Understanding the Factors Influencing PCB Costs
Before delving into cost-cutting strategies, it is essential to understand the factors that contribute to the overall cost of PCB Services. Several key elements impact the price of PCB manufacturing:
1. PCB Design Complexity
The complexity of a PCB design directly influences the manufacturing cost. Factors such as the number of layers, component density, trace width, and via size all contribute to the complexity of the board. More complex designs require additional processing steps and materials, resulting in higher costs.
2. Material Selection
The choice of materials used in PCB manufacturing plays a significant role in determining the cost. The most common base material for PCBs is FR-4, which is a glass-reinforced epoxy laminate. However, specialized applications may require the use of high-frequency materials like Rogers or Isola, which come at a higher price point.
3. Manufacturing Volume
The volume of PCBs being manufactured has a substantial impact on the overall cost. Higher production volumes often lead to lower per-unit costs due to economies of scale. Manufacturers can optimize their processes and materials when producing larger quantities, resulting in cost savings that can be passed on to the customer.
4. Turnaround Time
The turnaround time for PCB manufacturing also influences the cost. Faster turnaround times typically come at a premium, as manufacturers need to prioritize and expedite certain orders. Longer lead times allow for more efficient scheduling and resource allocation, which can help reduce costs.
Strategies for Cost-cutting in PCB Services
Now that we have a better understanding of the factors affecting PCB costs, let’s explore some effective strategies for cost-cutting in PCB services.
1. Design Optimization
One of the most crucial aspects of cost-cutting in PCB services is design optimization. By streamlining the PCB design, manufacturers can reduce complexity, minimize material usage, and improve manufacturing efficiency. Here are some design optimization techniques:
a. Minimizing Layer Count
Reducing the number of layers in a PCB can significantly lower manufacturing costs. Each additional layer requires more materials, processing steps, and time. By carefully planning the component placement and routing, designers can often achieve the same functionality with fewer layers.
b. Optimizing Component Placement
Efficient component placement is essential for cost-effective PCB manufacturing. Grouping similar components together and minimizing the distance between them can reduce the overall board size and simplify the routing process. This, in turn, leads to lower material costs and faster assembly times.
c. Standardizing Component Sizes
Using standardized component sizes and packages can help reduce costs by allowing for more efficient manufacturing processes. Standardized components are readily available and often less expensive than custom or specialized parts. Additionally, using common component sizes enables manufacturers to optimize their pick-and-place machines and reduce setup times.
d. Avoiding Tight Tolerances
Tight tolerances in PCB design can significantly increase manufacturing costs. Whenever possible, designers should aim for more relaxed tolerances that are still within the acceptable range for the intended application. Looser tolerances allow for more flexibility in the manufacturing process, reducing the need for specialized equipment and minimizing the risk of defects.
2. Material Cost Reduction
Material costs constitute a significant portion of the overall PCB manufacturing expense. By carefully selecting materials and optimizing their usage, companies can achieve substantial cost savings.
a. Material Selection
Choosing the appropriate materials for a PCB is crucial for balancing performance and cost. While specialized materials like Rogers or Isola offer excellent high-frequency performance, they come at a higher price point. For many applications, standard FR-4 material may suffice, providing adequate performance at a lower cost.
b. Panelization
Panelization is the process of arranging multiple PCB designs on a single panel for manufacturing. By maximizing the utilization of the panel area, manufacturers can reduce material waste and improve production efficiency. Effective panelization strategies, such as optimizing the placement of boards and minimizing the space between them, can lead to significant cost savings.
c. Thickness Reduction
Reducing the thickness of the PCB can also contribute to cost savings. Thinner boards require less material and are faster to manufacture. However, it is essential to ensure that the reduced thickness does not compromise the structural integrity or functionality of the PCB.
3. Volume Pricing and Batch Manufacturing
One of the most effective ways to reduce PCB costs is by leveraging volume pricing and batch manufacturing. Many PCB manufacturers offer discounted rates for larger order quantities, as it allows them to optimize their production processes and achieve economies of scale.
a. Volume Pricing
Negotiating volume pricing with PCB manufacturers can result in significant cost savings. By committing to larger order quantities, companies can secure lower per-unit prices. It is essential to carefully forecast demand and plan production schedules to take advantage of volume pricing without incurring excess inventory costs.
b. Batch Manufacturing
Batch manufacturing involves producing multiple PCBs simultaneously, either for the same design or for different designs with similar specifications. By grouping orders together, manufacturers can reduce setup times, minimize changeovers, and optimize material usage. This approach leads to increased efficiency and lower overall costs.
4. Vendor Selection and Relationship Management
Selecting the right PCB vendor and maintaining a strong relationship with them can have a significant impact on cost-cutting efforts.
a. Vendor Selection
When choosing a PCB manufacturer, it is crucial to consider factors beyond just the quoted price. Evaluating a vendor’s capabilities, quality control processes, and track record can help ensure that they can deliver high-quality PCBs consistently. Additionally, considering a vendor’s location and shipping options can impact the total cost of ownership.
b. Long-term Partnerships
Establishing long-term partnerships with PCB vendors can lead to cost savings over time. By building a strong relationship and consistently placing orders with a single vendor, companies can negotiate better pricing, secure priority service, and collaborate on cost-optimization initiatives. Long-term partnerships also enable better communication and coordination, reducing the risk of errors and delays.
c. Clear Communication
Clear and effective communication with PCB vendors is essential for cost-cutting. Providing detailed specifications, drawings, and requirements upfront can help avoid misunderstandings and rework. Regular communication throughout the manufacturing process can also help identify potential issues early on, allowing for timely corrective actions and minimizing costly delays.
PCB Cost-cutting Techniques: A Visual Overview
To summarize the key cost-cutting techniques discussed in this article, let’s take a look at the following table:
Technique | Description | Benefits |
---|---|---|
Design Optimization | Streamlining PCB design to reduce complexity and material usage | Lower material costs, improved manufacturing efficiency |
Material Cost Reduction | Selecting appropriate materials and optimizing their usage | Reduced material expenses, improved panel utilization |
Volume Pricing and Batch Manufacturing | Leveraging larger order quantities and grouping similar orders together | Discounted per-unit prices, increased production efficiency |
Vendor Selection and Relationship Management | Choosing the right vendor and building long-term partnerships | Consistent quality, priority service, collaborative cost optimization |
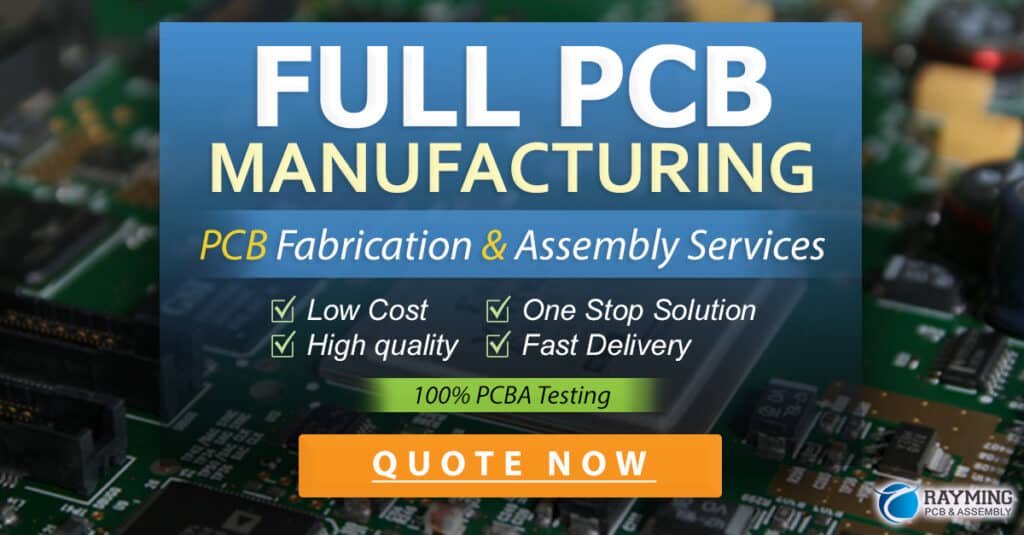
Frequently Asked Questions (FAQ)
-
Q: How can I determine if my PCB design is optimized for cost-cutting?
A: To assess the cost-effectiveness of your PCB design, consider factors such as layer count, component placement, standardized component sizes, and tolerance requirements. Consult with your PCB manufacturer or a design expert to identify potential areas for optimization. -
Q: Is it always better to choose the lowest-cost PCB vendor?
A: While cost is an important consideration, it should not be the sole deciding factor when selecting a PCB vendor. Evaluate a vendor’s capabilities, quality control processes, and reputation to ensure they can deliver high-quality PCBs consistently. Choosing the lowest-cost option may lead to compromised quality and reliability. -
Q: How can I forecast demand accurately to take advantage of volume pricing?
A: Accurate demand forecasting requires a combination of historical sales data, market trends, and customer insights. Collaborate with your sales and marketing teams to gather relevant information and use forecasting tools and techniques to predict future demand. Regular reviews and adjustments based on actual sales can help refine your forecasting accuracy over time. -
Q: What are the risks associated with reducing PCB Thickness for cost-cutting?
A: Reducing PCB thickness can help save on material costs, but it also comes with certain risks. Thinner boards may be more susceptible to warping, cracking, or other structural issues, especially in applications with high thermal or mechanical stress. It is essential to carefully consider the specific requirements of your application and consult with your PCB manufacturer to determine the appropriate thickness. -
Q: How can I ensure effective communication with my PCB vendor to support cost-cutting efforts?
A: To facilitate effective communication with your PCB vendor, provide clear and detailed specifications, drawings, and requirements upfront. Establish regular communication channels and designate a point of contact within your organization to coordinate with the vendor. Schedule periodic reviews and meetings to discuss progress, address any issues, and explore cost-optimization opportunities collaboratively.
Conclusion
Cost-cutting in PCB services is a multi-faceted approach that requires careful consideration of design, materials, manufacturing processes, and vendor relationships. By implementing the strategies and techniques discussed in this article, companies can significantly reduce their PCB Manufacturing Costs without compromising quality or functionality.
Design optimization, material cost reduction, volume pricing, batch manufacturing, and effective vendor management are all essential components of a successful cost-cutting strategy. By streamlining designs, selecting appropriate materials, leveraging economies of scale, and fostering strong partnerships with PCB vendors, businesses can achieve substantial cost savings and remain competitive in the ever-evolving electronics industry.
As technology advances and market demands continue to shift, staying informed about the latest cost-cutting techniques and best practices in PCB services is crucial. By continuously evaluating and refining their approach to PCB manufacturing, companies can adapt to changing circumstances and maintain a competitive edge.
Ultimately, the key to successful cost-cutting in PCB services lies in striking the right balance between cost optimization and maintaining the highest standards of quality and reliability. By carefully considering the strategies outlined in this article and collaborating closely with PCB vendors, businesses can navigate the complex landscape of PCB manufacturing and achieve their cost-cutting goals while delivering exceptional products to their customers.
No responses yet