Introduction to Controlled Impedance PCB
In today’s high-speed electronic devices, signal integrity is of utmost importance. As the demand for faster data transmission rates and higher frequencies continues to grow, designers face the challenge of maintaining signal integrity while minimizing noise, crosstalk, and other unwanted effects. One crucial aspect of achieving this goal is through the use of controlled impedance PCBs.
Controlled impedance PCBs are designed to maintain a specific characteristic impedance along the length of the copper traces. By carefully managing the impedance, designers can ensure that signals propagate through the traces with minimal reflections, distortions, and losses. This article will delve into the fundamental concepts of controlled impedance PCBs, their benefits, design considerations, and manufacturing processes.
Understanding Impedance in PCBs
What is Impedance?
Impedance is a measure of the opposition that a circuit presents to the flow of alternating current (AC) at a given frequency. It is a complex quantity that combines resistance and reactance, and is measured in ohms (Ω). In the context of PCBs, impedance refers to the characteristic impedance of the copper traces.
Characteristic Impedance
Characteristic impedance is the ratio of the voltage to the current in a transmission line, such as a PCB trace, when the line is infinitely long or terminated with its characteristic impedance. It depends on several factors, including the geometry of the trace, the dielectric constant of the substrate material, and the frequency of the signal.
The characteristic impedance of a PCB trace can be calculated using the following formula:
Z₀ = √(L/C)
Where:
– Z₀ is the characteristic impedance in ohms (Ω)
– L is the inductance per unit length in henries per meter (H/m)
– C is the capacitance per unit length in farads per meter (F/m)
Benefits of Controlled Impedance PCBs
Improved Signal Integrity
The primary benefit of controlled impedance PCBs is improved signal integrity. By maintaining a consistent characteristic impedance along the length of the traces, designers can minimize signal reflections, which occur when there is an impedance mismatch between the source, the trace, and the load. Reflections can cause signal distortions, overshoot, undershoot, and ringing, which can lead to data corruption and system malfunctions.
Reduced Crosstalk
Controlled impedance PCBs also help reduce crosstalk between adjacent traces. Crosstalk occurs when a signal on one trace induces an unwanted voltage on a neighboring trace through capacitive or inductive coupling. By properly spacing the traces and controlling their impedance, designers can minimize the coupling between them and reduce crosstalk.
Faster Signal Propagation
Maintaining a consistent characteristic impedance allows signals to propagate through the traces with minimal delays and losses. This is particularly important for high-speed digital signals, where timing is critical. Controlled impedance PCBs enable faster signal propagation, which translates to higher data transmission rates and improved system performance.
EMI Reduction
Controlled impedance PCBs can also help reduce electromagnetic interference (EMI). By minimizing signal reflections and crosstalk, designers can prevent the generation of unwanted high-frequency harmonics that can radiate from the traces and cause EMI issues. Additionally, using proper grounding and shielding techniques in conjunction with controlled impedance traces can further mitigate EMI.
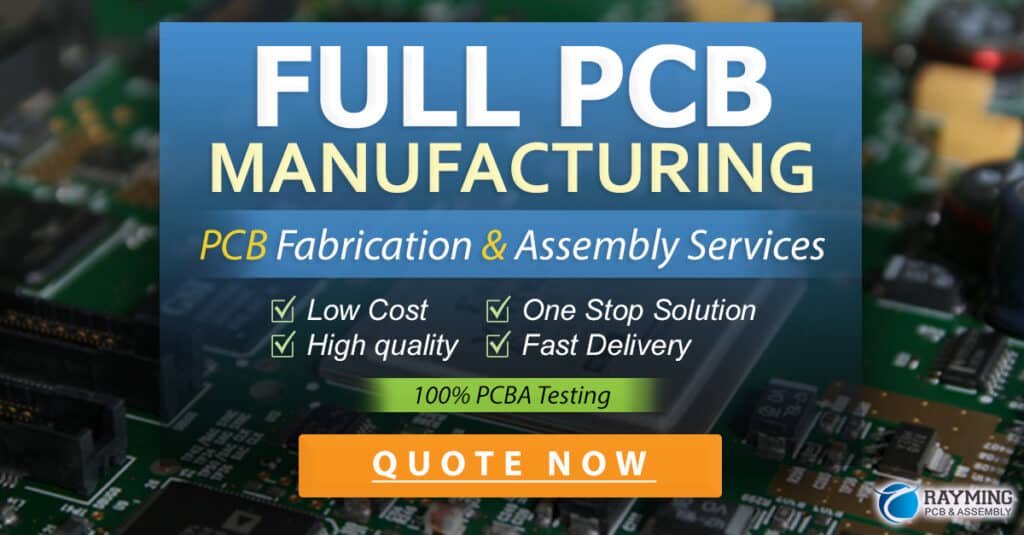
Designing Controlled Impedance PCBs
Stack-up Design
The first step in designing a controlled impedance PCB is to define the stack-up. The stack-up refers to the arrangement of the conductive layers (copper) and dielectric layers (substrate) that make up the PCB. The choice of materials, their thicknesses, and the order in which they are stacked play a crucial role in determining the characteristic impedance of the traces.
A typical four-layer PCB stack-up might consist of the following layers:
Layer | Material | Thickness |
---|---|---|
Top Copper | Copper | 1 oz. (35 μm) |
Dielectric 1 | FR-4 | 0.2 mm |
Inner Copper 1 | Copper | 0.5 oz. (17.5 μm) |
Core | FR-4 | 0.5 mm |
Inner Copper 2 | Copper | 0.5 oz. (17.5 μm) |
Dielectric 2 | FR-4 | 0.2 mm |
Bottom Copper | Copper | 1 oz. (35 μm) |
Trace Geometry
The geometry of the copper traces is another critical factor in controlling impedance. The width, thickness, and spacing of the traces determine their characteristic impedance. Wider traces have lower impedance, while narrower traces have higher impedance. Thicker traces also have lower impedance compared to thinner traces.
To calculate the characteristic impedance of a trace, designers can use various formulas or simulation tools. One commonly used formula for microstrip traces (traces on the outer layers) is:
Z₀ = 87 / √(εᵣ + 1.41) × ln(5.98 × h / (0.8 × w + t))
Where:
– Z₀ is the characteristic impedance in ohms (Ω)
– εᵣ is the relative dielectric constant of the substrate material
– h is the height of the substrate in mils (1 mil = 0.0254 mm)
– w is the width of the trace in mils
– t is the thickness of the trace in mils
For stripline traces (traces on the inner layers), the following formula can be used:
Z₀ = 60 / √εᵣ × ln(4 × h / (0.67 × (0.8 × w + t)))
Dielectric Material Selection
The choice of dielectric material is another important consideration in controlled impedance PCB design. The dielectric constant (εᵣ) of the substrate material directly affects the characteristic impedance of the traces. Common PCB substrate materials include FR-4, Rogers, and Isola, each with different dielectric constants and loss tangents.
Material | Dielectric Constant (εᵣ) | Loss Tangent |
---|---|---|
FR-4 | 4.3 – 4.7 | 0.02 |
Rogers RO4003C | 3.38 | 0.0027 |
Isola IS410 | 3.9 – 4.1 | 0.0145 |
Materials with lower dielectric constants, such as Rogers RO4003C, allow for wider traces and larger spacing between traces, which can be advantageous for high-speed designs. However, these materials are typically more expensive than standard FR-4.
Impedance Matching
To ensure proper signal transmission, it is crucial to match the impedance of the source, the traces, and the load. Impedance matching prevents signal reflections and ensures maximum power transfer. Common impedance values for PCB traces include 50 Ω, 75 Ω, and 100 Ω, depending on the application and the interface standards being used.
Termination techniques, such as series termination, parallel termination, and AC termination, can be employed to match the impedance of the traces to the source and load impedances. The choice of termination technique depends on factors such as the signal frequency, the rise time, and the available board space.
Manufacturing Controlled Impedance PCBs
Impedance Tolerance
When manufacturing controlled impedance PCBs, it is essential to specify the acceptable impedance tolerance. The impedance tolerance is the allowable deviation from the target characteristic impedance value. Common impedance tolerances are ±10% and ±5%, with tighter tolerances requiring more precise manufacturing processes and higher costs.
Impedance Testing
To ensure that the manufactured PCB meets the specified impedance requirements, impedance testing is performed. There are two main methods for impedance testing: Time Domain Reflectometry (TDR) and Impedance Coupon Testing.
Time Domain Reflectometry (TDR)
TDR is a technique that measures the reflections of a fast-rising pulse sent through the trace. By analyzing the reflected waveform, the characteristic impedance of the trace can be determined. TDR allows for the measurement of impedance along the entire length of the trace, making it useful for identifying impedance discontinuities and mismatches.
Impedance Coupon Testing
Impedance coupon testing involves the use of dedicated test coupons that are manufactured alongside the actual PCB. These coupons contain traces with the same geometry and material properties as the traces on the PCB. By measuring the impedance of the coupons using a specialized impedance tester, the characteristic impedance of the PCB traces can be verified.
Manufacturing Process Control
To achieve consistent and reliable controlled impedance PCBs, strict process control is necessary during manufacturing. This includes controlling the following factors:
- Copper thickness and uniformity
- Dielectric material properties and thickness
- Etching process and trace width control
- Lamination process and pressure control
- Environmental conditions (temperature and humidity)
By carefully monitoring and controlling these factors, manufacturers can ensure that the PCBs meet the specified impedance requirements with minimal variations.
Frequently Asked Questions (FAQ)
Q1: What is the difference between controlled impedance and non-controlled impedance PCBs?
A1: Controlled impedance PCBs are designed to maintain a specific characteristic impedance along the length of the traces, while non-controlled impedance PCBs do not have this design consideration. Controlled impedance PCBs offer better signal integrity, reduced crosstalk, and faster signal propagation compared to non-controlled impedance PCBs.
Q2: How does the dielectric constant of the substrate material affect the characteristic impedance?
A2: The dielectric constant of the substrate material is inversely proportional to the characteristic impedance of the traces. A higher dielectric constant results in a lower characteristic impedance, while a lower dielectric constant leads to a higher characteristic impedance. The choice of substrate material depends on the desired impedance and other design requirements.
Q3: What are the common impedance values used in PCB design?
A3: Common impedance values for PCB traces include 50 Ω, 75 Ω, and 100 Ω. The choice of impedance value depends on the application and the interface standards being used. For example, 50 Ω is commonly used for high-speed digital interfaces like USB and HDMI, while 75 Ω is used for video applications and coaxial cables.
Q4: What is the purpose of impedance matching in PCB design?
A4: Impedance matching is essential to ensure proper signal transmission and to prevent signal reflections. By matching the impedance of the source, the traces, and the load, designers can maximize power transfer and minimize signal distortions. Impedance matching techniques, such as termination, help achieve this goal.
Q5: How can manufacturers ensure consistent and reliable controlled impedance PCBs?
A5: To achieve consistent and reliable controlled impedance PCBs, manufacturers must implement strict process control during manufacturing. This includes controlling factors such as copper thickness and uniformity, dielectric material properties and thickness, etching process and trace width control, lamination process and pressure control, and environmental conditions. By carefully monitoring and controlling these factors, manufacturers can ensure that the PCBs meet the specified impedance requirements with minimal variations.
Conclusion
Controlled impedance PCBs are essential for maintaining signal integrity in high-speed electronic devices. By carefully designing the stack-up, selecting the appropriate dielectric materials, and controlling the trace geometry, designers can achieve the desired characteristic impedance and minimize signal integrity issues such as reflections, crosstalk, and EMI.
Manufacturing controlled impedance PCBs requires strict process control and impedance testing to ensure that the PCBs meet the specified impedance requirements with minimal variations. By understanding the fundamental concepts of controlled impedance PCBs and following best design and manufacturing practices, designers can create PCBs that deliver optimal performance and reliability in today’s demanding electronic applications.
No responses yet