Thermal Management
One of the primary concerns for users of copper PCBs is thermal management. As electronic devices become more compact and powerful, the amount of heat generated by the components increases. If this heat is not dissipated effectively, it can lead to performance issues and even damage the components. Copper PCBs play a crucial role in thermal management due to their high thermal conductivity.
Thermal Conductivity of Copper
Material | Thermal Conductivity (W/mK) |
---|---|
Copper | 385 |
Aluminum | 205 |
Gold | 314 |
Silver | 406 |
As seen in the table above, copper has a high thermal conductivity compared to other common materials used in PCBs. This property allows copper PCBs to effectively transfer heat away from the components and distribute it evenly across the board.
Thermal Vias
To further enhance thermal management, designers often incorporate thermal vias into copper PCBs. Thermal vias are small, plated holes that are strategically placed near heat-generating components to provide a direct path for heat to transfer to the other side of the board or to a heatsink.
Signal Integrity
Another important concern for users of copper PCBs is signal integrity. As the speed and frequency of electronic devices increase, maintaining the quality of the signals becomes more challenging. Copper PCBs play a vital role in ensuring signal integrity by providing a stable and reliable platform for signal transmission.
Impedance Control
One way to maintain signal integrity in copper PCBs is through impedance control. Impedance is the measure of opposition to the flow of alternating current (AC) in a circuit. By carefully designing the width, thickness, and spacing of the copper traces, designers can control the impedance of the PCB and minimize signal reflections and distortions.
Shielding
Another technique for maintaining signal integrity is shielding. Copper PCBs can be designed with shielding layers that protect sensitive signals from electromagnetic interference (EMI) and radio frequency interference (RFI). These shielding layers are typically made of copper and are connected to ground to create a Faraday cage around the sensitive components.
Manufacturability
The manufacturability of copper PCBs is another important concern for users. The design and layout of the PCB can have a significant impact on the ease and cost of manufacturing. Designers must consider several factors to ensure that the PCB can be manufactured efficiently and reliably.
Minimum Feature Size
One important factor in the manufacturability of copper PCBs is the minimum feature size. This refers to the smallest width and spacing of the copper traces that can be reliably produced by the manufacturing process. As the minimum feature size decreases, the cost and complexity of manufacturing increase.
PCB Class | Minimum Feature Size (mm) |
---|---|
Class 1 | 0.75 |
Class 2 | 0.30 |
Class 3 | 0.15 |
Class 4 | 0.075 |
The table above shows the minimum feature sizes for different classes of PCBs. Designers must choose the appropriate class based on the requirements of the application and the capabilities of the manufacturing process.
Design for Manufacturing (DFM)
Another important aspect of manufacturability is Design for Manufacturing (DFM). DFM is a set of guidelines and best practices that help designers create PCBs that are easy and cost-effective to manufacture. Some common DFM guidelines include:
- Avoiding acute angles in copper traces
- Providing adequate clearance between components and traces
- Using standard hole sizes and pad shapes
- Minimizing the number of layers in the PCB
By following DFM guidelines, designers can reduce the risk of manufacturing defects and improve the overall quality and reliability of the PCB.
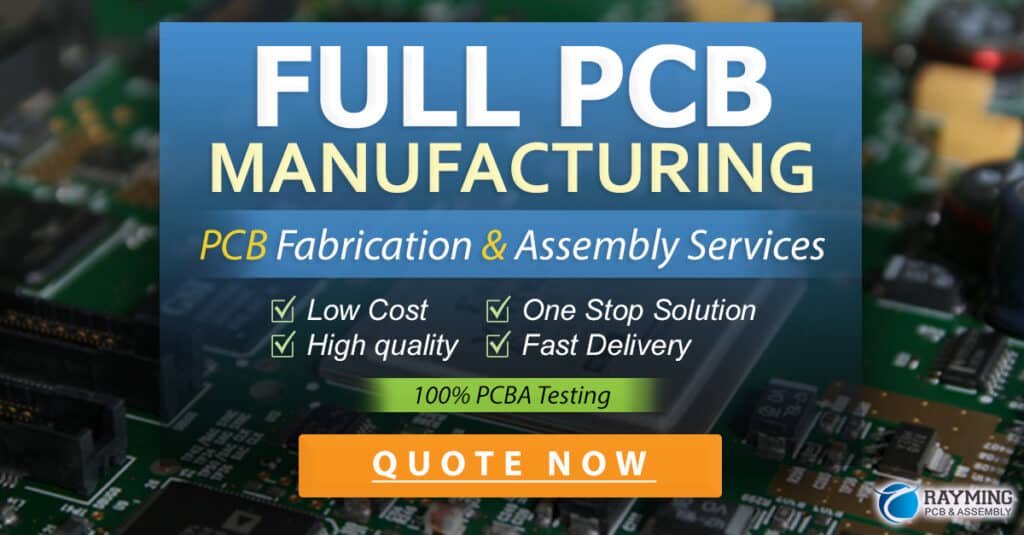
Reliability
The reliability of copper PCBs is a critical concern for users, especially in applications where failure can have serious consequences. Copper PCBs must be designed and manufactured to withstand the expected operating conditions and have a long service life.
Copper Thickness
One factor that affects the reliability of copper PCBs is the thickness of the copper traces. Thicker copper traces can carry more current and are less susceptible to damage from thermal and mechanical stresses. However, thicker traces also increase the weight and cost of the PCB.
Copper Thickness (oz) | Thickness (mm) |
---|---|
0.5 | 0.017 |
1 | 0.035 |
2 | 0.070 |
3 | 0.105 |
The table above shows the thickness of copper traces for different weights of copper. Designers must choose the appropriate copper thickness based on the current carrying requirements and the expected operating conditions of the PCB.
Solder Mask
Another factor that affects the reliability of copper PCBs is the solder mask. The solder mask is a protective layer that covers the copper traces and prevents accidental short circuits during soldering. The quality and thickness of the solder mask can have a significant impact on the reliability of the PCB.
Cost
Cost is always a concern for users of copper PCBs, especially in high-volume applications. The cost of a PCB depends on several factors, including the size, complexity, and quantity of the boards.
Material Cost
One of the main contributors to the cost of a copper PCB is the material cost. The cost of copper has fluctuated significantly in recent years, which can have a direct impact on the cost of PCBs. Other materials, such as the substrate and solder mask, also contribute to the overall cost of the PCB.
Manufacturing Cost
The manufacturing cost is another important factor in the overall cost of a copper PCB. The complexity of the design, the number of layers, and the minimum feature size can all affect the manufacturing cost. Additionally, the location and capabilities of the manufacturing facility can also impact the cost.
Environmental Impact
The environmental impact of copper PCBs is a growing concern for users, as electronic waste continues to be a major problem globally. Copper is a valuable resource that can be recycled, but the process of extracting and refining copper can have significant environmental consequences.
Recycling
One way to reduce the environmental impact of copper PCBs is through recycling. Many manufacturers offer recycling programs for used PCBs, which can help to reduce the amount of electronic waste that ends up in landfills. Recycling copper from PCBs can also help to reduce the demand for new copper mining.
Lead-Free Solder
Another way to reduce the environmental impact of copper PCBs is through the use of lead-free solder. Traditional solder contains lead, which can be harmful to the environment and human health. Lead-free solder, which typically contains tin, silver, and copper, is becoming more common in the electronics industry.
Intellectual Property
Intellectual property (IP) protection is a concern for many users of copper PCBs, especially in industries where the design of the PCB is a critical competitive advantage. Designers must take steps to protect their IP from theft or unauthorized use.
Non-Disclosure Agreements (NDAs)
One way to protect IP in copper PCBs is through the use of Non-Disclosure Agreements (NDAs). NDAs are legal agreements that prohibit the sharing of confidential information, such as PCB designs, with unauthorized parties. Designers should require all employees, contractors, and partners to sign NDAs before sharing any sensitive information.
Design Obfuscation
Another way to protect IP in copper PCBs is through design obfuscation. This involves intentionally obscuring or hiding certain aspects of the PCB design to make it more difficult for competitors to reverse engineer. Some common obfuscation techniques include:
- Using blind or buried vias
- Removing silkscreen labels
- Using non-standard component footprints
- Encrypting firmware or software
By using design obfuscation techniques, designers can make it more difficult and time-consuming for competitors to copy or reverse engineer their PCB designs.
FAQs
1. What is the difference between copper and aluminum PCBs?
Copper and aluminum are both used as conductive materials in PCBs, but copper is more commonly used due to its superior electrical and thermal conductivity. Aluminum PCBs are sometimes used in applications where weight is a critical factor, such as in aerospace or mobile devices.
2. Can copper PCBs be used in high-frequency applications?
Yes, copper PCBs can be used in high-frequency applications, but designers must take special care to ensure signal integrity. This may involve using techniques such as impedance control, shielding, and careful layout to minimize signal reflections and distortions.
3. How can I reduce the cost of my copper PCB design?
There are several ways to reduce the cost of a copper PCB design, including:
- Minimizing the size and complexity of the board
- Using standard component footprints and hole sizes
- Reducing the number of layers in the board
- Choosing a lower-cost substrate material
- Ordering in larger quantities to take advantage of volume discounts
4. What is the environmental impact of copper mining for PCBs?
Copper mining can have significant environmental impacts, including air and water pollution, habitat destruction, and greenhouse gas emissions. However, many companies are taking steps to reduce the environmental impact of copper mining, such as using renewable energy, minimizing waste, and investing in recycling programs.
5. How can I protect my IP when working with a PCB manufacturer?
To protect your IP when working with a PCB manufacturer, you should:
- Require all employees and contractors to sign NDAs
- Use design obfuscation techniques to make your PCB design more difficult to reverse engineer
- Choose a reputable manufacturer with a track record of protecting customer IP
- Consider filing for patent protection for your PCB design
In conclusion, copper PCBs are a critical component in many electronic devices, but users have several important concerns that must be addressed to ensure optimal performance and longevity. By carefully considering factors such as thermal management, signal integrity, manufacturability, reliability, cost, environmental impact, and IP protection, designers can create copper PCBs that meet the needs of their specific applications.
No responses yet