Introduction to Conductive Threads
Conductive threads are revolutionizing the world of smart textiles by providing flexible and seamless electrical pathways within fabrics. These innovative materials enable the integration of electronic components, sensors, and actuators into garments, creating a new generation of wearable technology. With the growing demand for smart textiles in various industries, such as healthcare, sports, and fashion, conductive threads have become a crucial element in the development of functional and interactive clothing.
What are Conductive Threads?
Conductive threads are textile yarns that have been specially designed to conduct electricity. They are typically made by coating or embedding conductive materials, such as silver, copper, or carbon, into traditional textile fibers like polyester or nylon. The conductive coating allows electricity to flow through the thread, enabling the transmission of signals and power within the fabric.
Properties of Conductive Threads
Conductive threads possess several key properties that make them suitable for use in smart textiles:
-
Conductivity: The primary property of conductive threads is their ability to conduct electricity. The level of conductivity varies depending on the material used and the manufacturing process.
-
Flexibility: Conductive threads are designed to be flexible and bendable, allowing them to be seamlessly integrated into fabrics without compromising the comfort and drape of the garment.
-
Durability: Conductive threads must withstand the wear and tear associated with regular use and laundering. They are often treated with protective coatings to enhance their durability and resistance to abrasion.
-
Compatibility: Conductive threads are compatible with various textile manufacturing processes, such as weaving, knitting, and embroidery, making them versatile for different applications.
Manufacturing Processes for Conductive Threads
The manufacturing of conductive threads involves several methods to incorporate conductive materials into textile fibers. The choice of method depends on the desired properties, such as conductivity, flexibility, and durability.
Coating Methods
One common approach to creating conductive threads is through coating methods. These methods involve applying a conductive material onto the surface of the textile fiber.
-
Electroless Plating: In this process, the textile fiber is immersed in a plating solution containing conductive particles, such as silver or copper. The particles adhere to the fiber surface, forming a conductive coating.
-
Sputter Coating: Sputter coating involves bombarding the textile fiber with conductive particles in a vacuum chamber. The particles form a thin, uniform coating on the fiber surface.
-
Dip Coating: Dip coating is a simple method where the textile fiber is dipped into a solution containing conductive particles. As the fiber is withdrawn, the particles adhere to the surface, creating a conductive coating.
Embedding Methods
Another approach to manufacturing conductive threads is by embedding conductive materials within the textile fiber.
-
Core-Spinning: In core-spinning, a conductive filament, such as silver or stainless steel, is used as the core of the thread. The core is then surrounded by traditional textile fibers, creating a conductive thread with a non-conductive outer layer.
-
Melt Spinning: Melt spinning involves mixing conductive particles with molten polymer and extruding the mixture through fine holes to create conductive fibers. These fibers can then be spun into conductive threads.
-
Yarn Wrapping: Yarn wrapping is a process where a conductive filament is wrapped around a non-conductive core yarn. This method allows for the creation of conductive threads with specific patterns and designs.
Applications of Conductive Threads in Smart Textiles
Conductive threads find numerous applications in the field of smart textiles, enabling the development of innovative and functional garments.
Wearable Electronics
One of the primary applications of conductive threads is in the integration of electronic components into clothing. By using conductive threads as electrical pathways, various electronic devices can be seamlessly embedded into garments.
Examples of wearable electronics using conductive threads include:
-
Fitness Trackers: Conductive threads can be used to create textile-based sensors for monitoring physiological parameters such as heart rate, respiration, and body temperature.
-
Gesture Control: Conductive threads can be woven into gloves or sleeves to enable gesture recognition and control of electronic devices.
-
Illuminated Clothing: LEDs can be connected to conductive threads to create illuminated patterns and designs on garments.
Textile-Based Sensors
Conductive threads can be used to create textile-based sensors for various sensing applications. These sensors can detect changes in pressure, strain, temperature, and moisture, among others.
Examples of textile-based sensors using conductive threads include:
-
Pressure Sensors: Conductive threads can be woven or knitted into fabrics to create pressure-sensitive areas. These sensors can be used for applications such as monitoring foot pressure in diabetic patients or detecting seat occupancy in automotive interiors.
-
Strain Sensors: By integrating conductive threads into stretchable fabrics, strain sensors can be created to measure the deformation and movement of the textile. These sensors find applications in motion capture, posture monitoring, and gesture recognition.
-
Temperature Sensors: Conductive threads with temperature-sensitive properties can be used to create textile-based temperature sensors. These sensors can be integrated into garments for monitoring body temperature or environmental conditions.
Textile Antennas
Conductive threads can be used to create textile-based antennas for wireless communication and data transmission. These antennas are flexible, lightweight, and can be seamlessly integrated into clothing.
Examples of textile antennas using conductive threads include:
-
RFID Antennas: Conductive threads can be embroidered or woven into fabrics to create RFID antennas for tracking and identification purposes.
-
Bluetooth Antennas: Textile-based Bluetooth antennas can be created using conductive threads, enabling wireless communication between wearable devices and smartphones or other electronic devices.
-
GPS Antennas: Conductive threads can be used to create textile-based GPS antennas for location tracking and navigation applications.
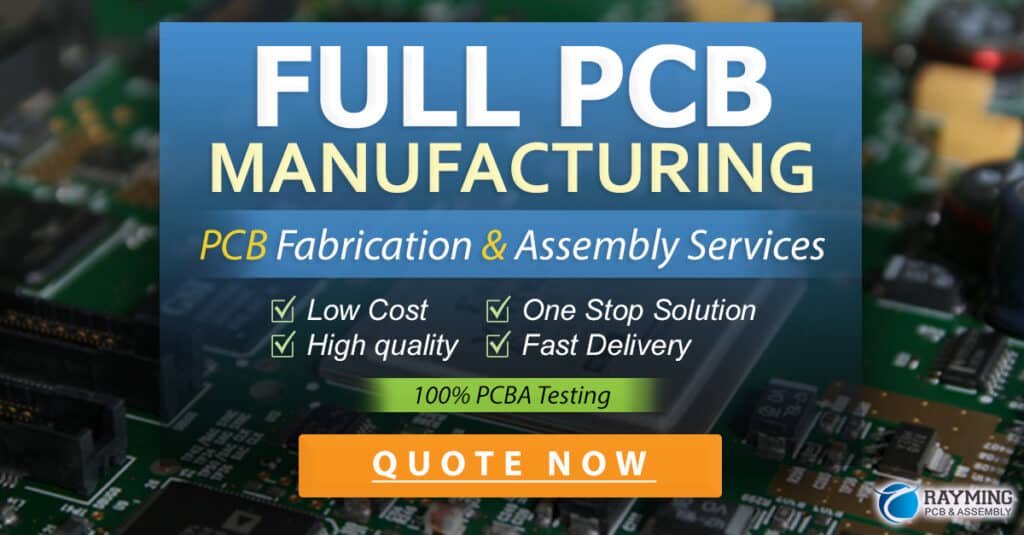
Challenges and Future Developments
While conductive threads have shown great potential in the field of smart textiles, there are still challenges to be addressed and future developments to be explored.
Challenges
-
Durability: Ensuring the long-term durability of conductive threads under repeated use and laundering is a significant challenge. The conductive coatings or filaments may degrade over time, affecting the electrical performance of the textile.
-
Standardization: The lack of standardization in the manufacturing and testing of conductive threads can lead to inconsistencies in their properties and performance. Establishing industry standards is crucial for ensuring the reliability and comparability of conductive threads.
-
Integration with Traditional Textiles: Seamlessly integrating conductive threads into traditional textile manufacturing processes can be challenging. Compatibility issues and the need for specialized equipment may hinder the widespread adoption of conductive threads.
Future Developments
-
Advanced Materials: Researchers are exploring new conductive materials and coatings to enhance the performance and durability of conductive threads. Nanomaterials, such as graphene and carbon nanotubes, show promise in improving the conductivity and mechanical properties of textile fibers.
-
Multifunctional Threads: The development of multifunctional conductive threads that combine electrical conductivity with other properties, such as antimicrobial activity or self-healing capabilities, is an area of active research. These advanced threads could expand the applications of smart textiles in healthcare and protective clothing.
-
Sustainable and Eco-Friendly Production: With the growing emphasis on sustainability, the development of environmentally friendly methods for manufacturing conductive threads is gaining attention. Researchers are exploring the use of biobased materials and recycled conductive waste as alternatives to traditional conductive coatings.
Frequently Asked Questions (FAQ)
-
Q: What are the most common materials used for making conductive threads?
A: The most common materials used for making conductive threads include silver, copper, stainless steel, and carbon-based materials like graphene and carbon nanotubes. -
Q: Can conductive threads be washed and laundered like regular clothing?
A: Yes, conductive threads are designed to withstand regular washing and laundering. However, the durability and longevity of the conductive properties may vary depending on the specific manufacturing method and materials used. -
Q: Are conductive threads safe to wear against the skin?
A: Conductive threads are generally safe to wear against the skin, as they are often coated or covered with non-conductive materials to prevent direct contact. However, it is important to ensure that the conductive threads are properly insulated and sealed to avoid any potential skin irritation or electrical hazards. -
Q: Can conductive threads be used for creating textile-based heaters?
A: Yes, conductive threads can be used to create textile-based heaters. By passing an electrical current through the conductive threads, heat can be generated through resistive heating. This principle is used in applications such as heated clothing and therapeutic heating pads. -
Q: Are conductive threads suitable for creating large-scale smart textile products?
A: Conductive threads can be used for creating large-scale smart textile products, such as smart carpets or interactive wallpapers. However, the scalability and cost-effectiveness of using conductive threads for large-scale applications may depend on the specific manufacturing processes and the required level of functionality.
Conclusion
Conductive threads have emerged as a key enabler for the development of smart textiles, providing flexible and seamless electrical pathways within fabrics. With their ability to conduct electricity, these innovative materials have opened up a wide range of possibilities for integrating electronic components, sensors, and actuators into garments.
From wearable electronics and textile-based sensors to textile antennas, conductive threads find numerous applications in various industries, including healthcare, sports, and fashion. The manufacturing processes for conductive threads, such as coating and embedding methods, have allowed for the creation of threads with specific properties and functionalities.
However, challenges such as durability, standardization, and integration with traditional textiles still need to be addressed to fully realize the potential of conductive threads. Ongoing research and future developments in advanced materials, multifunctional threads, and sustainable production methods hold promise for further advancing the field of smart textiles.
As the demand for smart and interactive clothing continues to grow, conductive threads will play a crucial role in shaping the future of wearable technology. With their flexibility, conductivity, and compatibility with textile manufacturing processes, conductive threads are poised to revolutionize the way we interact with our clothing and the world around us.
No responses yet