What is Copper Clad?
Copper clad is a type of material that consists of a base metal, typically steel or aluminum, which is then coated with a layer of copper. This process is known as cladding, and it combines the strength and durability of the base metal with the electrical conductivity and corrosion resistance of copper. Copper clad materials are widely used in various industries, including electronics, construction, and telecommunications.
Types of Copper Clad
There are several types of copper clad materials, each with its own unique properties and applications. Some of the most common types include:
-
Copper Clad Aluminum (CCA): CCA is a popular choice for electrical wiring and cable shielding due to its lightweight and cost-effective nature.
-
Copper Clad Steel (CCS): CCS offers excellent strength and durability, making it suitable for applications that require high mechanical performance, such as grounding rods and structural components.
-
Copper Clad Laminate (CCL): CCL is a composite material that consists of a non-conductive substrate, such as fiberglass or epoxy resin, which is then laminated with copper foil on one or both sides. It is commonly used in the production of printed circuit boards (PCBs).
Advantages of Copper Clad
Copper clad materials offer several advantages over pure copper or other conductive materials:
Cost-effectiveness
By using a base metal coated with copper, manufacturers can reduce the overall cost of production without sacrificing electrical conductivity or corrosion resistance. This is particularly important in applications where large quantities of conductive materials are required, such as in the telecommunications industry.
Improved Mechanical Properties
The base metal used in copper clad materials, such as steel or aluminum, provides enhanced mechanical strength and durability compared to pure copper. This makes copper clad suitable for applications that require both electrical conductivity and structural integrity.
Corrosion Resistance
Copper is known for its excellent corrosion resistance, which is why it is often used in outdoor applications or in environments where exposure to moisture and other corrosive elements is a concern. By cladding a base metal with copper, manufacturers can extend the corrosion resistance properties to the entire material.
Applications of Copper Clad
Copper clad materials are used in a wide range of industries and applications, including:
Electronics Industry
In the electronics industry, copper clad laminates (CCLs) are extensively used in the production of printed circuit boards (PCBs). PCBs are the backbone of modern electronic devices, providing the necessary electrical connections and mechanical support for various components. The copper foil on the surface of the CCL allows for the creation of conductive tracks, pads, and vias, which enable the flow of electrical signals between components.
Telecommunications
Copper clad materials, particularly copper clad steel (CCS) and copper clad aluminum (CCA), are commonly used in the telecommunications industry for applications such as:
- Coaxial cables
- Grounding rods
- Lightning protection systems
- Antennas and waveguides
The electrical conductivity and corrosion resistance of copper clad materials make them ideal for these applications, ensuring reliable signal transmission and long-term performance.
Construction and Infrastructure
In the construction and infrastructure sectors, copper clad materials are used for various purposes, such as:
- Electrical wiring and grounding systems in buildings
- Lightning protection systems for structures
- Reinforcement in concrete structures (copper clad steel rebar)
- Roofing and cladding materials (copper clad aluminum or steel)
The durability and corrosion resistance of copper clad materials make them suitable for these applications, providing long-lasting protection and performance.
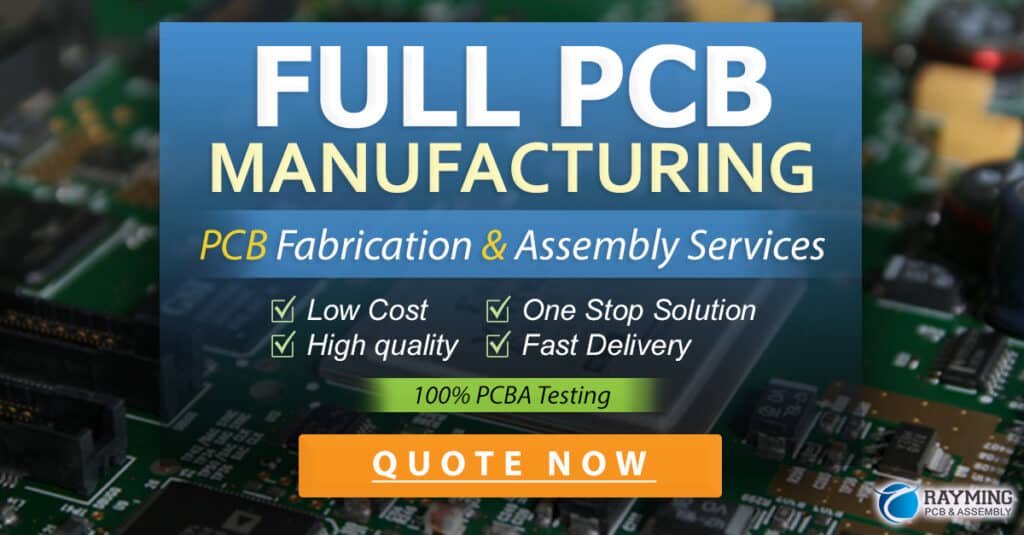
Copper Clad Manufacturing Process
The manufacturing process for copper clad materials involves several steps, depending on the specific type of copper clad being produced. Here is a general overview of the process:
-
Base Metal Preparation: The base metal, such as steel or aluminum, is cleaned and prepared for the cladding process. This may involve pickling, degreasing, or other surface treatments to ensure proper adhesion of the copper layer.
-
Cladding: The copper layer is then applied to the base metal using one of several methods, such as:
- Hot roll bonding: The base metal and copper are heated and passed through a series of rollers under high pressure, creating a strong metallurgical bond between the two materials.
- Electroplating: The base metal is immersed in an electrolytic solution containing copper ions, and an electric current is applied, causing the copper to deposit onto the surface of the base metal.
-
Explosive bonding: A controlled explosive detonation is used to create a high-velocity collision between the copper and base metal, resulting in a strong metallurgical bond.
-
Post-Cladding Processing: After the cladding process, the copper clad material may undergo additional treatments, such as annealing, to improve its mechanical properties and ensure a uniform copper layer thickness.
-
Finishing: Depending on the application, the copper clad material may be further processed, such as cutting to size, drilling, or forming, to meet the specific requirements of the end product.
Copper Clad vs. Pure Copper
While pure copper is an excellent conductor of electricity and heat, it has some limitations that make it less suitable for certain applications. Here is a comparison of copper clad materials and pure copper:
Property | Copper Clad | Pure Copper |
---|---|---|
Electrical Conductivity | Good, but slightly lower than pure copper | Excellent |
Thermal Conductivity | Good, but slightly lower than pure copper | Excellent |
Mechanical Strength | Higher, due to the base metal | Lower |
Corrosion Resistance | Good, due to the copper layer | Excellent |
Cost | Lower, due to the use of a base metal | Higher |
Weight | Lighter, depending on the base metal used | Heavier |
As shown in the table, copper clad materials offer a balance of electrical conductivity, mechanical strength, and cost-effectiveness, making them suitable for a wide range of applications where pure copper may not be the optimal choice.
Frequently Asked Questions (FAQ)
-
Q: What is the difference between copper clad aluminum (CCA) and copper clad steel (CCS)?
A: The main difference between CCA and CCS is the base metal used. CCA uses aluminum as the base metal, which makes it lighter and more cost-effective than CCS, which uses steel. However, CCS offers higher mechanical strength and durability compared to CCA. -
Q: Can copper clad materials be recycled?
A: Yes, copper clad materials can be recycled. The recycling process typically involves separating the copper layer from the base metal, which can then be recycled separately. This helps to conserve resources and reduce environmental impact. -
Q: How does the thickness of the copper layer affect the performance of copper clad materials?
A: The thickness of the copper layer can influence the electrical conductivity and current-carrying capacity of the copper clad material. Thicker copper layers generally offer better conductivity and can handle higher currents. However, thicker layers also increase the overall cost and weight of the material. -
Q: Are copper clad materials suitable for use in high-temperature applications?
A: The suitability of copper clad materials for high-temperature applications depends on the specific type of copper clad and the base metal used. Some copper clad materials, such as those with a steel base, may be suitable for high-temperature applications, while others, like those with an aluminum base, may have lower temperature resistance. -
Q: How does the corrosion resistance of copper clad materials compare to other conductive materials?
A: Copper clad materials offer excellent corrosion resistance due to the protective copper layer. This makes them more suitable for outdoor or harsh environment applications compared to some other conductive materials, such as aluminum or uncoated steel. However, the corrosion resistance of copper clad materials may be slightly lower than that of pure copper.
Conclusion
Copper clad materials offer a versatile and cost-effective solution for a wide range of applications that require electrical conductivity, mechanical strength, and corrosion resistance. By combining the desirable properties of copper with the structural integrity of a base metal, copper clad materials provide a balance of performance and affordability. As technology continues to advance, the demand for copper clad materials is expected to grow, particularly in the electronics, telecommunications, and construction industries. By understanding the properties, manufacturing processes, and applications of copper clad materials, engineers and designers can make informed decisions when selecting materials for their projects.
No responses yet