impact of any potential breaches.”
5. What are some of the key standards and frameworks for Industry 4.0?
Some of the key standards and frameworks for Industry 4.0 include:
– The Reference Architecture Model for Industry 4.0 (RAMI 4.0)
– The Industrial Internet Reference Architecture (IIRA)
– The National Institute of Standards and Technology (NIST) Cybersecurity Framework
– The International Organization for Standardization (ISO) standards for automation and data exchange in manufacturing
“These standards and frameworks provide a common language and set of best practices for implementing Industry 4.0 technologies,” explains Arcuri. “Manufacturers should familiarize themselves with these standards and use them as a guide in their own Industry 4.0 journeys.”
Conclusion
Industry 4.0 represents a major shift in how manufacturing is done, and Craig Arcuri believes that it will continue to transform the industry in the coming years. By leveraging technologies such as IoT, AI, robotics and 3D printing along with big data and analytics, manufacturers can achieve significant improvements in efficiency,productivity, quality, flexibility, and sustainability.
However, realizing the full potential of Industry 4.0 will require manufacturers to navigate a range of challenges and considerations, from cybersecurity risks and workforce skills gaps to change management and standards adoption.
“The transition to Industry 4.0 is not a one-time event but an ongoing journey,” says Arcuri. “It requires a strategic, holistic approach that involves people, processes, and technology. But for those manufacturers that get it right, the benefits can be game-changing.”
No responses yet