Introduction to PCB Drilling and Back Drilling
PCB (Printed Circuit Board) drilling is a crucial process in the manufacturing of electronic devices. It involves creating holes in the PCB substrate to allow for the insertion of components and the creation of electrical connections between layers. PCB drilling can be classified into two main categories: through-hole drilling and controlled depth drilling.
Through-hole drilling creates holes that pass completely through the PCB, while controlled depth drilling creates holes that only penetrate to a specific depth within the PCB stackup. Back drilling is a specific type of controlled depth drilling that is used to remove unwanted portions of plated through-holes (PTHs) in high-speed PCB designs.
The Importance of Controlled Depth Drilling and Back Drilling
Controlled depth drilling and back drilling are essential techniques in modern PCB manufacturing, particularly for high-speed and high-frequency applications. These techniques help to:
- Reduce signal integrity issues, such as reflections and resonances, by controlling the stub length of PTHs.
- Improve impedance matching and reduce parasitic capacitance and inductance.
- Minimize crosstalk between adjacent signal layers.
- Enhance the overall performance and reliability of the PCB.
PCB Stackup Design Considerations for Controlled Depth Drilling
To effectively implement controlled depth drilling and back drilling, it is essential to carefully design the PCB stackup. The stackup should be optimized to ensure proper drilling depths, minimize the risk of damage to the PCB, and maintain the desired electrical performance.
Factors Affecting PCB Stackup Design
Several factors must be considered when designing a PCB stackup for controlled depth drilling:
- The number and thickness of the PCB layers.
- The material properties of the PCB substrate, such as dielectric constant and loss tangent.
- The desired impedance of the signal traces.
- The spacing between signal layers and ground/power planes.
- The via and pad sizes for the drilled holes.
Best Practices for PCB Stackup Design
To ensure successful controlled depth drilling and back drilling, follow these best practices when designing your PCB stackup:
- Use a symmetrical stackup whenever possible to minimize warpage and ensure even distribution of stresses during drilling.
- Maintain consistent dielectric thicknesses between signal layers and ground/power planes to ensure consistent impedance.
- Use a sufficient number of ground and power planes to provide adequate shielding and reduce crosstalk.
- Minimize the number of different drill depths required to simplify the drilling process and reduce the risk of errors.
- Consult with your PCB manufacturer early in the design process to ensure that your stackup is compatible with their drilling capabilities.
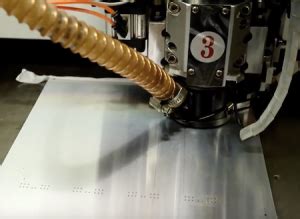
Configuring Controlled Depth Drilling Parameters
Once the PCB stackup has been designed, the next step is to configure the controlled depth drilling parameters. These parameters will determine the depth, diameter, and location of the drilled holes, as well as the drilling process itself.
Drill Depth and Diameter
The drill depth and diameter are two of the most critical parameters in controlled depth drilling. The drill depth determines how far into the PCB stackup the hole will penetrate, while the diameter determines the size of the hole.
To calculate the appropriate drill depth, you must consider the thickness of each layer in the PCB stackup, as well as the desired stub length for the PTHs. The stub length is the portion of the PTH that extends beyond the signal layer and can cause signal integrity issues if not properly controlled.
The drill diameter is typically determined by the size of the components and the required electrical performance. Smaller drill diameters can help to reduce the stub length and improve signal integrity, but they also increase the complexity and cost of the drilling process.
Drill Hit Accuracy and Registration
Drill hit accuracy and registration are critical factors in ensuring that the drilled holes are correctly positioned relative to the PCB features, such as pads and vias. Poor drill hit accuracy can result in misaligned holes, which can lead to manufacturing defects and reduced reliability.
To achieve high drill hit accuracy, it is essential to use a high-quality drilling machine with a precise positioning system. The PCB design files must also be accurately translated into machine-readable formats, such as Gerber or ODB++, to ensure that the drilling machine has the correct information.
Registration is the process of aligning the drilled holes with the PCB features on the outer layers. This is typically accomplished using registration marks or fiducials, which are precisely placed on the PCB to serve as reference points for the drilling machine.
Drilling Process Parameters
In addition to the drill depth, diameter, and hit accuracy, several other parameters must be considered when configuring the controlled depth drilling process:
- Spindle speed: The rotational speed of the drill bit, which affects the cutting speed and heat generation.
- Feed rate: The speed at which the drill bit advances into the PCB, which affects the hole quality and cycle time.
- Peck drilling: A technique used to break up chips and remove debris from the hole during drilling, which can improve hole quality and reduce the risk of damage to the PCB.
- Coolant and lubrication: The use of coolants and lubricants to reduce heat generation and improve the drilling process.
These parameters must be carefully optimized based on the specific requirements of the PCB design and the capabilities of the drilling machine.
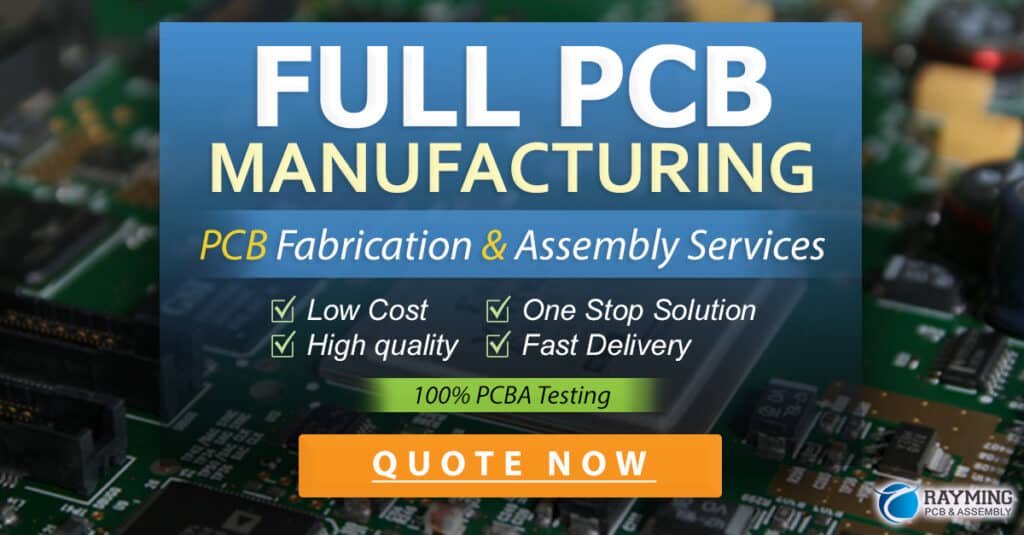
Implementing Back Drilling for Stub Length Control
Back drilling is a specific type of controlled depth drilling that is used to remove unwanted portions of PTHs in high-speed PCB designs. By removing the stub portion of the PTH, back drilling can help to reduce signal integrity issues and improve the overall performance of the PCB.
Back Drilling Process Overview
The back drilling process typically involves the following steps:
- Drilling the initial through-hole using a standard drilling process.
- Plating the through-hole to create the electrical connection between layers.
- Using a specialized back drilling machine to remove the unwanted portion of the PTH from the back side of the PCB.
- Cleaning and inspecting the back-drilled hole to ensure that the stub length has been properly controlled.
Stub Length Calculation and Control
To effectively implement back drilling, it is essential to accurately calculate and control the stub length of the PTHs. The stub length is determined by the thickness of the PCB layers and the location of the signal layers relative to the through-hole.
There are several methods for calculating the appropriate stub length, including:
- The 10H rule: This rule states that the stub length should be no more than 10 times the diameter of the hole (H) to minimize the risk of signal integrity issues.
- Simulation-based methods: These methods use electromagnetic simulation tools to model the PCB and calculate the optimal stub length based on the desired electrical performance.
- Empirical methods: These methods rely on experience and testing to determine the appropriate stub length for a given PCB design.
Once the stub length has been calculated, it must be carefully controlled during the back drilling process to ensure that the desired electrical performance is achieved.
Back Drilling Challenges and Solutions
Back drilling presents several challenges that must be addressed to ensure a successful outcome:
- Accuracy: Back drilling requires high precision to ensure that the stub length is accurately controlled and that the drilled hole does not damage adjacent layers or features.
- Cycle time: Back drilling adds an additional step to the PCB manufacturing process, which can increase the overall cycle time and cost.
- Material removal: Back drilling removes a significant amount of material from the PCB, which can affect the structural integrity and reliability of the board.
To overcome these challenges, PCB manufacturers have developed specialized back drilling machines and processes that offer high accuracy, speed, and material removal capabilities. These machines use advanced vision systems, high-speed spindles, and precision depth control to ensure that the back drilling process is performed efficiently and effectively.
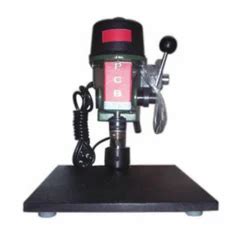
Testing and Verification of Controlled Depth Drilling and Back Drilling
After the controlled depth drilling and back drilling processes have been completed, it is essential to test and verify the results to ensure that the desired electrical performance has been achieved and that the PCB meets all applicable quality and reliability standards.
Electrical Testing Methods
There are several methods for testing the electrical performance of a PCB after controlled depth drilling and back drilling:
- Time-domain reflectometry (TDR): This method uses high-speed electrical pulses to measure the impedance and reflections of the PCB traces and vias.
- Vector network analysis (VNA): This method uses high-frequency signals to measure the scattering parameters (S-parameters) of the PCB, which provide information about the insertion loss, return loss, and crosstalk of the signals.
- Eye diagram analysis: This method uses an oscilloscope to display the quality of the signal waveforms and measure parameters such as jitter, rise time, and eye height.
These testing methods can help to identify any signal integrity issues related to the controlled depth drilling and back drilling processes and ensure that the PCB meets the desired electrical performance specifications.
Physical Inspection Methods
In addition to electrical testing, physical inspection methods are also used to verify the quality and accuracy of the controlled depth drilling and back drilling processes. These methods include:
- Cross-sectioning: This method involves cutting the PCB along a specific plane to expose the internal layers and features, allowing for visual inspection of the drilled holes and stub lengths.
- X-ray inspection: This non-destructive method uses X-rays to create images of the internal structure of the PCB, allowing for inspection of the drilled holes and other features without damaging the board.
- Microsectioning: This method involves mounting a small sample of the PCB in epoxy and polishing it to expose the internal layers and features, allowing for high-magnification inspection using a microscope.
These inspection methods can help to verify that the drilled holes and stub lengths meet the specified requirements and that there are no defects or damage to the PCB.
Best Practices for Implementing Controlled Depth Drilling and Back Drilling
To ensure the successful implementation of controlled depth drilling and back drilling in your PCB manufacturing process, consider the following best practices:
- Collaborate closely with your PCB manufacturer throughout the design and manufacturing process to ensure that your requirements are clearly understood and that the manufacturability of your design is optimized.
- Use simulation tools and modeling techniques to optimize your PCB stackup and controlled depth drilling parameters for your specific application and performance requirements.
- Implement strict process controls and monitoring systems to ensure that the drilling and back drilling processes are performed consistently and accurately, with minimal variability.
- Conduct thorough testing and inspection of your PCBs to verify that the desired electrical performance and quality standards are met, and to identify any issues or areas for improvement.
- Stay up-to-date with the latest advancements in controlled depth drilling and back drilling technologies and processes, and consider investing in specialized equipment and training to enhance your capabilities in this area.
By following these best practices and continuously improving your controlled depth drilling and back drilling processes, you can achieve higher-quality, higher-performance PCBs that meet the demanding requirements of today’s advanced electronic applications.
Frequently Asked Questions (FAQ)
- What is the difference between controlled depth drilling and back drilling?
-
Controlled depth drilling is a general term for drilling holes to a specific depth within the PCB stackup, while back drilling is a specific type of controlled depth drilling that removes the stub portion of plated through-holes (PTHs) from the back side of the PCB.
-
Why is controlled depth drilling important for high-speed PCB designs?
-
Controlled depth drilling is important for high-speed PCB designs because it helps to reduce signal integrity issues, such as reflections and resonances, by controlling the stub length of PTHs. This improves impedance matching, reduces crosstalk, and enhances the overall performance and reliability of the PCB.
-
What factors should be considered when designing a PCB stackup for controlled depth drilling?
-
When designing a PCB stackup for controlled depth drilling, factors such as the number and thickness of layers, material properties, desired impedance, layer spacing, and via/pad sizes should be considered. It is also important to maintain a symmetrical stackup, consistent dielectric thicknesses, and sufficient ground/power planes.
-
How is the stub length calculated for back drilling, and why is it important to control?
-
The stub length for back drilling is determined by the thickness of the PCB layers and the location of the signal layers relative to the through-hole. It is important to control the stub length to minimize signal integrity issues and achieve the desired electrical performance. Methods for calculating the stub length include the 10H rule, simulation-based methods, and empirical methods.
-
What testing and inspection methods are used to verify the quality of controlled depth drilling and back drilling?
- Electrical testing methods, such as time-domain reflectometry (TDR), vector network analysis (VNA), and eye diagram analysis, are used to verify the electrical performance of the PCB after controlled depth drilling and back drilling. Physical inspection methods, such as cross-sectioning, X-ray inspection, and microsectioning, are used to verify the accuracy and quality of the drilled holes and stub lengths.
No responses yet